今回はミニ四駆のMSフレキ(フレキシブル加工)の作成方法を解説していきます。
本記事で紹介するMSフレキは入手しやすいパーツのみで且つ、MSフレキ専用の治具(じぐ)は使用せず基本的な工具のみで作成することができます。
また、MSフレキ作成において初心者がつまづくであろう点も詳しく解説していくので、これからMSフレキを作りたいと思っている方におすすめの内容となっています。
尚、本記事はMSフレキの具体的な作成方法の解説がメインとなります。
※『作成に必要なパーツ・工具は以下の準備編』『MSフレキ精度を上げるための加工方法は以下のMSフレキの加工精度を上げる方法』にて別途解説しています。
それと、本記事とは別に樽バネを使用したMSフレキの作成方法も別途紹介しているので、樽バネが用意できる方は以下の記事も参考にしてください。
本記事は全体ボリュームが多くなっているため、よりスムーズに作業するためにも目次をご活用ください。
加工前に知っておくべきこと
ここでは、改造・加工をする上でMSフレキ作成(フレキシブル加工)について知っておくべきことを説明していきます。
これらを知っていると知っていないとでは作業効率も変わってくるので、初めてMSフレキを作る方は必ず目を通すようにしてください。
MSフレキの構造
いざMSフレキを作ろうと思ってもMSフレキの構造を知らないと 作業中に「今何のための加工をしているか分からない…」ということになったりもします。
そうならないために必要なのが「MSフレキの構造」を知ることで、まずはMSフレキの基本的な構造を紹介していきます。
以下の画像はマシンを横から見た概要図となりますが、MSフレキはスプリングを軸として以下のように動作します。
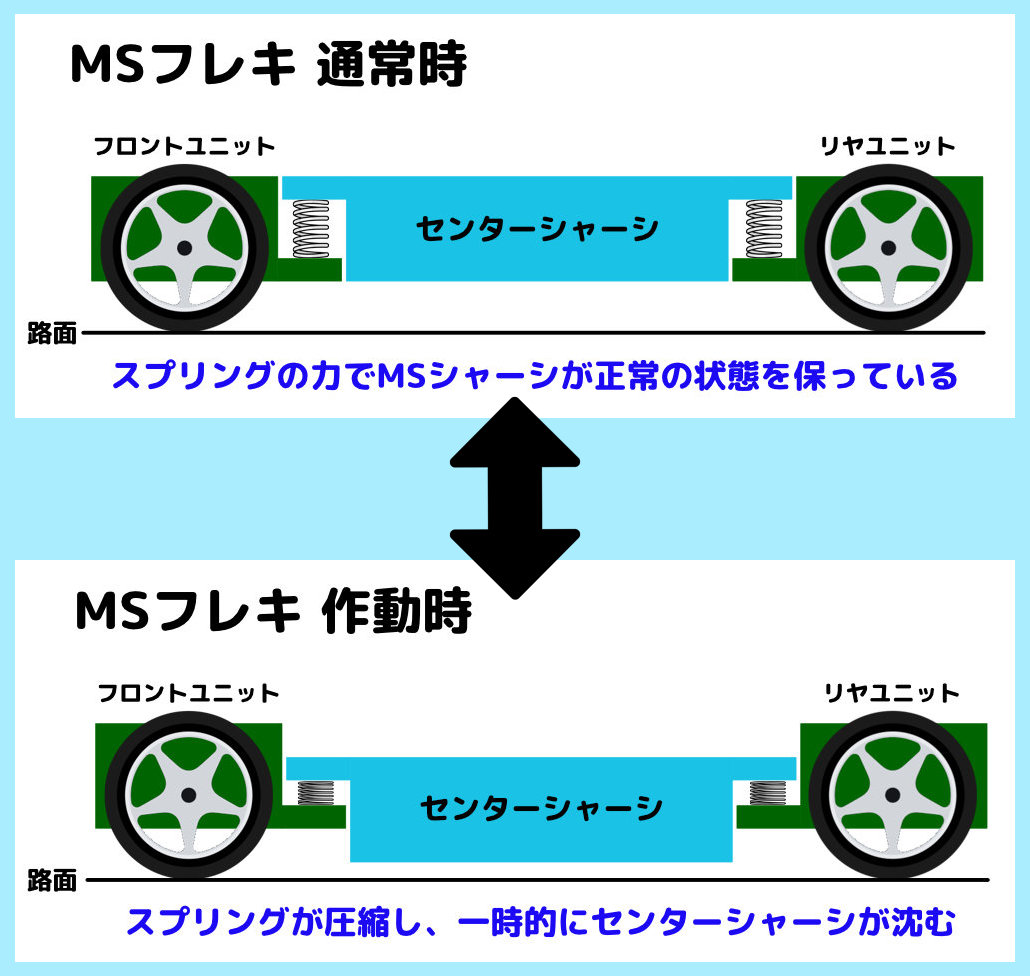
実際のMSフレキはもっと細かい構造となっていますが、基本的なMSフレキの作り・動作は上画像の形となります。
このスプリングを軸とした動きがMSフレキの特徴であり、この動きを実現させるための加工ということを覚えておいてください。
各加工作業の目的
MSフレキの構造が分かったところで次に知っておくべきことは「各加工作業の目的」となります。
「何の目的でこの箇所を加工しているのか」を各工程ごとに理解していれば加工作業がスムーズになり作業時間の短縮にも繋がります。
そして、作業効率を上げるためにも各加工作業の目的を知るべきであり、MSフレキ作成は基本的に以下のいずれかの目的で加工作業を行っていきます。
この加工をしないとフレキ可動できないので必須作業となります。
一部の加工を除き大雑把な作業で問題ないので基本的には加工難易度が低い作業となります。
この加工もある意味 実行しないとフレキ可動ができないので必須作業です。
