今回はミニ四駆のATバンパーのスラスト抜け対策方法(スラスト抜け防止方法)について解説していきます。
本記事で解説するスラスト抜け対策方法についてはフロント側・リヤ側のいずれにも対応可能ですが、今回はフロントATバンパーのスラスト抜け対策をメインに解説していきます。
尚、本記事の途中で解説している具体的な加工方法は当サイトで以前紹介したフロントATバンパーをベースとしていますが、そのフロントATバンパーと異なる形のものでも流用できる内容となっています。
スラスト抜けに困っている方は一読して頂ければと思います。
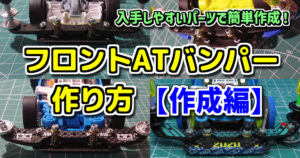
スラスト抜けについて
まずはスラスト抜けとは何なのか、スラスト抜けが起こることによってマシンはどのような影響を受けるのかについて解説していきます。
スラスト抜けとは
スラスト抜けとは走行中にローラーがフェンスに接触した衝撃やジャンプ後の着地時の衝撃でローラーのスラスト角が変わりアッパースラスト(ローラーが上向き)になることを示します。
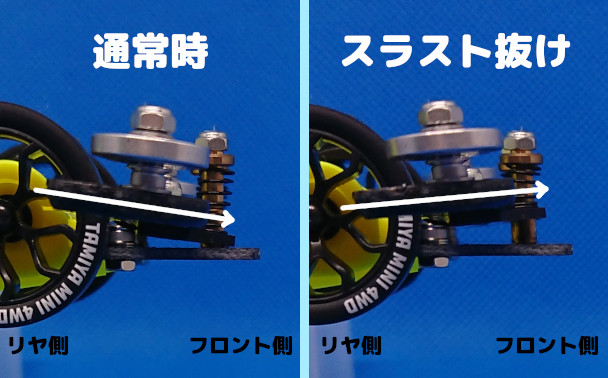
このスラスト抜けはすべてのマシンで起きるわけではなく、無加工のバンパーであったり デフォルトのバンパーにフロントステーなどを説明書通りに取り付けた状態(所謂リジットバンパー)では 基本的にバンパーの角度は固定されたままでスラスト抜けが起きることはありません。
スラスト抜けが起きやすいのは AT(オート トラック)バンパーと呼ばれる マシンの一部がコースフェンスに乗り上げた際にいなし効果を持つ構造のものであり、特に強い衝撃を受けやすいフロント側のバンパーはスラスト抜けすることが多々あります。
スラスト抜けのデメリットについては後述しますが、スラスト抜けが嫌なのであればスラスト抜けしないリジットバンパーにすればスラスト抜けに困ることはありません。
しかし、現代のミニ四駆のコースは走行中にジャンプを伴う立体セクションが当たり前の状況であり、それらのコースをより安定して走行するためにもATバンパーは必須とも言える改造となっています。
リジットバンパーでもATバンパーのようにコースフェンスに乗り上げた際にコース復帰させる改造は可能ですが、それでもATバンパーと比べるといなし効果は落ちてしまいます。
このことからスラスト抜けのリスクを考慮してもATバンパーを採用する人の方が圧倒的に多いのが現状となり、そのATバンパー使用時にスラスト抜けに悩まされている人も少なくありません。
スラスト抜けが起きると どうなるか
ではスラスト抜けが起きた場合にマシンにどういった影響があるかについて、フロントローラーとリヤローラーでそれぞれ挙動が変わってくるので、フロントとリヤに分けて解説していきます。
フロントローラーがスラスト抜けした場合
まずフロントローラーがスラスト抜けした場合ですが、スラスト抜けが発生することによりフロントローラーがアッパースラスト状態(ローラーが上向き)になります。
そして、アッパースラスト状態でコーナーに入るとマシンはローラーの向きに沿って走行し そのままコースから飛び出してコースアウトする可能性が高くなります。
ただし、スラスト抜けしたからといって必ずしもアッパースラストになるとは限らず、元のダウンスラスト(ローラーが下向き)の角度が大きければ多少のスラスト抜け程度ならダウンスラストの傾斜がただ若干浅くなるだけで済みます。
また、スラスト抜けによってフロントローラーがフラット状態(ローラーが水平の状態)であればコーナーリングが早くなったりもするので、時にはスラスト抜けがマシンにいい影響を与えることもあります。
