今回はVZ・MA・MS・FM-A・ARシャーシなどに対応した2軸フロントATバンパーの作成方法を解説します。
入手しやすいパーツと基本的な工具のみを使用し、比較的簡単にできる改造でありながら精度の高い作りとなっており、完成後のフロントATバンパーは以下のような形となります。
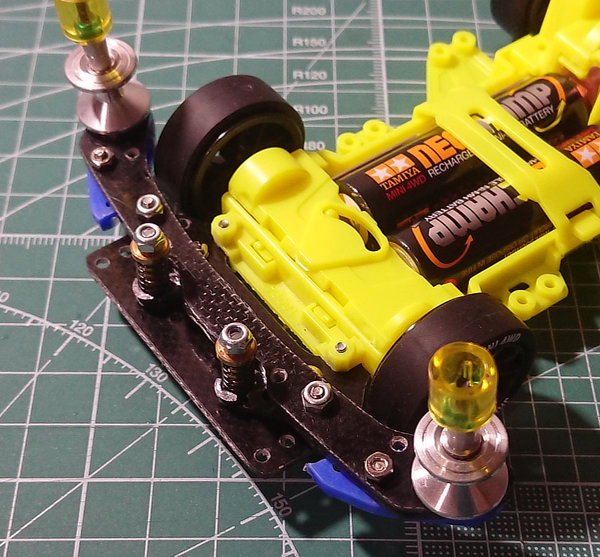
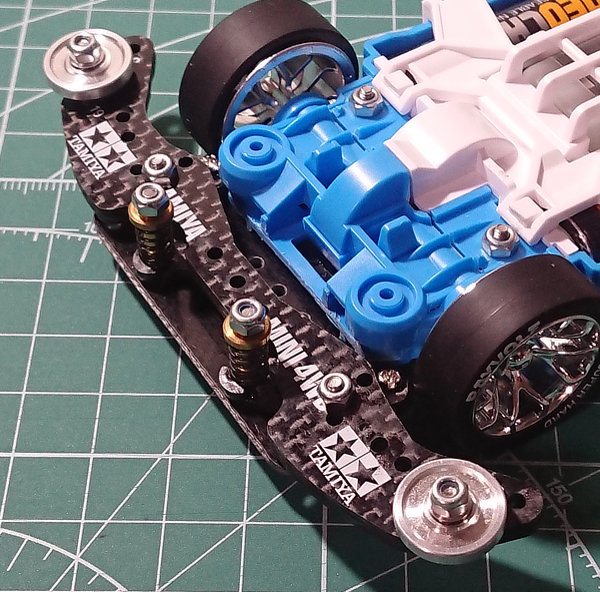
今回作成するATバンパーはリジットバンパーとなりますが、今回のフロントATバンパーの作成方法をベースとして以下の画像のATスライドダンパー及びATピボットバンパーに派生させることも可能です。
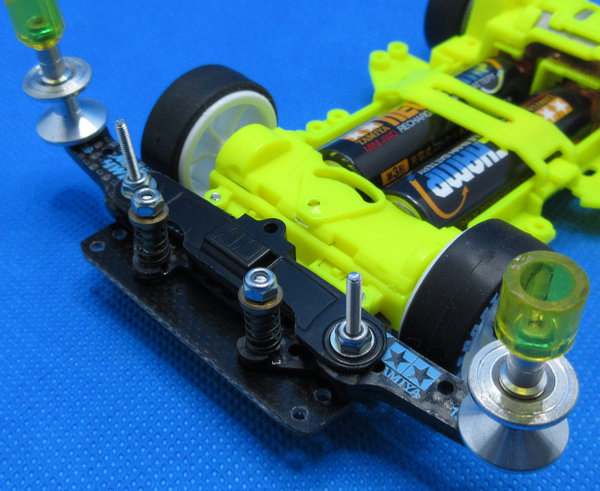
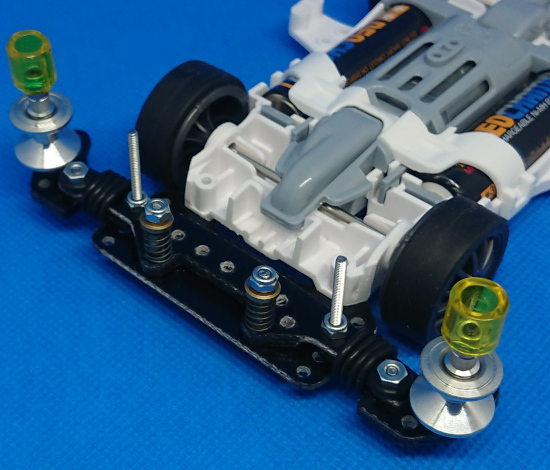
これらの派生させたバンパーについては別記事の「ATスライドダンパーの作り方」「ATピボットバンパーの作り方」にて解説しています。
また、今回のフロントATバンパーの特徴として 以下の形のフロント提灯を装着できるようになります。
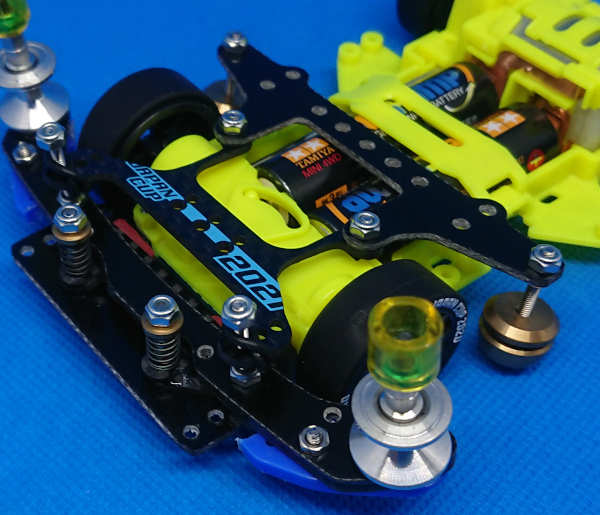
※上記 フロント提灯はFM-Aシャーシには非対応となっているのでご注意ください。
このフロント提灯の作成方法については以下の記事をご参照ください。
尚、今回の作成に必要なパーツ・工具の詳細については以下の「準備編」にて紹介しています。
シャーシの加工
フロントATバンパーの加工にあたり、シャーシ側でフロントATバンパーを設置するためのシャーシカットが必要となります。
VZ・MA・MS・FM-Aシャーシのカット方法については以下の記事にて解説しているので、本記事では省略します。
まだシャーシカット(バンパーカット)が完了していない方は以下の記事をご参照ください。
リヤブレーキステーの加工
ここではフロントATバンパーを構成するパーツの1つである リヤブレーキステー(以下 ブレーキステー)を加工方法を解説していきます。
ブレーキステーはフロントATバンパーの土台となり負荷がかかりやすいパーツなのでカーボンタイプが理想ですが、なければFRPタイプでも構いません。
ブレーキステーには、ビス穴の追加・皿ビス加工・干渉箇所の加工をおこなっていきます。
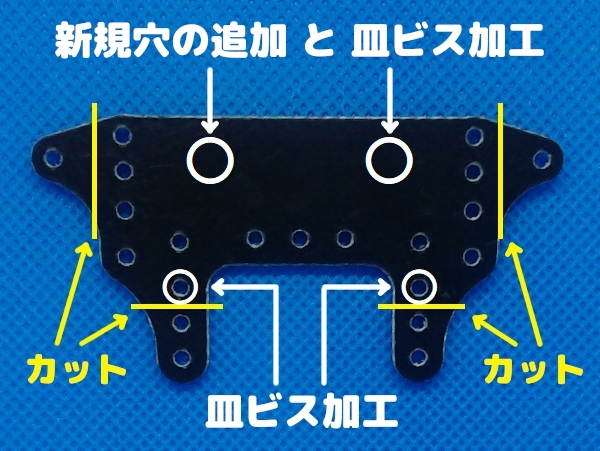
次から各箇所の詳細な加工方法を解説していきます。
ビス穴の追加
ここではブレーキステーにATバンパーを取り付けるためのビス穴の追加方法を解説していきます。
このビス穴の追加は以下のシャーシごとに穴をあける位置が異なるのでご注意ください。
尚、ビス穴の追加作業については中途半端に加工してしまうとビス穴の位置がズレ、ATバンパーの精度に支障がでることもあります。
より精度を上げるための加工方法を以下の記事の『ステー・プレート加工時の注意点』の項目で詳しく解説しているので、加工経験が浅い方は まずはこちらを一読してから作業することをおすすめします。
VZシャーシ用の穴あけ
VZシャーシ用の穴あけは 後述するMA・MSシャーシに比べてややリヤ(後ろ)寄りの位置にする必要があります。
リヤ寄りの位置にする理由として、フロント(前)寄りにしてしまうと別途取り付けるフロント提灯と適合しなくなるからで、フロント提灯を必要としない方はMA・MSシャーシ用の位置の穴あけでも問題ありません。
穴のあけ方については、カーボンマルチ強化プレートを用意して以下の穴の位置でビスとナットを使ってブレーキステーと結合させます。
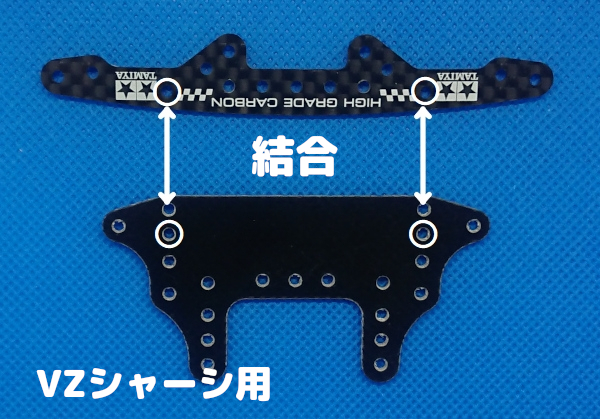
結合させたらカーボンマルチ強化プレートの既存ビス穴をガイドにして、2mmドリル刃でブレーキステーの以下の画像の丸の位置に新規穴をあけていきます。
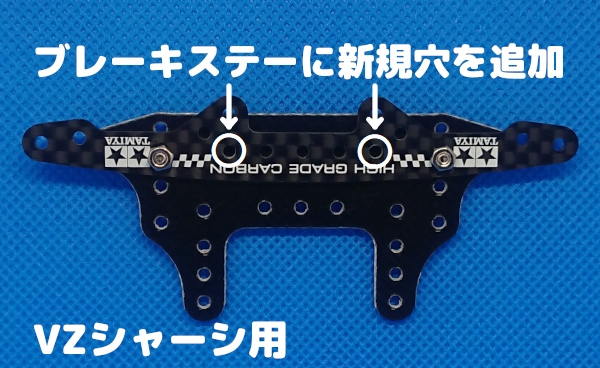
ブレーキステーに穴をあけるとドリルをあてた反対側の面にバリ(不要な出っ張り)ができていますが、この後の皿ビス加工でバリも除去できるので一旦はそのままで構いません。
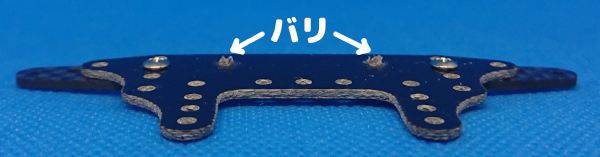
MA・MSシャーシ用の穴あけ
MA・MSシャーシ用の穴あけはVZシャーシに比べてややフロント(前)寄りの位置にします。
尚、VZシャーシでもフロント提灯が不要ということであれば、ここで解説するMA・MSシャーシ用の穴の位置でも問題ありません。
穴のあけ方については、カーボンマルチ強化プレートを用意して以下の穴の位置でビスとナットを使ってブレーキステーと結合させます。
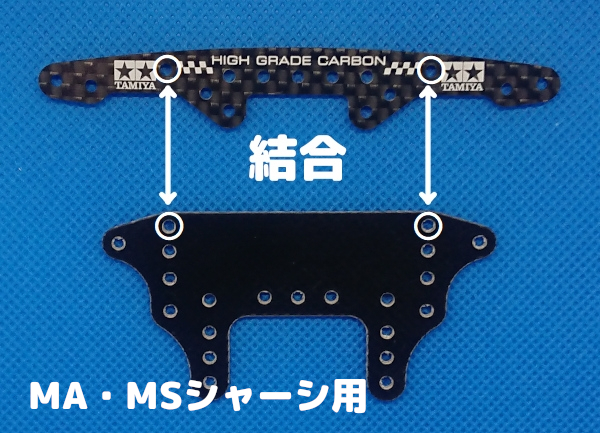
結合させたらカーボンマルチ強化プレートの既存ビス穴をガイドにして、2mmドリル刃でブレーキステーの以下の画像の丸の位置に新規穴をあけていきます。
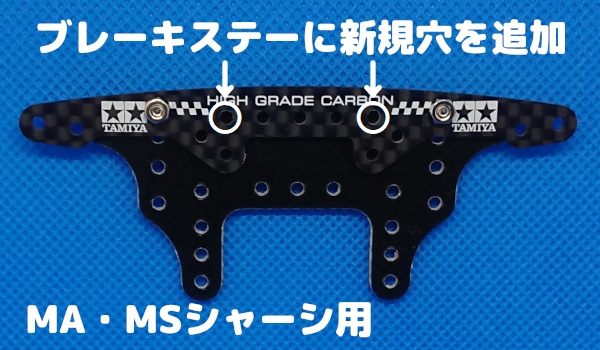
ブレーキステーに穴をあけるとドリルをあてた反対側の面にバリ(不要な出っ張り)ができていますが、この後の皿ビス加工でバリも除去できるので一旦はそのままで構いません。
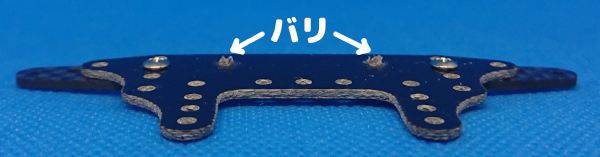
FM-Aシャーシ用の穴あけ
FM-Aシャーシ用の穴あけは、基本的に「MA・MSシャーシ」と同じ方法でおこないます。
VZシャーシ用の穴あけ方法でも駄目ではないんですが、MA・MSシャーシ用の穴あけを実施した方がATバンパーの土台となるブレーキステーの空きスペースが広く使えます。
ブレーキステーの空きスペースが広い方が、ATバンパーの加工の手間が省けたりスラスト角調整やスラスト抜け対策などのATバンパー完成後の追加加工がやり易くなるので、MA・MSシャーシ用の穴あけ加工をおすすめします。
尚、これ以降の加工方法については「VZシャーシ」「MA・MSシャーシ」のいずれかで作業方法が若干異なる箇所があり、その際は選択した方の加工方法を参考に作業を進めてください。
皿ビス加工
ビス穴の追加作業完了したら、次にシャーシ取付用のビス穴とATバンパー取付用のビス穴に皿ビス加工をしていきます。
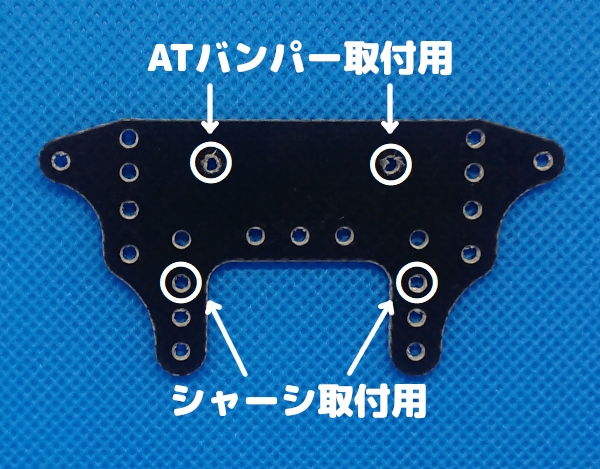
上の画像はVZシャーシ用の画像となっており、MA・MSシャーシのATバンパー取付用のビス穴の位置は若干違うのでご注意ください。
(新規であけた穴に皿ビス加工をするという理解でOKです)
皿ビス加工はリューターの皿ビス加工用ビットを使用します。
そして、ATバンパー取付用・シャーシ取付用のビス穴 計4箇所の同じ面に皿ビス加工をしていきます。
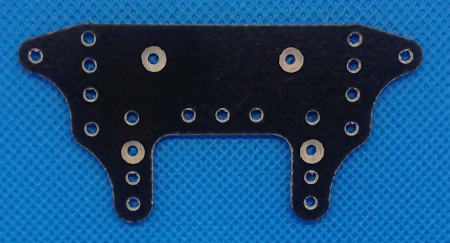
皿ビス加工する面はどちらの面でも構いませんが、バリがある面に皿ビス加工しておくとバリも取れて一石二鳥です。
干渉箇所の加工
ブレーキステーの仕上げに他のパーツと干渉する箇所を加工(カット)して整えていきます。
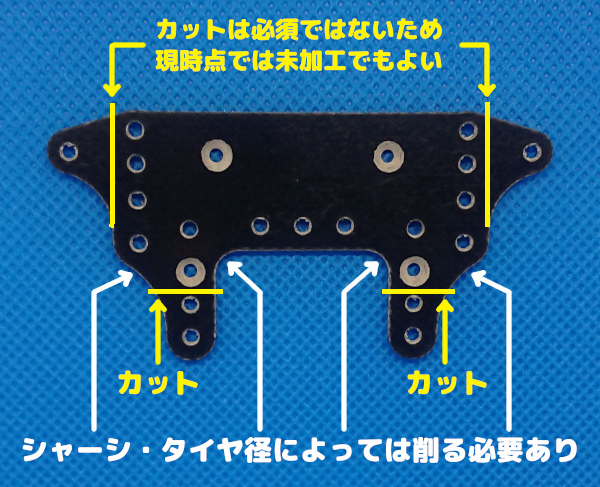
ここで上画像の加工をすべて実施してもいいんですが、両サイドのカットについては一旦保留でも構いません。
というのも両サイドは他のパーツに干渉しないケースもあり、両サイドを残しておいた方がブレーキステーの強度を保ったまま スラスト抜け対策の「つっかえ棒を付ける」加工ができるからです。
両サイドを多少残しておくことで スラスト抜け対策の「つっかえ棒を付ける」加工の際にブレーキステーの強度を保つことができます。
そのため、後に取り付けるバンパーに干渉するかしないかが分かってからの加工でも問題ないので後回しにしても構いません。
また、上画像の白矢印で示した箇所は使用するシャーシ・タイヤ径によっても加工度合いが異なり、シャーシによって削る・削らないが変わってくるので 自身の使用するシャーシに合わせて削る必要があります。
カットはリューターのダイヤモンドカッターを使用し、少し削る程度でしたらリューターの円筒形ビットを使用していきます。
以下の画像は不要箇所すべてを切り落とした後のものとなります。