出来次第ではスムーズになりすぎてシャーシ全体にガタが出てしまい駆動が不安定になったりしてしまうので、ある程度の加工精度が必要になり加工難易度が比較的に高い作業となります。
この加工でフレキの可動域が決まります。
今回は追加するパーツ1つで可動域が決まり、それ以外の箇所は可動域を作るための加工となるため、基本的には大雑把な加工でも問題ない作業となります。
以上が加工作業の目的となり、基本的には上記のいずれかの目的で加工作業を行っていきます。
(加工箇所によっては複数の目的を持つ作業もあり、一部の作業は上記目的に該当しないものもあります)
各加工作業がどの目的に該当するかについては 各加工作業ごとに随時補足説明していきます。
それでは次からMSフレキ作成の具体的な加工方法を解説していきます。
センターシャーシの加工
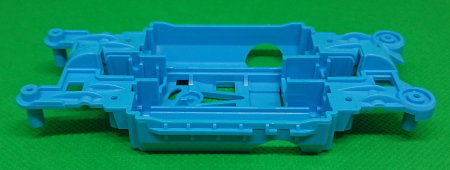
まずはセンターシャーシの加工方法を解説していきます。
シャーシの切断
まずはフレキ可動をさせるためにセンターシャーシのフロント側・リヤ側の両端を切断し、センターシャーシを3分割していきます。
最初の加工作業ではありますが、出来しだいでMSフレキの精度が変わってくる重要なところでもあるので細かく解説していきます。
センターシャーシはフロント・リヤ側の切断面が平行になるよう、真っすぐ切断します。
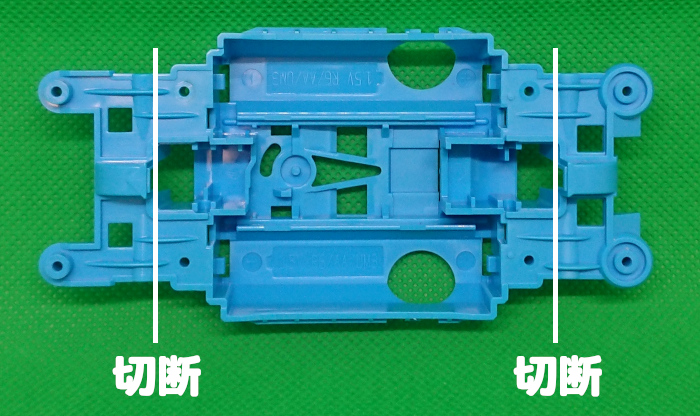
ポイントは地面に対して垂直に切断することです。
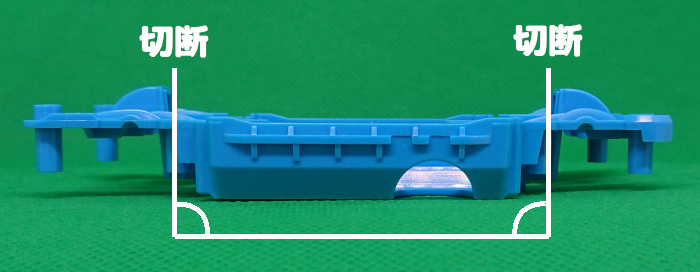
上記の箇所を切断をする際はクラフトのこを使用します。
切断のコツとしてはセンターシャーシのギヤカバーをガイドとして のこ刃の側面をギヤカバーに当てながら切断していきます。
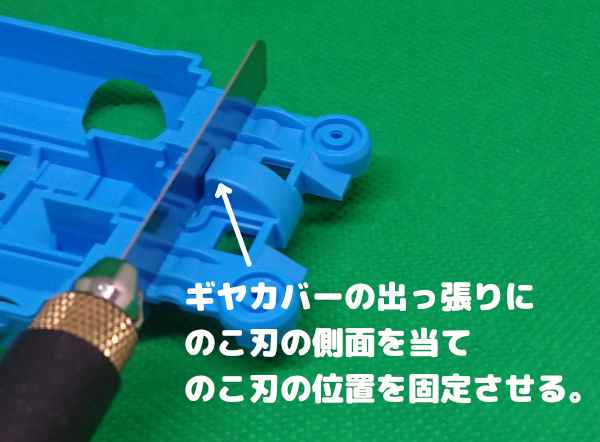
ただしギヤカバーが若干斜めに傾いているのでのこ刃を全体をギヤカバーに当てたまま切断すると少し斜めのカットになってしまいます。
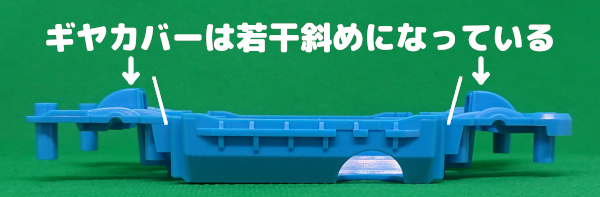
斜めカットにならないようにするためには、一度のこ刃全体をギヤカバーにあてのこ刃を置く位置を決め、のこ刃の天井に近い部分をギヤカバーから少し離してのこ刃が垂直であることを確認して切断していきます。
のこによっては刃のギザギザが大きい物もあり、ギザギザが大きいのこだと力を入れて切断しようとすると刃先が動かしづらく、特に通常のMSシャーシだと凹凸があるために非常に刃が通しにくくなります。
クラフトのこでの切断のコツは、刃をシャーシに当て ほとんど力を入れず軽くのこを持って、削るというよりもなぞる感じでゆっくりとのこを上下に動かします。
