今回は1軸 リヤアンカーの作成方法を解説してきます。
以前にも当サイトでは1軸・2軸のリヤATバンパーの作成方法をいくつか紹介してきましたが、リヤアンカーは今までのものよりも更にいなし効果が高く、ミニ四レーサーの間でも使用頻度が高いATバンパーとなります。
そして、そのリヤアンカーの作成方法を より詳しく丁寧に解説していきますので初心者の方でも比較的簡単にできる改造となっており、完成したリヤアンカーは以下のような形となります。
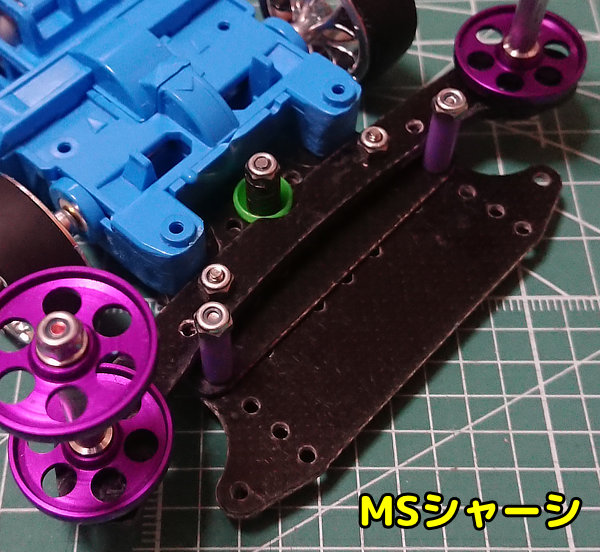
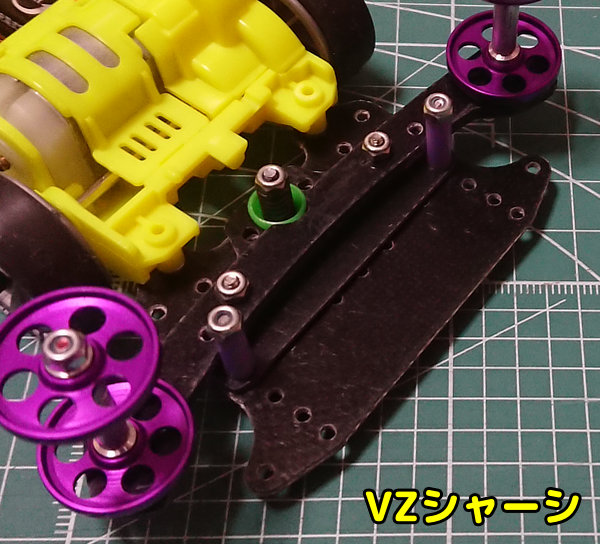
尚、今回の作成に必要なパーツ・工具の詳細については以下の「準備編」にて紹介しているので、そちらをご参照ください。
マスダンパープレートの加工
ここではボールリンクマスダンパーに付属しているFRPプレートの加工方法を解説していきます。
尚、このFRPプレートについては以後 マスダンパープレートという名称で話を進めて行きます。
マスダンパープレートには、穴の拡張・皿ビス加工・干渉箇所のカットの加工をおこなっていきます。
各加工方法を解説する前に、まずは穴の拡張に関する「加工精度による可動の違いについて」を紹介していきます。
加工精度による可動の違いについて
ここでは次に解説する穴の拡張の加工精度によってリヤアンカーの可動にどう影響してくるのかをリヤアンカーの構造画像を交えて解説していきますが、ここでの話は少し長くなるので すぐにリヤアンカーを作りたいという方は次の「穴の拡張」にお進みください。
まずはリヤアンカーの実際の構造及び各部パーツ名を紹介していきます。
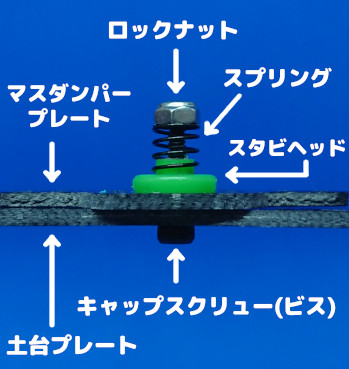
キャップスクリュー(ビス)はリヤアンカーの支柱となり、この支柱に各パーツが結合する形となります。
次に上の画像を同じ角度から見た断面図が以下となります。
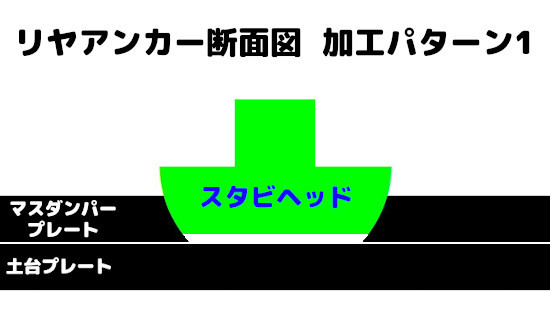
本来であればスタビヘッドは土台プレートに接触している状態の方が望ましいのですが、今回は圧力の流れを分かりやすくするために、敢えてスタビヘッドが土台プレートに接触していない前提の状態で説明してきます。
この断面図の構成はマスダンパープレートとスタビヘッドがフィットしており、理想的なマスダンパープレートの加工の形であり この形状を加工パターン1とします。
※断面図ではキャップスクリュー(ビス)・ロックナット・スプリングの表記は省略していきます。
まずはこの加工パターン1の マスダンパープレートを固定している仕組みから見ていきます。
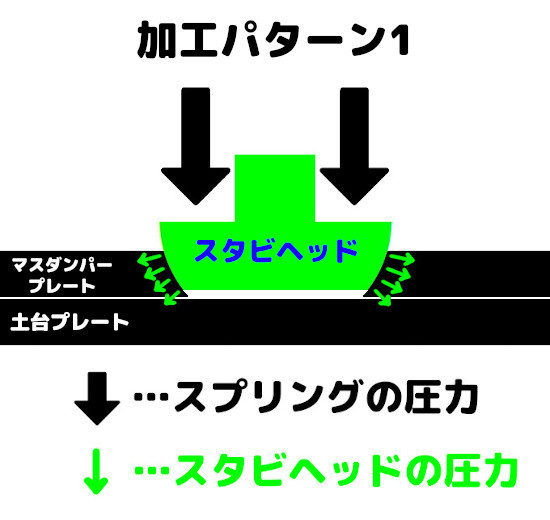
まずスプリングの圧力がスタビヘッドに伝わり、そのスタビヘッドにかかった圧力がマスダンパープレートに伝わることでマスダンパープレートを固定してガタつきを抑えており、スタビヘッドからの圧力でマスダンパープレートを押さえつけている形となります。
上の断面図のマスダンパープレートの曲線はスタビヘッドの形にぴったりとフィットしていてスタビヘッドからの圧力もマスダンパープレートに満遍なくかかり理想の圧力の流れとなります。
次にマスダンパープレートの曲線がスタビヘッドの形にフィットしなかった場合の加工パターン2と加工パターン3を見ていきます。
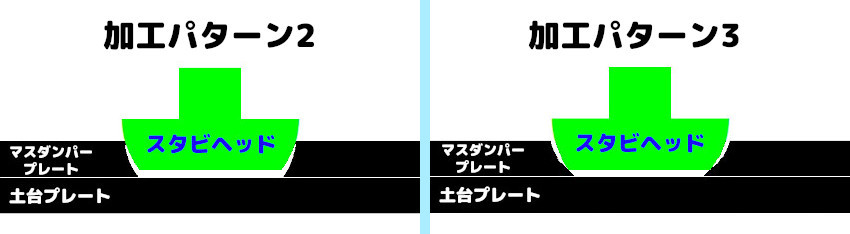
加工パターン2は曲線の傾きがやや急となっており マスダンパープレートの上部しかスタビヘッドに接触してなく、加工パターン3は曲線の傾きがややゆるやかになっておりマスダンパープレートの下部しかスタビヘッドに接触してません。
では上記の状態の形状である場合に圧力の流れがどうなるのかを見ていきます。
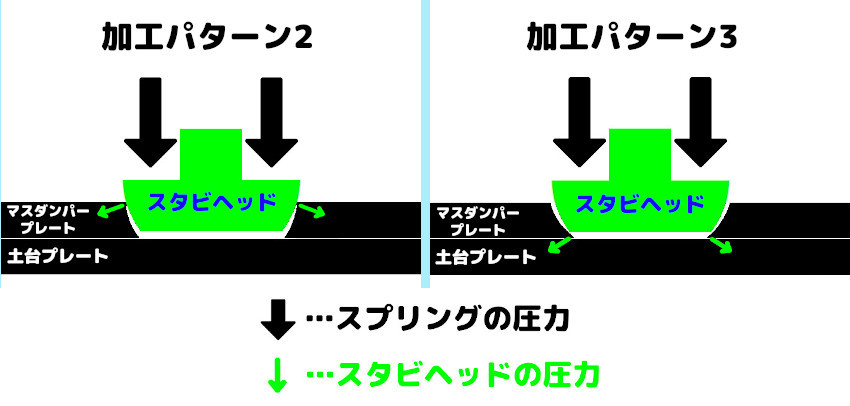
どちらの加工パターンもマスダンパープレートとスタビヘッドの接触している箇所だけに圧力がかかり 一見すると加工パターン1より圧力が弱く見えます。
しかし、スタビヘッドからの圧力は接触している部分に一極集中するため マスダンパープレートにかかる圧力自体は加工パターン1とほぼ同じとなります。
ただし、双方の接触面積が少ない分 マスダンパープレートとスタビヘッドの摩擦抵抗力が加工パターン1と比べて落ちてしまうため 同じ衝撃を受けた際に加工パターン2・3のマスダンパープレートは加工パターン1よりもブレやすくなってしまいます。
接触面積が少なくなりガタつきやすいのは加工パターン2・3の形状以外にも穴の曲線が均等に削れずいびつになった場合も該当してきます。
このことからマスダンパープレートの穴の曲線は出来る限りスタビヘッドの形に沿った加工パターン1のような形状が望ましく、リヤアンカーのバンパー部分がガタつきやすい原因の大半が この穴の曲線の加工精度に依存するのではないかと思われます。
ただ、上記のパターン2・3のような穴の曲線が駄目かと言うとそうでもなく、接触面積が少なく摩擦抵抗力が弱いということはいなし効果が高まるというメリットもありますし、スプリングの圧力を強めれば結果的にガタつきを抑えることもできます。
とは言え、できるだけできるだけ精度が高い加工をしていなし効果とガタつきにくさの両方を兼ね備えたバンパーを作っておきたいところではあります。
ちなみにリヤアンカーの理想の形は以下の断面図のようにスタビヘッドがマスダンパープレートと土台プレートのいずれにも密着している状態となります。
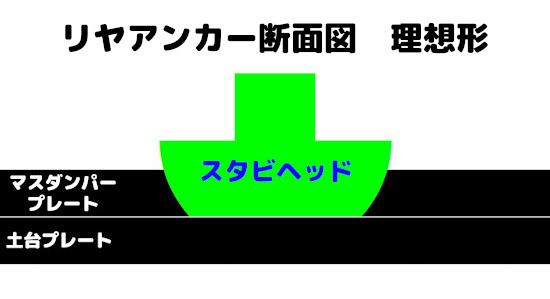
本記事ではこの理想形を目標にマスダンパープレートとスタビヘッドを加工し、次の穴の拡張では より精度が高い曲線にするための加工方法を解説していきます。
穴の拡張
マスダンパープレートにスタビヘッドを取り付けるために、マスダンパープレートの中央の穴をすり鉢状に拡張していきます。
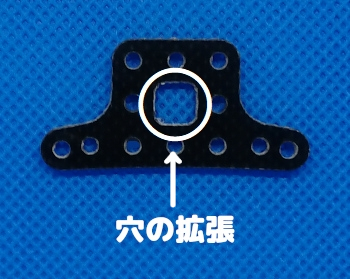
ここでの穴の拡張はリヤアンカーの加工精度にも影響し、最も重要な加工箇所でもあるので穴の拡張方法も複数のパターン紹介していきます。
直径8mm球型リュータービットを使った加工方法
別途リュータービットを購入する必要はありますが、以下の直径8mm球型リュータービット(もしくは直径8mm半丸型)さえ用意してしまえば 誰でも簡単に最適な穴の拡張が可能となります。
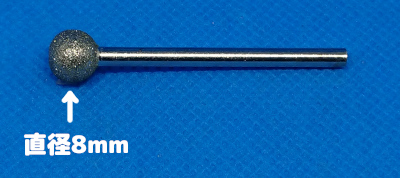
何故この直径8mm球型ビットが適しているかといいますと、スタビヘッドの直径も8mmだからです。
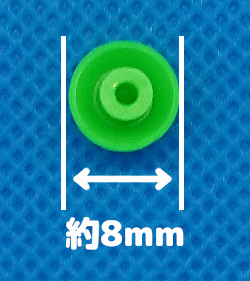
厳密に言うとスタビヘッドの直径は8.5mm程あることと スタビヘッドと直径8mm球型ビットの形状が完全に一致するというわけではないので、直径8mm球型ビットで削ったからといって 寸分たがわずにスタビヘッドがフィットするわけではありません。
しかし、現状この直径8mm球型ビットが最も適した穴があけられるということは間違いなく、リヤアンカーの加工に最も適したリュータービットとも言えます。
加工方法は極めてシンプルで、マスダンパープレート中央の穴に直径8mm球型ビットを垂直に当てて削るだけです。
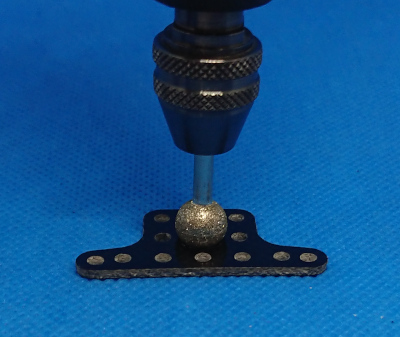
※上画像のようにマスダンパープレートを台に置いた状態でリューターを当てると台も削れてしまうので注意してください。
削る際は、以下の画像のように 手に直接 マスダンパープレートを持つ やり方がおすすめです。
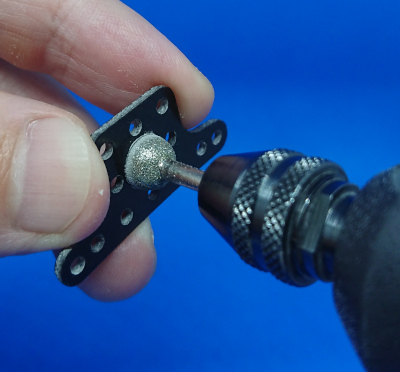
削りすぎには注意
穴の拡張については 深く削れば削るほどバンパーの安定性は増しガタつきを抑えることができます。
しかしながら、安定性を出すためにと 穴を削りすぎてしまうと、その後のスタビヘッドの加工で その穴の深さに合わせようとするとスタビヘッドが破損してしまいリヤアンカー自体が機能しなくなってしまうので削りすぎには注意しましょう。
以下の画像は直径8mm球型ビットで穴を拡張した後の画像となりますが、直径8mm球型ビットを使用する場合は この穴の拡張度合いが スタビヘッドが破損しないギリギリの大きさとなります。
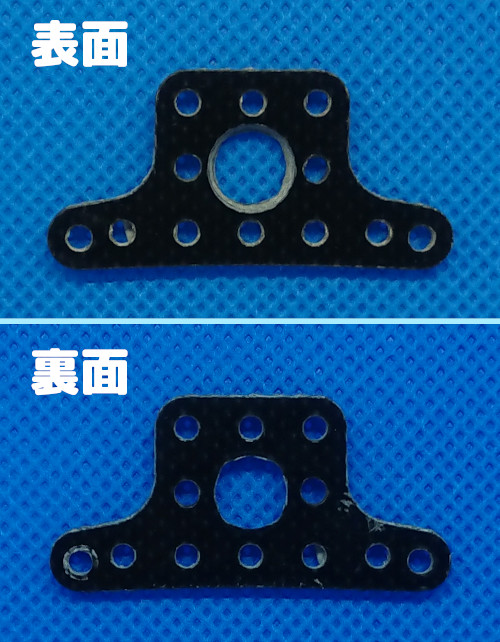
これ以上穴を深くしてしまうとスタビヘッドの加工にも影響が出るので、どのくらい穴を拡張して良いのか分からない方は上の画像を直径8mm球型ビットでの穴拡張度合いの目安として参考にしてもらえればと思います。
砲弾形リュータービットを使った加工方法
上記の直径8mm球型ビットを使用しない場合は、代わりに砲弾形リュータービットを使用していきます。
この砲弾形ビットを使用した穴拡張は多少手間はかかるものの、ビットは100円ショップで購入できるため工具費は非常に安く済むのが特徴で リヤアンカーの穴拡張に使う工具としても非常に使用率が高いアイテムとなっています。