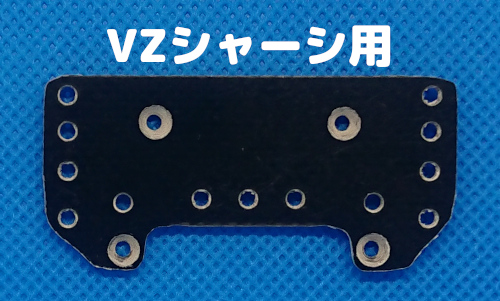
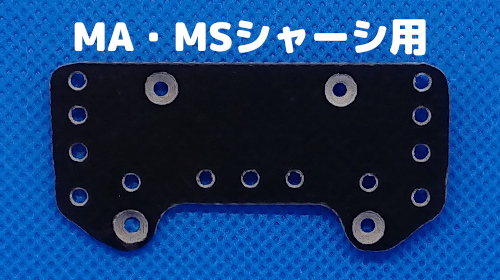
実際どのくらい削るべきか分からない場合は、まずはしっかりと強度を保てる範囲で削った状態で実際のシャーシに取り付け、シャーシ・タイヤに干渉していれば再度削るという形で少しずつ調整していきましょう。
スラスト抜け対策加工
基本的にブレーキステーの加工は上記までの手順で完成となりますが、ブレーキステーを利用したスラスト抜け対策をしたい場合は ここから追加で加工が必要となります。
ブレーキステーのスラスト抜け対策加工はこれまでの加工よりも幾分か手間がかかり精密さが求められるので、初めてフロントATバンパーを作るという方は 一旦スラスト抜け対策の加工は保留して構いません。
尚、具体的な加工方法については別記事[スラスト抜け対策方法 解説]の『つっかえ棒をつける』の項目にて解説しているので、そちらをご参照ください。
別記事[スラスト抜け対策方法 解説]の「つっかえ棒をつける」で紹介しているスラスト抜け対策を実施した場合、ブレーキステーのビス穴を拡張することになるのですが、それによりパーツ結合ビスを使ってのスラスト角度調整ができなくなります。
スラスト角調整方法詳細についてはスラスト角調整項目の『パーツ結合のビスでの調整』にて解説しています。
ただ、スラスト角の調整はこのパーツ結合ビスを使用する以外の方法もあるので、個人的にはスラスト抜け対策用にビス穴を拡張するのをおすすめします。
尚、ブレーキステーのスラスト抜け対策の具体的な加工方法については以下の記事にて解説しているので時間があれば一読頂ければと思います。
フロントステーの加工
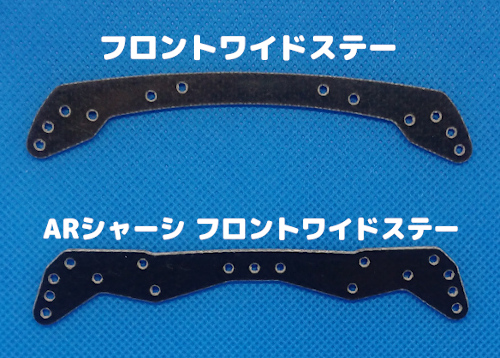
ここではフロントATバンパーを構成するパーツの1つであるフロントステーの加工方法を解説していきます。
フロントワイドステーに関しては、フロントワイドステー フルカウルミニ四駆タイプ(以下 フロントワイドステー)かARシャーシ FRPフロントワイドステー(以下 ARフロントステー)のいずれかを加工していきます。
どちらのステーを選ぶかは ご自分の技量・マシンに合った方を決めて頂ければと思います。
各ステーの特徴
どちらのステーを使用するかを選ぶために、それぞれのステーの特徴を以下にまとめました。
11mmローラーに対応していない
スラスト角の調整に手間がかかる
加工が簡単
カーボンタイプの入手が困難
ATバンパー軸とローラーの距離が長い
ほぼすべてのローラーに対応
スラスト角の調整が比較的簡単
加工にやや手間がかかる
カーボンタイプが入手しやすい
ATバンパー軸とローラーの距離が短い
次から上記の各特徴について細かく解説していきます。
対応するローラー
それぞれのステーの対応しているローラー穴が以下となります。
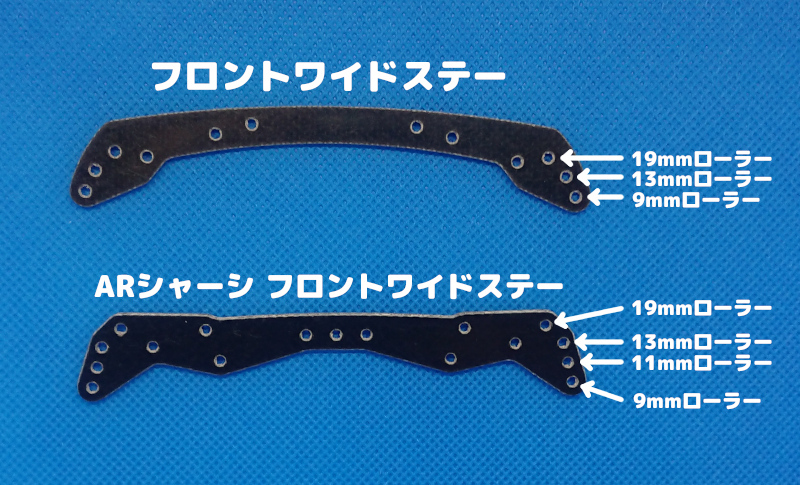
いずれのステーも大半のローラーに対応していますが11mmローラーを使用するのであればARフロントステーを使用する方がよろしいかと。
また、17mmローラー対応穴についてはいずれのステーもないので、17mmローラを使用する場合は19mm用の穴を使うか17mm用の穴を新規で作る必要があります。
スラスト角の調整
スラスト角の調整についてはARフロントステーを使用する場合はステーの形状的にスラスト角の調整が比較的簡単に行えます。
それに対してフロントワイドステーは別途スラスト角調整プレートなどを用意する必要があるため、スラスト角調整にはやや手間がかかります。
とは言えフロントワイドステーでもスラスト角を調整する方法は複数あり、ARフロントステーの方がスラスト角調整方法のバリエーションが少し増えるということだけであって それほど難易度の差があるわけではありません。
ARフロントステーならではのスラスト角の調整方法やフロントワイドステーでもできるスラスト角調整方法を「スラスト角の調整」に載せていますのそちらを内容を見て判断して頂ければと思います。
加工の手間
ステー自体の加工の手間に関してはフロントワイドステーは一部削るだけと比較的楽です。
それに対してARフロントステーは削る作業とビス穴の追加作業が必要になりフロントワイドステーに比べて やや手間がかかります。
ただ手間がかかると言ってもビス穴の追加が面倒なぐらいで他の加工作業はフロントワイドステーとさほど変わりません。
手間かどうかはこの後解説する加工方法を見て判断して頂ければと思います。
※フロント提灯が不要という方はARフロントステーの穴追加作業は不要となり、加工の手間はフロントステーと変わらなくなります。
カーボンタイプの入手について
カーボンタイプの入手については フロントワイドステーのカーボンタイプは限定品のため入手が困難であり、時期によっては定価で購入するのが難しいこともあります。
それに対してARフロントステーのカーボンタイプであるカーボンフロントワイドステーは通常品であり基本的にはいつでも購入でき、定価どころか値引き価格でも購入可能となっています。
尚、ARフロントステーはFRPタイプとカーボンタイプで若干形が異なりますが、加工方法は基本的に変わりません。
ATバンパー軸とフロントローラーの距離
ここの特徴の違いについては、ATバンパー軸とフロントローラーの距離の特性を分かっている前提で解説していきます。
距離の特性については別記事[スラスト抜け対策方法 解説]内の『ATバンパー軸とフロントローラーの位置』の項目で解説しているので、以下の内容がピンとこない場合はそちらを見て頂ければと思います。
以下の画像はATバンパー軸から13mmローラー中心の距離を比較したものとなります。
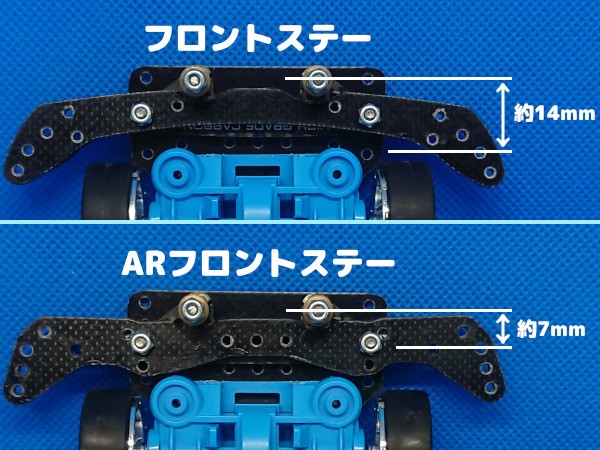
フロントワイドステーの方がARフロントステー(カーボンフロントワイドステー)に比べて軸からローラーまでの距離が倍ほどあります。
ここの距離が長い程スラスト抜けしにくくなるため フロントワイドステーの方がバンパーの安定性が高い傾向にあるということになります。
ただ、いずれもステーもATバンパーが安定する最低条件は満たしており、上記の数値の差でどのくらい安定性が変わって来るかは未知数なところもあるので そこまでシビアに考える必要はないと思われます。
とにかく安定性を求めるということであればATバンパー軸とフロントローラー距離が長いフロントワイドステーを推奨します。
特徴のまとめ
いずれのステーも一長一短になるので迷っている方は一旦以下の加工内容を確認してから判断して頂ければと思います。
どちらでも良いということで、見た目で好きな方を選ぶのもありかと思います。
また、本記事で作成するフロントワイドステー及びARフロントステーについては出来る限り破損しないように同じステーを2枚重ねて補強していきますが、本記事では補強の方法・手順の説明については省略しています。
補強方法・補強手順の詳細については以下の記事にて解説しているので、より強固なステー(バンパー)を作りたいという方はこちらもご参照ください。
フロントワイドステーの加工
ここではフロントワイドステーの加工方法を解説していきますのでARフロントステー(カーボンワイドステー)を加工する場合は「ARフロントステーの加工」をご覧ください。
フロントワイドステーは以下の加工をしていきます。
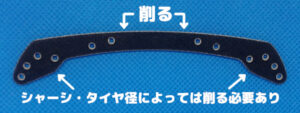
上の画像だけでは実際にどこを削るのか分かりづらいので、加工済みのブレーキステーとカーボンマルチ強化プレート(未加工でもOK)を用意し、各パーツをシャーシに取り付けた状態で干渉箇所を確認することをおすすめます。
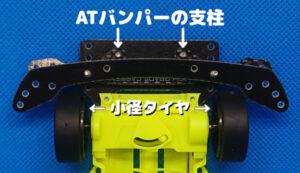
※組み立て方法については本記事の後半で解説している「仕上げ」の項目をご参照ください。
上の画像を見るとATバンパーの支柱となるビスには干渉していませんが、支柱となるビスには後に真鍮パイプ・スプリングを取り付け支柱の直径が大きくなり フロントワイドステーに干渉してしまうので削る必要があります。