とは言え、スラスト抜けのメリット・デメリットを考えると、デメリットの方が大きく メリットの部分は狙ってできるものでもなく偶発的な要因が多いので フロントローラーのスラスト抜けは可能な限り避けたいところではあります。
リヤローラーがスラスト抜けした場合
次にリヤローラーがスラスト抜けした場合ですが、これはフロントローラーとは様相少し異なり 文章で説明するよりも画像で説明した方が早いので、画像を交えて解説してきます。
以下の画像はリヤローラーをアッパースラストに固定したマシンのリヤローラーがフェンスに当たった時の挙動を示したものとなります。
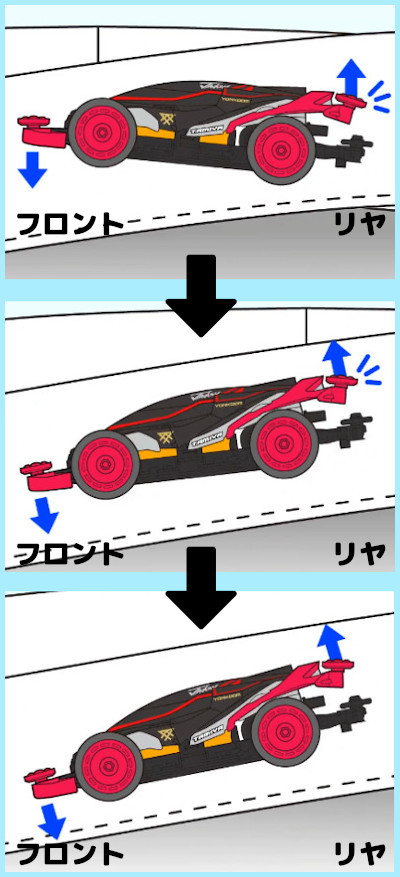
リヤーローラーがスラスト抜けしてアッパースラストになった状態でフェンスに当たると、リヤローラの向きにあわせてマシンのリヤ側が浮き その反動でフロント側が沈み マシンがコース内に収まりコースアウトを防ぐことができます。
上の画像だけ見るとリヤローラーはスラスト抜けしてアッパースラストになっても良いかと思えますが、無駄にリヤ側(リヤタイヤ)が浮いてしまうと一時的にフロントタイヤだけで走る事になりタイヤが路面を蹴る力が半減します。
更にはリヤタイヤが浮いた後にタイヤが路面に戻る時に無駄にバウンドしてしまいマシンの走りが不安定となり 最悪その不安定は走りが原因となりコースアウトを誘発することもあります。
このことからリヤローラーが頻繁にスラスト抜けを起こしてアッパースラストになることは速度低下にも繋がるため、意図しないところでのスラスト抜けは避けたいところでもあります。
ただ、リヤローラーはフロントローラに比べてフェンスから受ける衝撃が少なくスラスト抜けしにくいことと、スラスト抜けした場合 恩恵を受けることもあるのでフロントローラー程スラスト抜けに気を遣う必要もないかと。
そうした事情も考慮して、今回はフロント側のスラスト対策方法をメインで解説していきますが、リヤ側にも応用できる対策方法もあるので必要があればリヤ側にも適用してもらえればと思います。
スラスト抜けの原因
スラスト抜け対策をする上で何故スラスト抜けが起こるかを知っておくことで、この後解説するスラスト抜け対策方法をより理解しやすくなることから、まずはスラスト抜けが起きる代表的な2つの原因を解説していきます。
ATバンパー軸とフロントローラーの位置
スラスト抜けの根本的な発生要因としては、フロントローラーがフェンスに接触し、フロントローラーが衝撃を受け その衝撃がATバンパーの軸に伝わります。
そして、衝撃を受けたATバンパーの軸はフロントローラーと同じ方向(後方)への力が加わり、結果ATバンパーごと後方(リヤ側)に引っ張られてスラスト抜けの状態となります。
このことからATバンパー軸よりもフロントローラーが前にあると、ATバンパー軸への衝撃がより強くなってしまうので、ATバンパー軸はフロントローラーよりも前に配置することがフロントATバンパーでの必須事項とも言えます。
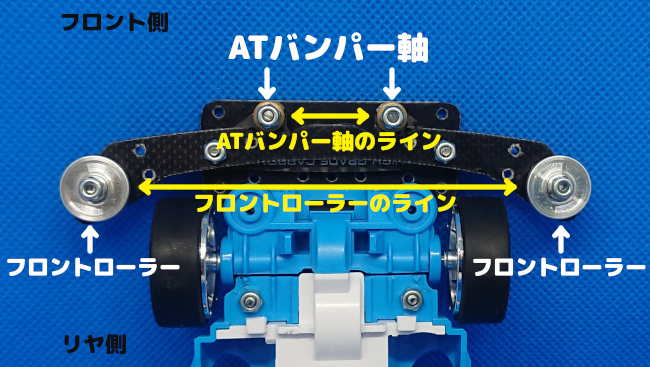
上の画像は当サイトの別記事で作成したフロントATバンパーのものとなり、ATバンパー軸のラインがフロントローラーのラインよりも前側(フロント側)に配置された構成となって必須条件は満たしています。
もし、上の画像とは異なる形のフロントATバンパーを作成しようと思っている方はこのATバンパー軸とフロントローラーの位置だけには十分注意し、くれぐれもフロントローラーの位置がATバンパー軸よりも前にならないようにしてください。