このなぞる動作だけで徐々にシャーシも削れてきて、ある程度削れてきたら少し力を入れてもいいんですが、終始 力を入れずひたすらのこ刃を上下にスライドするだけでもカットできます。
センターシャーシの切断作業はギヤカバーをガイドにして削りますが、それだけだと刃がずれてしまうことがあります。
そこで、より真っ直ぐ切断しやすくなるよう、切断する箇所を確認できる目印(切断ガイド)を作る方法を2パターン紹介していきます。
シャーシに切断ガイドを作る方法①
その①はシャーシに線を引く方法となります。
まず、定規を用意して、ギヤカバーに定規を当て 定規が真っすぐになっていることを確認して、油性ペンで線を引きます。
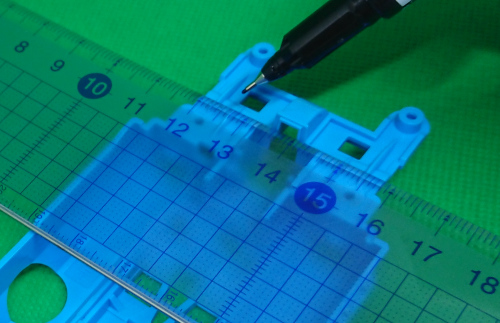
線を引いたらそれをガイドにして切断していくんですが、通常のMSシャーシは凹凸があるので線を引くのが大変な上 線を引いても結構見づらかったりします…
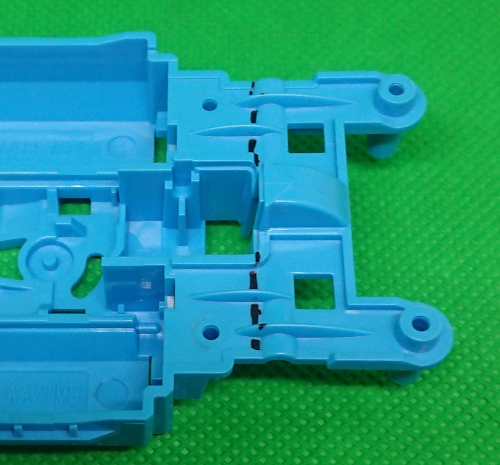
そこで通常のMSシャーシみたいに凹凸がある場合は、下の画像のように切断面の端と端だけマーキングしてそれを指標に切断した方がやり易いかと思います。
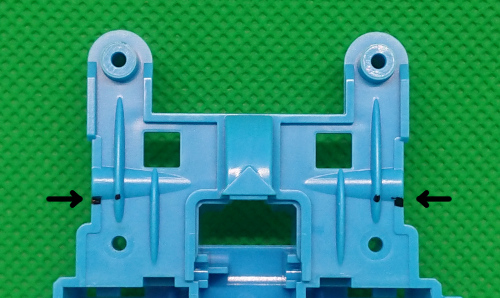
ただし、ペンを使っての方法だと黒シャーシの場合に黒色ペンだと線が見えなくなるので、白色などの線が分かりやすいペンを用意する必要があります。
そうした、適切なペンがない場合は次に紹介する方法を試してみてください。
シャーシに切断ガイドを作る方法②
その②はシャーシにテープを貼る方法となります。
テープを切断ガイドにする場合は、目視でそのままテープをセンターシャーシに貼って構いません。
ただ、それだとうまく貼ったつもりがテープが真っすぐではなかったということもあるので、目視でうまくテープを貼れない方は以下の方法を試してみてください。
まず、マルチテープやマスキングテープなどの色付きのテープ(カットする長さは6cm以上推奨)と定規を用意して、以下の手順で定規の裏面にテープを貼り付けます。
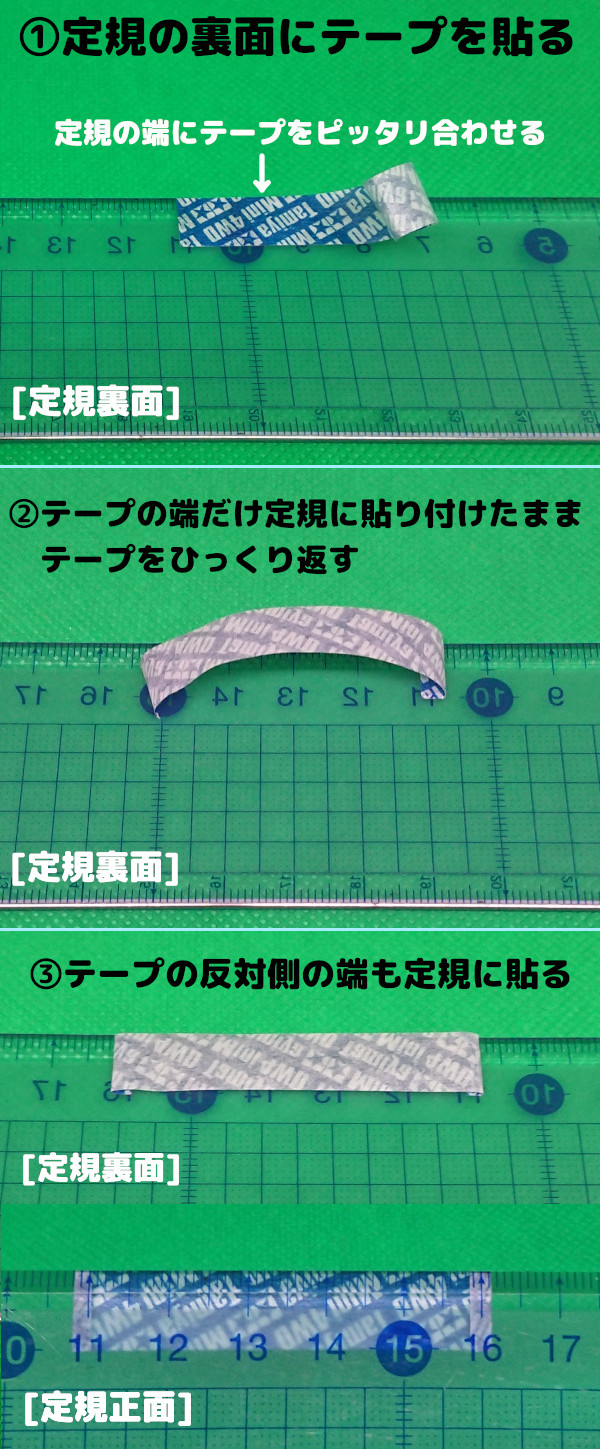
定規にテープを貼り終えたら、定規をセンターシャーシのギヤカバーに合わせて、定規が真っすぐになるよう調整し、定規が真っすぐの状態で 定規をシャーシにくっつけ定規をしっかり押してテープをシャーシに付けていきます。
そのまま定規を上に上げるとテープが剥がれる可能性があるので、下の画像のように定規を片方向にスライドさせて片方のテープを定規から剥がして、更に反対側に定規をスライドしてもう片方も定規から剥がします。
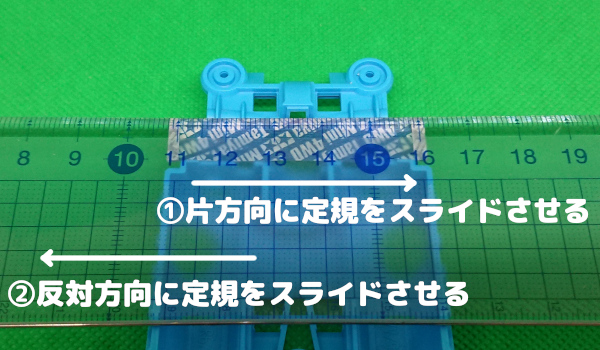