またタイヤと干渉している箇所については、上の画像はVZシャーシに取り付けたケースのものであって、MA・MSシャーシ用のブレーキステーあったり ペラタイヤ加工しているものであれば干渉せず未加工のままでも問題ありません。
この段階でどこまで削ってよいのかわからなければ一旦削る作業は保留にして他のパーツを加工してから再度組み立てて干渉箇所を確認してからでも構いません。
尚、ステーを削る工具はリューターの電動リューター用ビット5本セットに付属している円柱形ビット、もしくは皿ビス加工用ビットの側面を使うと楽に加工ができます。
とりあえずVZシャーシに対応できるステーを加工しておけばMA・MSシャーシでも流用できます。
尚、今回はVZシャーシ用の加工をしており、完成したのが以下の画像のものとなります。
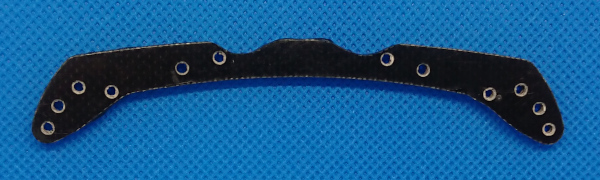
ARフロントステーの加工
ここではARフロントステー(カーボンフロントワイドステー)の加工方法を解説していきますのでフロントワイドステーを加工する場合は「フロントワイドステーの加工」をご覧ください。
ARフロントステーは以下の加工をしていきます。
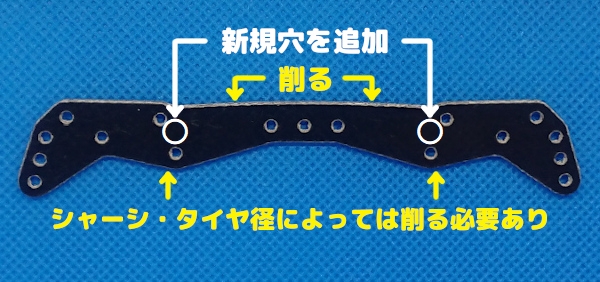
下の箇所を削る作業についてはシャーシ・タイヤ径によって異なり、削る箇所の詳細については後ほど解説していきます。
まずはARフロントステーに新規穴をあけるために、カーボンマルチ強化プレートを用意して以下のビス穴の位置でビスとナットを使い結合させます。
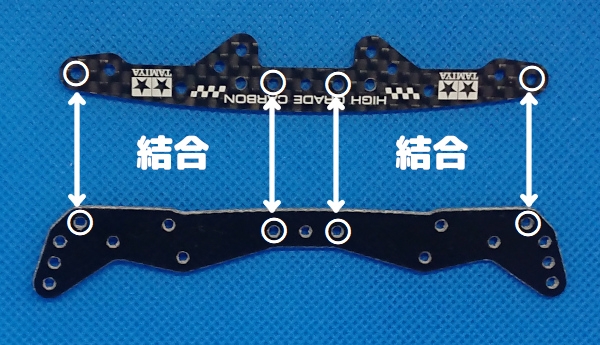
ステー・プレートを固定したらカーボンマルチ強化プレートの既存ビス穴をガイドにして、ARフロントステーの以下の箇所に2mmドリル刃を使用して新規穴をあけていきます。
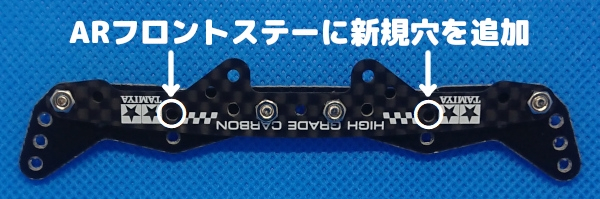
穴あけが完了したら、カーボンマルチ強化プレートを取り外して、以下の干渉する箇所を削っていきます。
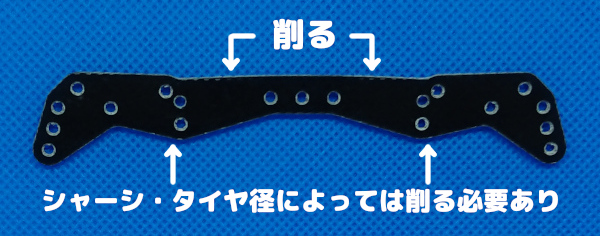
上の画像だけでは実際にどこを削るのか分かりづらいので、加工済みのブレーキステーとカーボンマルチ強化プレート(未加工でもOK)を用意し、各パーツをシャーシに取り付けた状態で干渉箇所を確認することをおすすめます。
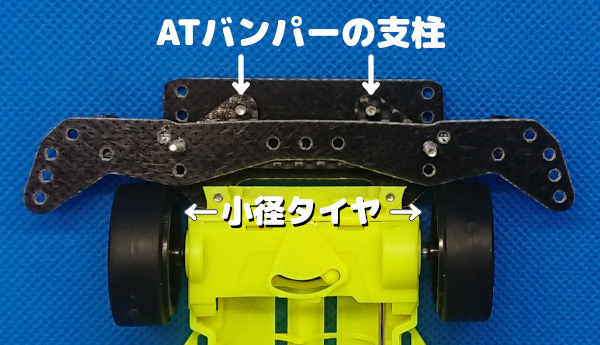
※各パーツの組み立て方法については本記事の後半で解説している「仕上げ」をご参照ください。
上の画像を見るとATバンパーの支柱となるビスには干渉していませんが、支柱となるビスには後に真鍮パイプ・スプリングを取り付け支柱の直径が大きくなり ARフロントステーに干渉してしまうので削る必要があります。
また、上の画像のタイヤと干渉している箇所については、VZシャーシに取り付けた際のパターンとなります。
このため、MA・MSシャーシ用のブレーキステーであったり・ペラタイヤ加工していれば干渉することはないので 未加工のままでも問題ありません。
現時点でどこまで削ってよいのかわからなければ、一旦削る作業は保留にして他のパーツを加工してから再度組み立てて干渉箇所を確認してからにしましょう。
尚、ステーを削る工具はリューターの電動リューター用ビット5本セットに付属している円柱形ビット、もしくは皿ビス加工用ビットの側面を使うと楽に加工ができます。
とりあえずVZシャーシに対応できるステーを加工しておけばMA・MSシャーシでも流用できるので今回はVZシャーシ用の加工を施し いずれのシャーシにも対応できるようにしています。
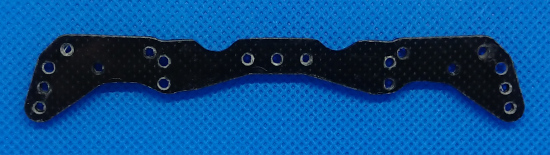
尚、カーボンフロントワイドステー(以下 カーボンワイドステー)を加工する場合もARフロントステーと同じ要領で以下のように加工していきます。
カーボンマルチ強化プレートを用意して以下のビス穴の位置でビスとナットを使い結合させます。
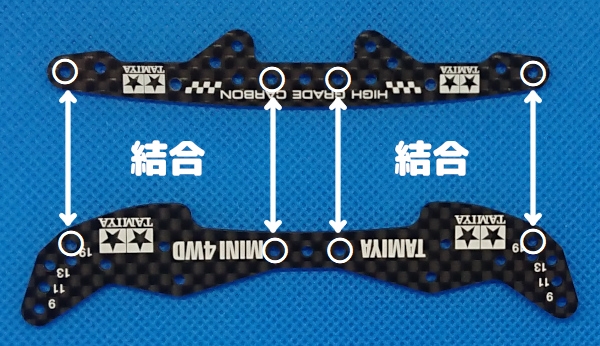
ステー・プレートを固定したらカーボンマルチ強化プレートの既存ビス穴をガイドにして、カーボンワイドステーの以下の箇所に2mmドリル刃を使用して新規穴をあけていきます。
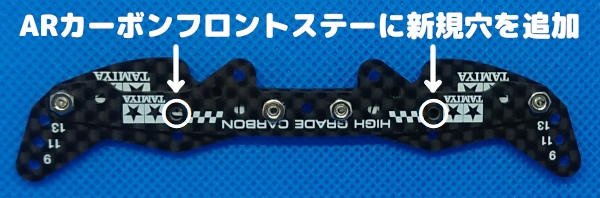
穴あけが完了したら、ARフロントステーと同様に各パーツをシャーシに取り付けた状態で干渉箇所を確認し削って完成したのが以下となります。
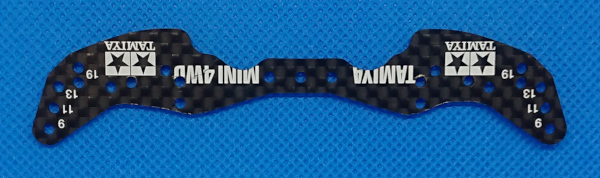
※上記のカーボンワイドステーには先程あけたビス穴以外の穴も追加されていますが、これは引っ掛かり防止用のフロントアンダーガードを固定するためのビス穴なので今回の改造とは直接関係ありません。
ARフロントステー・カーボンワイドステーについてはフロント提灯を使用する場合のみ新規穴追加作業が必要となります。
フロント提灯を使用しない場合は、既存ビス穴を使ってパーツ結合できるので新規穴を追加する必要はありません。
現時点でフロント提灯を使用するかどうか決まっていないということであれば、新規穴をあけるに越したことはないので、とりあえずは新規穴をあけておくことをおすすめします。
マルチプレートの加工
ここではフロントATバンパーを構成するパーツの1つであるスーパーXシャーシ カーボンマルチ強化プレート(以下 マルチプレート)の加工方法を解説していきます。
マルチプレートはフロントATバンパーの可動部でもあり摩耗が激しいパーツであるためカーボンタイプがおすすめです。
ただし、カーボンタイプは限定商品ということもあり、時期によっては入手困難なこともあるので、入手できない場合は「スーパーXシャーシ・FRPマルチプレート」で構いません。
そして、マルチプレートの加工概要は以下となります。
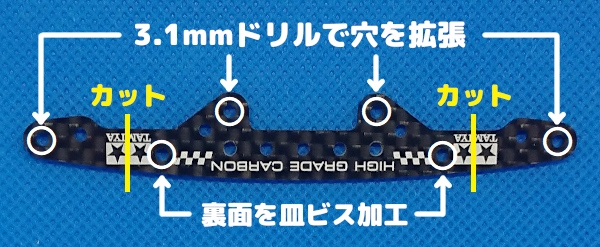
※マルチプレートの加工内容はどのシャーシも共通であるため、シャーシ毎での加工の違いはありません。
次から各加工の詳細を解説していきます。
穴の拡張・ヤスリがけ・皿ビス加工
ここではマルチプレートの穴の拡張・ヤスリがけ・皿ビス加工方法を解説していきます。
穴の拡張
まずは穴の拡張方法から解説していきますが、穴の拡張が必要となる理由は以下となります。
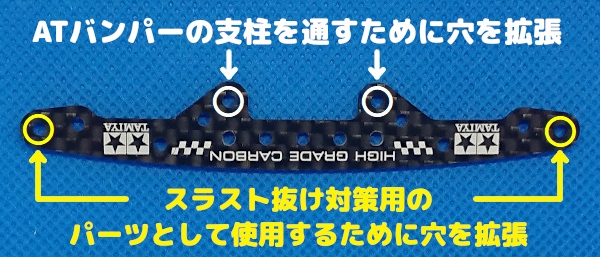
上画像の内容を補足説明すると中央寄り2つのビス穴はATバンパー支柱を通す箇所となるので穴の拡張が必要になります。
また、両端2つのビス穴は、後に加工するスラスト抜け防止用のパーツとして使用し、使用の際には3.1mの穴があいてることが条件となるため穴の拡張が必要になります。
スラスト抜け防止用の箇所については後回しにしても構いませんが、この段階でやっておいた方が後々楽になることと、ATバンパー支柱用の穴加工のついでにできるので、一緒にやっておくことを推奨します。
穴の拡張はいずれも3.1mmドリル刃を使っていきます。
もし3.1mmドリル刃を所持していない場合は、加工手順は増えますが3.0mmドリル刃でも同じサイズの穴をあけることが可能です。
(3.0mmドリル刃は100均で購入可能です)
ただし3.0mドリル刃だけを通した状態では穴の幅がやや狭く、追加で電動リューター用ビット5本セットに付属している円柱形ビットで穴を拡張する必要があります。

3.0mmドリル刃で拡張した後は、少々面倒ですが すぐに円柱形ビットを使わず 一旦皿ビス加工ビットで3.0mmに拡張した円の周りをほんの少しだけ削って円の外側に溝を作ります。
そして、その溝をガイドに円柱形ビットを使って穴をさらに拡張させていきます。
こうすることで3.1mmドリル刃を使った時とほぼほぼ同じサイズの円にすることが可能になります。
ヤスリがけ
穴の拡張が完了したら、拡張作業で出来たバリを取るのと 後ほど実施するスラスト抜け対策加工の準備として以下の箇所をヤスリがけしていきます。
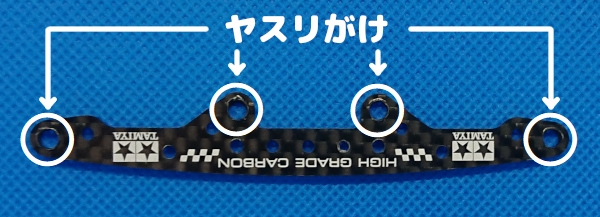
ヤスリがけに使用する工具は板ヤスリが推奨ですが、板ヤスリがなければ棒ヤスリ・紙ヤスリでも構いません。
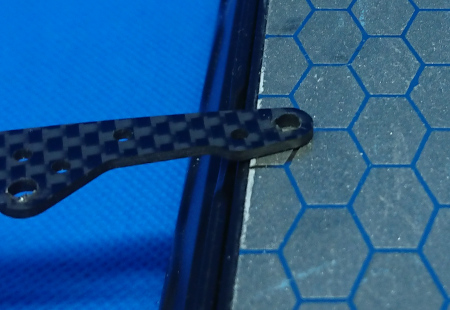