尚、ATバンパー軸とフロントローラーの位置関係については上記で紹介した条件以外にもATバンパー軸の幅やローラーのコーナーフェンスにあたる箇所の高さなどの複数の要因も絡んできます。
そうした各要因の詳細をを説明していくと力学?的な話も入ってきて話が長くなるので省略させてもらいます(単に私が詳しく説明できないというのもありますが…(笑))
スプリングの圧力
スラスト抜けのもう一つの発生要因としてスプリングの圧力が挙げられ、これについては図を交えて解説していきます。
まずはマシンの側面から見たフロントATバンパーのフラット状態(スラスト角0度)が以下となります。
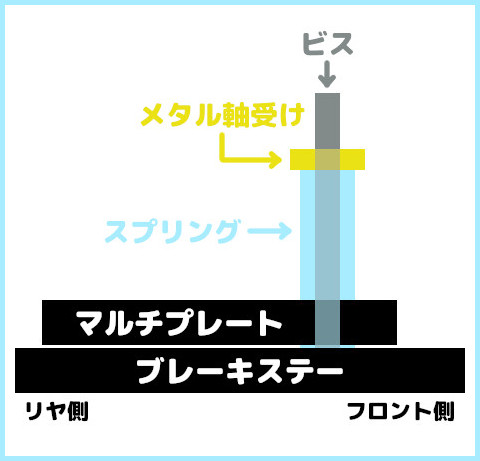
※上画像の構造は別記事で紹介しているフロントATバンパーがベースとなっています。
解説に必要な最低限のパーツのみ記載しているのでフロントATバンパーの構成に含まれるナット・フロントステー・ローラーなどのパーツは図から省いています。
このフラット状態では、スプリングの圧力はフロント側・リヤ側共に均等なのでスラスト抜けしにくい状態となっており、スプリングの圧力が強中弱3段階あると仮定した場合ここでの圧力は「中」となります。

このままの状態であれば可動をスムーズにするためのマルチプレートの穴拡張の加工を間違えないければスラスト抜けも起こりにくくなります。
ただ、あまりフロントステーをフラットにする方も少ないと思いますし、スラスト角が0度だとコーナリング時のコースアウトの心配もあるので現実的な構成ではありません。
そして、次はスラスト角を付けた状態の図となります。
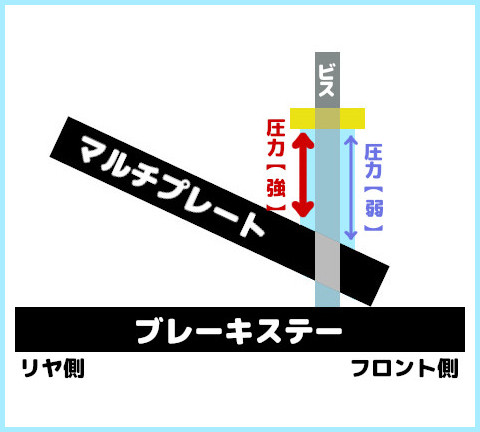
※フラット状態のとの違いを分かりやすくするためスラスト角は敢えて25度と極端な傾斜にしています。
スラスト角を付けマルチプレートに傾斜ができたことによりスプリングの圧力がフロント側・リヤ側とで変わってきています。
スプリングは長さが短いほど圧力が強くなるので、スプリングの長さが長いフロント側はリヤ側に比べてスプリングの圧力が弱くなります。
その結果、ATバンパーが衝撃を受けた際にフロント側のマルチプレートが上がりやすくなり スラスト抜けを誘発しやすい状態となってしまいます。
以下の画像は過去に私が作成した旧バージョンのフロントATバンパーとなります。
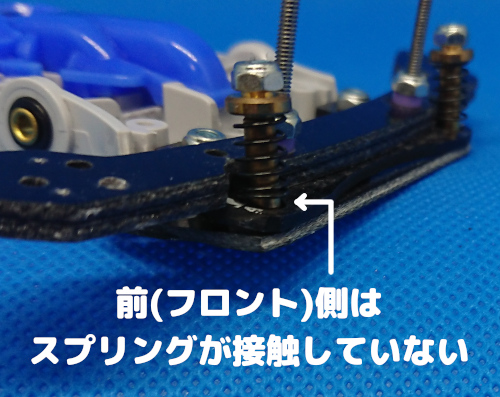
上画像はスラスト角がある状態でATバンパーが可動した拍子にスプリングがリヤ側だけに接触して、フロント側は一切接触していない状態になっています。
以下の画像の矢印で示した箇所がスプリングのフロント側となります。
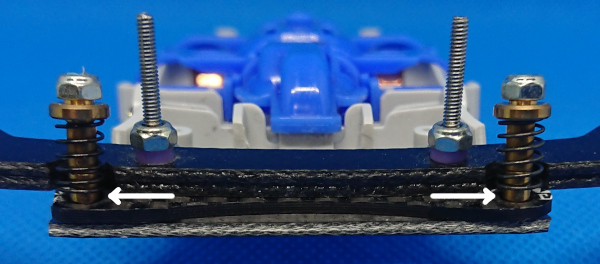
上画像をよく見るとわかるのですがATバンパーのフロント側はスプリングの圧力が弱いどころかほぼ圧力がない状態であり、ATバンパーが簡単にフラット状態に戻ってしまいます。
スラスト抜け対策方法
ここではいくつかのスラスト抜けの対策方法を紹介していきます。
ATバンパー軸とローラーの距離を離す
スラスト抜けの原因の「ATバンパー軸とフロントローラーの位置」で解説したように、スラスト抜けを起こしにくくさせるためにはATバンパー軸をフロントローラーよりも前(フロント側)に配置することが必須となります。