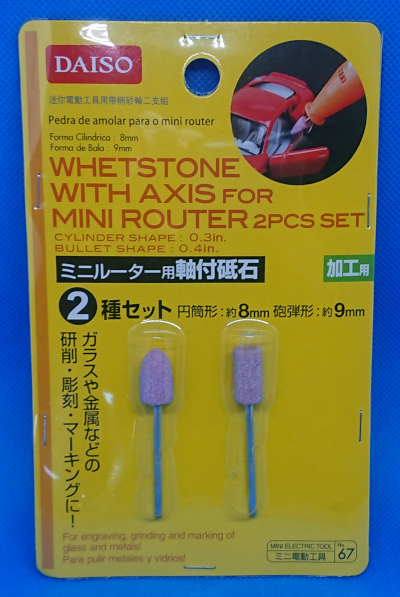
砲弾型ビットを使用した加工方法については、まずはマスダンパープレート中央の穴に砲弾形ビットを垂直にあてます。
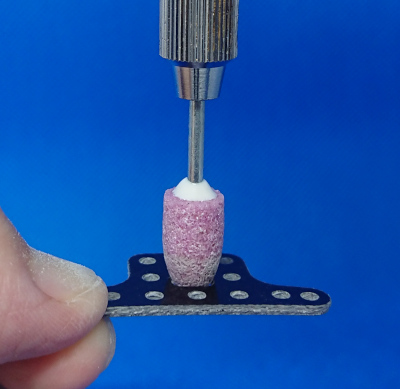
この垂直に当てる作業ではビットをあてすぎて穴が深くならないよう注意し、以下の状態ぐらいまでの加工していきます。
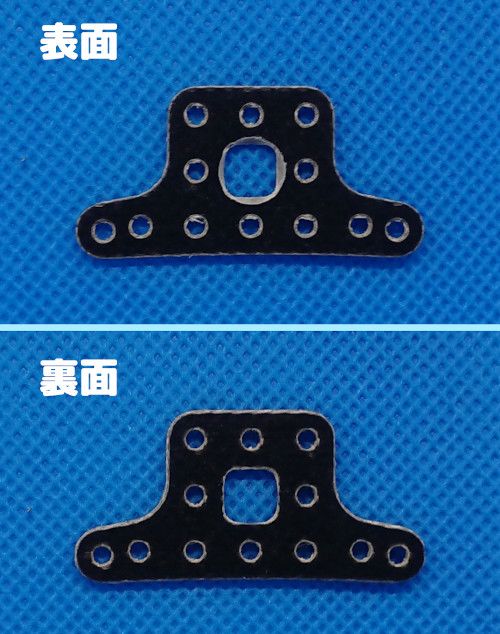
表面は穴の外側に円ができ、裏面はまだ元の状態の形を保っている程度の加工でOKです。
次に砲弾形ビットを少しだけ傾けた状態で穴の周りをぐるっと回していきます。
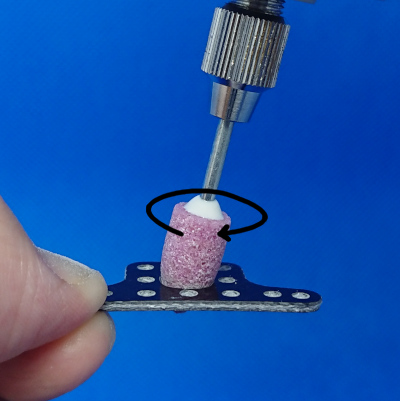
あまり削りすぎてしまわないよう、砲弾形ビットを軽く当てつつ何周か回して以下の状態になるぐらいまで削って穴拡張作業は完了となります。
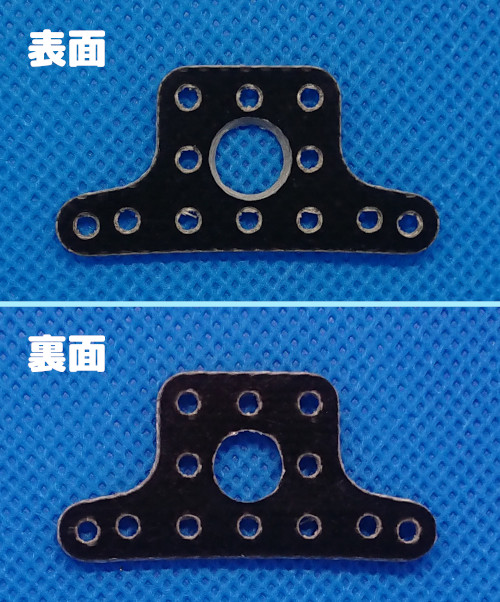
表面は綺麗なすり鉢状となり、裏面は完全な円に拡張される ほんの直前ぐらいの状態の仕上がりを目標としていただければと思います。
砲弾形ビットの傾ける角度は浅めに
砲弾形ビットを回す際にビットを傾けすぎてしまうと、冒頭で紹介した加工パターン3のような状態になってしまうので、くれぐれもビットの傾けすぎずに浅めに傾けることを意識して穴拡張を行いましょう。

皿ビス加工
マスダンパープレートにバンパーを取り付けるために、マスダンパープレートの裏面(穴が狭い方)に皿ビス加工をしていきます。
皿ビス加工する箇所については、取り付けるバンパーの形状によって異なるので、ご自分が使用したいバンパーに合ったビス穴を選んで頂ければと思います。
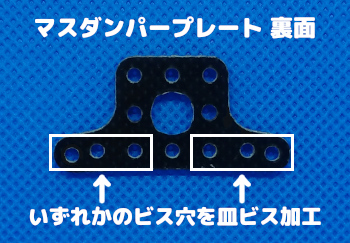
皿ビス加工には皿ビス穴加工ビットを使用していきます。
本記事ではフロントワイドステーを使用する前提で解説していくので以下の箇所に皿ビス加工を施しました。
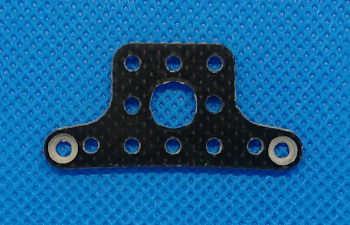
干渉箇所のカット
最後にマスダンパープレートがシャーシと干渉する箇所をカットしていきます。
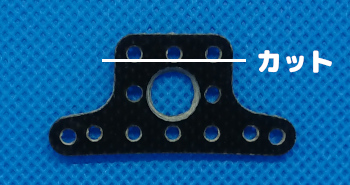
このカット作業については必須ではありません。
使用するシャーシやリヤアンカーの位置によってはカットをしなくてもシャーシに干渉しないこともあるので、一旦ここでの作業は保留にして最後のシャーシ取り付け時に干渉しているかを確認してからカットしても構いません。
カットする場合はリューターのダイヤモンドカッター・円筒形ビットなどを使用します。
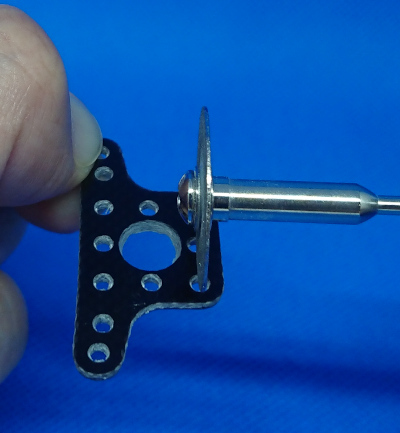
まずダイヤモンドカッターでばっさりとカットしてきますが、余分なところまでカットしてしまわないよう 拡張穴の上部のビス穴間を繋ぐ感じで少し余裕を持たせて切断します。
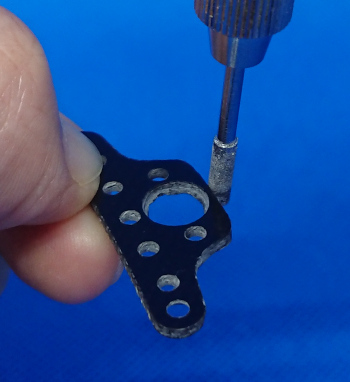
その後円筒形ビットなどでカットした面を綺麗に整えていきます。
くれぐれも拡張穴の箇所まで削ってしまわないよう慎重におこなっていきましょう。
そして、今回は様々なケースに対応できるよう以下のようにカットしました。
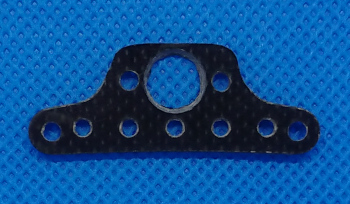
以上でマスダンパープレートの加工は完了となります。
【番外編】カーボンプレートを使用した場合
ここでは番外編として、以下のマスダンパー用カーボンプレート(以後 スクエアカーボン)を使用する場合の加工方法を解説していきます。
※すでにFRPプレートで加工が完了している場合は ここを読み飛ばして 次の『スタビヘッドの加工』へお進みください。
スクエアカーボンもFRPプレートと同じ加工方法で問題ありませんが、スクエアカーボンにはスタビヘッドを設置するための中央の穴がありません。
そうしたことから、スクエアカーボンを使用する場合は、まずプレート中央に穴をあける必要があります。
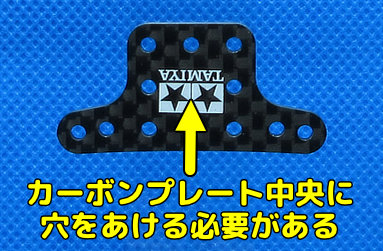
この中央の穴の位置は かなり重要で、穴が中央からずれてしまうとリヤアンカー全体のバランスが悪くなることもあるので 慎重に行う必要があります。
そこで、本記事では できる限り正確にスクエアカーボンの中央に穴をあけるための方法を以下の手順に分けて解説していきます。
①穴あけガイドの用意
まず、中央に穴をあけるためのガイド用アイテムが必要となりますが、これは以下のように3つの連続したビス穴があるステー・プレートであれば何でも構いません。
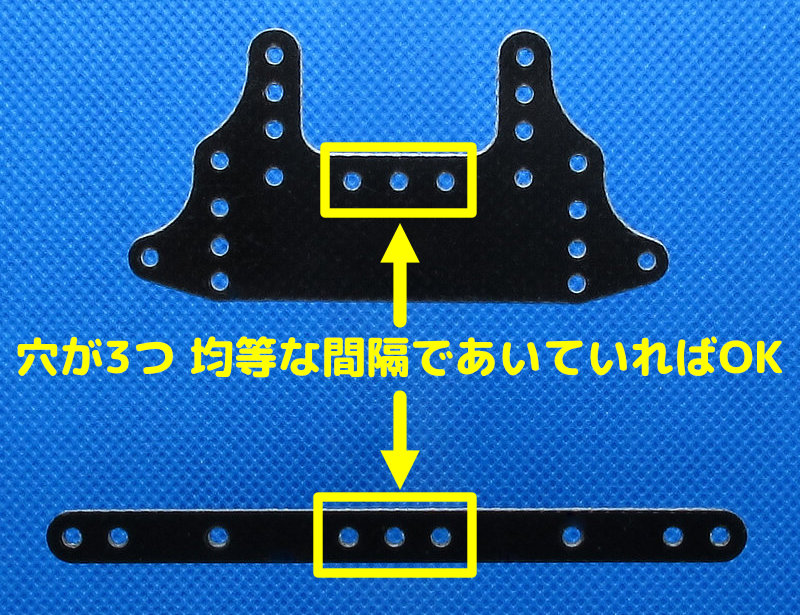
何でも構いませんとはいったもののガイドとして使用するステー・プレートはカーボンタイプをおすすめします。
カーボンタイプを進める理由は、カーボンをガイドとして使用した方が より正確な位置取りがしやすいからです。
何故カーボンの方が正確な位置取りがしやすいかは本記事では省略しますが、カーボンステー・プレートが用意できるのであればそちらを優先して使用してください。
尚、穴あけガイド用のステー・プレートを以後 ガイド用プレートという名称で解説を進めていきます。
②ガイドとの結合
ガイド用プレートが用意できたら、スクエアカーボンとガイド用プレートを以下の位置でビス・ナットを使用し結合させていきます。
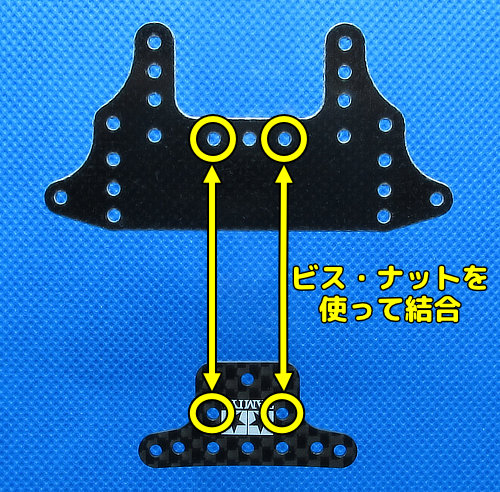
※今回はFRPブレーキステーをガイド用プレートとして使用していきますが、前述したように できればFRPではなくカーボンタイプを使用することをおすすめします。
結合時は互いのプレートがズレていないかをしっかり確認することをお忘れなく。
以下の画像のようにスクエアカーボンとガイド用プレートを結合させたらここでの作業は完了となります。
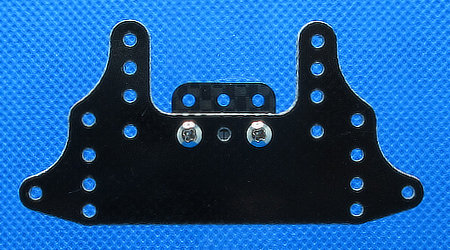
尚、ステー・プレート間のズレを減らす方法については以下の記事にて詳しく解説しているので、より正確に作業したいという方は ご参照ください。
ちなみにスクエアカーボンを2つ用意できるのであれば、以下のように4箇所の固定が可能となり、より加工精度が上がります。
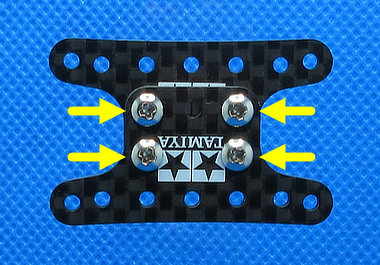
③穴あけ
ガイド用プレートとの結合が完了したら、ガイド用プレートのビス穴を穴あけガイドにしてスクエアカーボンの中央部に穴を追加していきます。
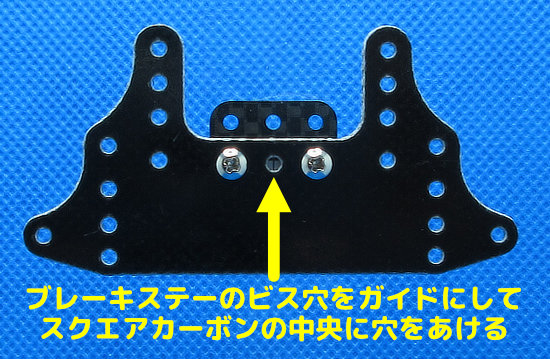
穴あけには2mmドリル刃を使用します。
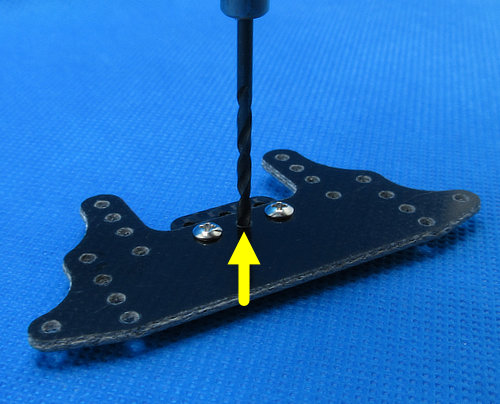
もし、2.1mmドリル刃を所持しているのであれば 2.1mmドリル刃を使用した方がより正確な穴をあけることが可能です。
ただし、プレートのビス穴の形状によっては2.1mmドリル刃だと刃が通せないこともあるので、その場合は2mmドリル刃で構いません。
スクエアカーボンの中央部に穴ができたら、ガイド用プレートを取り外して 穴あけ作業は完了となります。
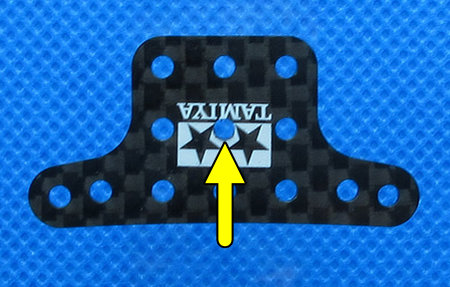
④穴の拡張
前の作業で中央部に穴があきましたが、この段階ではまだ穴が小さいので ドリル状のビット等を使用して穴を拡大していきます。
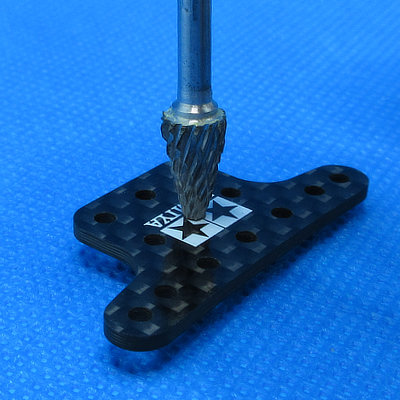
穴の拡張サイズは直径5mm程で構いません。
それより小さい分にはまったく問題ありませんが大きくしすぎてしまうと取り返しがつかなくなるので、くれぐれも穴の拡張しすぎにはご注意ください。
穴を拡張しすぎない対策として、以下の画像のように マルチテープを貼り 削るラインを分かりやすくします。
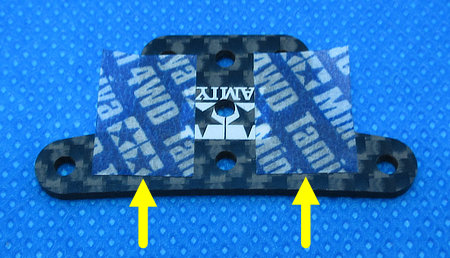
上の画像は分かりやすくするために両サイドに計2枚貼っていますが、中心穴を均等に拡張していくので 1枚貼るだけでも構いません。
そして、以下の画像のように ある程度穴を拡張できればOKです。
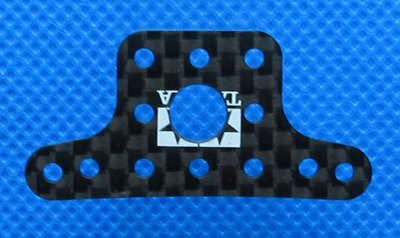
どの辺まで削って良いか分からない方は、表面にプリントされているTAMIYAの文字の最初の「T」と最後の「A」を残す形にしておけばOKです。
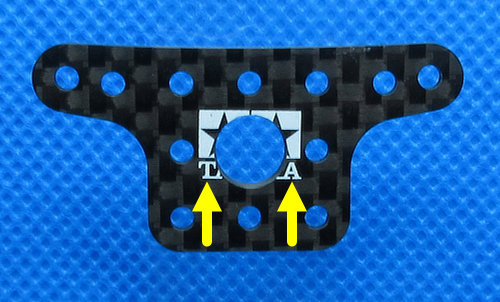
必ずしも上の画像と同じように穴を拡張する必要はなく、穴の大きさは若干異なっても構いません。
そして、ある程度の穴の拡張が完了したらスクエアカーボンの加工作業は一旦完了となります。
これ以降の作業は未加工のFRPマスダンパープレートと同じ作業になるので、前述している『マスダンパープレートの穴の拡張』の手順から引き続き加工作業を実施してください。