ここでのヤスリがけは穴拡張作業で出来たバリを取るのはもちろんのこと、それ以外に後のスラスト抜け対策加工作業で実施するパーツ同士の接着をしやすくするための効果があります。
このため、表面のコーティングを取り除く程度削ればOKで、ヤスリがけは片面(表面)だけに行い、中央部分2箇所のヤスリがけは穴周りの上半分だけでOKです。
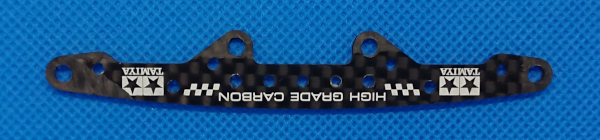
(裏面にバリがあれば そこだけはヤスリで除去しておきましょう)
※ここの加工はスラスト抜け対策のためであり、何故この加工が必要なのかは別記事[スラスト抜け対策方法 解説]内の『スプリングの圧力を均等にする』の項目で解説しています。
そこを一読し不要と判断したのであれば、ここの加工作業は飛ばして次の「干渉箇所のカット」に進んでもらって構いません。
また、上の画像はヤスリがけした後の状態になりますが、中央部分の右側の穴周りは接着時に使用する上半分だけヤスリがけをした状態となっています。
(左側は穴の周り全体をヤスリがけしてしまいましたが、これはこれで特に問題はないので、このままマルチプレートは継続して使用していきます)
両サイドについても穴周りの外側半分を削るだけでもOKですが、広く削ってもまったく問題ないので、大雑把に削ってもらって構いません。
どの範囲までヤスリがけしていいのか分からない場合はこの後のスラスト抜け対策加工にて加工必要箇所を確認して頂ければと思います。
皿ビス加工
「4箇所の穴の拡張及びヤスリがけ」が完了したら、次にマルチプレートとフロントステーを結合させるために使用するビス穴に皿ビス加工をしてきます。
尚、このビス穴を使ってスラスト角の調整もしくはスラスト抜け対策を行う場合は皿ビス加工は不要です。
※スラスト抜け対策の加工方法詳細については別記事[スラスト抜け対策方法 解説]の『つっかえ棒を付ける』の項目にて解説しております。
現時点でどうしていいか分からない場合は、一旦皿ビス加工は保留として後回しでも構いません。
(皿ビス加工を実施した場合でもスラスト角の調整・スラスト抜け対策は可能なので、皿ビス加工をしてしまっても構いません)
ここでは該当のビス穴をスラスト角の調整・スラスト抜け対策としては使用しない前提で以下の箇所を皿ビス加工していきます。
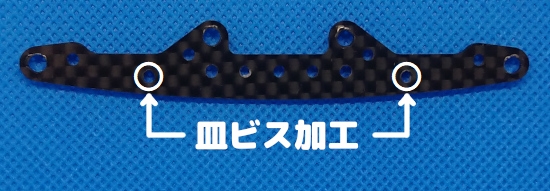
今回の加工では文字・ロゴがプリントされている面を表面としているため、無地の方を裏面として こちらに皿ビス加工をしていきます。
逆に無地の方を表面にしたいということであれば文字・ロゴがプリントされている面に皿ビス加工をしていきます。
尚、フロント提灯は使用せず、ARフロントステー(カーボンワイドステー)を使用する場合は以下の箇所を皿ビス加工して 以下のビス穴を使用することでARフロントステー(カーボンワイドステー)の穴追加作業を省くことができます。
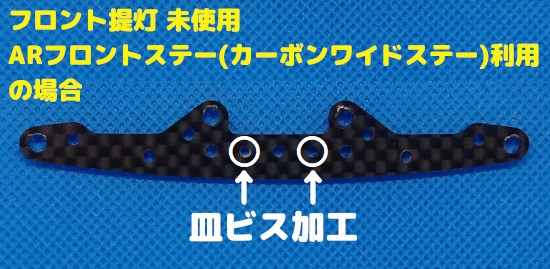
どちらのビス穴を使用するのかまだ決まっていない場合はとりあえず上記の4箇所すべて皿ビス加工しても構いません。
(余計な所を皿ビス加工したからといってATバンパーの可動に影響することはありませんのでご安心を)
干渉箇所のカット
マルチプレートを以下の順番でリューターのダイヤモンドカッターにて切断していきます。
※ダイヤモンドカッターがなければクラフトのこでカットしても構いません。
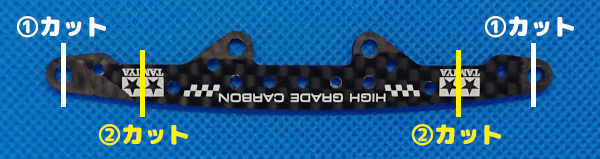
上の順番を無視して内側(②)から切断しても問題ありませんが、外側(①)を後回しにすると後々①の切断作業がやりづらくなるので、上記の順番を推奨します。
次から上記の順番の手順で加工方法を解説していきます。
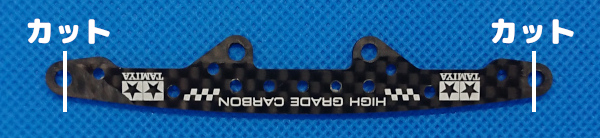
最初のカットでは切断後の端材を後に使用することを想定して、その端材が半円程残るようにしておきます。
そのため、ダイヤモンドカッターをあてる箇所はビス穴の円の中心部分というよりも、中心よりも少しマルチプレートの内側寄りの位置をカットラインにすると半円の形として切り落とすことができます。
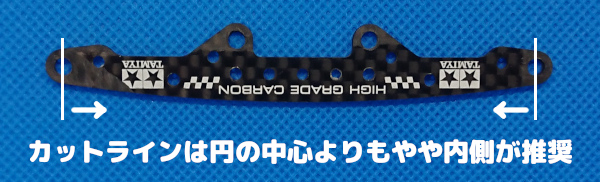
切り取った端材は後の「スラスト抜け対策加工」で使用するので、無くさないよう大切に保管しておきましょう。

両端のカットが完了したら次に内側の干渉箇所をカットしていきます。
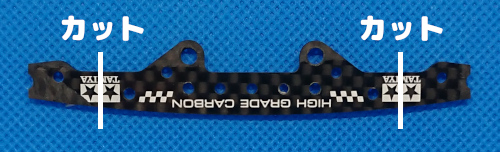
使用するローラーによってはここをカットしなくても干渉しませんが、引っ掛かり防止対策をする際に邪魔になってくる箇所でもあるので、この段階でカットしておくことを推奨します。
干渉箇所をカットしたら カット箇所を整えていきますがこの箇所は後々フロントステーに下に隠れて見えなくなることと、整えなくてもATバンパー可動には影響してこないので、整えるか整えないかはお好みで構いません。
整える場合はリューターの円柱形ビットか皿ビス加工ビスの側面を使うと楽の作業ができるのでおすすめです。
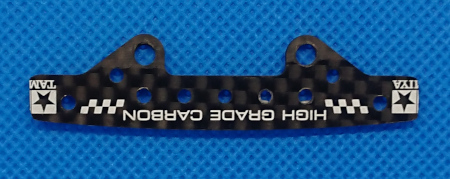
この段階でマルチプレートの大枠の形は完成となり、これ以降はATバンパーとしての機能を上げるための加工をしていきます。
可動の調整
ここではATバンパーの効きを良くするために、以下のATバンパー支柱を通す穴を加工していきます。
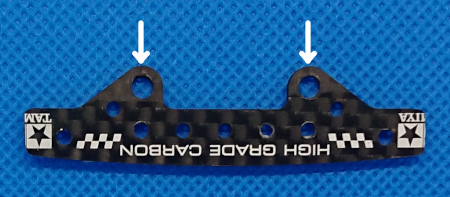
上の画像の矢印で示した穴は「穴の拡張」のところですでに3.1mmドリル刃で穴を拡張していますが、この状態だとATバンパーの支柱は通せるものの、その支柱に対して穴がピッタリすぎるのでマルチプレートがスムーズに可動しません。
そこでマルチプレートをスムーズに可動させるため更なる穴の拡張が必要になるわけですが、どう可動させるか分からないと加工を失敗してしまう可能性もあるので、加工方法の解説の前にマルチプレートをどのように可動させるのか見ていきましょう。
まず、デフォルト時(ATバンパーが可動していない状態)のマルチプレートの状態は以下となります。
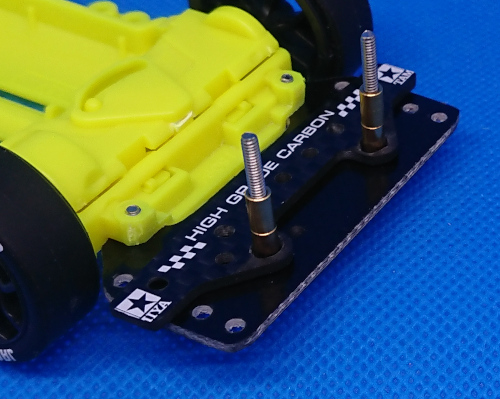
そして、ATバンパーがスムーズに動くためには上の画像の状態から以下の3方向への可動が必要となります。
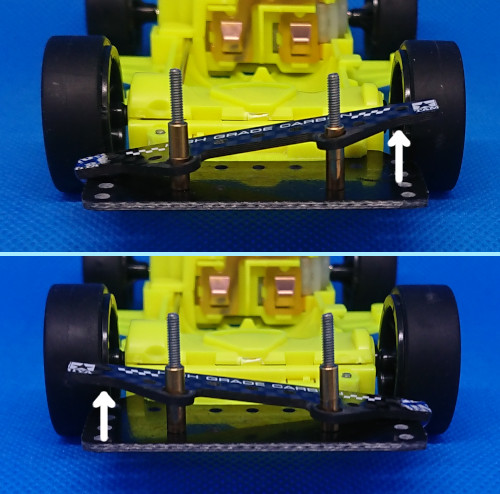
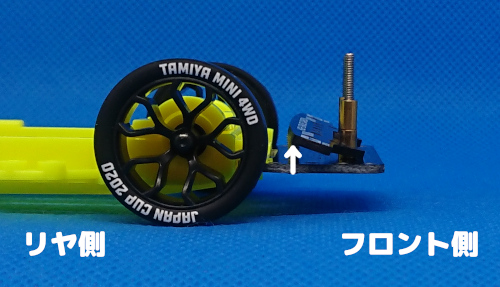
※最後の画像の可動域についてはATバンパーの可動にも必要ですが、それ以外にフロント提灯との連動動作やATバンパーにスラスト角を付ける場合にも必須となるためにしっかり対処していきたい可動域となります。
以上がATバンパーの可動に必要な3方向の動きとなります。
厳密には3方向というよりも上の画像の矢印で示した箇所の範囲全体で可動させるわけですが、上記3箇所の方向への可動を意識しておけば問題ないかと思われます。
そして上の画像のように可動させるための更なる穴の拡張作業では3.1mmドリル刃を使用します。
(3.1mmドリル刃がない場合は3.0mmドリル刃でOKです)
ここでの加工作業の注意点として、ドリル刃の回転速度を早くしすぎないようにしましょう。
ドリル刃の回転速度が速すぎると、必要以上に削れてしまうことがあり、削り過ぎて穴が広がりすぎるとバンパーがガタついてしまうことがあります。
そうならないためにもできるだけゆっくりと回転させながら慎重におこなうのが望ましく、電動ドリルよりも回転速度の融通が利く手動での作業がおすすめです。
ミニ四駆ドライバーPROなどのドリルビットを装着できる工具があれば、それに3.1mmドリル刃を装着すれば手動での作業が可能となります。

尚、電動ドリルでも回転速度調整が可能なものであればそちらでも構いません。
当サイトで紹介している小型 電動ドライバーであれば回転速度の調整はできませんが 回転速度も速すぎるということもなほどよく穴の拡張ができるのでこちらもおすすめです。
ドリル刃のあて方については先程の可動を想定した向きで、以下の画像のようにマルチプレートを傾けながら削っていきます。