以下の画像が別記事で作成したフロントATバンパーのATバンパー軸とフロントローラーの位置関係となりますが、マシンを上から見下ろした時にATバンパー軸のラインがフロントローラーのラインよりも前方(フロント側)にあります。
この互いのライン間の距離が長ければ長いほどATバンパー軸が受ける衝撃が減り、よりスラスト抜けが発生しづらくなります。
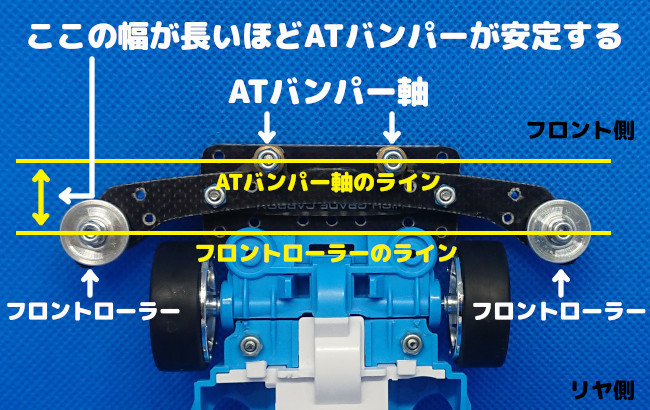
以下の画像は基本的に同じ構造のフロントATバンパーではありますが、バンパー部分のステーのみ変えたものとなっていて、この2種類のステーごとのライン間の幅を見ていきたいと思います。
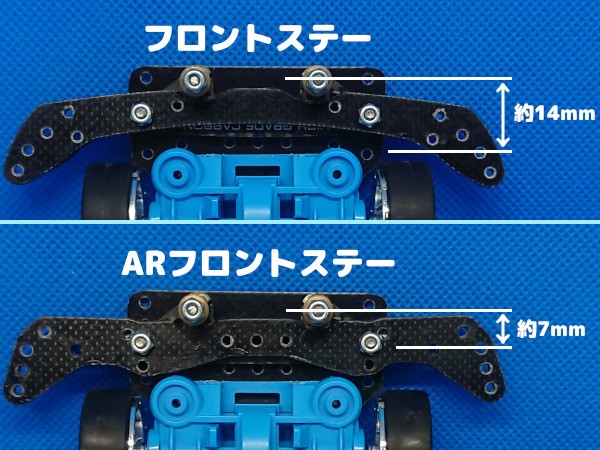
フロントローラーのラインについてはいずれのもステーも13mmローラー取り付けラインです。
そして、同じ13mmローラーを取り付けた場合のフロントローラーのラインからATバンパー軸のラインまでの距離がステーで異なり、距離が長いフロントステーの方が安定感があるATバンパーとも言えます。
このことからスラスト抜けに対する安定性を重視するなら、よりローラーの位置が後方になるフロントステーを選ぶべきかと思います。
更に同じステーでも使用するローラー径を小さくすればより後方(リヤ側)にローラーを配置できるので、各ステーの最も後方にあるローラー穴(9mmローラー用)が最も望ましいことのなりますが、必ずしも9mmローラーがそのコースに適しているとは限りません。
そもそも各ローラー穴ぐらいの距離の違いでどのくらい衝撃を減らすかは正直分かりづらく、スラスト抜け対策のために使用するローラー径を選択するよりも コースに合ったローラー径を選択した方が効果的かと思われます。
とにかくステー選び・ローラー選びで迷ったらより後方(リヤ側)に配置できるのを選択するのもありかと思います。
スプリングの圧力を上げる
ここでは「スプリングの圧力」が原因で発生するスラスト抜けの対策方法で、ステーの前後にかかるスプリングの圧力が違うとしても、スプリング自体の圧力を上げれば全体にかかる圧力も増えるわけで、以下の2種類の方法でスプリングの圧力を上げていきます。
スプリングを硬くする
非常にシンプルな方法でパーツを変えるだけでスプリングの圧力を変えられるので、もっとも簡単な方法でもあります。
現在販売されているグレードアップパーツのスプリングを硬さは以下となります。
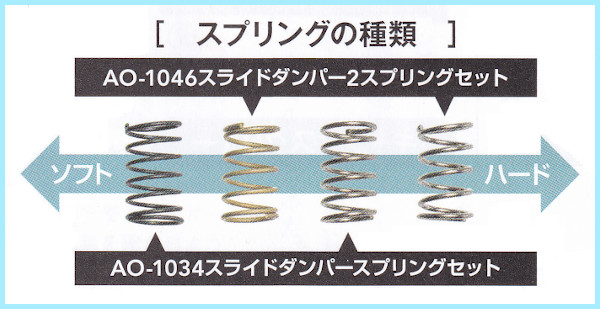
最初はスプリングセットの最も圧力が弱い黒のスプリングを使い、圧力が弱くスラスト抜けが起こりやすいようであれば同梱している銀のスプリングに変えます。
それもあわなければスプリングセット2のスプリングを試してみると良いかもしれません。
ただし、スプリングを硬くした場合ATバンパーが安定する反面 ATバンパーとしてのいなし効果が落ちてしまい、フェンスに乗り上げた際のコース復帰率が下がる可能性があるので一長一短の方法でもあります。
スプリングの幅を変える
こちらもある意味「スプリングを硬くする」方法と同一で、スプリングの幅(距離)を短くすればスプリングの圧力を強くすることができます。
実際の例として今回解説しているATバンパーのスプリング部分は真鍮パイプ2個にしていますが、これを真鍮パイプ1個と真鍮パイプよりも短い3mmスペーサーの構成にすることでスプリングの幅を短くすることができます。
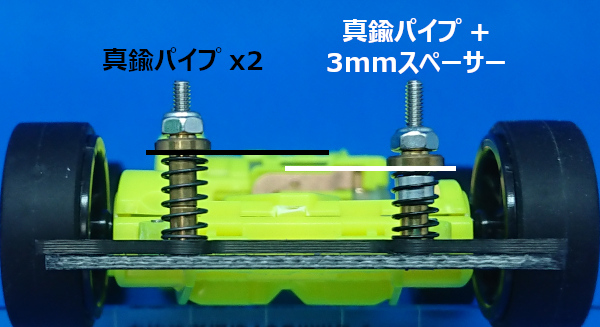