貼り終えた後は必ずテープが真っすぐになっていることを確認して、もし真っすぐでなければ、もう一度定規にテープを貼って再度挑戦しましょう。
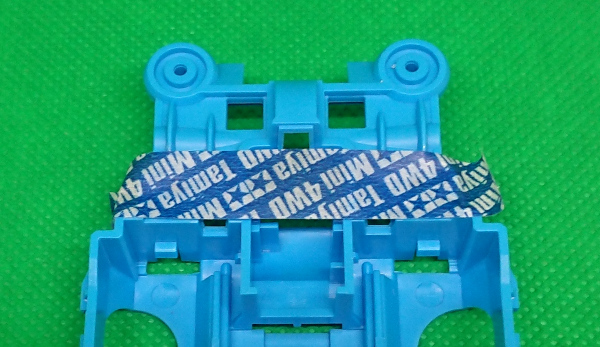
あとはテープを目安にしてのこ刃を当てていくんですが、ギヤカバーをガイドにのこ刃を当てると丁度テープ側面の外側に刃がくるので、テープを切断せずにシャーシだけ切断する形になります。
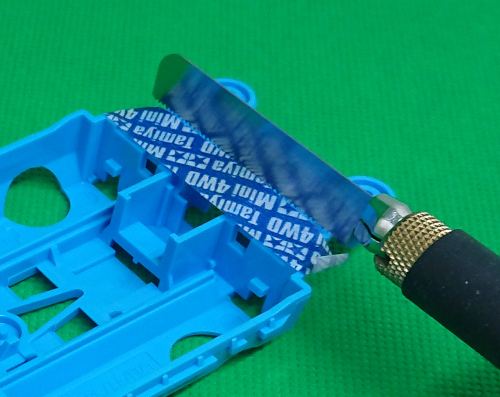
センターシャーシの切断後
センターシャーシを切断すると削りカスが大量に出るので、工作シートの上にさらにキッチンペーパーなどの使い捨ての用紙を引いておくと後片付けが楽になります。
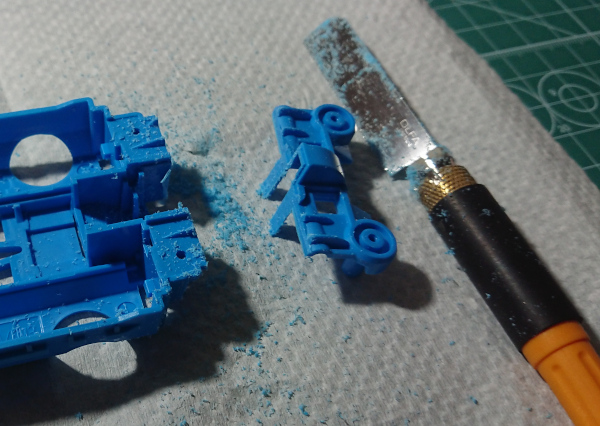
センターシャーシ切断が完了すると3つのパーツに分かれ、分断したセンターシャーシのフロント側・リヤ側はこれ以降ユニットカバーという名称で解説していきます。
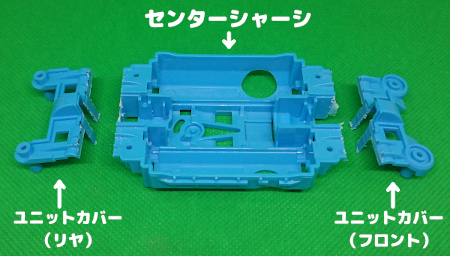
切断後のセンターシャーシの加工
この項目ではシャーシ切断後のセンターシャーシの加工方法を解説していきます。
ギヤケース周りの加工
まずはフレキ可動の妨げになるセンターシャーシ切断面の箇所をカットしていきます。
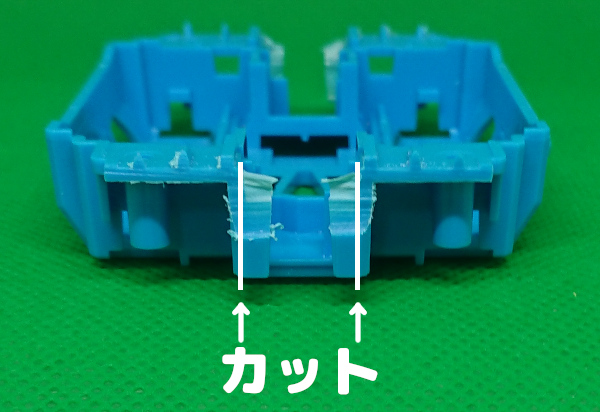
※フロント・リヤ側の両方をカットしていきます。
ここの加工は大雑把で構わないのでニッパーでカットしていきます。
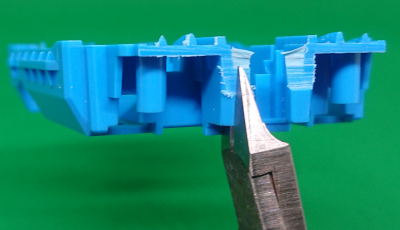
切断面は粗くなっても問題ありませんので、一旦不要な部分を切り落とし次の工程に進んでいきます。
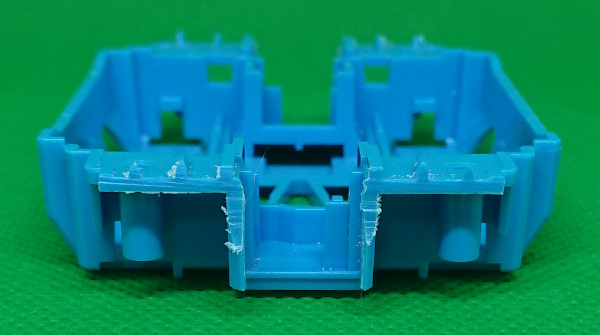
次に以下の画像の状態になるように加工していきます。
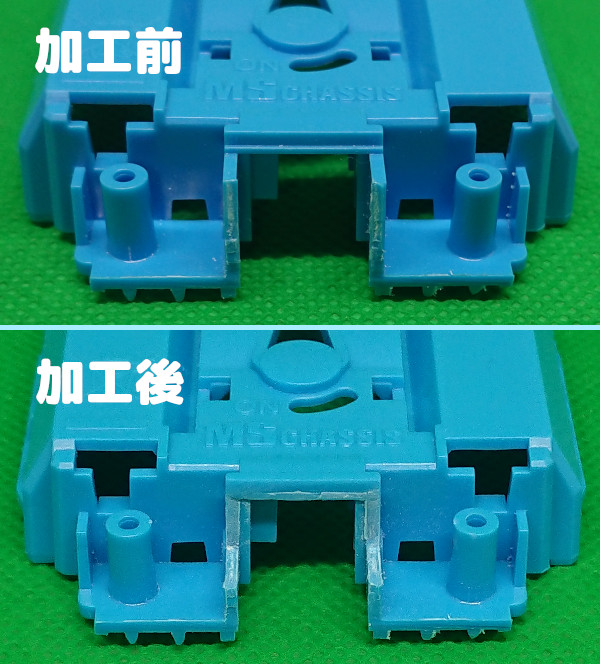
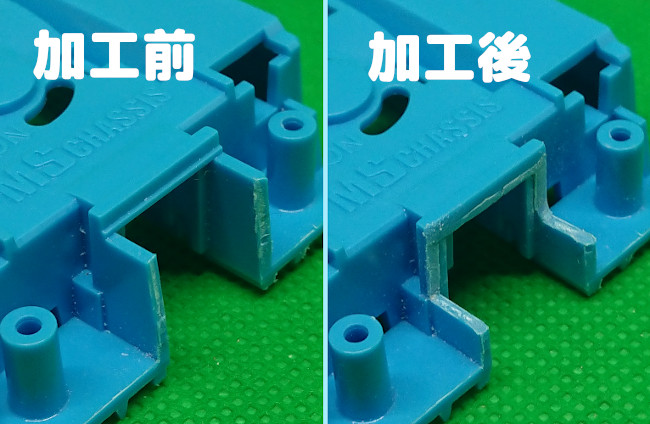
次から上の画像の状態にするまでの加工方法を解説していきます。
尚、加工作業は片側のみの解説となりますが、フロント・リヤ側の両方を同じように加工していきます。
フレキ可動域を極力狭くしたいという場合は、「ギヤケースでの可動域の調整」の加工方法を実施した方が作業効率が良くなると思うのでそちらをご参照ください。
まずはギヤケース加工の第一段階として、ギヤケースの以下の箇所をカットしていきます。
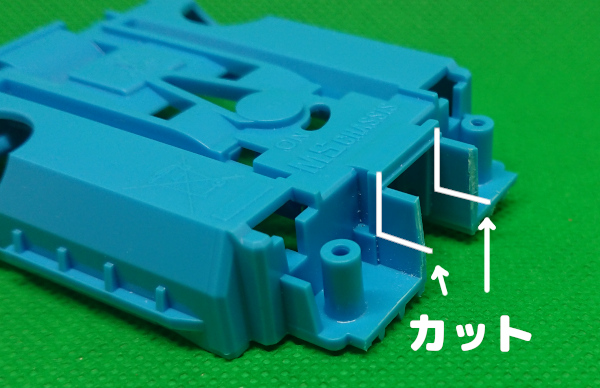
カットする際は以下のラインを目安にすると綺麗に仕上げることができます。
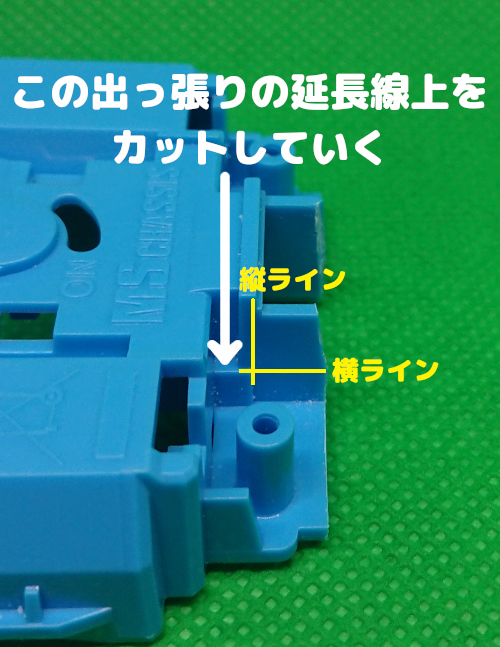