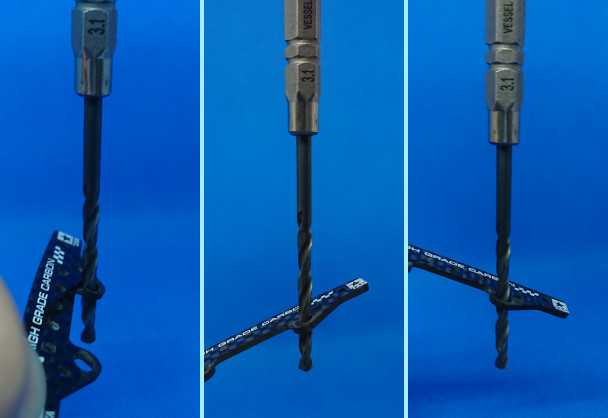
上記のようにドリル刃で拡張するのが最もメジャーな方法となりますが、個人的におすすめな加工工具は電動リューター用ビット5本セットに付属している円柱形ビットです。

使い方はドリル刃と同じ要領となりますが、リュータービットの場合はリューターを起動させた状態でマルチプレートを傾けるだけで簡単に削ることができます。
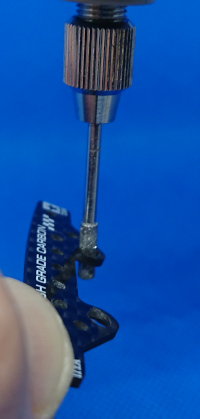
それ以外の工具では直径3mm程の丸型・半丸(半円)型の棒ヤスリでも加工可能で、手頃なものとして100円ショップで購入できる以下のやすりセットはおすすめです。
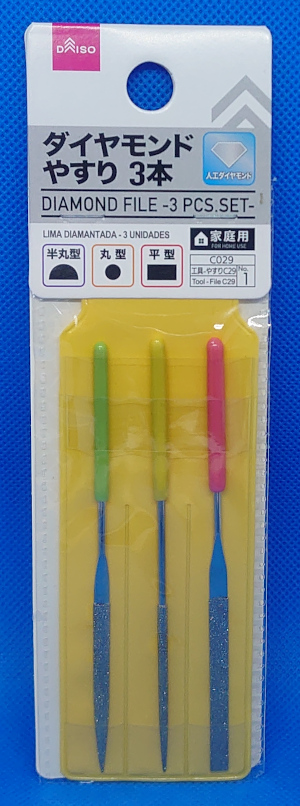
上記3本セットの半丸型は、いい具合に支柱穴を削るのに適しています。
そして、マルチプレートをどのくらいの角度を付けて削るかは、ご自身の可動させたい範囲によって変わってきます。
どのくらい削ってよいか分からない場合は一旦ここの作業は保留にして、実際に各パーツを結合させシャーシに取り付けて可動を確認してからでも構いません。
削りすぎるとATバンパーがガタついてしまう
削れば削る程 可動はスムーズになりますが、削りすぎるとATバンパーがガタつき バンパーとしての機能が損なわれてしまいます。
特にリュータービットで削る場合は、あっという間に削れてしまうのでマルチプレートを傾ける際は慎重におこなっていきましょう。
この可動調整の加工は取り返しの付かない要素でもあるため、初めてATバンパーを加工するという方はATバンパー全体の構成が出来てから作業することをおすすめします。
くれぐれもどのくらい削るか分からず適当に削ることだけはないように注意しましょう。
スラスト抜け対策加工
ここではスラスト抜け対策となる加工方法を解説していきます。
まず、ここで紹介する「スラスト抜け対策加工」については必須作業ではないので、実施しなくてもフロントATバンパーは作成可能です。
特に初めてフロントATバンパーを作るという方は一旦ここの作業は飛ばして、後回しにする もしくは作成に慣れてきてから取り掛かっても構いません。
何故この加工が必要なのかは別記事[スラスト抜け対策方法 解説]内の『スプリングの圧力を均等にする』の項目で解説しているので、そちらを一読し必要であると判断した場合のみの加工で構いません。
そして、ここでは「干渉箇所のカット」で切り取った以下のマルチプレート端材を使用していきます。
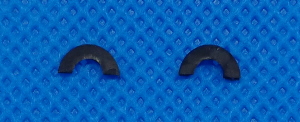
この状態から100~150度ぐらいの扇形になるように削っていきます。
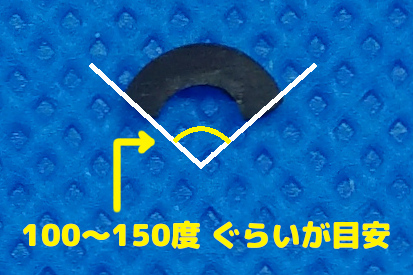
この角度については、半円(180度)の形のままだとスプリングが真ん中(フロント・リヤの中間)にあたり フロント側へのスプリング圧力がやや足りなくなります。
逆に円を小さくしすぎる(100度未満)と可動を繰り返した時にスプリングが追加したマルチプレート端材にうまく乗らずフロント側のスプリング圧力がほぼないに等しい状態になってしまいます。
これらのことから、それらの間を取って100度~150度ぐらいの扇形がベストという判断です。
そして、扇形に削る作業については、細かいパーツでもあるので板ヤスリか紙ヤスリを使うことを推奨します。
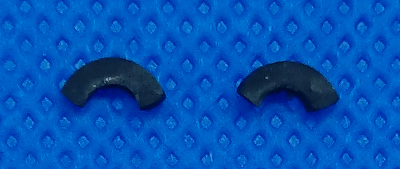
端材の加工が完了したら次に、このマルチプレート端材をマルチプレートに取り付ける準備をします。
まずシャーシを用意して、シャーシにブレーキステーとビスを取り付けます。
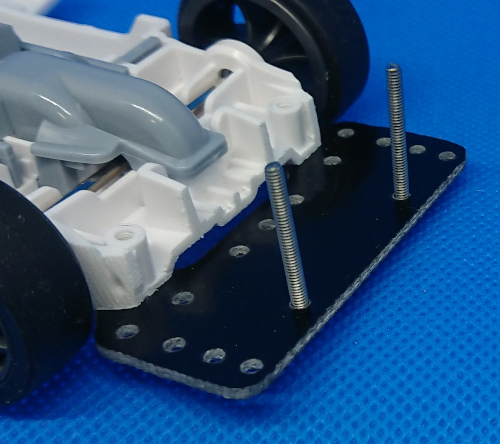
※どのように組み立ててよいか分からない方は「仕上げ」の項目をご参照ください。
ここで2段アルミローラー用5mmパイプ(以下 真鍮パイプ)の周りにマルチテープを貼ります。
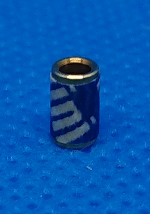
こうすることでこの後の接着作業で接着剤がはみ出て真鍮パイプに直接付くことを防げますし、仮に接着剤がついてもテープをはがすだけでOKなので、多少接着剤がはみ出ても問題ありません。
ビスにテープを貼った真鍮パイプを取り付けます。
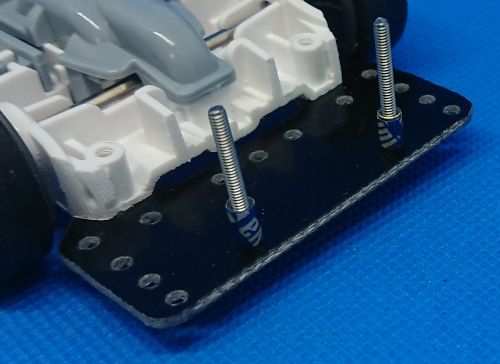
更に加工済みのマルチプレートを以下の画像のようにセットします。
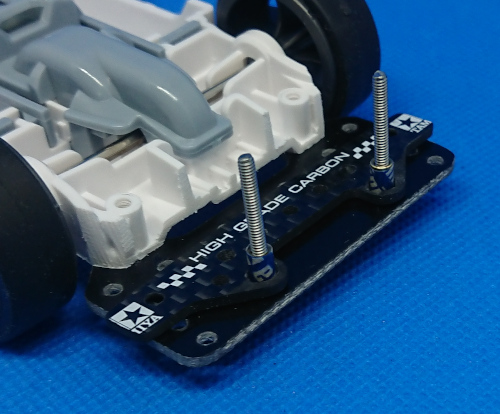
マルチプレートのATバンパー軸穴のフロント側周辺に接着剤をつけていきます。
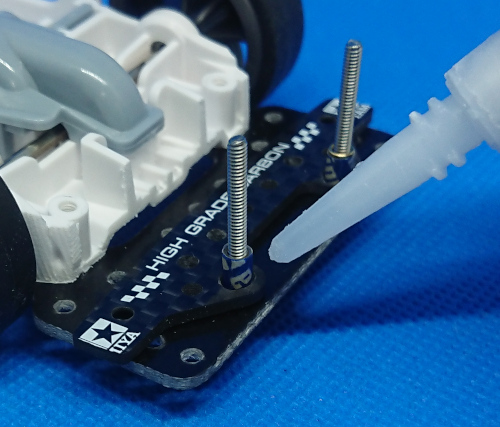
※上の画像では瞬間接着剤を使用していますが、瞬間接着剤で固定すると走行中に強い衝撃を受けた際に取れてしまうことが多々あるので、以下のような粘りっ気があり粘着力が強い接着剤を推奨します。
接着剤をつけたらマルチプレート端材のヤスリがけした面を地面に向けてピンセットでつまみ
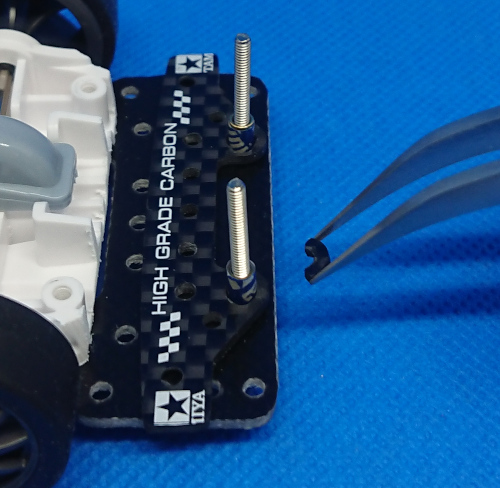
真鍮パイプをガイドにしながらマルチプレートに載せて接着させます。
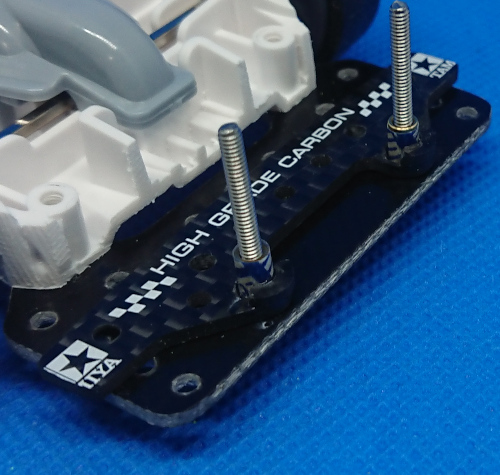
ここで接着剤がはみ出て、真鍮パイプのテープに接着剤が付着した場合、接着剤が完全に乾燥してしまうとマルチプレートにテープがこびりついてしまい後々剥がすのが面倒になります。
このため、できる限り早い段階でマルチプレートと真鍮パイプを切り離しておくことを推奨します。
ただ、真鍮パイプを外した拍子にマルチプレート端材まで外れてしまうということもあるので、真鍮パイプに接着剤が付着した場合は以下の画像のようにビスを真鍮パイプに差して左右に揺らしながら外す方法がおすすめです。
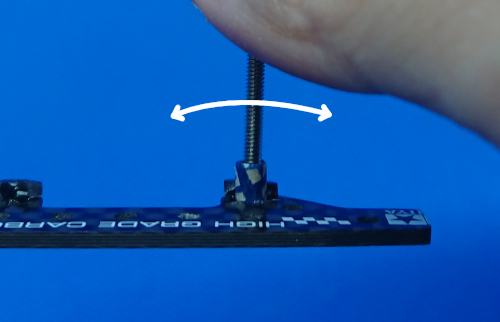
そして最後に、追加したマルチプレート端材を より接着させるために側面にも接着剤をつけていきます。
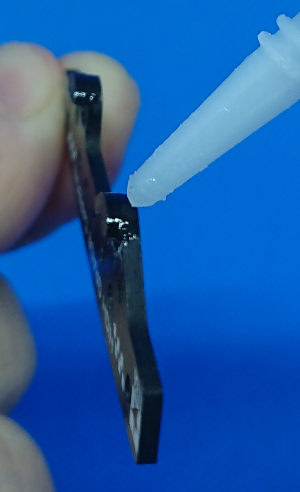
ここに付ける接着剤は、可能であれば少しサラサラめのウェーブ瞬間接着剤あたりがおすすめです。
これだけのためにサラサラの接着剤を用意する必要はありませんが、先ほど紹介したジェル状の強力瞬間接着剤だと白化現象が起き 見た目が結構白くなってしまうので、見た目にこだわる人は使い分けた方が良いかと。
接着剤を付けたら、あとは接着剤が乾燥するのを待ち、完成です。
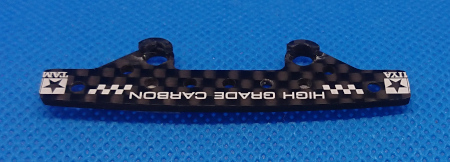
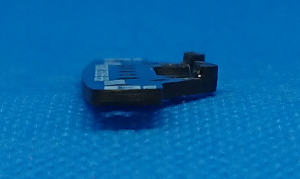
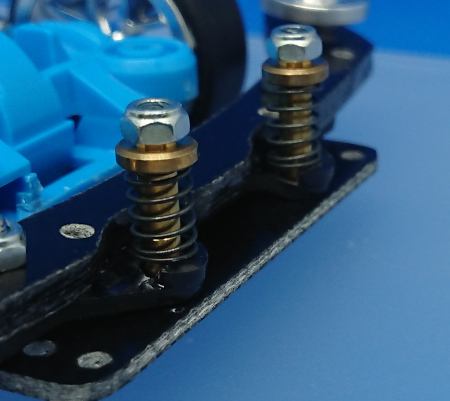
尚、何もガイドなしで直接マルチプレートに接着できる自信があるという方は上記のようにブレーキステーや真鍮パイプを用意せずに直接くっつけてもOKです。
可動時に端材が干渉する可能性がある
マルチプレート端材の円が180度に近づくにつれ、ATバンパーが可動した時に接着した端材がATバンパー支柱に干渉してしまいATバンパーの可動の妨げになることがあります。
その場合は「可動の調整」での加工と同じ要領で3.1mmドリル刃かリューターの円柱型ビットで削っていきます。
ただし、ドリル刃で削る場合はパーツに結構な負担がかかり 接着した端材が取れてしまうことがあるので、個人的にはパーツへの負担が少ない円柱型ビットでの作業がおすすめです。
円柱型ビットであれば端材だけピンポイントで削れ 余計な所を削らずに済みます。
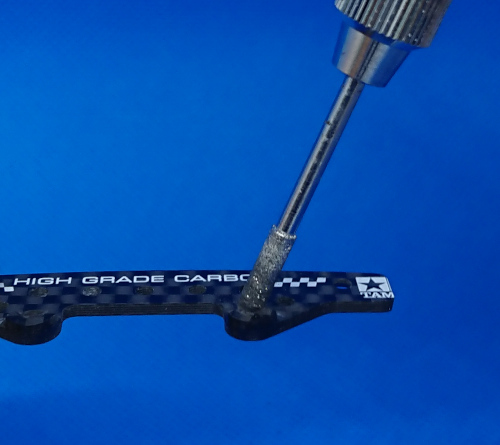
また、上のような円柱型ビットがないということであれば、「可動の調整」の所で紹介した丸型・半丸型(半円型)の棒ヤスリがおすすめです。
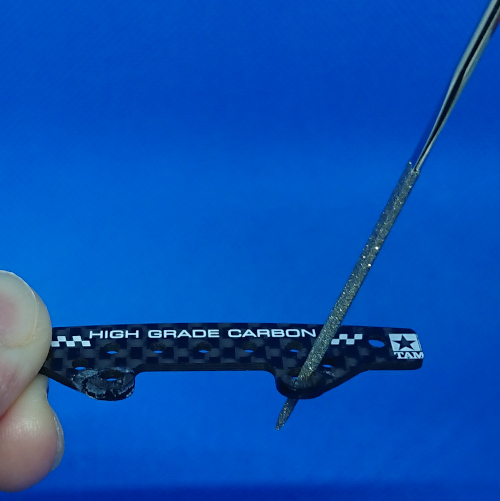
※上の画像の棒ヤスリは100円ショップで購入できるやすり3本セットの半丸型のものとなります。