スタビヘッドの加工
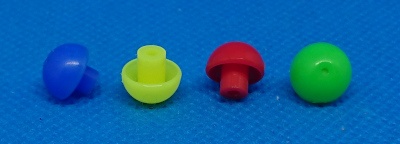
ここではリヤアンカーの可動の要となるスタビヘッドの加工方法を解説していきます。
スタビヘッドの加工概要については「ヘッド部分のカット」「穴の拡張・貫通」「円筒部分のカット」があり どの加工から実施しても構いません。
個人的には以下の加工手順がおすすめとなります。
次からは上記のおすすめ加工順に各加工方法の詳細を解説していきます。
①ヘッド部分のカット
まずはマスダンパープレートにスタビヘッドをフィットさせるためにヘッド部分をカットしていきます。
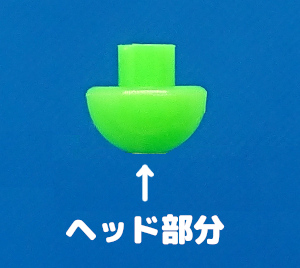
加工方法説明の前にヘッド部分カットの重要性を以下の断面図をベースに話していきますが、以下はヘッド部分が削り切れていない状態となります。
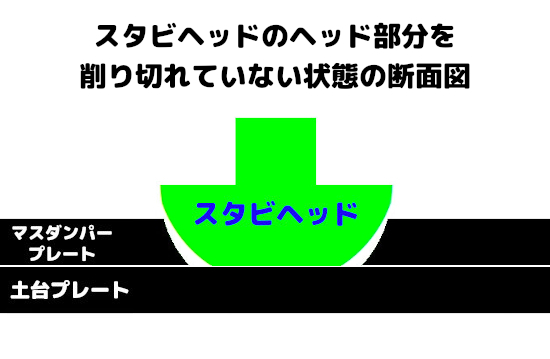
上の断面図は一見するとマスダンパープレート側の穴拡張が失敗したかに見えますが マスダンパープレート側は理想的な曲線の穴拡張ができている状態となっています。
しかし、スタビヘッドのヘッド部分が削りきれていないために マスダンパープレートとスタビヘッドがフィットせず隙間ができてしまい、結果マスダンパープレートがガタつくことになってしまいます。
こうなってしまわないためにもスタビヘッドのヘッド部分はマスダンパープレートからはみ出てしまわないようカットする必要があります。
どのくらいカットするかは マスダンパープレートの加工具合によって異なりますので、加工したマスダンパープレートにスタビヘッドをセットし、はみ出している部分を確認しカットしていきます。
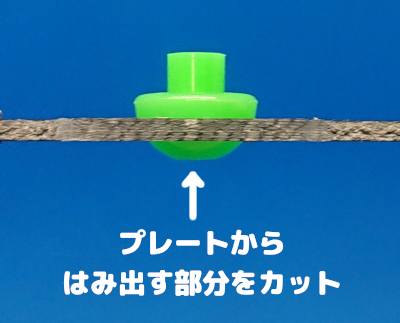
このはみ出した状態でスタビヘッドのヘッド側をペンでなぞるとカットする箇所が分かりやすくなるのでおすすめです。
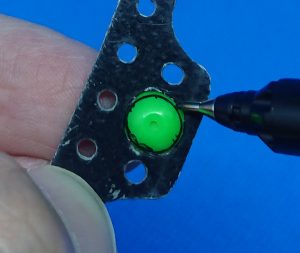
ペンでなぞる際にスタビヘッドが傾いてしまうとカットラインもずれてしまうので、スタビヘッドが垂直にセットされていることを確認しましょう。
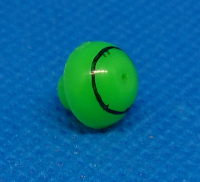
ヘッド部分のカットにはニッパーとヤスリを使っていきますが小さいパーツが故にカットはやりづらい作業でもあります。
そこでより作業をやり易くするために長めのビスとスペーサーを用意し、プラスドライバーを使って以下のようにスタビヘッドに取り付けます。
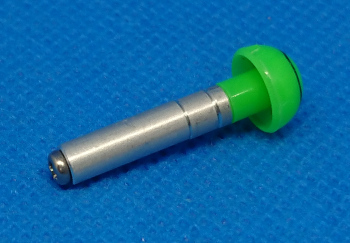
こうすることでカット作業が格段に楽になるので、直接スタビヘッドを持っての加工はやりづらいという方は試して頂ければと思います。
ヘッド部分をカットする準備ができたら、まずはニッパーでざっくりカットします。
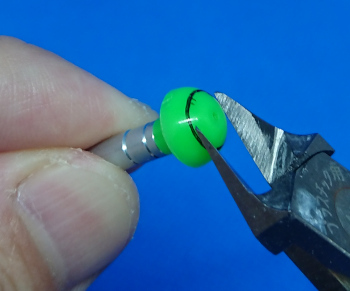
ここでカットしすぎてしまうと取り返しがつかないので、少し浅めのカットで構いません。
ある程度カットしたら仕上げにヤスリで慎重に削っていきます。
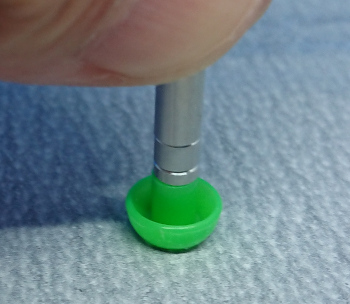
ここで使用するヤスリはなんでも構いませんが、個人的には紙ヤスリでやると削りやすいのでおすすめです。
あとはマスダンパープレートからはみ出さないところまで削り、削り終わったらビスとスペーサーを取り外してヘッド部分のカットは完了となります。

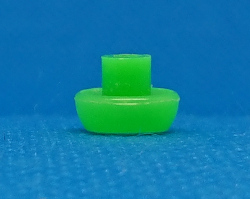
削りすぎには注意
ヘッド部分はマスダンパープレートからはみ出さないギリギリのところまで削るのが理想です。
少し削りすぎる分にはリヤプレートのガタつきにはあまり影響しないので、マスダンパープレートからはみ出さなければ多少削り方はいびつでも問題ありません。
注意すべきなのは「削りすぎて円管の部分に達してしまう」ことで、ヘッド部分を削りすぎてしまうと円管との根元部分に達しスタビヘッドが以下のようになり 使い物にならなくなってしまいます。
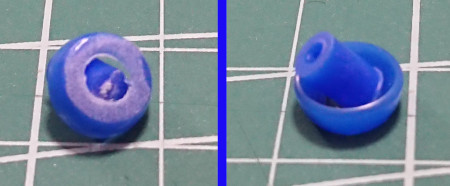
実はこれがマスダンパープレートの穴を拡張しすぎない理由でもあり、マスダンパープレートの穴を拡張しすぎると どうしてもスタビヘッドのヘッド部分も削る必要があり それに合わせ削ると上の画像のような状態になってしまいます。
こうならないためにもマスダンパープレートの穴を拡張しすぎないよう注意しましょう。
②穴の拡張・貫通
ここではスタビヘッドにリヤアンカーの支柱を通すことと可動をスムーズにするために、スタビヘッドの穴を拡張・貫通していきます。
穴の拡張・貫通にはドリル刃を使用しますが、ドリル刃のサイズについては2.1mm~2.5mmが推奨です。
何故、2.1mm~2.5mmとアバウトな数値かと言いますと、正直なところ どのサイズでもOKだからです(笑)
穴の直径が2.1mmに近いとバンパーはぐらつきにくくなり安定性が増す反面 可動が若干スムーズにいかなくなります。
それに対して 穴の直径が2.5mmに近いと可動はスムーズになりますがバンパーが多少ぐらつきやすくなりやや安定性が落ちるので、それぞれの穴の大きさには一長一短あります。
個人的には2.5mmが推奨で、ぐらつきやすくなると言っても 2.1mmの穴の時と比べて 明らかに違うわけでもなく、2.5mmの穴でもしっかりとバンパーとしての安定性もあります。
それと2.5mmドリル刃自体も100円ショップで購入でき、追加で購入したとしても費用負担が少なくて済みます。
もし、2.1mm・2.2mm・2.3mm・2.4mm・2.5mmのドリル刃を所持しているようであれば、まずは最小の2.1mmから拡張させ可動を確認し 可動がイマイチだと感じたら徐々にドリル刃のサイズを上げていくと良いかと思います。
では、肝心の 穴の拡張・貫通の加工方法ですがドリル刃をスタビヘッドの既存穴がある円筒側から通して、ドリル刃で穴を拡張しながら貫通させていきます。
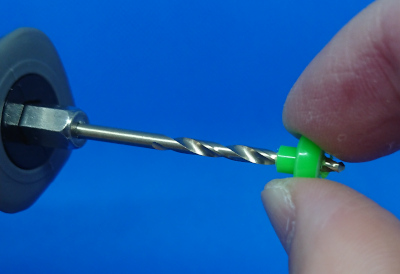
ここでの作業のコツとしてはドリル側を回さずに、スタビヘッド側を回すとやり易くなります。
スタビヘッドを回す際に 指がすべってしまうという場合はスタビヘッドの周りにマルチテープを貼るとすべりにくくなるので試して頂ければと思います。
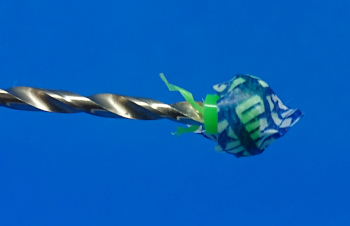
穴を貫通させた後はバリ(不要な出っ張り)がでるのでニッパーでカットしていきます。
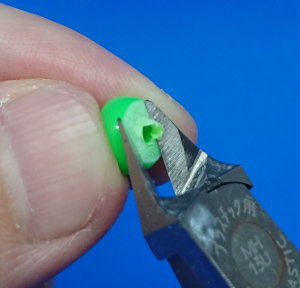
③円筒部分のカット
最後にリヤアンカーの可動域を増やすために円筒部分をカットしていきます。
この円筒部分についてはカットしなくてもリヤアンカーとしての動作はしてくれますが、未加工の状態だと可動域が幾分か制限されてしまうのでカットすることをおすすめします。
カットについては真横からスタビヘッドを見た時に、円筒部分が1~2mmほどはみ出した状態にするのがおすすめです。
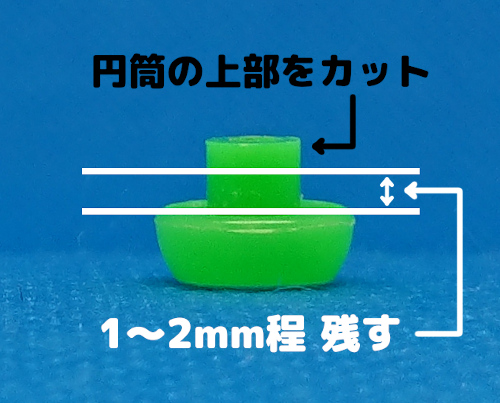
円筒部分のはみ出す部分が長い方がバンパーとしての安定感は上がる一方で可動域はやや落ち、逆にはみ出す部分が少なければバンパーとして安定感はやや落ちますが可動はよりスムーズになります。
どのくらいの長さが適切かはマスダンパープレートの穴の拡張度合いによっても異なりますので、まずは円筒部分を長めに残しておいて、実際に組み立ててから可動を確認し まだ長いと感じたらカットしていくほうが無難かと思われます。
カット方法についてはニッパーとヤスリを使い、あらかじめカットラインに線を引いてからカットするのもありですし、何も印を付けず目視でザックリ カットするのもありでお好きなやり方で構いません。
今回は個人的におすすめな加工方法を紹介していきます。
まずFRPステー・プレートにドリルかリューターで5mm~8mm範囲内の穴をあけ、その穴にスタビヘッドの円筒部分を通します。
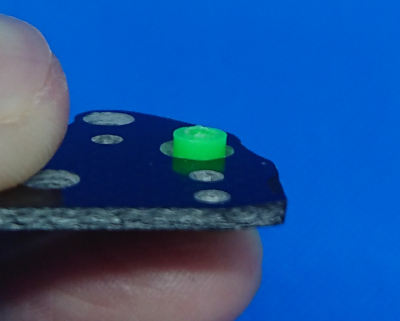
このまま指でスタビヘッドをおさえた状態にしたままで はみ出た円筒部分をニッパーでカットします。
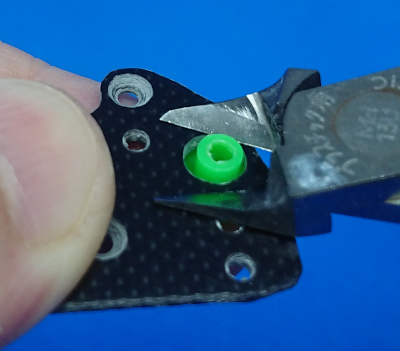
FRPステー・プレートの幅が1.5mmなので、ステーの面に沿ってニッパーを当て切断すれば円筒部分を1.5mm残した形でカットできます。
他にも簡易スパナ(厚さ約1.7mm)を当ててカットすることで、FRPステー・プレートよりも やや多めに円筒部分を残すこともできます。
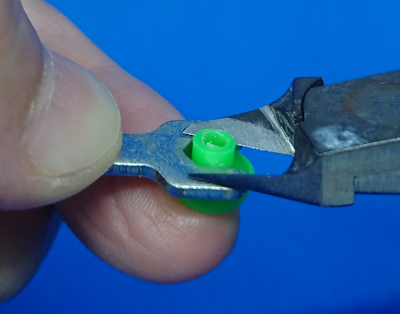
また、上記の方法で一気にニッパーで切断した際に下の画像のように円筒部分が歪むことがあります。