ここでのカットはフレキ可動をさせるために実施するため、上の画像のようにきっちりとカットする必要はなく大雑把な加工で問題ありませんが、縦ラインについては綺麗にカットした方が後の作業が少し楽になります。
そして、次から各箇所を見やすくするためにシャーシをひっくり返して解説していきます。
切断のコツとして、ギヤケースの内側の出っ張りをニッパー切断時のガイドとして使用します。
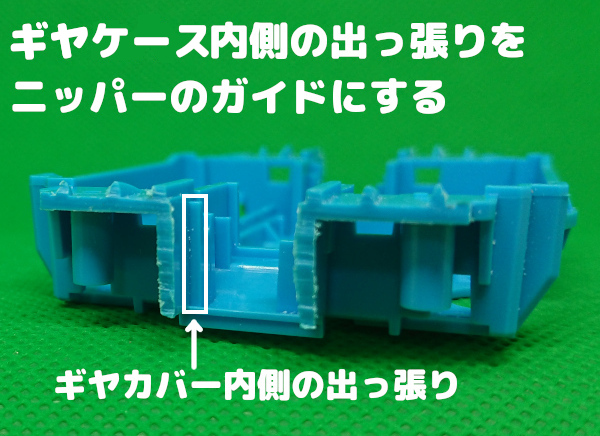
ニッパーの刃先の部分をギヤケース内側の出っ張りに乗せたまま、反対側のニッパーの刃先を見て切断する高さを調整します。
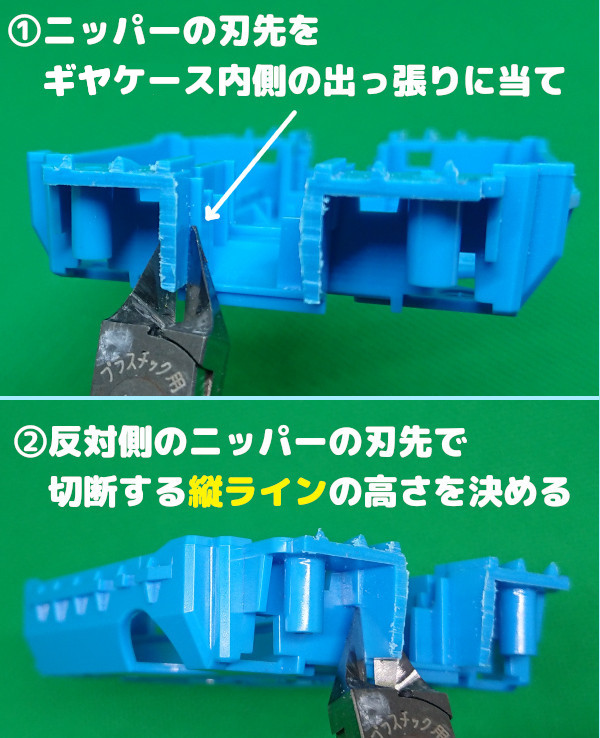
ニッパーの位置が決まったらそのままカットします。
縦ラインをカットしたら、ギヤケース外側の出っ張りを目安にして横ラインもニッパーでカットしていきます。
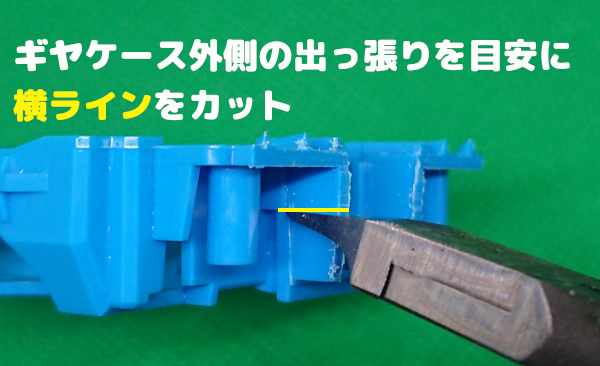
これでギヤケース加工の第一段階が完了です。
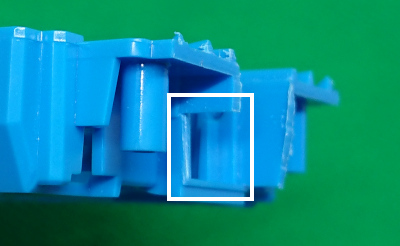
この箇所以外のフロント・リア側の残り3箇所も同じようにカットしていきます。
次にギヤケース加工の第二段階として、元々ある既存の出っ張りと今カットした箇所にできた出っ張りを削っていきます。
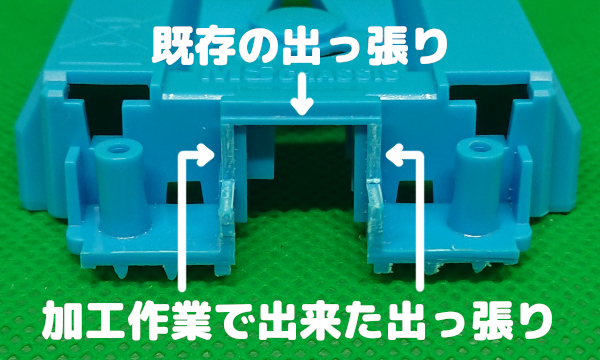
ニッパーでカットした箇所にできた出っ張りもそうですが、既存の出っ張りを削らないとフレキ可動ができず、削り方が甘いとフレキ可動がスムーズにいかないのでしっかりと削っていきましょう。
加工手段は様々ありますが一例として、最初はニッパーでカットできるところまで切り落とし、細かく残ったバリは棒ヤスリで削っていきます。
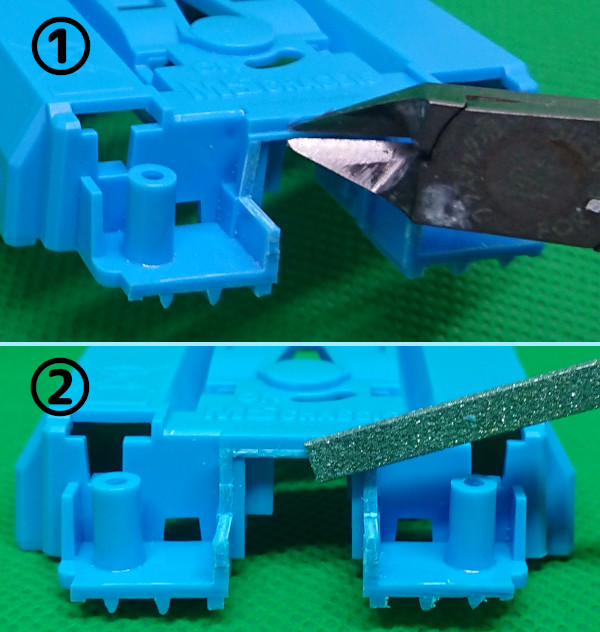
ニッパーで出っ張りがカットしづらければ代わりにデザインナイフで削るか、もしくは最初から棒ヤスリで削っても構いません。
出っ張りを取り除いたらギヤケースの加工は完了となります。
きちんと削れているかどうかはフロント(リヤ)ユニットの加工完了後にシャーシを仮組みして、この箇所が干渉していなければOKです。
既存の箇所は削らないようにする
ギヤケースの出っ張りを削る際の注意点として、以下の箇所をむやみに削ってしまうとMSフレキの精度に影響しガタつきの原因になってしまうので、くれぐれも削らないよう注意してください。
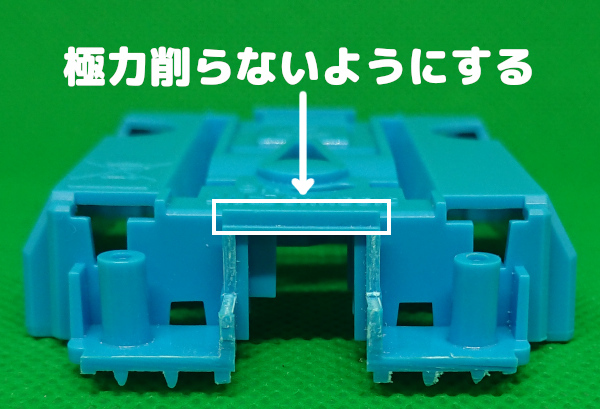
そうは言っても、加工作業の中で上記の箇所だけ削らないようにするのは結構困難ではあります。