以上がスラスト抜け対策加工の解説となりますが、この箇所に端材を取り付ける理由・意味については以下の記事にて詳細を解説しているので、気になる方は一読頂ければと思います。
スラスト角の調整
ここではスラスト角の調整方法について解説していきます。
スラスト角の調整については様々な方法があり、メジャーな方法だとスラスト角調整プレートを自作して取り付けるという方法があります。
今回はスラスト角調整プレートなしでフロントATバンパーにスラスト角を付ける方法を解説していきます。
※機会があればスラスト角調整プレートの作り方も本記事とは別に紹介しようと思います。
パーツ結合のビスでの調整
マルチプレートとフロントステー間の結合で使用する皿ビス加工したマルチプレートのビス穴を使ってスラスト角を調整していきます。
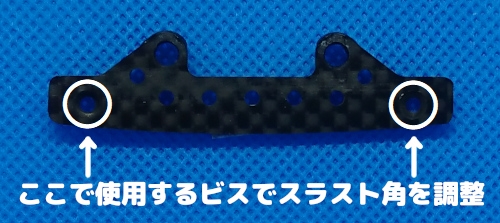
皿ビス加工をした穴ということで鍋ビスを取り付けると窪みにはまってビスが安定して設置できなくなりますが、小ワッシャー・大ワッシャーを間に挟むことで皿ビス加工の窪みも関係なくなるので、すでに皿ビス加工済みでもしっかりとビスを固定することができます。
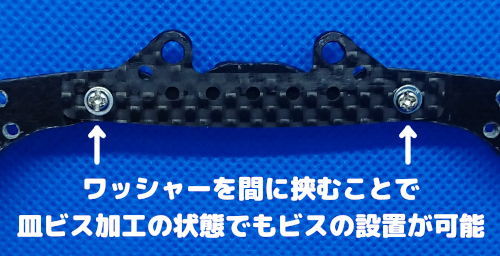
そしてここで使用するワッシャーの厚み(小か大か)や数量を変更してスラスト角の微調整をおこなっていきます。
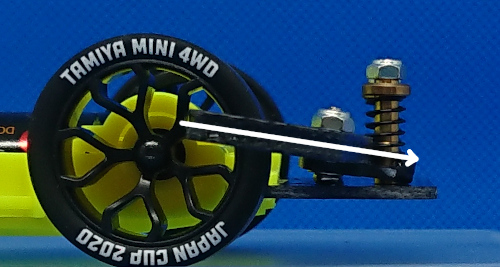
このスラスト角の調整方法はどのシャーシ・どのプレートタイプでも対応可能で最もオーソドックスで手法となります。
「つっかえ棒をつける」スラスト抜け対策を実施した場合、この方法は使えない。
別記事[スラスト抜け対策方法 解説]の「つっかえ棒をつける」で紹介しているスラスト抜け対策を実施した場合、パーツ結合のビスがブレーキステーを貫通する形となります。
そのためスラスト抜け対策用にブレーキステーを加工した場合は、上記で紹介したスラスト角の調整方法は使えなくなります。
このスラスト角の調整を取るか、スラスト抜け対策を取るかは、両方の加工方法を確認した上で判断頂ければと思います。
尚、スラスト角度を調整する方法は様々あるので、個人的にはスラスト抜け対策用にブレーキステーを拡張することをおすすめします。
そして、次からは各ステー毎に別のスラスト角調整方法を解説していきます。
ARフロントステーの場合
ステー比較の所でも話しましたが、ARフロントステー(カーボンワイドステー)の方がフロントワイドステーに比べてスラスト角調整方法のバリエーションが豊富です。
バリエーションが豊富な理由として、マルチプレートと結合した際にできる以下の画像のスペースを利用してスラスト角の調整が可能となります。
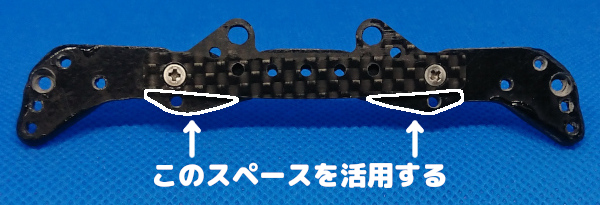
ARフロントステー自体はマルチプレートの上に取り付けるので、1.5mmのプレートを1枚挟むことでフラットになります。
さらにそのプレートのところにローラー角度調整プレートセットなどの何らかのパーツを追加すれば その追加したパーツ分の高さが増しスラスト角をつけることができます。
追加パーツを取り付けるのはARフロントステー側かブレーキステー側のどちらでも良く、今回はMA・MSシャーシでできるスラスト角の調整方法の1例を紹介します。
まず、マルチプレートの加工作業で出た端材を以下の形に加工します。
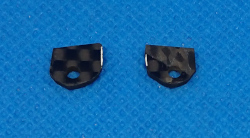
これにビス・ナット・1.5mmスペーサーを追加してブレーキステーの既存ビス穴に設置します。
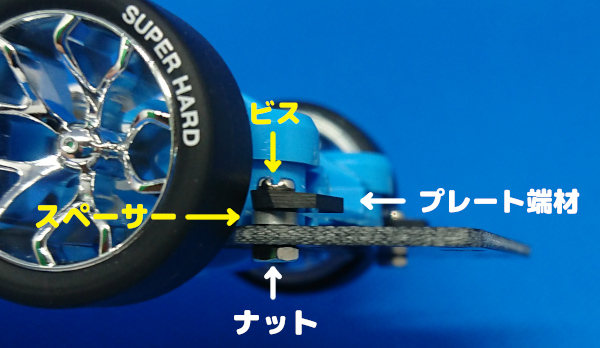
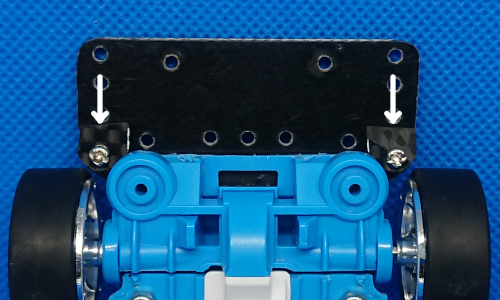
この状態で組み立てたバンパーを乗せると、冒頭で紹介したARフロントステーの空きスペースに丁度当たり、ATバンパーにスラスト角を付けることができます。
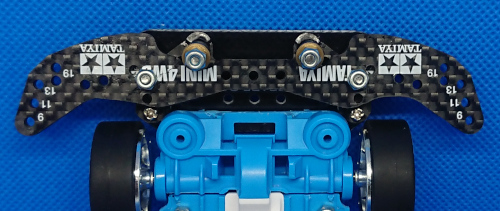
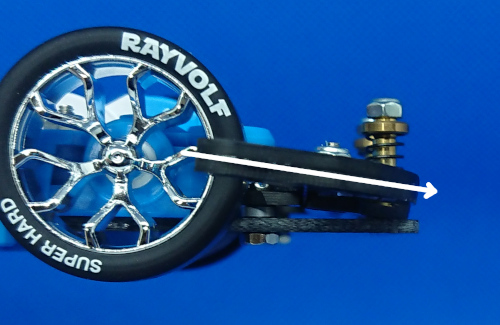
ただ上記の方法はブレーキステーの空きスペースが比較的広いMA・MSシャーシのみで可能で、ブレーキステーの空きスペースが狭いVZシャーシでは使用できません。
VZシャーシの場合は以下のようにトラスビス・ナット・スペーサー・小ワッシャーなどを、ブレーキステーの既存ビス穴に設置することによりスラスト角を付けることが可能です。
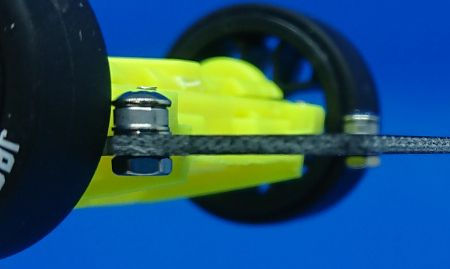
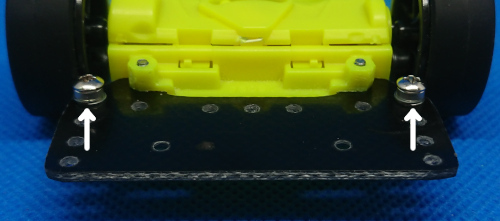
また、VZシャーシを所有していて且つARフロントステーを使用する場合のみ使える方法になりますが、以下の方法でスラスト角を調整することも可能です。
まず、VZシャーシ切断の際に余った端材を以下のように加工します。
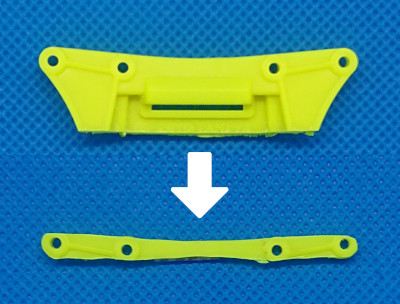
そして加工した端材とARフロントステーを結合させます。
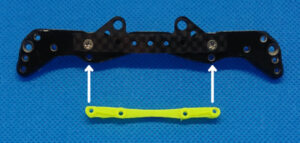
※ただし、結合させるためにはマルチプレートも少し削る必要があります。
VZシャーシの端材はビス止めできるのでナットなしで端材を固定することができます。
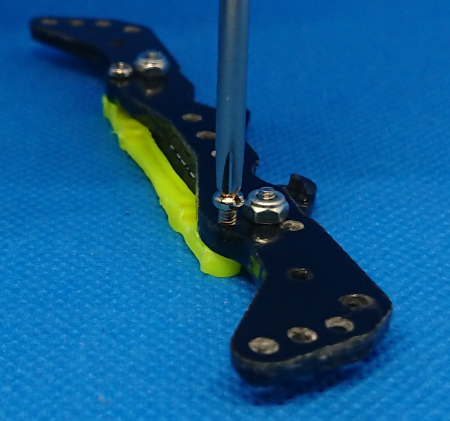
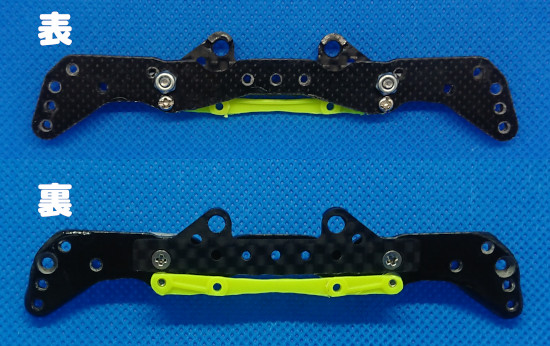
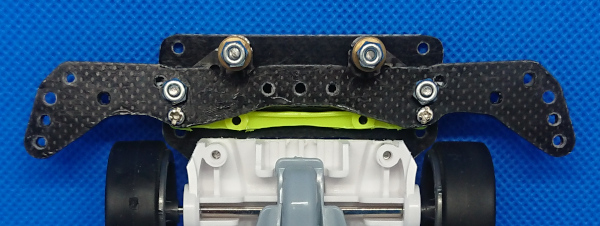
これでATバンパーにスラスト角が付いた状態になるので、あとはそのままシャーシにセットして完了です。
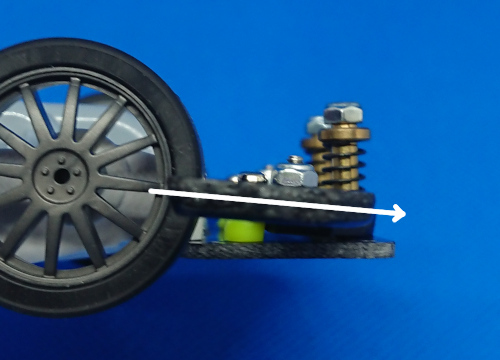
また、ARフロントステーとVZシャーシ端材の間に小ワッシャーを入れる事で高さの微調整が可能となります。
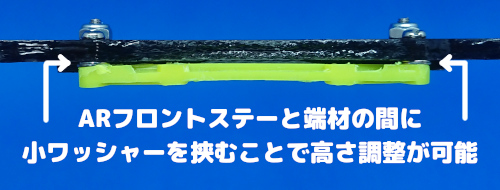
フロントワイドステーの場合
フロントワイドステーはARフロントステーのようなスペースがないので、ARフロントステーでおこなったスラスト角の調整方法は使用できません。
フロントワイドステーの場合はマルチプレートに何かをあててATバンパーのリヤ側の部分の高さを増すことでスラスト角の調整が可能となります。
ビスを使用した調整方法
1つ目のスラスト角の調整方法としてVZシャーシであれば、ブレーキステーの既存ビス穴を使用してトラスビス・ナット・ワッシャー等でフロントワイドステーのスラスト角の調整が可能です。
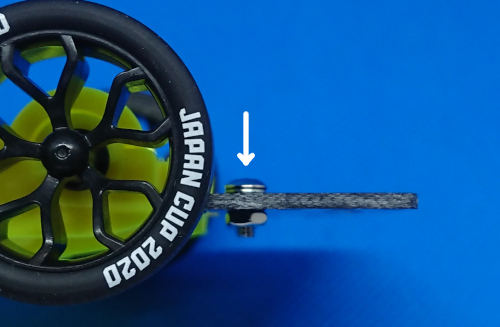
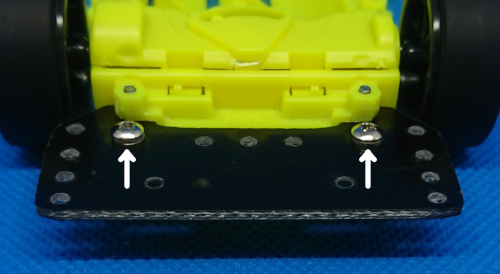
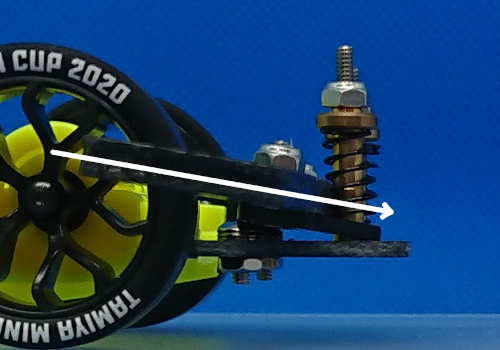
MA・MSシャーシの場合は上記の既存ビス穴を使ってもVZのようにはマルチプレートがあたらないので残念ながら同じビス穴を使用することができません。
このため、スラスト角調整用にブレーキステーに新規のビス穴をあけるか次に紹介するローラー角度調整プレートセットを使用した方法で調整する必要があります。
ビスのはみ出しには対処が必要
スラスト角調整でビスを使用する場合に、スラスト角によっては一番短いトラスビスを使用してもビスが突出することがあります。
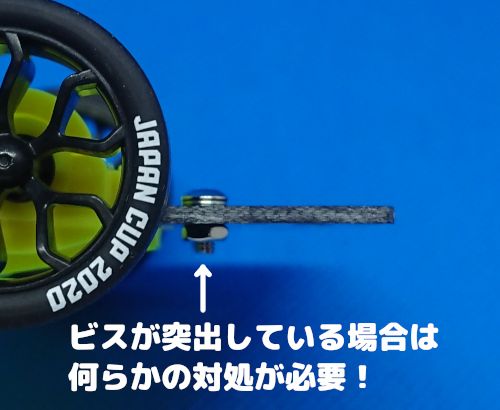
ビスが地面側に突出しているとコースのスロープなどにあたりコースを傷つけてしまう可能性があるために、ビスにゴムキャップを付けるか、ビスが突出しないよう適切な長さにカットするかの対処をしていきましょう。
ビスの加工方法については以下の記事にて紹介しています。
ローラー角度調整プレートセットを使用した調整方法
2つ目のスラスト角の調整方法はローラー角度調整プレートセットというグレードアップパーツを使用してスラスト角の調整をおこないます。
※ローラー角度調整プレートセットの構造・仕様については別記事「ローラー角度調整プレートセット 使い方」をご参照ください。