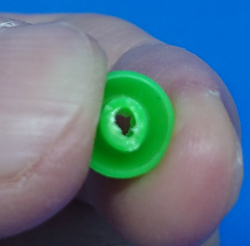
その場合は円筒部分をラジオペンチ等で挟んで 軽く押すと元の形状に戻すことができます。
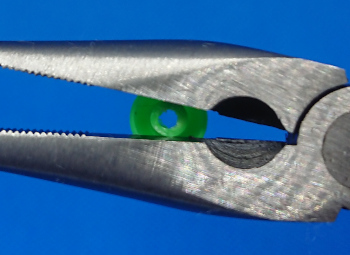
更にもう少しだけ削りたかったり 切り口を綺麗に整えたい場合は、ヘッド部分の加工と同様にヤスリがけをしていきます。
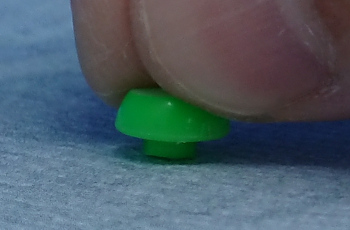
円筒部分のカットについては、そこまで綺麗に整えなくても安定性や可動には影響がないので ある程度アバウトな加工でも問題ありません。
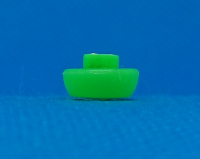
以上でスタビヘッドの加工は完了となります。
リヤブレーキステーの加工
ここではリヤアンカーの土台となるリヤブレーキステー(以下 ブレーキステー)の加工方法を解説していきます。
ブレーキステーはリヤアンカーの土台になるパーツであり そこそこの負荷がかかるためカーボンタイプが理想ですが、用意できなければFRPタイプでも問題ありません。
(今回はFRPタイプを加工していきます)
このブレーキステーの加工についてはバリエーションが豊富で基本的には2枚のブレーキステーを用意しますが、場合によっては1枚でも対応可能となりますので、ご自分のマシン・シャーシに合った加工方法を選択して頂ければと思います。
本記事ではブレーキステーを2枚使用する方法をメインで解説していきます。
またリヤアンカーの加工ではFRPマルチワイドステーを使用した加工方法も多く紹介されており、ブレーキステーの代わりにFRPマルチワイドステーを使用した加工方法も別途紹介していきます。
各ビス穴の役割について
まず加工解説の前にブレーキステーの各ビス穴の役割について紹介していきます。
各ビス穴の役割を把握することでブレーキステーの様々なバリエーションの加工にも対応できるようになってくるので、リヤアンカーを初めて作成されるという方は目を通して頂ければと思います。
ブレーキステーで使用するビス穴及び使用目的は以下となります。
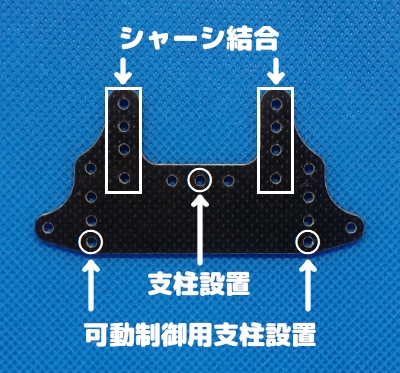
次からは上記の各ビス穴について詳しく説明していきます。
シャーシ結合のビス穴
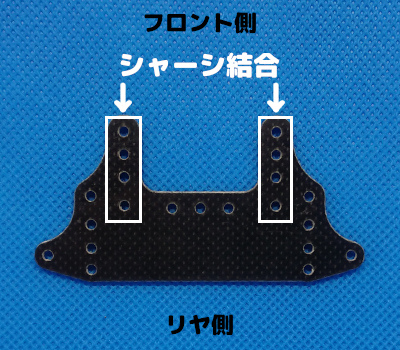
シャーシ結合のビス穴はシャーシと結合させるためのもので、枠内のいずれか1組(左右1個ずつ)を使用します。
使用するビス穴がフロント側に近いとローラーベース(フロントローラーとリヤローラーの距離)が長くなり、ビス穴がリヤ側に近いとローラーベースが短くなります。
どの穴を使用するかはご自由ですが、フロント側寄りのビス穴を使用する場合 ブレーキステーを2枚使用した時にマシンの全長が公認競技会規則で定められている165mmを越えてしまう可能性があるので、フロントバンパーの構成も考慮して どのビス穴を使用するか判断しましょう。
尚、本記事ではリヤ側寄りの2組のビス穴を使用するパターンの構成を紹介していきます。
支柱設置のビス穴
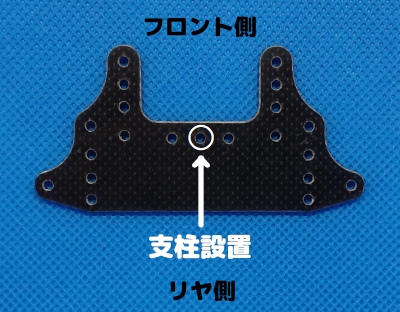
支柱設置のビス穴はリヤアンカーの支柱であるキャップスクリューもしくはビスを設置するためのもので、どの加工バリエーションでもビス穴の位置は上記の箇所で固定となります。
可動制御用支柱設置のビス穴
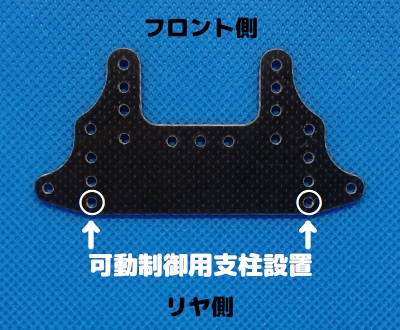
まず可動制御用支柱(ストッパー)とはバンパーの可動を制御するための支えであり、リヤアンカーは1軸ということで 支えがないとバンパーがぐらつき本来のバンパーとしての機能が果たせなくなるので、可動制御用支柱(ストッパー)が必須となります。
そしてこの可動制御用支柱設置のビス穴に、可動を制御するための支柱を設置します。
使用するビス穴の位置はバンパーの形状によってはベストな位置も変わってきますが、これ以上フロント側に寄せてしまうとバンパー側の加工(削る)が必要となり バンパーの強度が著しく落ちてしまう可能性もあるので基本的にはこのビス穴を使用することになります。
尚、この可動制御用支柱設置のビス穴は2枚目のブレーキステーの結合用としても使用していきます。
1枚目の加工
ここからはブレーキステーの加工方法を解説していきます。
1枚目のブレーキステーは必須となり、この1枚目でシャーシ結合・支柱設置・可動制御用支柱(ストッパー)設置のすべてを担います。
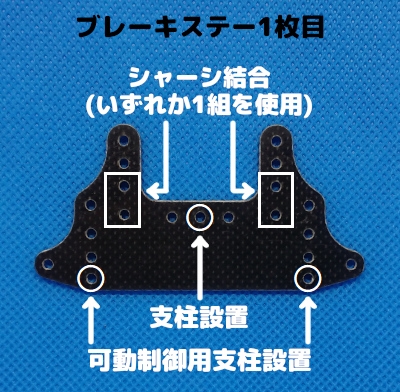
ブレーキステー1枚目はこれらのビス穴を残して 不要な箇所をカットしていきます。

上画像の白丸は使用するビス穴を示し、加工パターン1と加工パターン2で使用するシャーシ結合のビス穴が異なるためカットする箇所も若干変わってきます。
加工パターン1はどのシャーシにも対応したオーソドックな加工パターンであり、ブレーキステーをどう加工すべきか迷ったら とりあえずこの加工パターンで良いかと思います。
加工パターン2はよりシャーシに接近した加工パターンであり、基本的にはMSシャーシ向けのものとなります。
なぜ加工パターン2がMSシャーシ向けかと言いますと、MSシャーシは他のシャーシに比べてリヤバンパーを取り付けるビス穴とシャーシとのスペースが広めになっています。
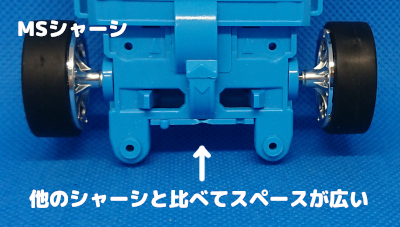
これによってリヤアンカーを設置した際に他のシャーシに比べてスペースに若干の余裕ができます。
MSシャーシ以外でも加工パターン2のブレーキステーを設置できなくはないですが、リヤアンカー側の加工には限界があるため どうしてもシャーシ側の加工が必要となり少々手間がかかってしまいます。
とりあえず加工パターン1でカットしておけば、後から加工パターン2の形に変更することも可能なので、まずは加工パターン1のカットをすることをおすすめします。
干渉箇所のカットにはリューターのダイヤモンドカッターを使用してざっくり削り、その後円筒形ビットなどで綺麗に整えていきます。
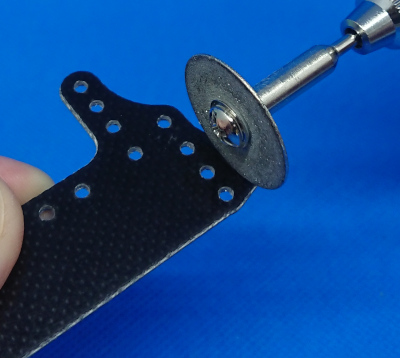
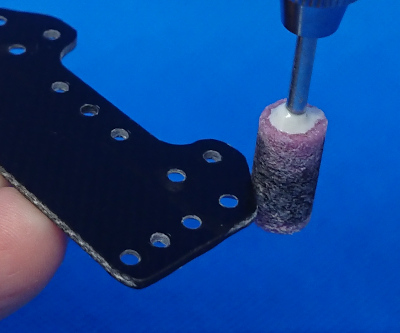
そして、加工後のブレーキステーは以下となります。
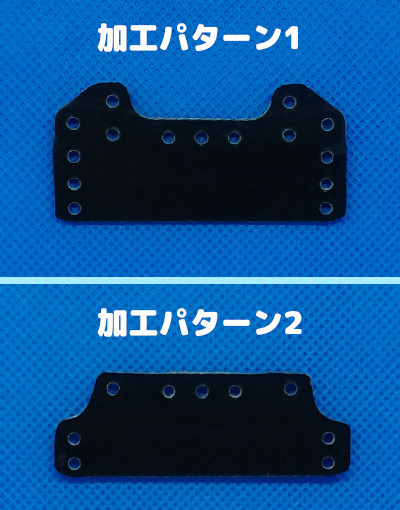
これで1枚目のブレーキステーは完成となりますが、さらに軽くしたい場合は以下の箇所をカットしても構いません。
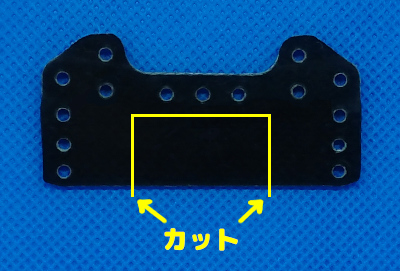
※いずれの加工パターンもカットする箇所は同じなので加工パターン1の加工例のみ掲載しています。
上のカット箇所は一見すると「もっと広くカットできるのでは?」と思う方もいるかもしれませんが、さらに軽くしようとしてカットラインをビス穴1個分横に広げてしまわないよう注意してください。
何故カットラインを広げては駄目かと言うと、これ以上 横を削るとマスダンパープレートの固定が不安定となりリヤアンカー自体のガタに繋がってしまうからです。
以下の画像はマスダンパープレートやスタビヘッドを取り付けたものとなりますが、マスダンパープレートの左右の最も長い部分の下には必ずブレーキステーがあるようにしてください。
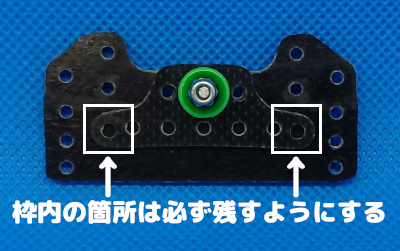
マスダンパープレートの中央下部の部分は空洞になっても構いませんが、上の画像の左右の枠内の部分だけはしっかりと残すようにしてください。
このことからマスダンパープレートとまったく接触していない 下の部分についてはカットしても問題ありませんので、ギリギリまで軽くしたいのであれば 両サイドのビス穴の強度がしっかり保てる範囲でギリギリまで広げてカットしてもらって構いません。
カットする際はカットする箇所を分かりやすくするためにマルチテープなどを貼り、テープのラインに沿ってリューターのダイヤモンドカッターでカットしていきます。
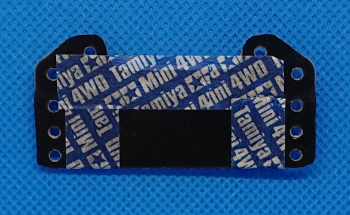
ちなみにブレーキステーを1枚しか使用しない場合は上記の箇所をカットしてしまうとブレーキスポンジが貼れなくなってしまうので、ご自分の使用用途に合わせてカットすべきかどうか判断しましょう。
2枚目の加工
2枚目のブレーキステーはブレーキスポンジやマスダンパーを設置するために使用します。
2枚目のブレーキステーは1枚目のブレーキステーと結合させるためのビス穴が必要となり、いずれかのビス穴をブレーキステー間 結合用として使用します。
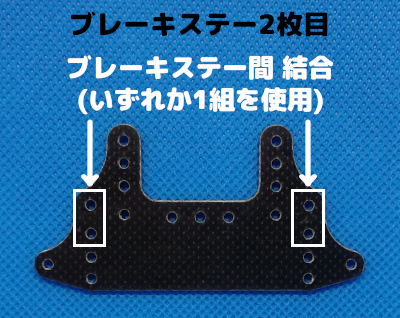
使用するビス穴が上段の場合 下段のビス穴に比べてマシン全長が長くなるので、公認競技会規則で定められているマシン全長165mmを越えてしまわないよう、ご自分のマシン構成にあったビス穴を選んでいきます。