上の画像は左側が真鍮パイプ2個、右側が真鍮パイプ1個+3mmスペーサーとなっており、右側の方がスプリングの幅が短くスプリングの圧力が増している状態となっており、スペーサーをより短い1.5mmに変えれば更にスプリング圧力を増すことができます。
ただしスペーサーに変える場合、バンパーの拡張した支柱部分の穴は真鍮パイプの通るスペースしかなくスペーサーは通ることができないため可動域が少し制限されてしまいます。
そうした可動域の問題を回避する方法として切断した真鍮パイプを用いる手段もあります。
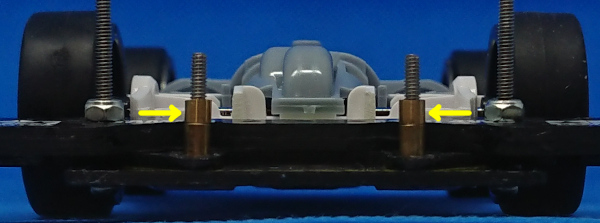
真鍮パイプの切断方法については以下の記事にて解説しているので、加工する場合はこちらをご参照ください。
この方法と先程紹介した「スプリングを硬くする」方法を組み合わせれば、スプリングの圧力をより細かく調整できるようになります。
ただし、スプリングの幅を狭めるとスプリングの圧力が増えると同時にATバンパーとしていなし効果が落ちてしまうので、こちらも一長一短の方法ではあります。
支えを付ける
これは1軸ATバンパーでは必須とも言える方法で、以下の画像のように前後に「支え」をつけることでスラスト抜けを防止することができます。
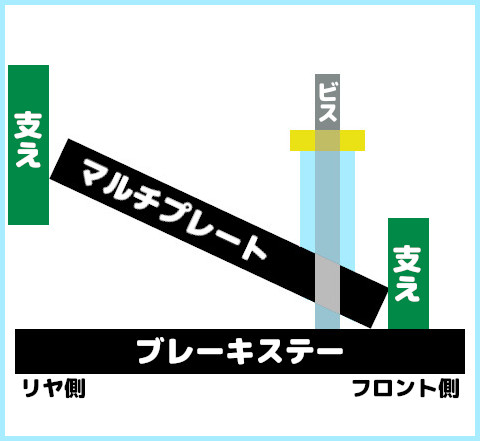
以下の画像は「支え」を設置する箇所の一例となり、必ずしも以下の位置に設置するのがセオリーということではありませんが、フロント側・リヤ側のそれぞれ左右に支えを置くことでATバンパーを安定させることができます。
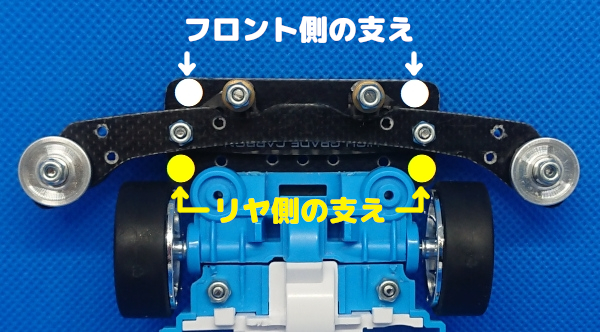
支えを設置するポイントとしてはフロント側の支えはは地面寄りの位置で、リヤ側の支えは天井寄りの位置でATバンパーを支えることによりスラスト抜けを発生しづらくさせます。
支えに使うパーツとして代表的なのがスペーサーで、フロント側であればビスとスペーサーを使って支えとなる支柱をブレーキステーに取り付ける方法があります。
また、リヤ側であればプレートやスペーサーを使ってシャーシかブレーキステーに取り付けたり・直接シャーシ自体を支えとしたりと様々なバリエーションがあります。
ただ、これらの方法はATバンパーを支えてくれるメリットがあると同時に、ATバンパーの動きに制限がかかりいなし効果が減少するというデメリットもあります。
そもそもこの方法は1軸ATバンパーでは必須であり非常に重宝する方法ですが、2軸のATバンパーはこれらの支えがなくてもそれなりにATバンパーは安定した状態にあるので、デメリットになることもあります。
2軸ATバンパーで支えを付けるということであればリヤ側だけでも十分効果があるので、まずはリヤ側に支えを付け可動を確認します。
それでもATバンパーがぐらつきスラスト抜けしやすいということであればフロント側の支えを追加するということでいいと思います。
つっかえ棒を付ける
こちらは上で紹介した支えを付けるを応用した方法で、多少加工の手間はかかりますが今回紹介するスラスト抜け対策方法のなかでも最も効果が大きいとも言えるおすすめの対策方法でもあります。
バンパーの中心部分につっかえ棒を付けることでスラスト抜けを防止し、概要図は以下となります。
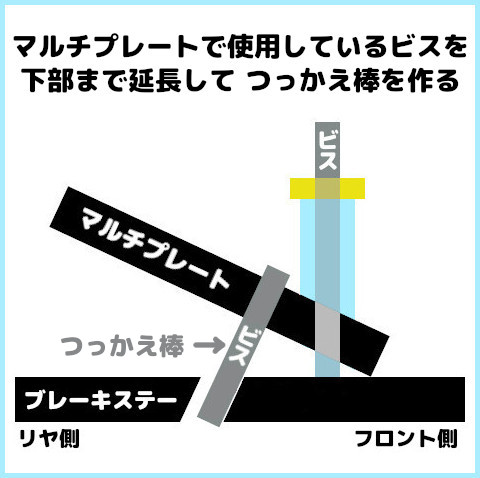
マルチプレートにビスを取り付け ブレーキステー側はビスを貫通させるための穴をあけ、このビスをつっかえ棒として使用していきます。
(当サイトで紹介しているフロントATバンパーの場合は各パーツ結合用としてマルチプレートに装着するビスを下部まで延長させ それをつっかえ棒としています)