基本的な使い方はこれまで紹介してきた他の方法と同様にブレーキステーとマルチプレートの間にこのローラー角度調整プレートセットをセットしてスラスト角をつけていく形になります。
それでは実際の使用方法をVZシャーシを使って解説していきます。
まずブレーキステーにローラー角度調整プレートセットのチップを設置します。
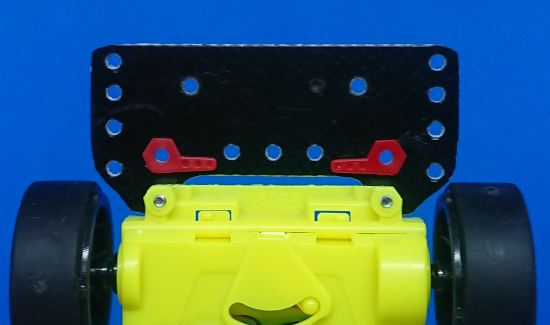
チップの設置箇所については既存のブレーキステーのビス穴をガイドとして一時的にビス穴にビスを通して そこにチップを置くと丁度いい感じの位置になります。
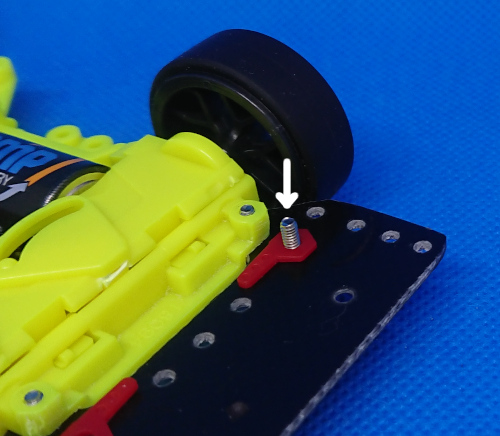
そしてチップを接着剤等でブレーキステー側に固定して、あとはフロントATバンパーを設置していきます。
(フロントATバンパーの設置手順については「仕上げ」の項目をご参照ください)
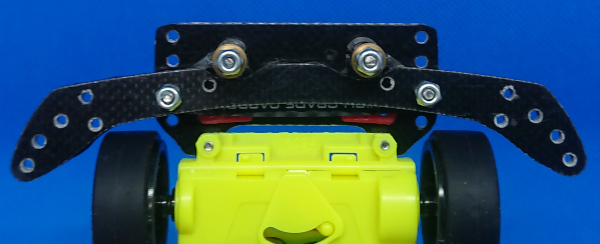
これでフロントATバンパーにスラスト角が付きます。
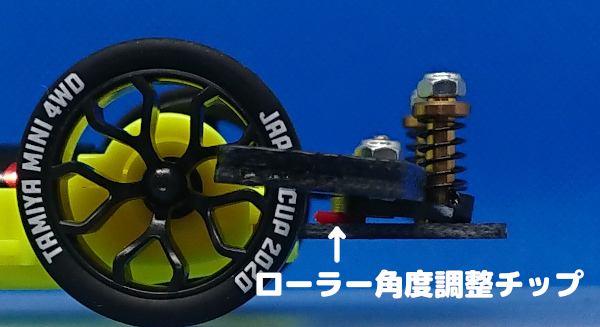
上の画像は傾斜3°のチップを使用していますが、傾斜が小さいチップに変えることでスラスト角を下げたり、チップを追加して重ねて使用することにスラスト角を上げたりすることが可能です。
ちなみにこのチップを使用してスラスト角を調整する方法はフロントワイドステーを使用した場合に限らず、ARフロントステーを使用した場合でも使うことが可能です。
そして、ここで注意してもらいたいのははチップの設置位置です。
チップを左右対称の位置に置くことはもちろんとして、チップの前後の位置によって同じ傾斜角のチップを使用した場合でもスラスト角が変わってきます。
そのチップの設置位置の重要性について図を交えて解説していきます
(ここでは図を見やすくするために それぞれの角度は敢えて実践では使われない高めの数値に設定しています)
まずはチップが適切な場所に配置された図が以下となります。
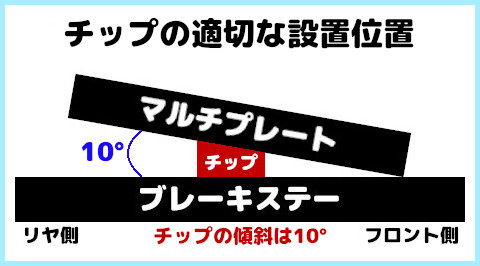
チップの設置位置が適切な箇所にあるため、マルチプレートとチップがピッタリ重なり、マルチプレートはチップと同じ傾斜角になっています。
では続いて、まったく同じチップを前方(フロント側)に設置した場合の図を見ていきましょう。
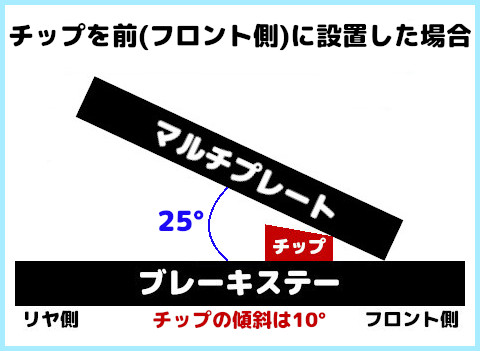
チップを前方に置いた場合はチップの前方の突起部分だけがマルチプレートと接触するため、マルチプレートのスラスト角はチップよりも大きくなってしまいました。
では次は上の画像とは反対に 後方(リヤ側)にチップを設置した場合の図を見ていきましょう。
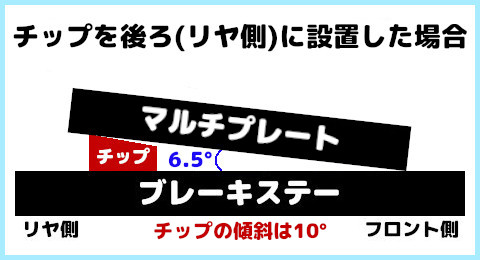
チップを後方に置いた場合はチップの後方の突起部分だけがマルチプレートと接触するため、マルチプレートのスラスト角はチップよりも小さくなってしまいました。
このように同じ傾斜角のチップでも前後の位置を変えるだけでマルチプレート(ATバンパー)のスラスト角も変わってきます。
チップを前方(フロント側)に設置するのは避けた方が良い
チップを前過ぎる位置に置くとマルチプレート(ATバンパー)の重心が後ろ寄りになってしまい、ATバンパーがぐらつきやすくなり・重心が後方にいくことでスラスト抜けを誘発しやすくなってしまいます。
このためチップはなるべく後方(リヤ側)に置くようにしましょう。
もし、前方に設置しないとチップの傾斜・厚さがATバンパーとピッタリ合わないということであれば、以下の図のようにチップ自体の厚みを変えることで適切な位置を調整することができます。
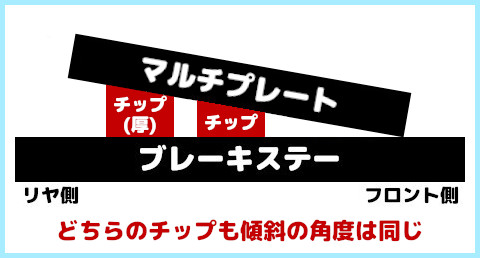
チップの厚さ(高さ)を上げる手段としてお手軽なのはチップの下にワッシャーを置く方法ですが、微妙にマシン重量が増えるデメリットがあります。
少しでもマシンを軽くしたいということであればクリヤーボディなどのクリアパーツの端材を適切な大きさに切り取ってチップの下に設置すれば見た目的にも目立ちません。
ただし、チップを厚くした際に後方にチップをずらすにしても下げられる距離には限界があり、チップとマルチプレートをフィットさせようとして後方に下げ過ぎるとATバンパー自体と接触しないという本末転倒なことが起こります…
こうしたことからローラー角度調整プレートセットのチップでスラスト角を調整する場合は、チップの位置はなるべく後方(リヤ側)寄りをおすすめします。
チップの傾斜にピッタリとATバンパーがフィットすることを重視するよりも、例えチップとATバンパーの接触面積が少なくても 自分の理想とするスラスト角になるようにチップの厚さを重視した方が良いかと思います。
尚、ローラー角度調整プレートセットの構造・仕様などについては以下の記事で解説しているので、ローラー角度調整プレートセットが少しでも気になったのであれば閲覧していただければと思います。
仕上げ
これまで加工してきたパーツを組み合わせ、フロントATバンパーを組み立て、可動確認をおこなっていきます。
パーツの結合
バンパーの作成
まずは加工してきたパーツを結合させバンパー部分を作っていきます。
パーツの結合には皿ビス(6mmが推奨)とロックナットを使用します。
下の画像のようにフロント提灯を取り付ける場合は、ここで使用する皿ビスがフロント提灯の支柱になるので長めの皿ビス(25mmぐらいが推奨)を使用します。

結合方法については各ステー毎に以下のビス穴を使用しますが、いずれの組み合わせもマルチプレートを下にセットしていきます。
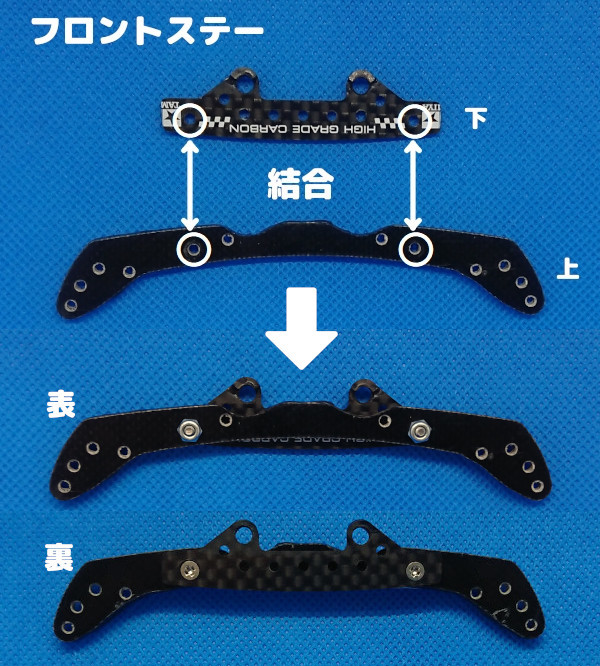
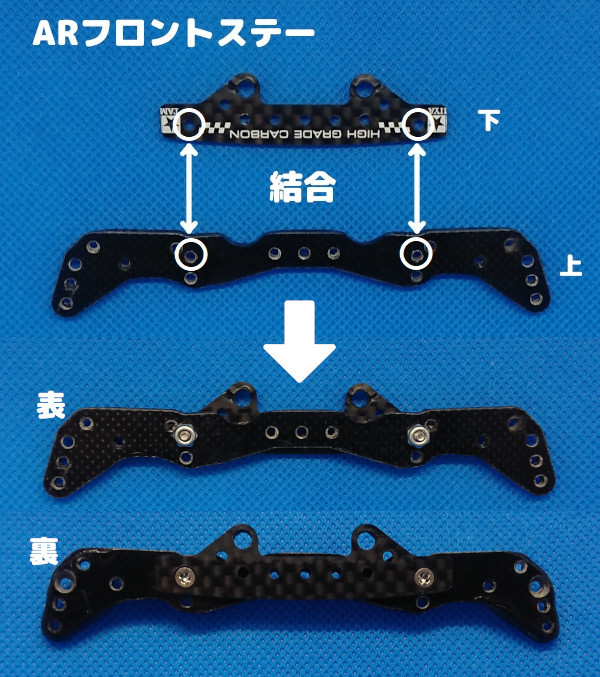
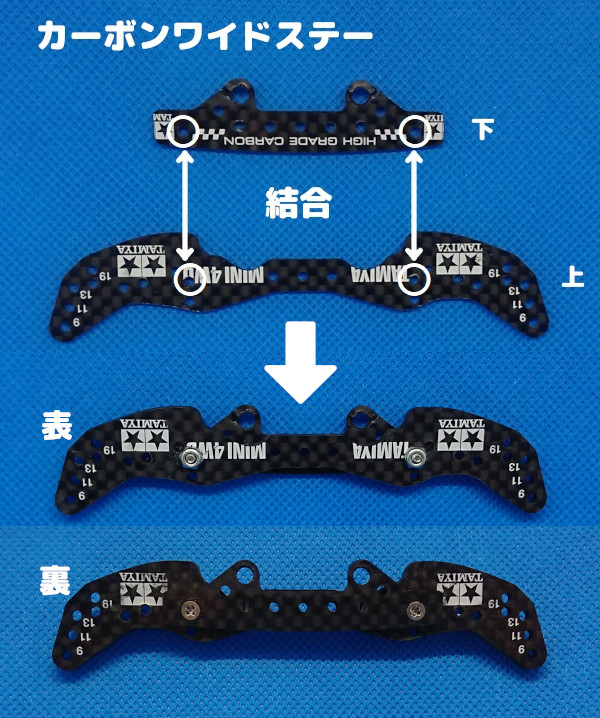
尚、カーボンワイドステーについては同じステーの裏面同士を重ねているため、表も裏も文字・ロゴがプリントされている面が見えるかたちとなっています。
ステー・プレート間のズレに注意
上記の結合の際にステー・プレート間でズレることがあり、ズレたまま結合してしまうとATバンパー全体の向きがズレ バランスが悪い状態になってしまうので、ビス止めする時に互いのステー・プレートが平行になっていることを確認しましょう。
尚、ARフロントステー(カーボンワイドステー)であれば中央部分のビス穴もマルチプレートと同じ箇所にあるので、ビス止めする時だけ中央部分にもビスを通せばズレを減らすことが可能です。
これはARフロントステーかカーボンワイドステーを使用する場合に限られますが、フロント提灯が不要で追加の穴をあけていない場合は以下のビス穴を使って結合させても構いません。
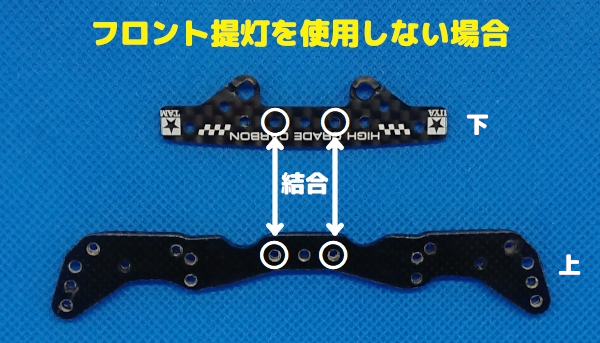
ただ、この場合マルチプレート裏面の白丸箇所に皿ビス加工が必要となりますので注意してください。
ブレーキステーの取り付け
加工したブレーキステーの以下の画像の矢印で示したビス穴とシャーシを結合させます。
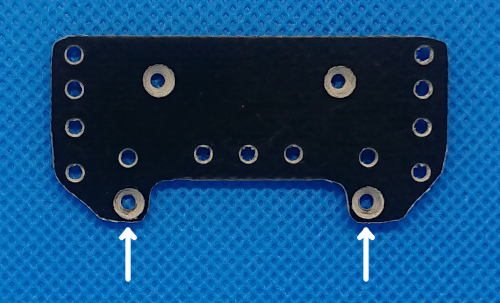
各シャーシは以下の画像の矢印で示したビス穴を使用して、皿ビス(6mmか8mm)でビス止めしていきます。
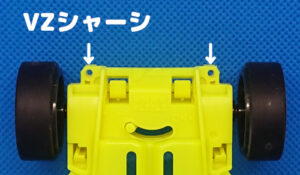
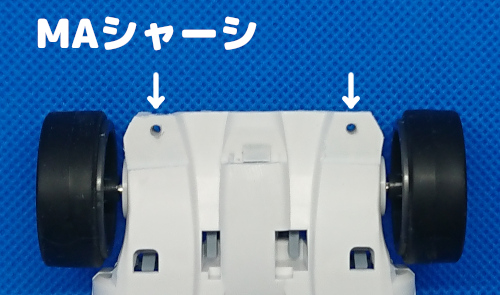
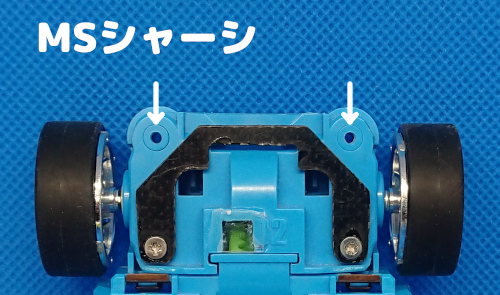
ブレーキステーの結合が完了したら、ブレーキステーがシャーシ・タイヤに干渉しないかを確認し、干渉している場合はブレーキステーかシャーシを加工していきます。
また、スラスト角調整のためにブレーキステー側に何らかのパーツ追加が必要な場合はこの段階で設置しておきましょう。

ブレーキステーをそのまま取り付けた場合はVZシャーシは他のシャーシに比べて地上高がやや高めの位置となり、ブレーキ・ローラーなどの全体的な位置が高めになります。
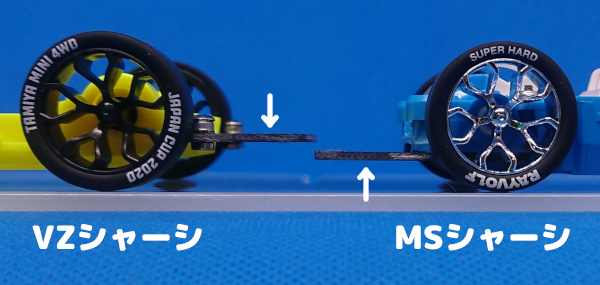