尚、今回は上段のビス穴を使用する加工パターンで解説していきます。
加工については、ブレーキステー間の結合の際は2枚目のブレーキステーが下段となるため皿ビス加工が必要となり、使用するビス穴の皿ビス加工と、不要となる部分をカットしていきます。
まずは皿ビス穴加工ビットを使い皿ビス加工をします。
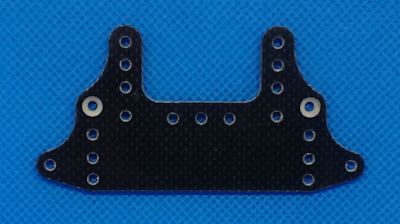
※皿ビス加工については、ブレーキステー間 結合の際に2枚目を上にする場合は皿ビス加工は不要となるので、どちらのブレーキステーを上にするか決めていない方は一旦皿ビス加工は保留でも構いません。
ちなみにここで皿ビス加工したとしても、2枚目のブレーキステーを上にした際に目立った支障はありませんので、皿ビス加工をしてしまっても取り返しがつかないことにはなりませんのでご安心ください。
皿ビス加工が終わったら、不要箇所をカットします。
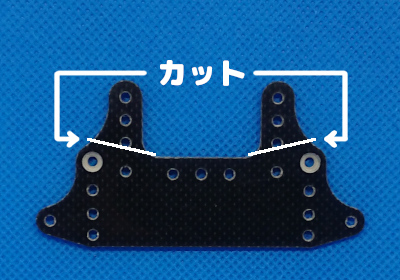
不要箇所のカット方法は1枚目のブレーキステーと同じようにリューターのダイヤモンドカッターと円筒形ビットなどを使用し綺麗に整えていきます。
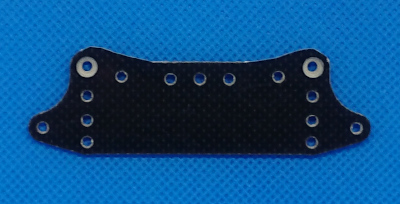
以上で2枚目のブレーキステーの加工は完了となります。
バンパーの加工
ここではリヤアンカーのバンパー部分の加工方法を解説していきます。
使用するバンパーについてはマスダンパープレートの以下の画像の白枠内のビス穴に適合するものであればどれでもOKです。
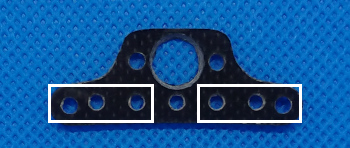
基本的にはどのステー・プレートでも上記のビス穴に適合するので、お好きなものを選んで構いませんがステー・プレートによっては加工の手間がかかるものもあるのでご注意ください。
本記事ではリヤアンカーでの採用率が高いフロントワイドステー(以下 フロントステー)をベースに加工方法を解説していきます。
フロントステーは以下の箇所を加工していきます。
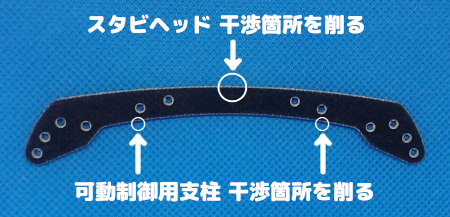
まずスタビヘッドとの干渉箇所の加工については、スタビキャップに干渉しないところまで削ればOKで、マスダンパープレートの穴のようにスタビキャップの曲線に合わせて綺麗に削る必要はありません。
削る際は大きめの円筒形ビットを使うと簡単に削ることができ、バンパーの強度さえ保てれば多少雑に削っても問題ありません。
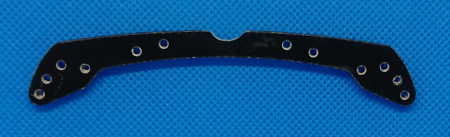
次に可動制御用支柱との干渉箇所を削っていきますが、フロントステーが未加工な状態のままだと可動制御用支柱と密着しすぎてATバンパーとしてスムーズに可動しないので、スムーズに可動させるために削っていきます。
具体的にどの箇所をどのくらい削るかは実際にリヤアンカーを組み立て 可動制御用支柱との干渉度合いを確認しながらおこないます。
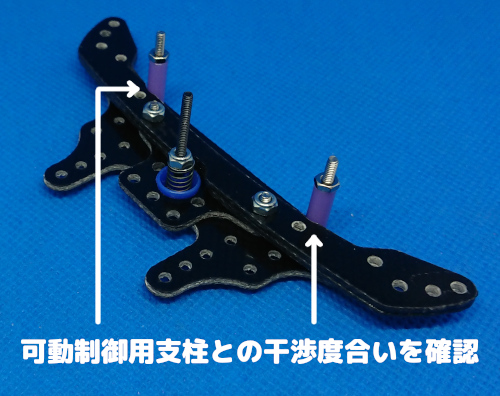
※組み立て方法については「リヤアンカーの組み立て」をご参照ください。
可動制御用支柱との干渉箇所及び干渉度合いを確認したら フロントステーに目印などを付けて削っていきますが、削るのはほんの僅かで良く、逆に削りすぎてしまうとバンパーがガタついてしまうので注意してください。
削る際はリューターの円筒形ビットを使うと簡単にできます。
しかし、電動リューターだと「ついつい削りすぎてしまった…」ということもあるので初心者の方は半丸型の棒ヤスリ等で少しずつゆっくりと削っていったほうが良いかもしれません。
そして、削り終えたバンパーが以下となります。
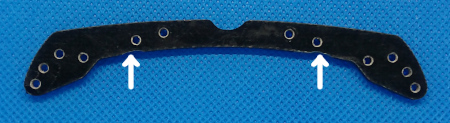
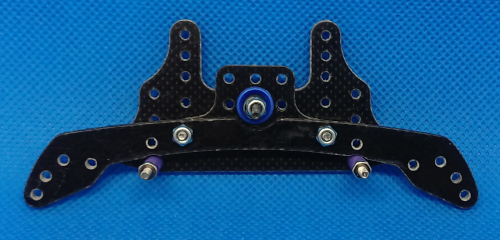
一見すると削っていないようにも見えますが、上の画像のように僅かに削るだけで可動がスムーズになります。
ちなみにフロントステーについては強度を上げるために本記事では2枚重ねのステーを使用していますが、必ずしもステー・プレートを2枚重ねる必要もなく どうするかはお好みで。
ただ、支柱部分との干渉箇所を削ることでステー・プレートの強度が落ちてしまうので できれば補強しておきたいところではあります。
ステー・プレートを2枚重ねした補強方法については以下の記事て詳しく説明しているので、よろしければこちらもご参照ください。
尚、ステー・プレートを重ねる際は、ケースによっては事前に引っ掛かり防止対策をした方が良く、引っ掛かり防止用の加工方法については以下の記事をご参照ください。
仕上げ
ここではリヤアンカーを実際の走行で使用できるように、組み立てから最終調整までを解説していきます。
リヤアンカーの組み立て
これまで加工してきた各パーツを結合させリヤアンカーを組み立てていきます。
マスダンパープレートとフロントステーの結合
まずはマスダンパープレートとフロントステーと結合させます。
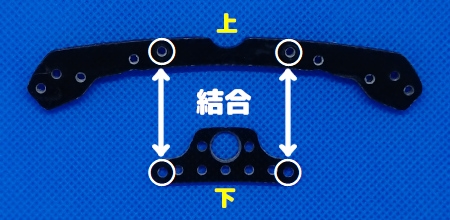
結合にはマスダンパープレートの裏面の皿ビス加工したビス穴に皿ビス(8mm)を通し、その上にフロントステーを乗せロックナットで固定します。
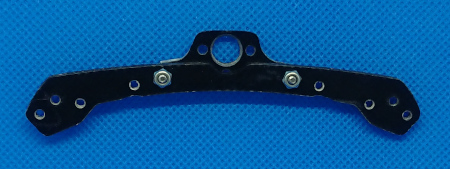
今回フロントステーを2枚重ね(厚さ3mm)としているので8mmの皿ビスを使用していますが、フロントステーが1枚ということであれば6mmの皿ビスで問題ありません。
ブレーキステーの結合
次にブレーキステーの1枚目と2枚目を結合させ土台プレートを作成します。
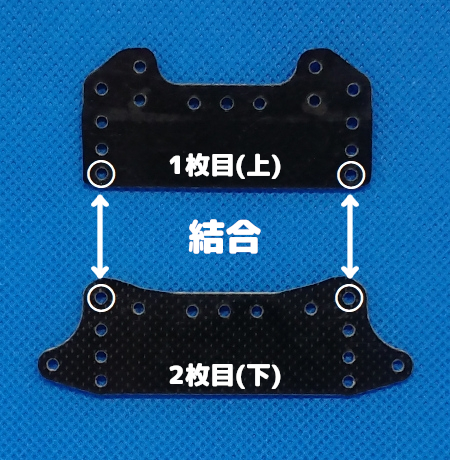
結合はブレーキプレート2枚目を下にして 2枚目の裏面の皿ビス加工したビス穴に皿ビスを通し、その上にブレーキステー1枚目を乗せ、更にその上に可動制御用支柱となるスペーサーを取り付けてロックナットで固定します。
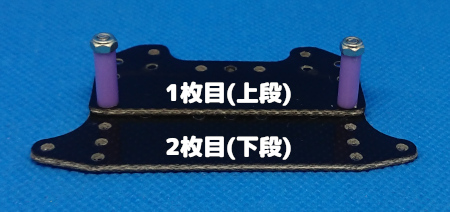
ここで取り付けるスペーサーの長さは12mmが推奨で、使用する皿ビスは15mmだとギリギリ長さが足りないため 上の画像ではカットして17mmにした皿ビスを使用しています。
※ビスのカット方法については「ビス・ネジ 加工方法」の記事をご参照ください。
ビスカットが面倒くさいということであれば以下の画像のように20mmの皿ビスを用意して12mmスペーサーと3mmスペーサーを取り付けてビスの余長を無くしていきます。
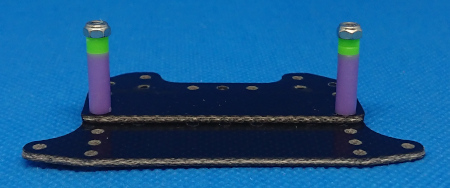
取り付けるスペーサーを12mmだけにしたいという場合は、20mmの皿ビスを取り付け 突出したビスの箇所にゴムキャップなどを付け、ビスの先端部分を保護していきましょう。
スペーサーを短くする場合はリヤアンカーの可動域に注意
可動制御用支柱(ストッパー)としてのスペーサーの長さは必ずしも12mm以上である必要はなく、それよりも短くしても構いません。
ただ、スペーサーを短くする場合は スペーサーの高さ以上にリヤアンカーが可動してしまわないよう注意しましょう。
以下の画像はスペーサーの長さを短くした時にリヤアンカーが可動した状態ですが、バンパーがストッパーの高さを越えてしまっています。
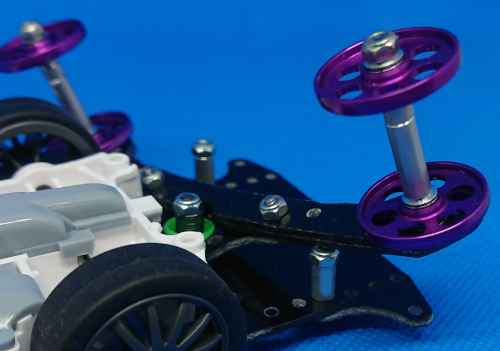
バンパーが更にストッパーを越えてしまうと予期せぬ位置にバンパーが固定されてしまいます。
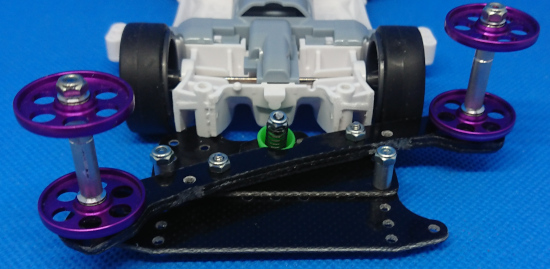
この状態になってしまうと余程のことがない限りバンパーも元に戻らなくなり バンパーが斜めの状態で走行し続けなくてはいけなくなります。
こうなってしまわないようにするためにも、ご自分のリヤアンカーの可動域に合わせてスペーサーの高さを調整するようにしていきましょう。
先程の説明でブレーキステー1枚目を上に・2枚目を下に結合すると言いましたが、1枚目を下にして2枚目を上にする構成でも構いません。
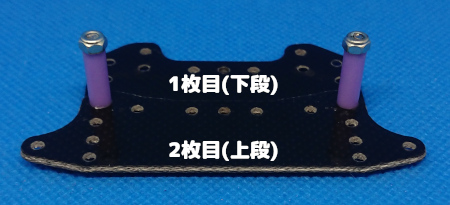
マシンの車高などの関係でブレーキステーの高さを変えたいという場合は上画像のパターンを試してみてはいかがでしょうか。
ただしブレーキステー2枚目を上にする場合、マスダンパープレートと干渉してしまわないよう注意しましょう。

ブレーキステー2枚目を上にした場合、マスダンパープレートと同じ高さに位置となり ブレーキステーがマスダンパープレートに干渉してしまうとバンパーが不安定になることがあるので くれぐれも干渉してしまわないよう注意しましょう。
尚、ブレーキステー2枚目を上段にする場合は、ブレーキステー1枚目の加工で可動域制御用支柱(ストッパー)を取り付けるビス穴に皿ビス加工が必要となるのでご注意ください。
各パーツの組み立て
上記パーツの結合が完了したら、最後に各パーツを組み合わせ リヤアンカーを組み立てていきます。