しかし、以下の画像のようにヤスリをかける向きを工夫することによって削ってはいけない所を極力避けることも可能です。
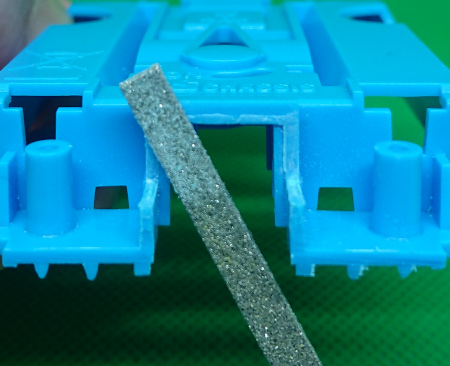
このように、ご自分のやり易い方法で極力 既存の箇所を削らないようにしましょう。
ただ、多少削れてしまう分には問題ないので、誤って削ってしまったからといってシャーシが簡単にガタつくというわけではありません。
そして、元々出っ張っていた箇所については、既存の箇所以上に削って多少くぼむぐらいでもガタつきにはほぼ影響しないので、既存の箇所さえしっかり残しておけば出っ張りのところは思いっきり削っても大丈夫です。
一方 出っ張りの箇所については既存の箇所以上に削って多少くぼむぐらいでもガタつきにはほぼ影響しないので、既存の箇所をしっかり残しておけば出っ張りのところは思いっきり削っても大丈夫です。
四隅の加工
可動をスムーズにするために下の画像の黒い箇所を削っていきます。
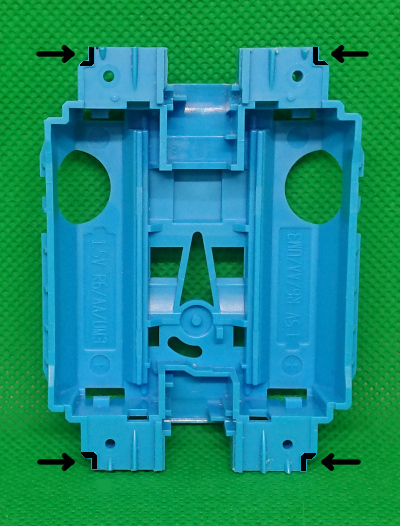
削る箇所が分からいづらい場合は、先にフロント(リヤ)ユニットを加工してからセンターシャーシと重ねてみて どの部分が干渉しているか確認すると良いかもしれません。
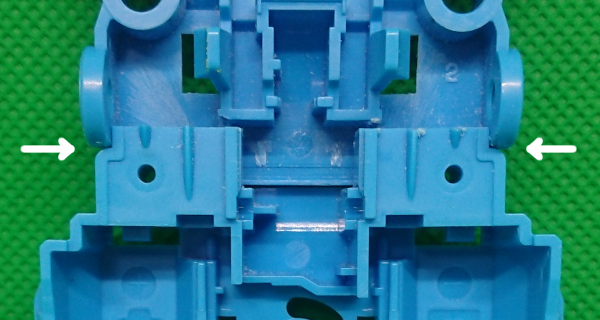
この箇所はわずか0.5mm程カットすれば十分なので棒ヤスリで削るか、もしくは思い切ってニッパーでバッサリカットしても構いません。
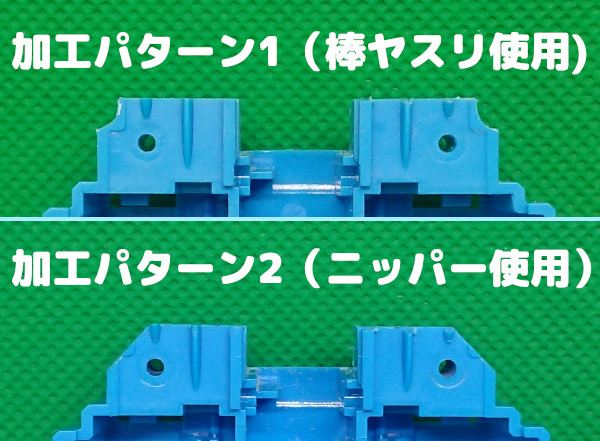
※ここでの加工具合でガタつきに影響するということはないので大雑把な加工でも問題ありません。
ちなみにこの箇所はフロント(リヤ)ユニットの加工具合によっては、加工なしでもフレキ可動がスムーズにいくことがあります。
このことから、一旦ここの加工は保留にしてフロント(リヤ)ユニットを加工してからパーツを結合し、加工が必要と分かってからでも構いません。
ビス用の穴の拡張
センターシャーシにビスを通すため、既存の穴を2mmドリル刃で拡張していきます。
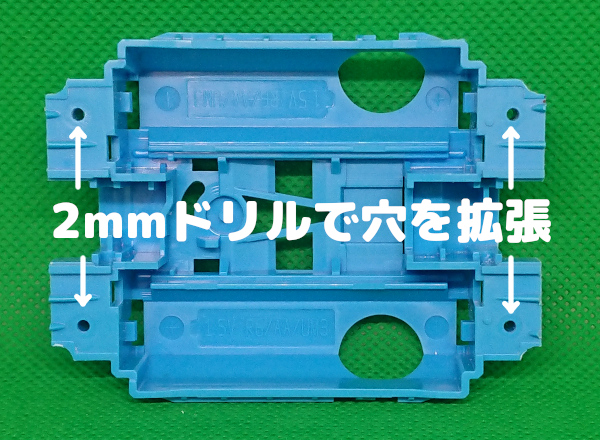
この箇所はセンターシャーシとフロント・リヤユニットを結合する際に互いのパーツが外れてしまわないための留め具が必要となります。
そして、その留め具を固定するためにはビスが必要となり、そのビスを通しやすくするために穴を拡張していきます。
2mmドリル刃で穴を拡張しておけばビスを通すことが可能になりますが、実のところ2mmドリル刃ではビスがスムーズに通らないことがあります。
特にこの箇所はメンテナンス時に頻繁にビスの着脱が必要になり、ビスの通りがスムーズでないとメンテナンス性が非常に悪くなってしまいます。