このままの位置で問題なければそのままで構いませんが、もう少しブレーキステーの高さを低くしたいという場合は、シャーシとブレーキステーの間にスペーサーを入れることで高さを調整することができます。
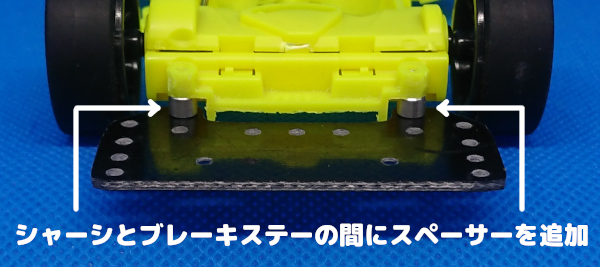
スペーサー以外にもワッシャーを使う事で高さの微調整が可能となるので、タイヤ径などに合わせて適切な高さに調整していきましょう。
組み立て
ここでは各パーツを組み立てフロントATバンパーを完成させていきます。
まずブレーキステーの以下の位置に皿ビスを通します。
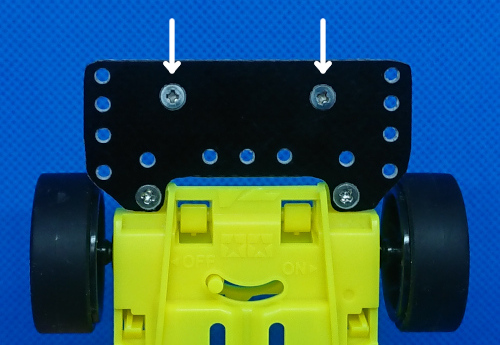
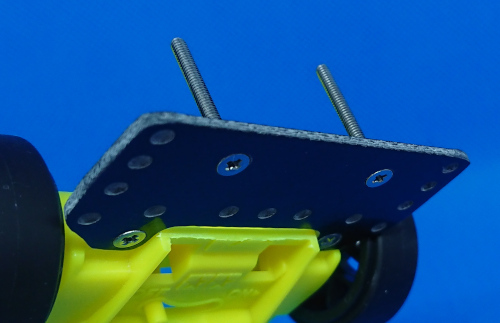
この皿ビスがATバンパー軸となります。
ATバンパー軸の皿ビスの長さについては今回の構成では17mm程の皿ビスが適しています。
ただし、その長さにするためには皿ビスの加工が必要となるため、ここではそれに近い長さの20mmの皿ビスを使用していきます。
スプリングの硬さを調整するために支柱の長さを短くした場合は15mmの皿ビスが最適の長さになってきます。
ビスを取り付けた後、このままシャーシを戻すとビスが下に落ちてしまうので一旦裏側にマルチテープ等を貼ってビスを仮固定します。
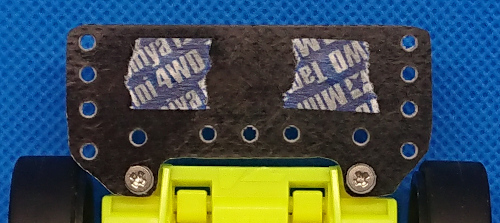
次に左右のビスに真鍮パイプを2個づつ取り付けます。
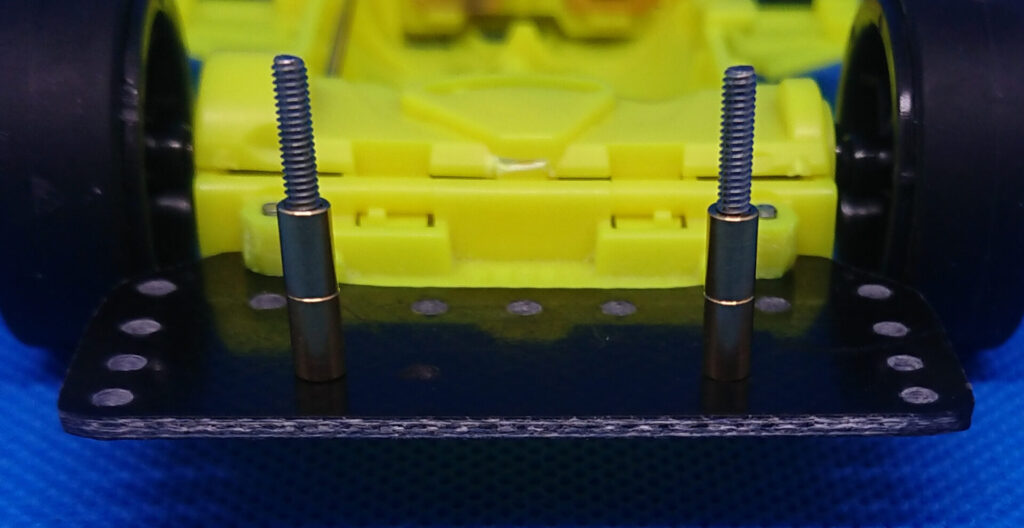
更にその上に 結合したバンパーを結合したバンパーの拡張穴から通します。
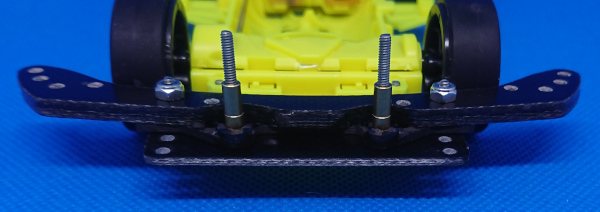
結合したバンパーを載せたら、ビスに まずスプリングを通し、その上にメタル軸受けを載せます。
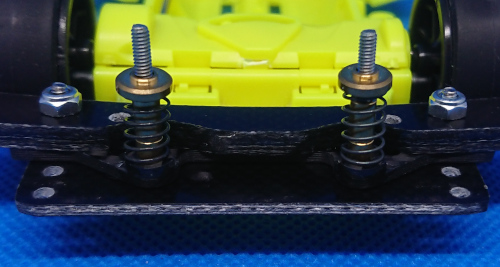
この状態から一旦工具を使わずに、ロックナットを手で回せる範囲でビスに固定していきます。
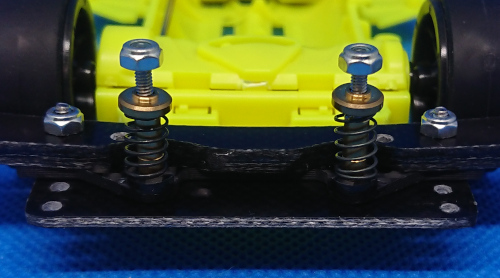
ロックナットが少し固定されたら、ブレーキステー裏面のテープを剥がして、プラスドライバー・ボックスドライバーでロックナットをしっかりと固定します。
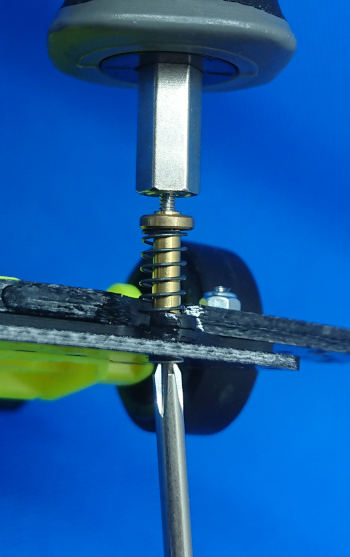
この段階でATバンパー軸のビスに余長がある場合はゴムパイプ・ボールスタビキャップ等でビスの先端部を塞ぎます。
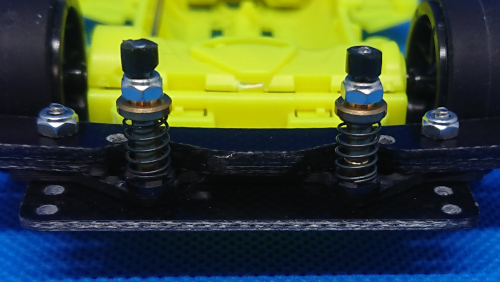
あとはフロントステーにお好みのローラーや引っ掛かり防止対策のパーツなどを取り付けてフロントATバンパーの完成です。
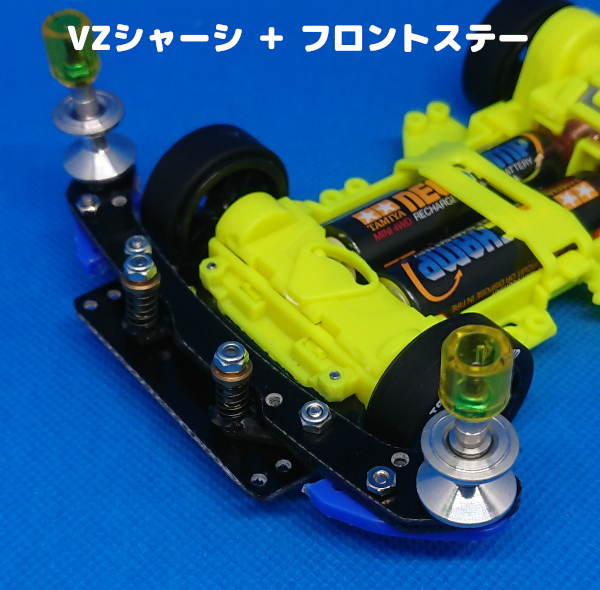

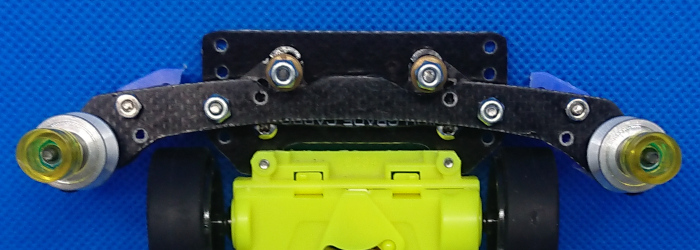
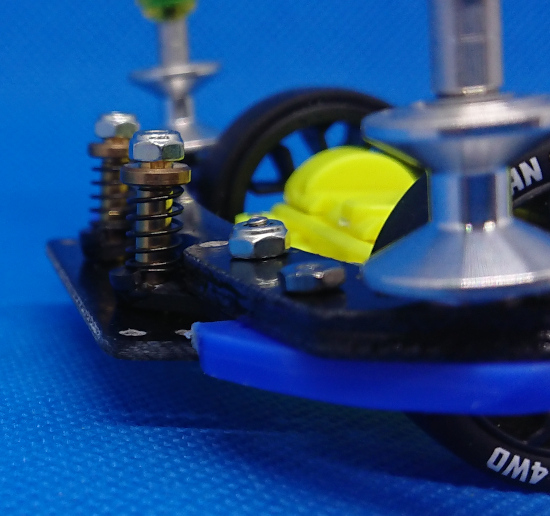
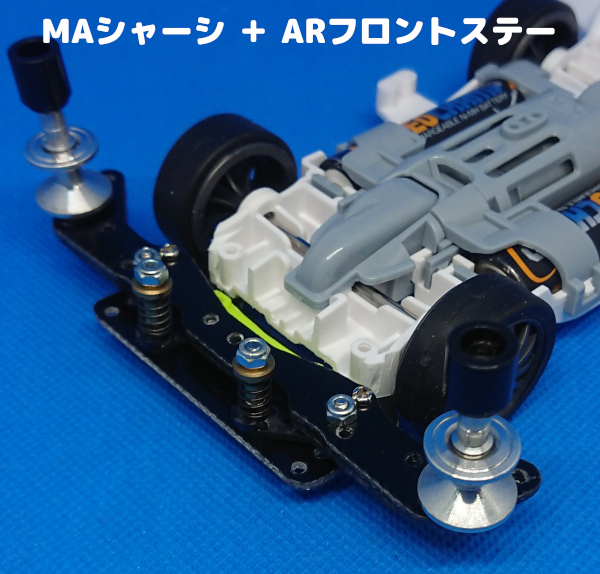
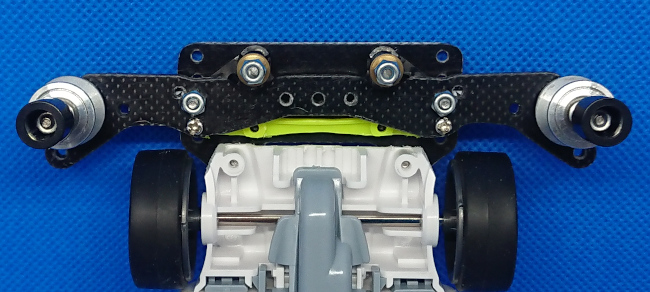
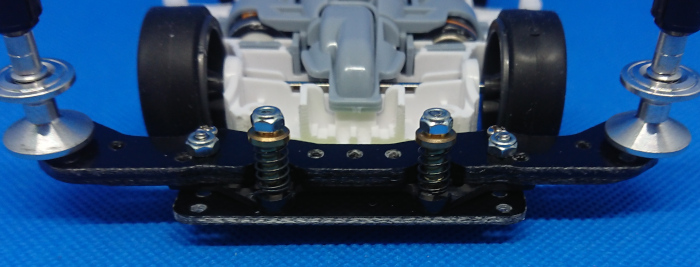
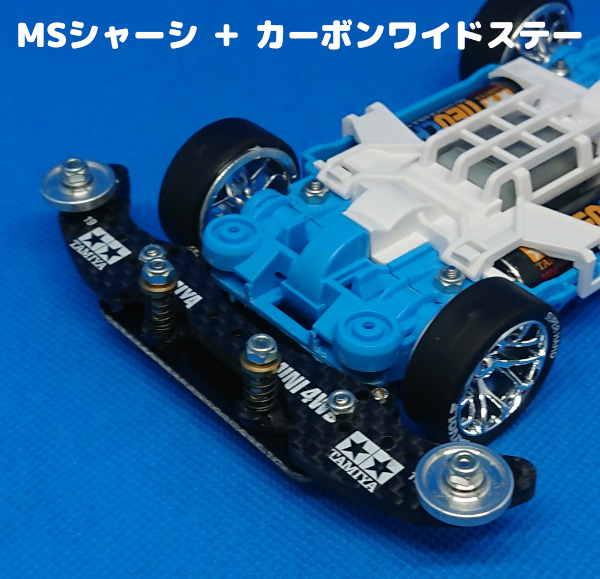
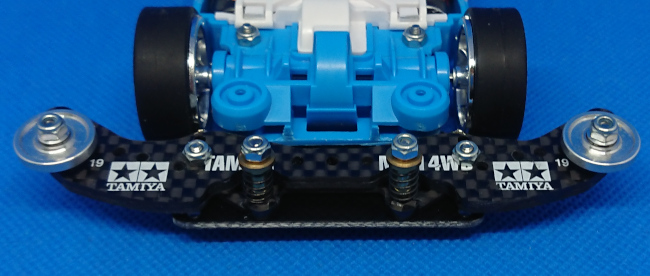
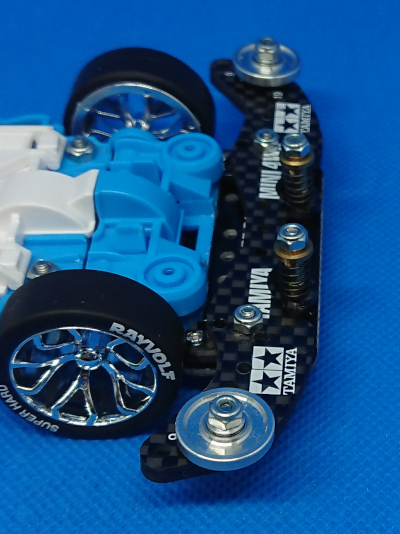
可動確認
加工がすべて完了したら フロントATバンパーの前傾する動き、フェンスに乗り上げた際の動きを確認して可動に問題がないかを確認します。
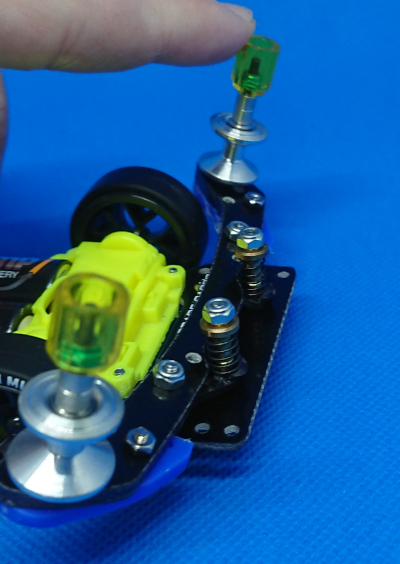
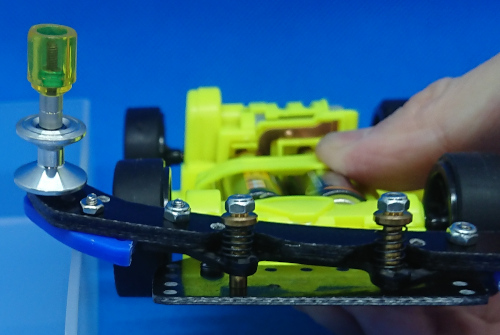
特にフェンスに乗り上げた際に動きについては真鍮パイプにグリスを塗る事でよりスムーズになります。
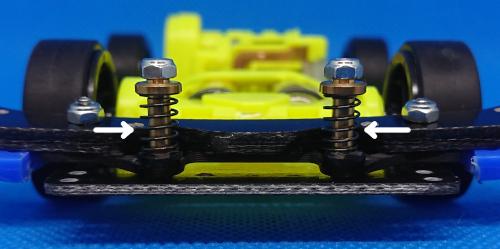
逆に、シャーシを激しく揺らしてみてATバンパーのぐらつきが目立つということでしたら、以下の記事にてスラスト抜け対策方法を紹介しているので、こちらの内容を試して頂ければと思います。
最後に
本記事では出来る限り多くのシャーシ・多くの加工パターンに対応できるようにと記事を書いてきたわけですが、気づけば結構なボリュームとなっていました…(笑)
ただ記事のボリュームはあるものの設置するシャーシ・ご自分の作りたいバンパーの形に絞れば 加工手順自体はシンプルなので、目次から必要なところだけ絞って閲覧して頂ければと思います。
また、今回作成したフロントATバンパーは当サイトの別記事で紹介しているフロント提灯とも連動できる形となり、これに連動したフロント提灯の作成方法については以下の記事にて解説しているのでよろしければご参照ください。
それと今回のフロントATバンパーをベースにATスライドダンパー・ATピボットバンパーにも派生が可能で、こちらについても別途作成方法を解説しているので よろしければご参照ください。
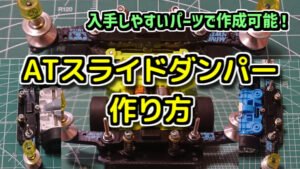
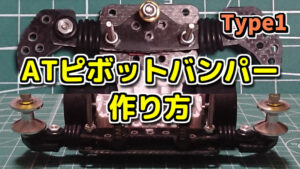
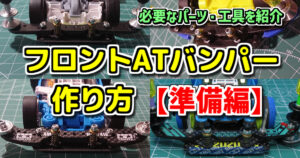
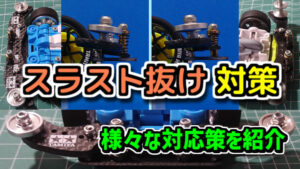
コメント
コメント一覧 (8件)
ミニ四駆復帰初心者です。
全記事読みました!大変参考になりますとともに、ありがたい気持ちでいっぱいです。
丁寧に紹介してくださっているので、自身でも取り掛かり易く、毎日楽しく新たな趣味として没頭させてもらっています。
これからも頑張ってください!応援しています!!
コメント及び当サイトの記事を読んで頂きありがとうございます!
今後も更新頻度は不定期になるかと思いますが、新たな改造・ミニ四駆に関する情報などをお届けする予定なので お時間がある時に当サイトを覗いて頂ければ幸いです。
それと同じミニ四駆復帰組としてお互いに楽しんでいきましょう!
お世話になります。
1年以上の前の記事に質問することをお許しください。
ビス穴の追加についてなのですがfmaシャーシで作成する場合どのシャーシを参考にすればよろしいでしょうか?
よろしくお願いします。
>>初心者さん
コメントありがとうございます。
FM-Aシャーシについては本記事の冒頭で紹介したフロント提灯には非対応となっているため、ブレーキステーのビス穴追加は「VZ」「MA・MS」のどちらでもOKでお好みで構いません。
また、もし急ぎでないようであれば、どちらのシャーシに合わせるのがより適切なのかを調査したいので、ビス穴追加加工については一旦保留してもらえると幸いです。
ただし、回答まで おそらく早くても2週間ほどかかってしまい(それよりも長くなるかもしれません…)だいぶ待たせることになってしまうので 保留しない方が良いかもしれません。
お世話になります。
丁寧な説明ありがとうございました。
特に急ぎではないのでお時間ありますときにご教示いただきましたら幸いです。
>>初心者さん
大変お待たせいたしました。
問い合わせ頂いたFM-Aシャーシの穴あけについては、基本的に「MA・MS」のやり方を推奨します。
なぜMA・MSのやり方を推奨するかについては本記事の『ビス穴の追加』項目にFM-Aシャーシの項目を追加しましたのでそちらをご確認お願いします。
また、別記事『シャーシカット方法』にて新たにFM-Aのシャーシカット(バンパーカット)のやり方も追加したので、まだバンパーカットしていないようであればこちらの記事も参考にしてみてください。
あかし様
お世話になります。
何から何まで詳しい説明ありがとうございました。
こちらのサイトは私のような者にはとても心強いのでこれからもよろしくお願いします。
>>初心者さん
私の方も「初心者さん」の質問のおかげで 勉強でき新たな知識を得られたことを感謝しています。
これからもミニ四駆の役立つ情報をどしどし載せていく予定なので、今後ともよろしくお願いいたします。