まずは土台プレートの支柱設置用ビス穴の裏面から支柱となるキャップスクリューもしくはビスを通します。
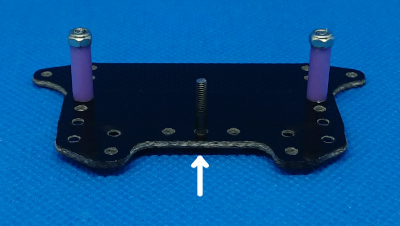
上の画像は25mmのキャップスクリューをカットしたものを使用していますが、無加工のキャップスクリューやビスでも構いません。
おすすめの支柱や選定方法については後半の「支柱で使用するパーツについて」にて解説していきます。
次に結合させたマスダンパープレートの拡張した穴の部分に支柱が通るようにして、土台プレートの上に乗せます。
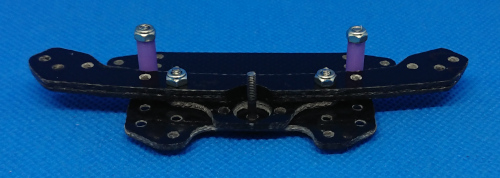
結合させたマスダンパープレートを乗せたら、次にスタビヘッド・スプリングの順番で支柱に通していきます。
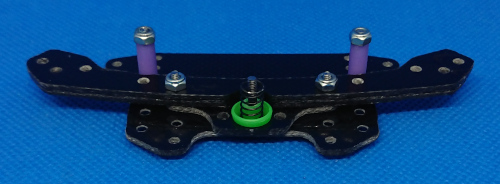
最後にロックナットで固定してリヤアンカー組み立てが完了となります。
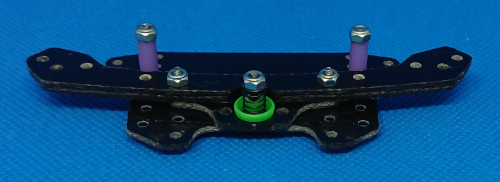
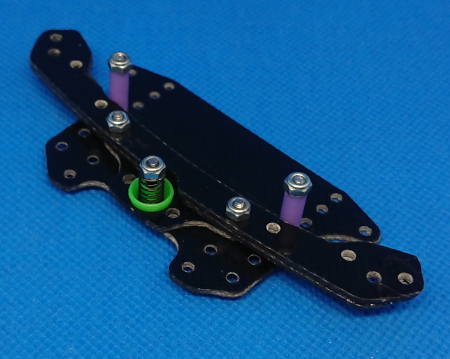
支柱で使用するパーツについて
上記のリヤアンカーを構成するパーツの一つである支柱について詳しく解説していきますが、まず支柱として使用するパーツはキャップスクリューもしくはビスを使用します。
これらのパーツで個人的に推奨するのがキャップスクリューで、そのキャップスクリューには25mmと30mmの2種類があります。
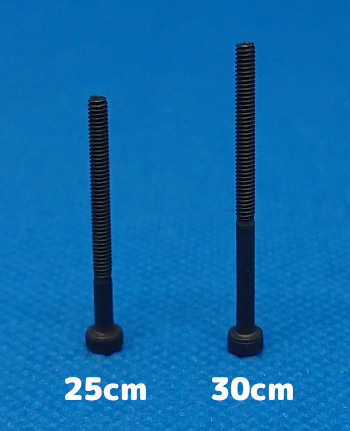
まずキャップスクリューをおすすめする理由として、キャップスクリューにはネジのギザギザがない部分があり この部分では スタビヘッドがよりスムーズに可動します。
実際にキャップスクリューとビスのそれぞれにスタビヘッドを通して動かしてもうらうと分かりますが、ビスだとゴリゴリする感じがしますが、キャップスクリューだとスムーズに動きます。
このことから可動をよりスムーズしたいのであればキャップスクリューが推奨となりますが、そのキャップスクリューも25mmと30mmで違いがあり、上の画像を見てもらうと分かるようにネジのギザギザがない部分の長さが違います。
25mmの方はギザギザがない部分がやや短く スタビヘッドが可動して少し上にいくだけでビスのギザギザにあたるのに対して、30mmの方はスタビヘッドが上に上がってもツルツルした部分内に留まるので常時スムーズに可動してくれます。
こうしたことを考えると30mmのスタビキャップがベストなんですが、30mmを使用した場合 ツルツルの部分が長すぎてロックナットが下まで設置できずスプリングに圧力が与えられなくなる欠点があります…
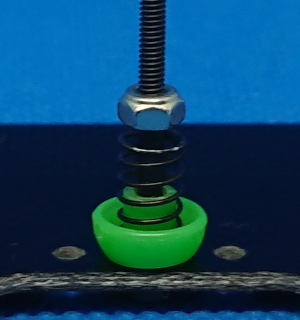
この対策としてマシンキットに付属しているシャフトの軸受け(POM)・カウンターギヤの軸受けを用意します。
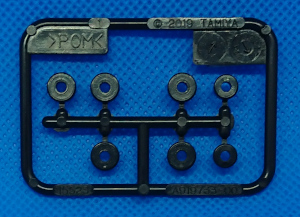
※これらのパーツは基本的にはどのマシンキットにも付属しています。
この軸受けパーツをスプリングとロックナットの間に入れることで30mmのキャップスクリューでもスプリング部分の幅(スプリングの圧力)を調整することが可能となります。
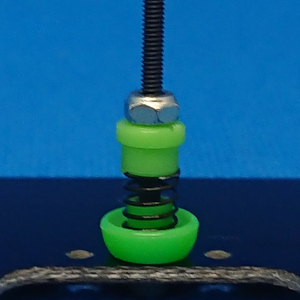
上記の方法であれば30mmキャップスクリューも問題なく使用できるようになりますが、僅かではありますが追加パーツ分の重量が増えるというデメリットもあります。
25mmも30mmもそこまで極端にスタビヘッドの可動に違いが出るというわけではありませんので、どちらの長さのキャップスクリューを使用するかはお好みで構わないかと。
またキャップスクリューの代わりに鍋ビスを使用する場合は長さ12mmの鍋ビスがおすすめで、できるだけビスを安定させるためマスダンパープレートの裏面は鍋ビスとワッシャーをセットにして取り付けていきましょう。
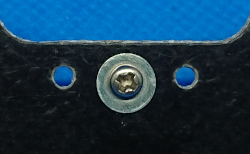
尚、本記事では25mmキャップスクリューをカットしたものを支柱として採用していますが必ずしもカットする必要はなく カットせずにビスの先端が飛び出ている場合はスタビキャップなどを付けて対処すればOKです。
ビスをカットしたいという場合のカット方法については以下の記事にて解説しておりますので、よろしければこちらもご参照ください。
また、支柱をしっかりと固定したいという場合はキャップスクリューをカットせずに長いままの方がよいケースもあります。
キャップスクリューを支柱固定に活用する方法については後述する『支柱を固定する』にて解説しているので、こちらを見てからキャップスクリューをどのくらいカットするかを判断してください。
シャーシへの取り付け
リヤアンカーの組み立てが完了したら、シャーシに取り付けていきます。
シャーシによっては未加工のままでは取り付けができないものもあり、リヤアンカーが設置できない場合はシャーシを加工する必要があります。
シャーシが未加工でリヤアンカーが設置できないという方は、以下の記事を参考にシャーシを加工してみてください。
そして、シャーシ結合する際はリヤアンカーの土台プレートのシャーシ結合用ビス穴にトラスビスもしくは鍋ビス(丸ビス)を使用していきます。

トラスビス・鍋ビスでなくても、シャーシ結合用ビス穴に皿ビス加工をしていれば皿ビスを使用しても構いません。
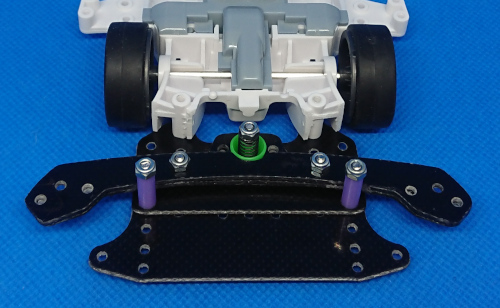
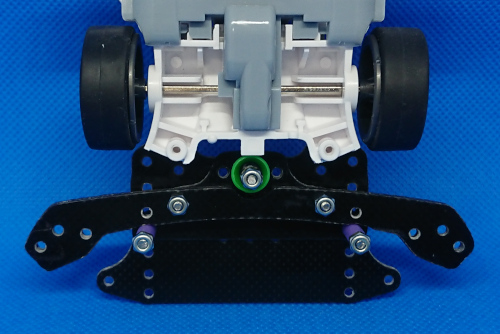
鍋ビスを使用する場合はワッシャーも忘れずに取り付けていきましょう。
リヤアンカーをシャーシにセットしたら、後はバンパー部分にお好みのローラーを取り付け、土台プレートにお好みのブレーキスポンジやマスダンパーを取り付けてリヤアンカーが完成となります。
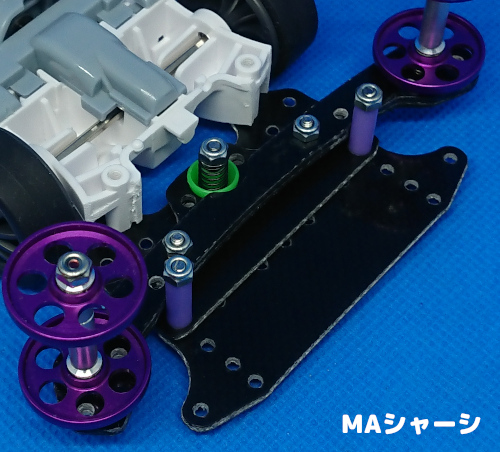
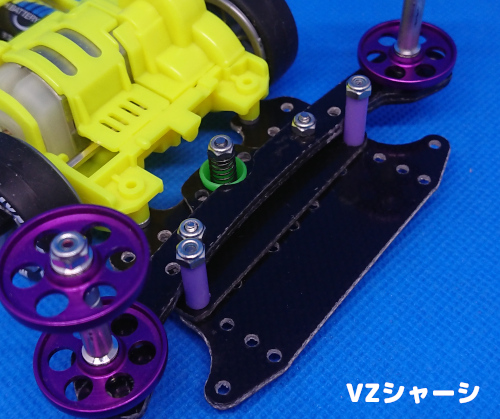
上の画像はブレーキステー1枚目に加工パターン1を採用したものとなりますが、ブレーキステー1枚目を加工パターン2にすることにより下の画像のように リヤアンカーをよりフロント寄りに設置することも可能となります。
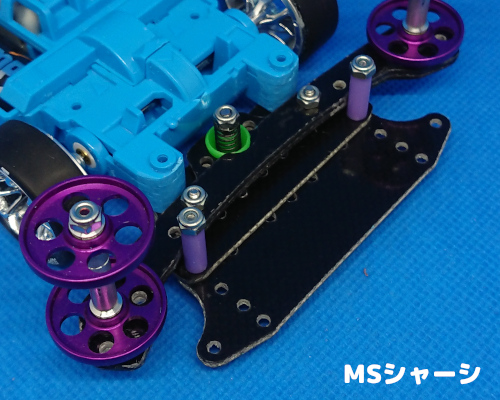
ただし、リヤアンカーをフロント寄りに設置する場合は、シャーシのボディーキャッチのツメをカットすることはもとより それ以外の部分の加工も必要になるのでご注意ください。
最終調整
リヤアンカーが完成したら最後にATバンパーとしての可動を確認していきます。
バンパーの可動がスムーズにいかないという場合はスプリングの圧力を弱める もしくは以下の箇所にグリスを塗っていきます。
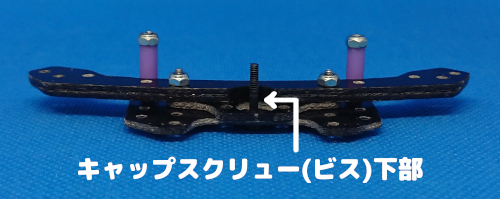
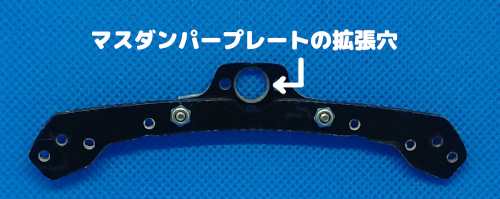
逆にバンパーが可動しすぎてぐらつくという場合は次の「ガタつきを抑える方法」にて対処法を解説しているのでそちらをご覧ください。
ガタつきを抑える方法
ここではリヤアンカーがガタついてしまう場合の対策方法を紹介し、より安定したリヤアンカーにするための方法を解説してきます。
スプリングの圧力を強くする
リヤアンカーを固定し安定させる力はスプリングの圧力に依存し、このスプリングの圧力を強くすることでリヤアンカーのガタつきを抑えることができます。
そのスプリングの圧力を上げる方法は2つあり、1つ目はスプリング自体を今よりも硬いものに変えることです。
現在タミヤからは以下の4種類のスプリングがありスライドダンパースプリングセットとスライドダンパー2スプリングセットが販売されています。
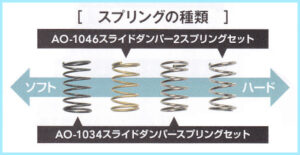
このスプリングを今よりも硬い(ハードな)スプリングに変えることで圧力を強くしリヤアンカーをより安定させることが可能となります。
ただし、スプリングの圧力を上げるということはガタつきを抑えると同時にリヤアンカーとしていなし効果が落ちるというデメリットもあるので注意してください。
そして、スプリングの圧力を上げる方法の2つ目はスプリングを固定させるロックナットを更に締めることです。
ロックナットを締めてスプリングの幅が狭くなればなるほどスプリングの圧力が増していくわけですが、このロックナットを締める方法は簡単にスプリングの圧力が微調整できるのが特徴です。
ただし、ロックナットを締める方法で注意して欲しいのは、スプリングの幅を狭くすると同時にスタビヘッドの可動域が減り、それによってリヤアンカー全体の可動域も減り、結果いなし効果が落ちてしまいます。
もしもロックナットを締めて丁度いいスプリング圧力になったのいいけど、スタビキャップの可動域が狭くなってしまったという場合は、スタビヘッドの円筒部分をさらにカットすることで可動域も広がってくるので そちらを試してみてください。