このつっかえ棒がスラスト抜け対策として実際どうように作用するかの概要図は以下となります。
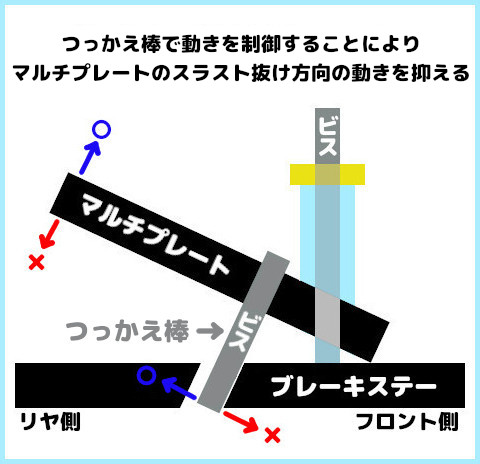
ブレーキステーのつっかえ棒を通しているスペースのフロント側をほぼ無くし リヤ側を広めにすることでつっかえ棒の前後の動き調整します。
このつっかえ棒がフロント側に傾くことを制御することによりマルチプレートがスラスト抜けする方向への可動を抑えることができます。
そして、次からつっかえ棒をマシンに実装させる具体的な方法を解説していきますが、加工のベースとなるバンパーは別記事のフロントATバンパーを使っていきます。
ATバンパーは必ずしも本記事で紹介しているものを使用する必要はなく、他の形のものでも活用可能となります。
まずマルチプレート側は各ステーと結合するために使用するビスをスラスト抜け制御用のつっかえ棒にするため、少し長めのビスとスペーサー(3mm)を用意してマルチプレートと各ステーを結合させます。
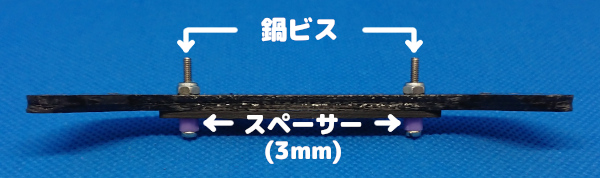
※今回は全体の構成を見やすくするために敢えて 無駄に余長があるビスを使用しています。
ここでポイントとなるのがスペーサーの追加です。
このスペーサーを使うことでマルチステー下部へのビスの延長が可能になり、つっかえ棒としてもいい具合にブレーキステーと干渉しスラスト抜けを制御する役割を果たしてくれます。
(上のATバンパーの構成では丁度3mmスペーサーが長すぎず短すぎの幅でフィットします)
そしてブレーキステー側は以下の既存ビス穴を拡張していきます。
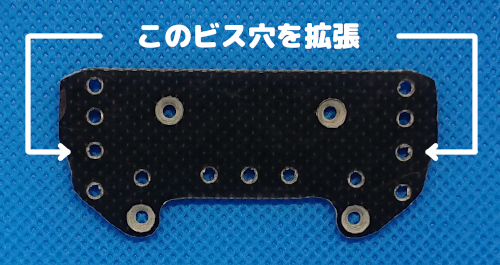
ブレーキステーのビス穴拡張にはリューターを使用し、電動リューター用 ビット5本に含まれる細めの円筒形ビットを使用します。

このビットがビス穴に丁度入るので、ビス穴にビットを入れて徐々に穴を拡張していきます。
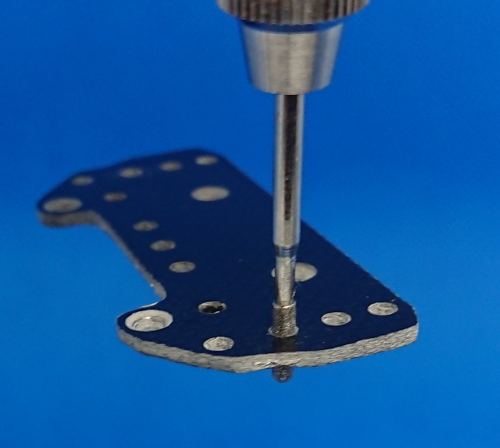
そしてブレーキステーのビス穴を拡張し つっかえ棒付きのマルチプレートを取り付けた状態が以下の画像となります。
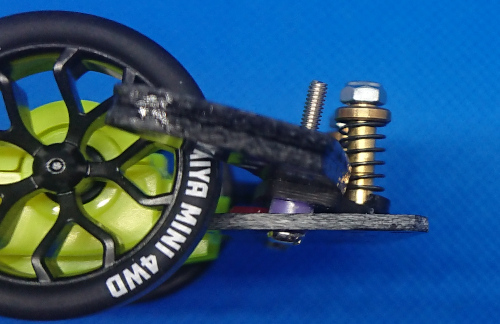
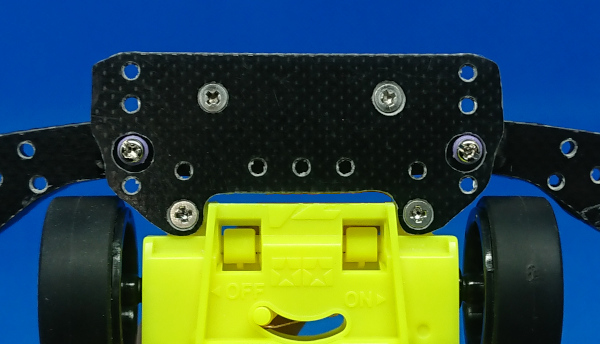
ここで注意して欲しいのはブレーキステーのビス穴拡張方法で、適当にビス穴を拡張してしまうとスラスト抜け防止の効果が著しく落ちてしまいます。
しっかりとスラスト抜け防止をしつつATバンパーとしての可動もスムーズにさせるためにはビス穴の四方(上下左右)を以下の画像のように加工していきます。
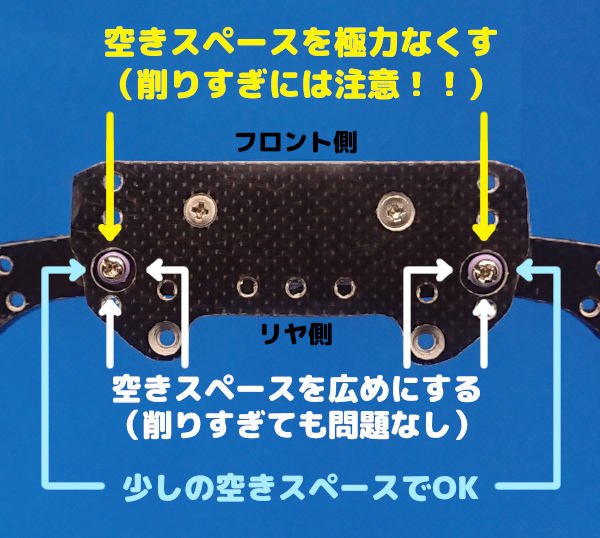
ビス穴の上部(フロント側)の部分とつっかえ棒(スペーサー)とのスペースを無くすことでスラスト抜けを防止し、ビス穴の下部(リヤ側)のスペースを広くすることでスラスト抜けとは反対方法の可動がスムーズになります。
また、ATバンパーの左右の傾きをスムーズにさせるために穴の内側(中央側)に適度な空スペースが必要となります。
特にビス穴の上部の加工は 削りすぎてしまうとスラスト抜け防止の効果が出なくなるため要注意加工箇所でもあります。
以下の画像は 今回の画像のベースとなっているフロントATバンパーの具体的な加工方法となっているので、当サイトで紹介しているフロントATバンパーを使用している方は以下の内容を参考に加工してください。