このことから、可能であれば2.1mmドリル刃での拡張を推奨します。
(この穴を拡張しすぎたからといってフレキ精度に影響することはありません)
ただ、2.1mmドリル刃で拡張するとなれば、当然2.1mmドリル刃を別途購入する必要があるわけで 使用用途も限られてきます。
「それだけにために購入するのは勿体ない」ということであれば、2mmドリル刃を繰り返し通して穴を拡張することも可能なので、まずは2mmドリル刃で試してみてください。
それでもビスがスムーズにいかなくてメンテナンス時にビスの取り外しが面倒くさいということであれば2.1mmドリル刃の購入を検討してみましょう。
尚、2.1mmドリル刃でおすすめなのは以下のもので、精度も良く安価で購入することが可能です。
ちなみに、2.1mmドリル刃はクリヤーボディをマシンに固定する際にも活躍します。
以上でセンターシャーシの加工は終了となりますが、一部追加で加工した方が良い箇所もあります。
それらについては別記事の「可動をスムーズにする」項目で詳細を解説していますので、可動がスムーズにいかない場合は以下の記事をご参照ください。
ユニットカバーの加工
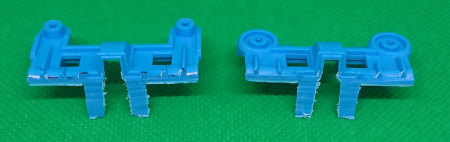
ユニットカバーはフロント・リヤ側の2つのパーツとなりますが、どちらも加工内容は同じなのでフロント側をピックアップして解説していきます。
不要箇所のカット
センターシャーシ切断の際に残った不要箇所はフレキ可動の邪魔になるのでニッパーでカットします。
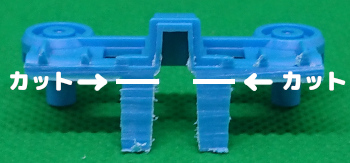
ここはカットするだけでOKです。
ギヤカバーの出っ張りをカット
フレキ可動時に下画像の出っ張りが干渉するので、可動をスムーズにするために出っ張りをカットします。
ついでにシャーシ切断時にできたバリ(不要な出っ張り)もカットしていきます。
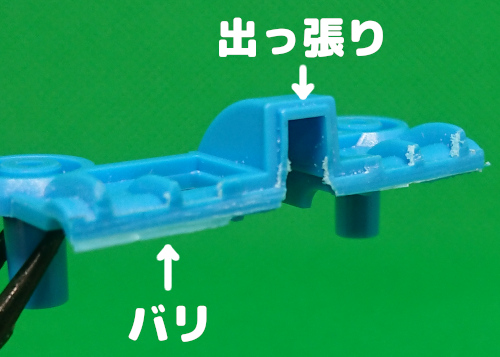
出っ張りとバリは同義語なので意味が一緒なんですが、本記事では元々ある出っ張りは出っ張りと呼び、加工途中で出来た出っ張りをバリと呼んでいきます。
加工方法については最初にニッパーかデザインナイフで切れるところまで削って、板ヤスリか棒ヤスリで綺麗に整えていきます。
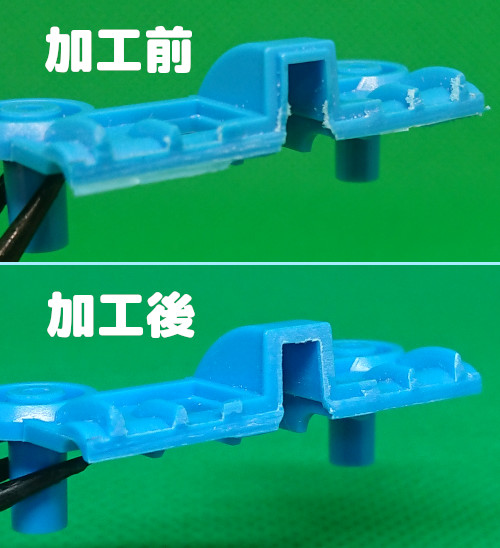
ギヤカバーとの干渉箇所の加工
先程加工した部分とは別に 以下の箇所もフレキ可動時に干渉するので、可動をスムーズにするために削っていきます。
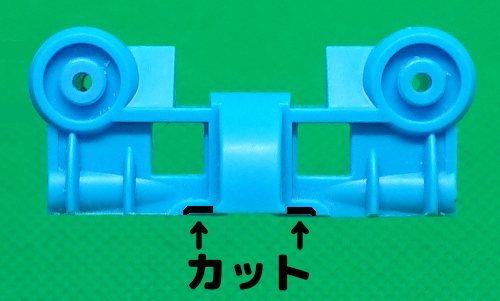
どのくらい削るかは最初のシャーシの切断の切れ具合によっても変わってくるので、仮組みの際に干渉度合いを確認してから削っても構いません。