スプリングの圧力を上げる方法はリヤアンカーのガタつきを抑える反面 いなし効果が落ちるという欠点もありますが、自分のマシンに合った適度な固定力といなし効果を発揮できる圧力の調整をして頂ければと思います。
支柱を固定する
リヤアンカーがガタつく主な原因はスプリングの圧力によるものですが、それ以外もう一つ大きな原因として支柱となるキャップスクリュー・ビスの不安定さもあります。
支柱は基本的にスプリングの圧力のみで固定されており、スプリングの圧力を上げれば支柱も安定しますが 限界があり 支柱のグラつきを完全に抑えることはできません。
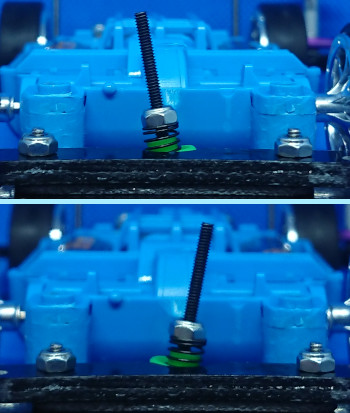
支柱が前後左右に傾いてしまうと当然バンパー部分もそれに合わせて前後左右にブレてしまいます。
そこで、支柱のブレを無くすための支柱固定パーツを作成方法及び利用方法を解説していきます。
支柱固定パーツの作成に必要なパーツ
支柱(キャップスクリュー・ビス)を固定させるためのパーツの条件として「支柱設置用のビス穴」と「シャーシ結合用のビス穴」の位置がまったく同じである必要があります。
そして、ブレーキステー1枚目の加工において加工パターン1と加工パターン2のどちらの形にしたかによって必要なパーツが変わってきます。
いずれの加工パータンも同じブレーキステーをもう1枚使えば済む話ではあるんですが、それだと使わない箇所が多すぎて勿体ない感じもしてしまうので、それぞれの加工パターンに合った 適切なパーツを紹介してきます。
まず、加工パターン1用の適切なパーツとしてはスーパーXシャーシ FRPリヤローラーステーがおすすめです。
加工パターン1用パーツとしては最も安く購入でき、加工した後に不要になった部分もヒクオのパーツなどで活用することができるため より無駄なく使えるパーツかと思われます。
これ以外にも価格は多少高くなりますが、ARシャーシ FRPリヤワイドステーやFRPマルチワイドリヤステーでも作成可能です。
加工パターン2用の適切なパーツとしてはFRPマルチ補強プレートがおすすめです。
このFRPマルチ補強プレートは価格も安いことはさながら 2枚付属しているので1つはリヤアンカー支柱固定用で もう1つは別の用途で使用することができます。
他に加工パターン2用のパーツとしてFRPマルチワイドリヤステーであれば、すでに同じビス穴はあいているのでビス穴を追加する作業を省くことも可能です。
それともう一つ用意するパーツとして無加工のキャップスクリューか長めのビスが必要になります。
キャップスクリューを使用する場合は25mm・30mmどちらを使用するかはお好みでお任せしますが、この場合はどちらかというと30mmタイプがおすすめです。
ビスを使用する場合は設置するシャーシによっても適切な長さが変わってくるので、一旦できるだけ長いビスを用意し設置後に適切な長さに変更する で構いません。
支柱固定パーツの作成方法
ここでは支柱固定パーツの作成方法を解説していきますが、ブレーキステーの加工パターン1用のパーツ作成方法を解説していきます。
今回、支柱固定パーツ用のパーツとしてスーパーXシャーシ FRPリヤローラーステーを使用し、以後このパーツを支柱固定パーツと呼んでいきます。
まずは加工済みブレーキステー(加工前・加工後どちらでOK)と支柱固定パーツをビス・ナットで結合させます。
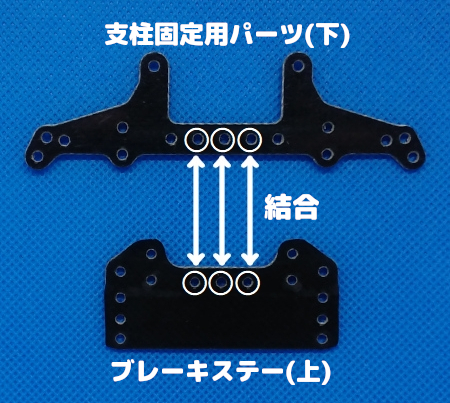
両パーツを結合する際はブレーキステーを上にして支柱固定パーツを下にしますが、逆に付けてもひっくり返せばいいだけなので何も考えずに結合して構いません。
それとビス止めする箇所に関しては左右2箇所のビス固定でも構いませんが 極力ビス穴の位置がズレてしまわないよう3箇所以上のビスで固定することを推奨します。
固定が完了したらブレーキステーの既存ビス穴をガイドにして2mmドリル刃で支柱固定パーツにビス穴を追加します。
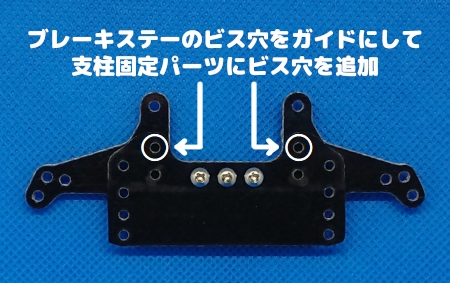
支柱固定パーツにビス穴を空けたらブレーキステーから取り外します。
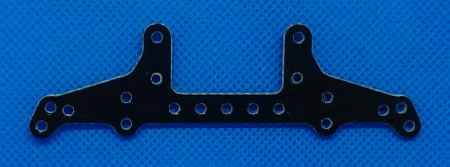
次に支柱固定パーツの以下の不要箇所をリューターのダイヤモンドカッターでカットしていきます。
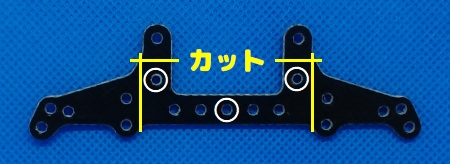
これで支柱固定パーツの作成は完了となります。
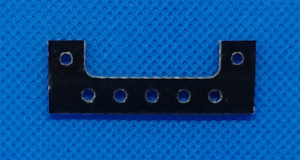
上の支柱固定パーツは必要最低限の箇所をカットした形となりますが、以下のビス穴さえ残して最低限の強度を保てれば さらに削っても問題ありません。

シャーシやバンパーの形によっては上の画像の状態では干渉してくることがあるので
さらに加工する必要が出てくるかもしれませんが、あとは実際に設置してみて干渉する箇所があれば追加で加工していきましょう。
支柱固定パーツの設置
支柱固定パーツが完成したらシャーシに設置するわけですが、事前にシャーシにリヤアンカーを取り付け、支柱のロックナットは取り外した状態にしておきます。
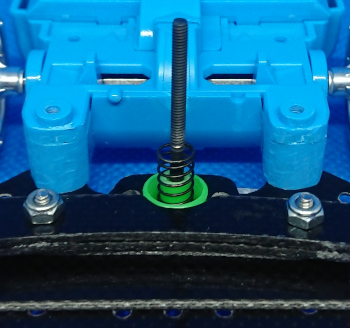
このままだと支柱が土台プレートから落ちてしまうので土台プレート裏にマルチテープ等を貼って支柱の落下を防いでいきます。
次に先程作成した支柱固定パーツを上から仮で取り付けます
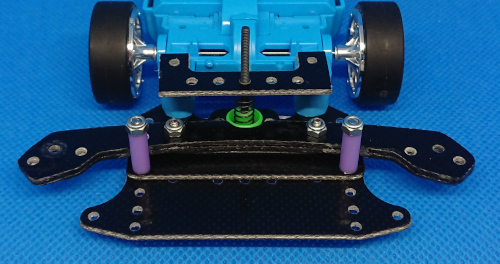
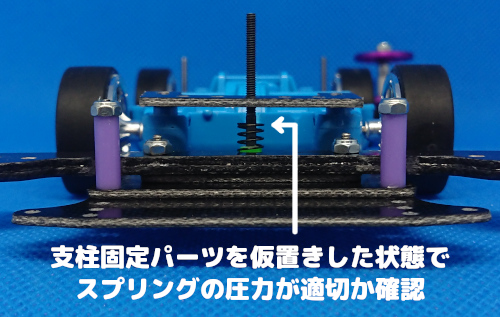
ここでスプリングの圧力が適切かを確認していきます。
上の画像のように支柱固定パーツとスプリングの間に隙間ができてしまうと、スプリングへの圧力がゼロになってしまいます。
こうした場合は、一旦支柱固定パーツを取り外して支柱に 軸受けパーツを追加して適切なスプリングの幅になるようパーツの厚みを調整していきます。
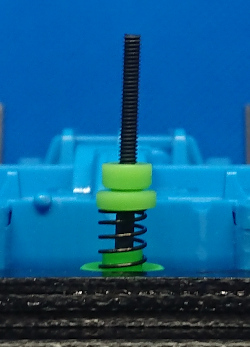
スプリング圧力の調整が終わったら支柱固定パーツの以下の3箇所をビスとロックナットで固定します。
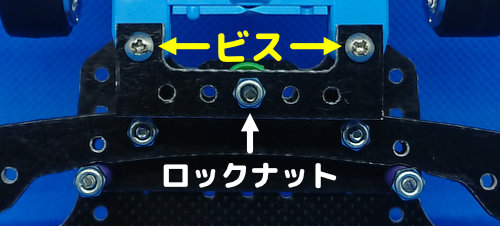
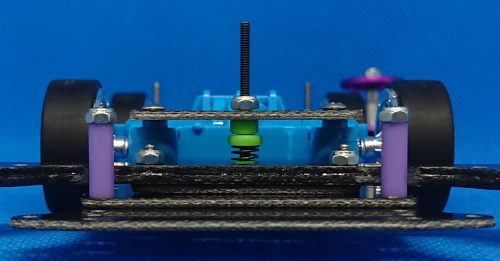
また、25mmのキャップスクリューかビスを使用するのであれば、支柱固定パーツを使用しない時と同じようにロックナットでスプリングの圧力を簡単に微調整することができます。
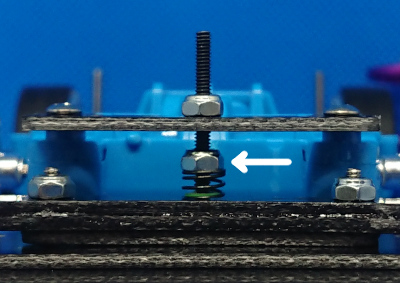
逆にスプリングの圧力が強すぎる場合はシャーシと支柱固定パーツの間にスペーサーやワッシャーなどを入れて、支柱固定パーツの高さを上げていきます。
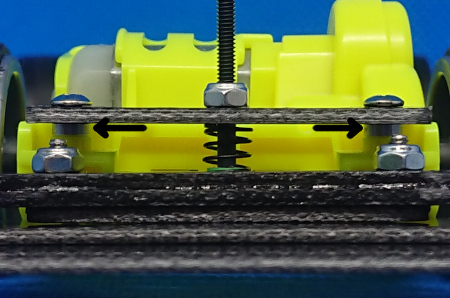
適切なスプリング圧力が調整できたら、ビスの突出している部分をリューターでカットする もしくはスタビキャップ・ゴムキャップなどを付けて対処していきましょう。
また、支柱固定パーツが低い位置に設置されていると、バンパーが可動した時に干渉し バンパーの可動域を狭めてしまうこともあり、下画像の丸を付けた箇所は特に干渉しやすい所でもあります。
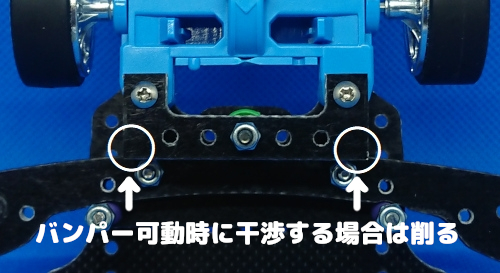
支柱固定パーツはそれほど負担がかかるわけではないので、最初から必要なビス穴だけ残してカットするのもありかと思います。
大ワッシャーを設置する
こちらはマスダンパープレートのガタつきを抑える方法となります。
マスダンパープレートは基本的にスタビヘッドの圧力でブレを抑制しています。
そして、スタビヘッドの可動をスムーズにさせるためにスタビヘッドとマスダンパープレートの接触部分にグリスを塗ることで リヤアンカーの動きがスムーズになります。
しかし、動きがスムーズになる反面 マスダンパープレートの固定力が落ちガタつく原因となることもあります。
そうしたマスダンパープレートのガタつきを抑える方法として、組み立て時の支柱(キャップスクリュー)にスタビヘッドを付ける前に大ワッシャーを設置します。
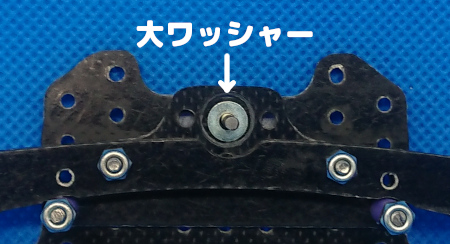
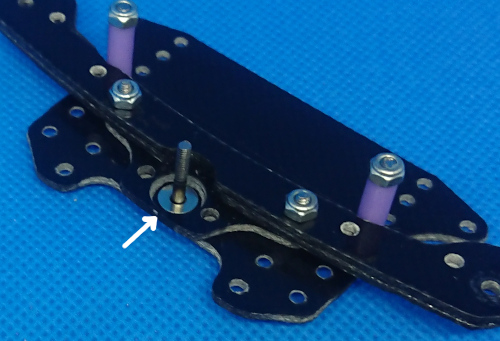
では何故大ワッシャーを設置するだけでガタつきを抑えられるのかを、まずは以下の断面図を見てもらいたいと思います。
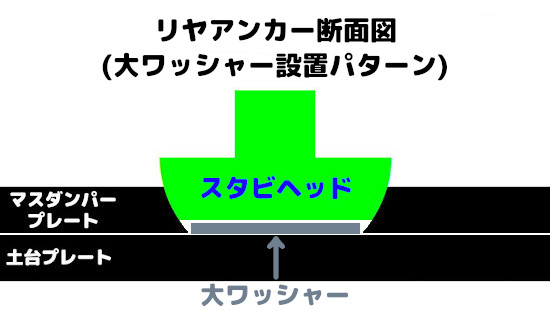
上の断面図には表示していませんが大ワッシャーの中心には支柱が通っているため基本的にブレることはなく、マスダンパープレートが横に移動した際に大ワッシャーがストッパーとなり大きくズレるのを防いでくれます。
大ワッシャーの厚さはわずか約0.4mmで、実際のところマスダンパープレートと大ワッシャーの接触する箇所の面積は小さくなります。