適切なスラスト抜け防止用の穴を作るためには、VZシャーシ用とMA・MSシャーシ用で加工の仕方が少しが変わり、加工概要は以下となります。
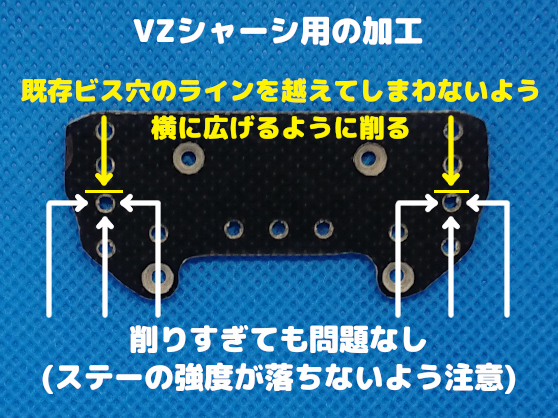
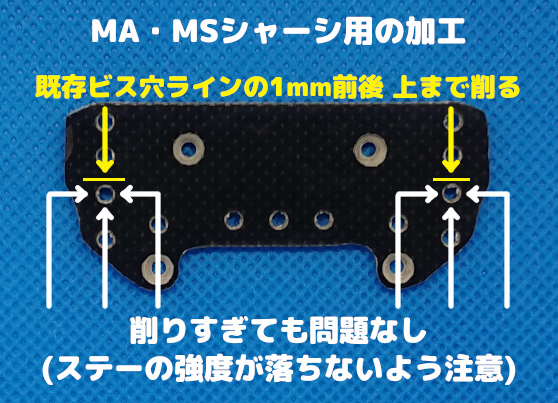
ビス穴の上部の加工はフロントATバンパーの支柱の位置で最適なラインが変わるためVZシャーシ用かMA・MSシャーシ用かで少し削り度合いが変わってきます。
※MA・MSシャーシ用に穴を拡張する場合は皿ビス穴加工ビットを貫通させても穴全体のスペースに余裕があるので、より早く穴拡張したいのであれば最初に皿ビス穴加工ビットを貫通させることをおすすめします。
VZシャーシ用のブレーキステーは既存ビス穴の上部のラインを越えて削らないよう横に広げるように削り、MA・MSシャーシ用のブレーキステーは既存ビス穴の上部のラインから更に1mm前後程削っていきます。
もう一点加工時に注意すべき点として、ビス穴の上部の最適な加工ラインはバンパーのスラスト角によっても若干変わってくるということです。
あらかじめスラスト角を付けた状態のバンパーを用意し、手間ではありますが何度もパンパ―をブレーキステーにセットしながら穴の拡張度合いが問題ないかを確認しながら慎重に作業することをおすすめします。
尚、各シャーシ用にビス穴を拡張したものが以下となります。
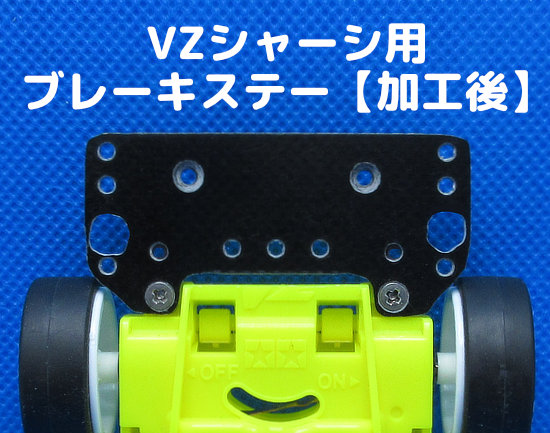
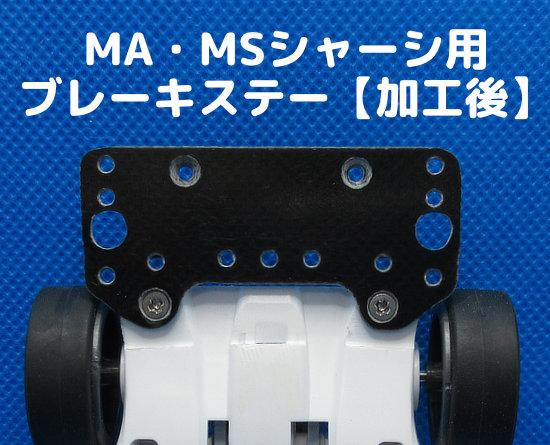
上の加工後のVZシャーシ用のブレーキステーは若干いびつな形をしていますが、ビス穴上部の箇所さえつっかえ棒にフィットさせていればOKです。
何度も言いますが、くれぐれもビス穴上部を削りすぎないよう十分注意してください。
このつっかえ棒のための加工は、ATバンパーのメンテナンス性アップの追加効果もあります。
ATバンパーをブレーキステーに取り付けたままの状態で、ATバンパーの支柱となっているビス締めを調整することが可能となります。
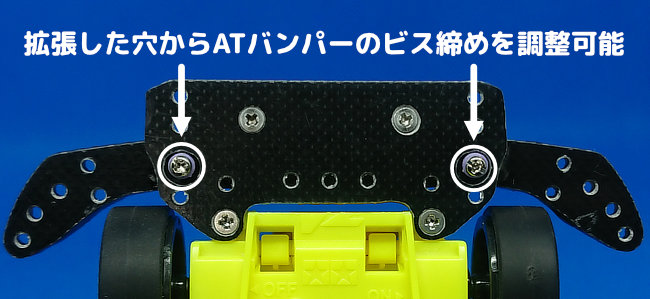
通常であればATバンパーを分解したい場合は、ATバンパーを一旦ブレーキステーから取り外す必要がありますが、それが不要となるのでメンテナンス性が向上します。
ATバンパー自体 ブレーキステーに取り付けた後にメンテナンスする機会も少ないかに思えますが、、ATスライドダンパーのようなビスの締め具合が重要となってくる場合には 非常に重宝します。
基本的にビス穴の拡張による他の改造への弊害はないので、このメンテンナンス性向上のためだけに穴を拡張するのも大いにありです。
普段からATバンパーのメンテナンス頻度が多いという方は、ビス穴を拡張してみてはいかがでしょうか。
スプリングの圧力を均等にする
こちらも今回紹介するスラスト抜け対策方法の中でも比較的効果が大きい方法となり、上のつっかえ棒を付けると併用することでよりスラスト抜け防止の効果が増し、おすすめの対策方法でもあります。
ATバンパーにスラスト角をつけることによりスプリングの前側・後ろ側の圧力が変わる事はスラスト抜け原因の「スプリングの圧力」のところで図を交えて説明しましたが、あらためてその図見てみましょう。
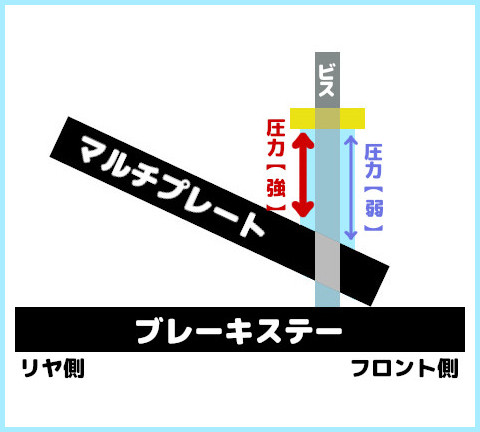
このようにフロント側スプリング圧力が弱くなり、結果スラスト抜けが起きやすくなってしまいます。
しかし、以下の画像のように 前側の部分だけマルチプレートの高さを増やせば前後の圧力を均等にすることが可能です。