しかし、マスダンパープレート・大ワッシャーが土台プレートに接触している状態であれば その小さな接触面積であっても大ワッシャーがマスダンパープレートをしっかりと抑えてくれます。
そして、この構造によってコーナーリング時にフェンスから伝わる衝撃に対しても大ワッシャーのストッパー効果によりマスダンパープレートの無駄なブレを抑制することができます。
また、断面図だけ見ると左右(両サイド)だけのガタつき防止に見えますが、左右だけでなく前後(フロント・リヤ)のガタつきも抑えることができます。
尚、大ワッシャーを設置する際の注意点として、大ワッシャーの厚さ(約0.4mm)分 スタビヘッドの高さも上がるため、スタビヘッドの底を少し削る必要があることをお忘れなく。
その他パーツを使ったリヤアンカー作成例
ここでは今回紹介してきたパーツとは異なるパーツを使ってリヤアンカーを作成する例を紹介していきます。
FRPマルチワイドステーを使った作成例
土台プレートとしてブレーキステーの1枚目の代わりにFRPマルチワイドステー(以下 マルチステー)を使ったパターンであり、マルチステーを以下のように加工して使用します。
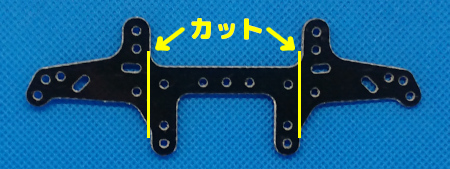
加工は非常にシンプルで両サイドをカットするだけとなり、リューターのダイヤモンドカッターのみでも可能で、加工後は以下のようになります。
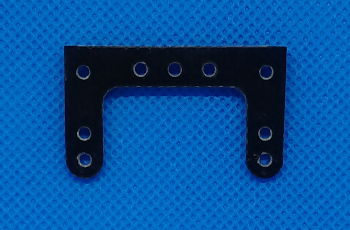
そして、加工後のマルチステーの使用するビス穴は以下となります。
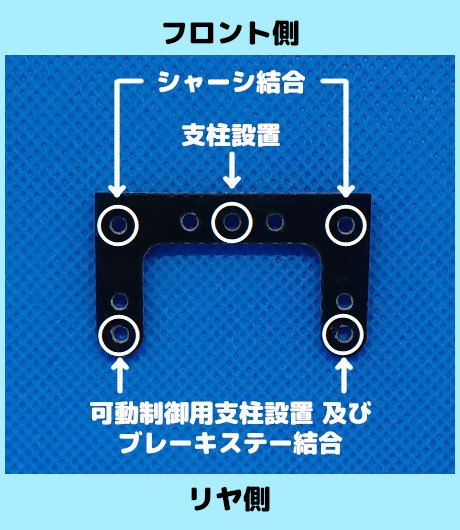
基本的にはブレーキステー1枚目と同じように使用していきますが、可動制御用支柱(ストッパー)設置のビス穴の位置がブレーキステーに比べてややリヤ寄りになります。
このため、フロントステーをバンパーとして使用する場合のストッパーと干渉する箇所は削る必要がなくなり ストッパーもスペーサーよりも太いパーツに変更する必要があります。
ストッパーの代替えパーツとしてハイマウントチューブスタビ(湯呑スタビ)かマルチブレーキセットに付属しているパーツが一般的です。
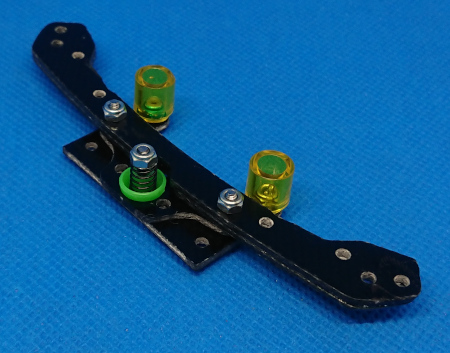
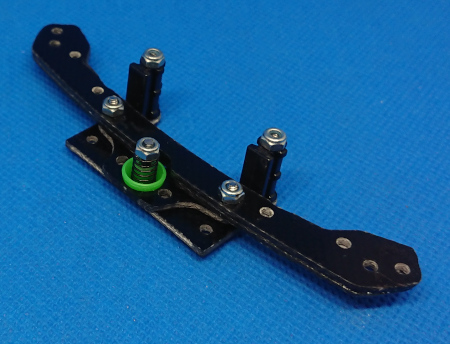
※リヤスキッドローラーセットにもマルチブレーキセットと同様のパーツが付属されています。
ただこれらのパーツだとフロントステーとの間に結構な隙間ができてしまい、これだけだと結構ガタついてしまいます…
フロント側にもストッパーを付けて対応する方法もありますが、リヤ側のストッパーだけで対応するのであれば、これらの隙間を極力無くすためにハイマウントチューブスタビの場合はマルチテープを何重にも巻いて厚さを増しました。
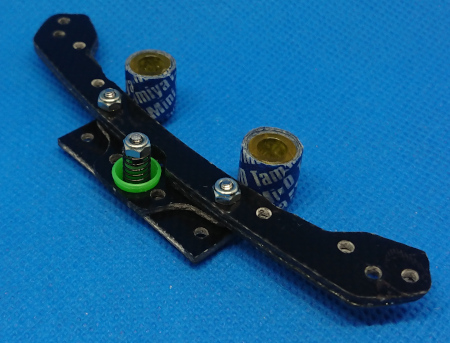
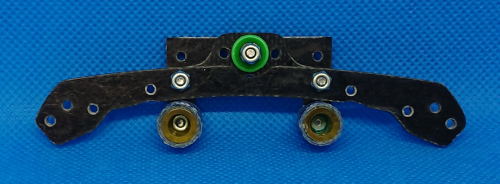
少々不格好な方法ではありますが この方法であれば微調整も簡単にできます。
同様にマルチブレーキセットに付属しているパーツを設置した場合も隙間ができ、こちらはストッパーの箇所が平面となっているのでクリヤーボディの端材やプラ板などを適切な大きさに切り取って接着剤で貼り付ければ隙間を埋めることができます。
また、マルチステーも可動制御用支柱設置のビス穴を使ってブレーキステーを追加することが可能で、ブレーキステーの以下のビス穴と結合することができます。
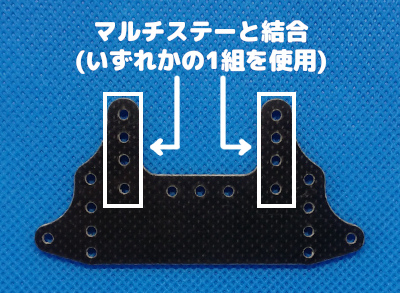
取り付けるビス穴の位置を変更することによりマシン全長の長さを調整することが可能で、ブレーキステーを追加することによりブレーキスポンジやマスダンパーの設置が可能となります。
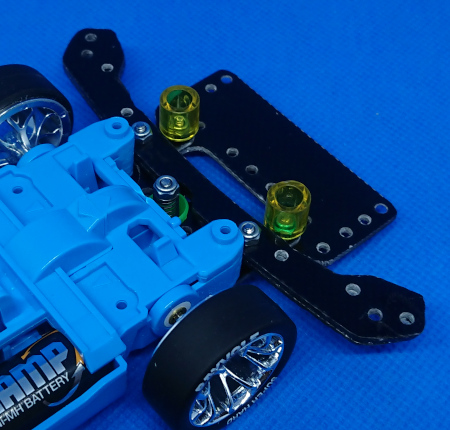
上記の画像はブレーキステーの両サイドを加工してマルチステーと結合させた状態となります。
ちなみにマルチステーを使用する場合は基本的にMSシャーシに取り付けることになると思いますが、下の画像のようにMSシャーシにリヤアンカーを取り付けた場合、シャーシ自体もバンパーのストッパーとなります。
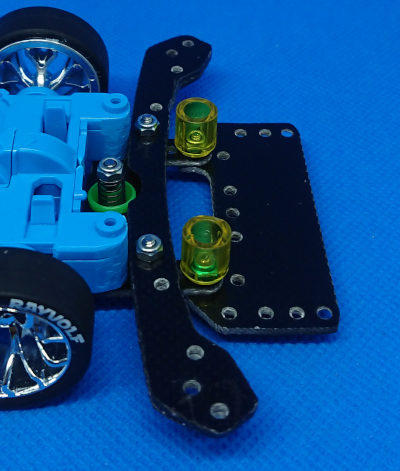
むしろ上の画像の状態だと可動制御用支柱はサブのストッパーとなり、メインのストッパーはシャーシ側になります。
このことから先程隙間が空いてしまうと言っていた可動制御用支柱の箇所も わざわざ隙間を埋めなくてもフロント側のシャーシの方でストッパーの役割を担ってくれてガタつきを抑えることができます。
以上がマルチステーを使用した使ったリヤアンカーの作成例となり、リヤアンカーの土台パーツというとブレーキステーよりもこちらの方がメジャーではないかと思われます。
マルチステーはブレーキステーよりも安く購入でき、土台ステーとしての加工もブレーキステーに比べてシンプルでやり易いのが利点であり、一見するとこちらのステーの方が優秀にも見えます。
しかし、個人的にはマルチステーは中級者・上級者向けとも思っており、初めてリヤアンカーを作成するという方にはあまりおすすめできません。
なぜ中・上級者向けなのかについては、次の「ブレーキステーとの違い」にて詳しく解説していきます。
ブレーキステーとの違い
ここでは土台プレートとしてのマルチステーとブレーキステーの違いを解説していきます。
まず土台プレートとして各シャーシへの設置について、マルチステーはMSシャーシ以外のシャーシでは設置が難しいのに対して、ブレーキステーは基本的にはどのシャーシへも簡単に取り付けることができます。
※MSシャーシ以外のシャーシへの設置が難しいことについては『ブレーキステー1枚目の加工』のところで詳しく解説しているので省略します。
マルチステーは1つのパターンの加工しかできず リヤアンカー全体がシャーシにより近い状態なので MSシャーシ以外のシャーシに設置する場合はシャーシ側の加工も必須となり その分の手間も増えてしまいます。
そして、最も違う点はシャーシ結合用のビス穴と支柱設置用のビス穴の位置関係が違うことです。
ぱっと見、シャーシ結合用のビス穴と支柱設置用のビス穴の位置はいずれのステーも同じ位置関係に見えますが、実は微妙に異なっています。
まずマルチステーと形が似ているブレーキステーの加工パターン2のビス穴の位置関係を見ていきます。
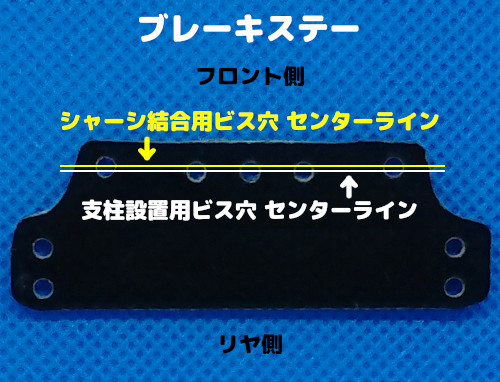
上のブレーキステーの支柱設置用のビス穴はシャーシ結合用ビス穴よりもややリヤ寄りにあります。
続いてはマルチステーのビス穴の位置関係を見ていきます。
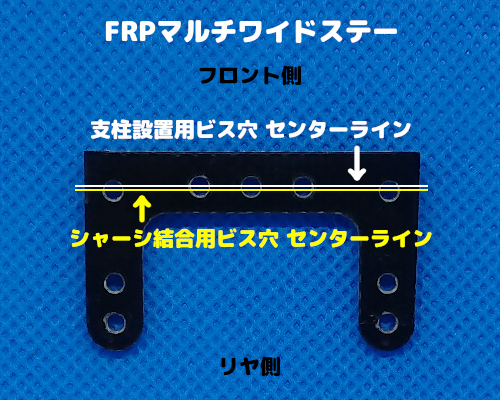
上のマルチステーの支柱設置用のビス穴はシャーシ結合用ビス穴よりもややフロント寄りにあります。
このようにマルチステーの方が支柱設置用のビス穴がフロント寄りにあり、これによってブレーキステーよりもリヤアンカーが僅かにシャーシに近づく形となります。
ほんの僅かな違いではあるんですが、マルチステーの方がリヤアンカー全体がシャーシに近いため マスダンパープレートやバンパーを削ったり・シャーシ側を削る必要が出てきます。
削るのはリヤアンカー・シャーシに限らずMSフレキでお辞儀防止ステーを付けている場合は、お辞儀防止ステーも削る必要が出てきて加工の手間が増えてしまいます。
こうしたことからマルチステーを土台プレートとして使う場合は 少々手間がかかる可能性があることをあらかじめ考慮しておくと良いかもしれません。
ただ、デメリットだらけでもなく、マルチステー自体の加工は簡単でしかも軽量なパーツであるメリットもあるので、ご自分の改造スキルやマシン状況に応じてマルチステーとブレーキステーを使い分けるのがベストかと思われます。
最後に
今回はリヤアンカーの最も基本的な形の作成方法を紹介してきました。
リヤアンカーのバリエーションは様々あり、日々ギミックも進化していますが、根幹となる部分については基本的には今も昔も違いはありません。
まずは本記事の作り方を参考にしアンカーの基礎を把握して頂き、それを元に自分オリジナルのアンカーギミックを作ってもらえればと思います。
また、「まだ自分にはリヤアンカーを作るのは難しい…」と思った方は、より簡単に作れる以下の1軸リヤATバンパーの作成をおすすめします。
上記の1軸リヤATバンパーは加工工程も少ないながらも、いなし効果もリヤアンカーに匹敵するものとなっていますので初心者の方は まずはこちらを作成してみてはいかがでしょうか。
尚、本記事はまだ未完成な部分があり「その他パーツを使ったリヤアンカー作成例」については一部紹介できていない状態で、いつその情報を更新するか未定ですが 後程本記事で追記する予定です。
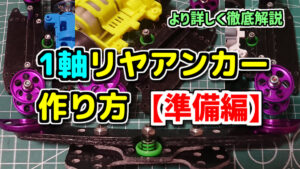
コメント