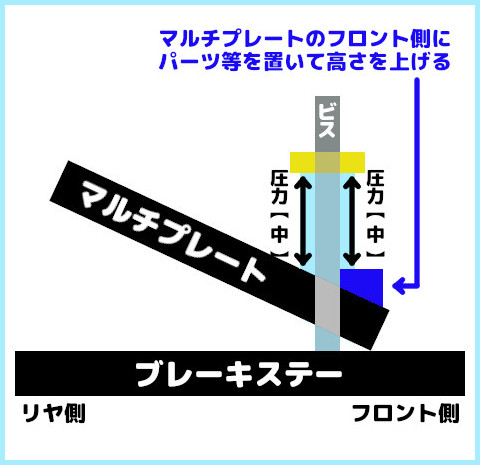
この高さを上げるパーツとしておすすめなのがステー・プレートの端材で、ステー・プレート1枚分の厚さ(1.5mm)を追加することでフロント側の高さを1.5mm上げることができます。
フロントATバンパー用のマルチプレートのフロント側に載せるパーツの作り方は別記事[フロントATバンパー 作り方]の「スラスト抜け対策加工」にて解説しているのでここでの説明は省略します。
ただ、1.5mm厚の高さで前後のスプリング圧力が均等になるかと言うとそうでもなく、今度はフロント側のスプリング圧力が増してしまいます。
こうなると またスプリング圧が不均等になってしまいますが、前側を抑える力が強ければスラスト抜けが発生しにくく、ATバンパーの動きとしても特別悪くなるということもないので、前側の圧力が強い分には問題ないかと。
また、この対策方法はスラスト角がないフラットの状態でも効果を発揮し、フロント側のスプリング圧力が強いため、むやみにスラスト抜けが出るということも抑えることできます。
加工の手間が少々かかる方法ではありますが、地味に効果を発揮するスラスト抜け対策でもあるので、余裕がある方は試してみてはいかがでしょうか。
最後に
今回はスラスト抜け対策(スラスト抜け防止方法)にスポットをあてて解説してきました。
スラスト抜け対策方法は多種多様で今回紹介した対策方法以外にも様々な方法があります。
ATバンパーの構造によっても適した対策方法が変わってきますので、本記事の内容を参考にご自分のマシンに適したスラスト抜け対策方法を見つけてもらえれば幸いです。
尚、本記事内で度々紹介していますが、本記事で使用している実機マシンのフロントATバンパーの作成方法については以下の記事にて解説していますので、興味がある方はこちらも一読して頂ければと思います。
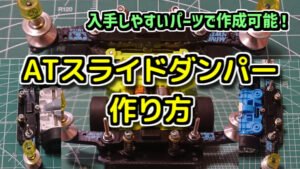
コメント
コメント一覧 (2件)
こちらのブログを見て、10年以上ぶりにミニ四駆を初め、大変参考にさせて頂いてます。
MSシャーシでつっかえ棒の為の穴拡張をしたのですが、画像のとおりフロント側から3つ目の穴を拡張したところ、つっかえ棒が入らない位置に穴がありました。(穴より大幅にフロント側につっかえ棒が来てしまう)
加工参考画像をよく確認するとどちらもVZ用のブレーキステーの画像を使用していると思いますが、MS用では軸ビスの穴の位置がフロント寄りにあると思いますので、MSの場合拡張する穴はもっとフロント寄りにした方がいいんでしょうか?
長文失礼しました。
>>APACHEさん
当ブログの閲覧及びコメントありがとうございます。
ご指摘の通りMS用の場合は軸ビスがフロント寄りにあるため よりフロント寄りに穴を加工(拡張)する必要があります。
参考になるか分かりませんが、各シャーシの加工後(穴拡張後)の画像も追加しましたので そちらも参考にしてみてください。
一点注意点を上げますと、加工後のブレーキステーの穴の位置が必ずしも正解というわけではなく、軸ビスの位置は加工過程で若干前後することがあります。
また、スラスト角によっても適切な穴の加工具合が変わったりするのでご自分のマシンに合った最適な穴拡張を実施して頂ければと思います。
幸いAPACHEさんのブレーキステーはフロント側を削る余裕があるようなので、すでに加工済みのブレーキステーもまだ生かせるかと思われます。
(ビス穴の後ろ側(リヤ側)を削りすぎる分には ほぼ影響はありませんのでご安心を)