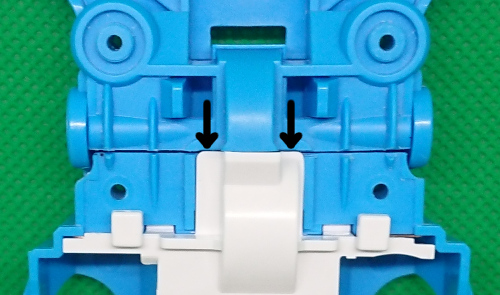
ちなみに上記のユニットカバーの形であれば該当箇所を1mm程削るだけでOKですので、棒ヤスリが適しているかと。
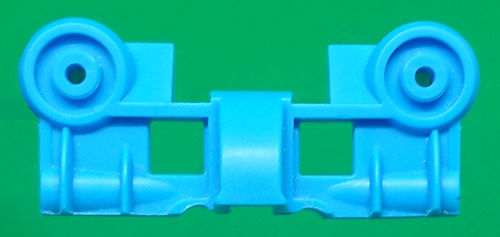
ギヤカバーと干渉するということで、ユニットカバーを加工しなくてもギヤカバー側を加工してフレキ可動をスムーズにすることができるのお好きな方の加工で問題ありません。
ただユニットカバー側を加工しておけば、基本的にギヤカバー側は加工する必要がなく、万が一ギヤカバーが壊れて交換する時も別の未加工のギヤカバーがすぐに使えるので、個人的にはユニットカバー側を加工することを推奨します。
フロントユニット(N-02)の加工
続いてはフロントユニット(N-02と文字が入ったパーツ)の加工手順を解説していきます。
まずはフロントユニットの各部名称を記載しておきます。
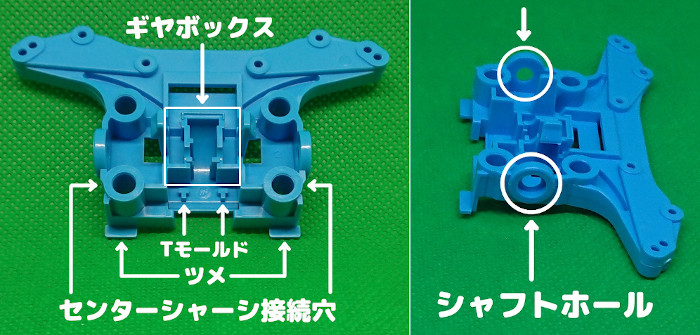
今後はこの名称を使って解説していくので、どの場所を示しているか分からなくなったら上の画像を確認してください。
フロントユニットの加工についてはこれから解説する順番の通りでなくても良いので、ご自分のやり易い所から加工してもらって構いません。
不要箇所のカット
フレキ可動及びフレキ可動をスムーズにするため、不要な箇所をカットしてきます。
ツメ・Tモールドのカット
フレキ可動させるためにツメとTモールドをニッパーでカットしていきます。
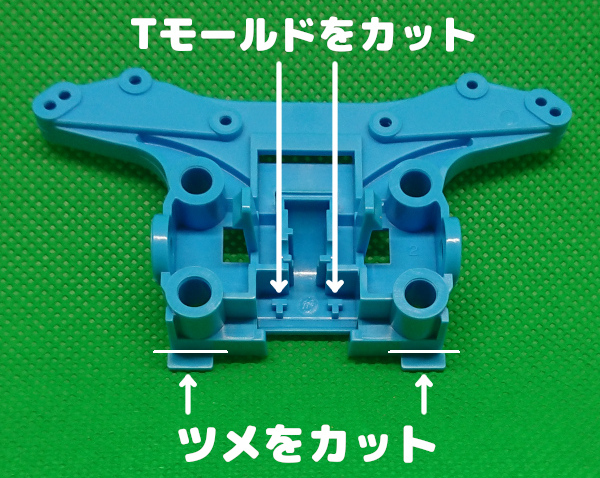
※Tモールドはフレキ可動した際にセンターシャーシ側のギヤが干渉してしまうのでカットします。
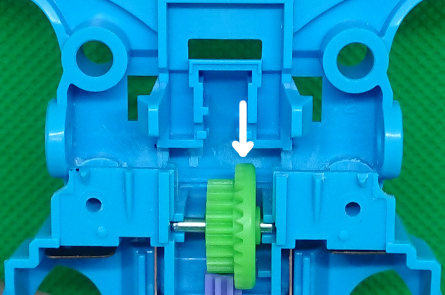
センターシャーシ接続穴の側面のカット
次に可動をスムーズにするためにセンターシャーシ接続穴の側面をニッパーでカットしていきます。
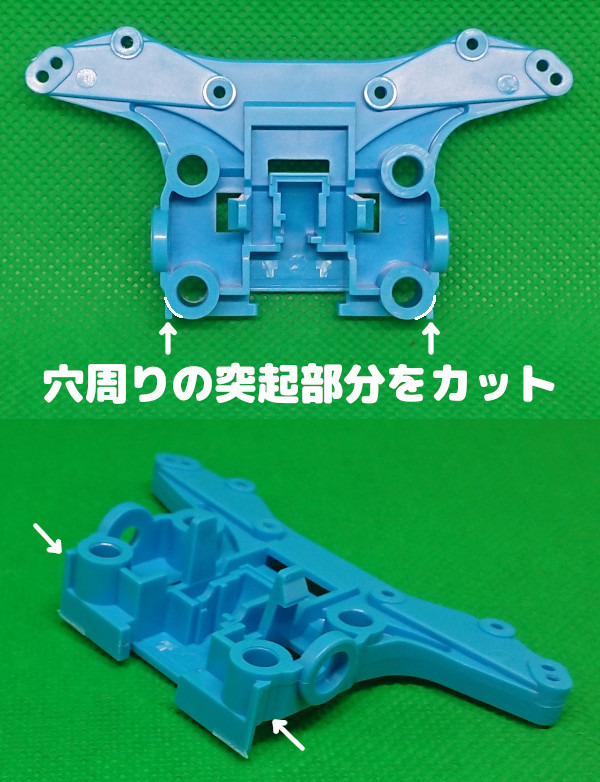
ここのカットはセンターシャーシ接続穴の側面から下の所まで一気に切り落としてしまって問題ありません。
どこまでカットして良いか分からな方は以下の加工前・加工後画像を参考にしてください。
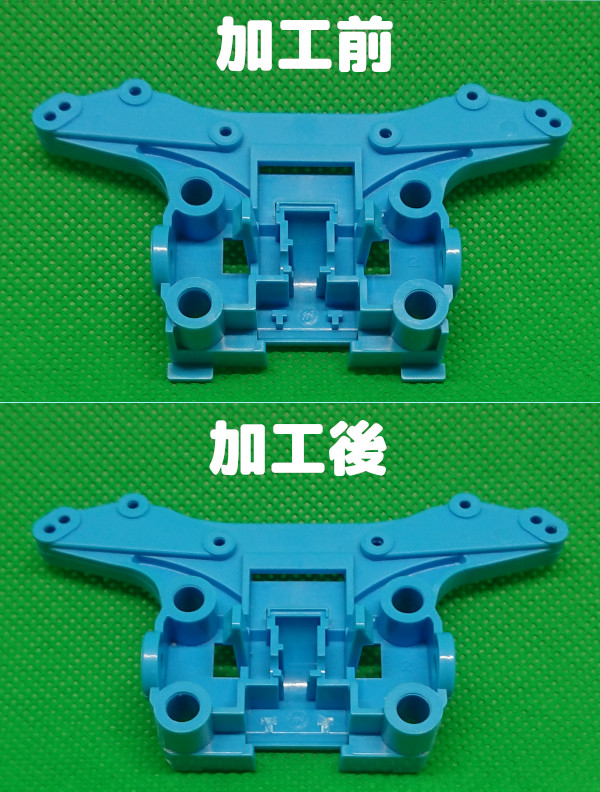
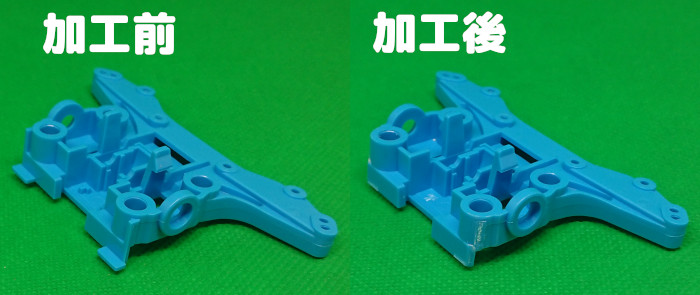
ギヤボックス周辺の加工
ここではギヤボックス周辺とセンターシャーシ接続穴を加工してきます。
まず最初にこの項目での加工完了後の画像を載せておきます。
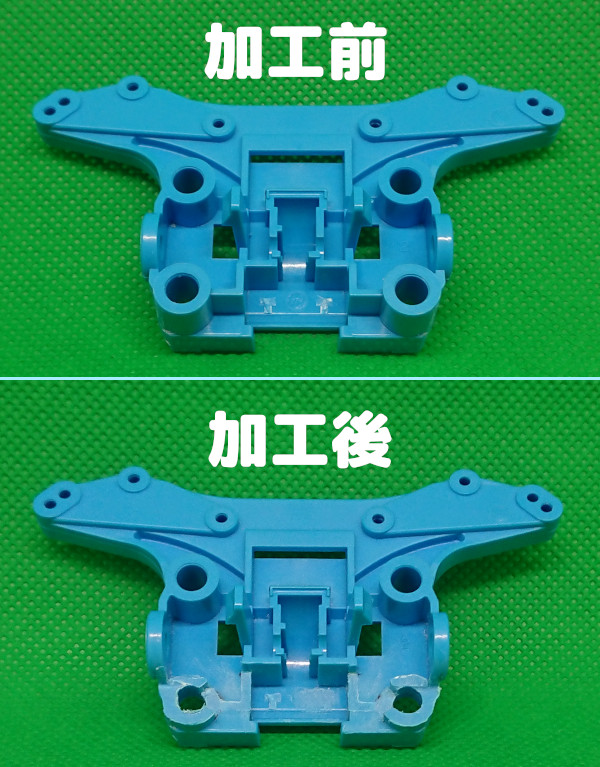
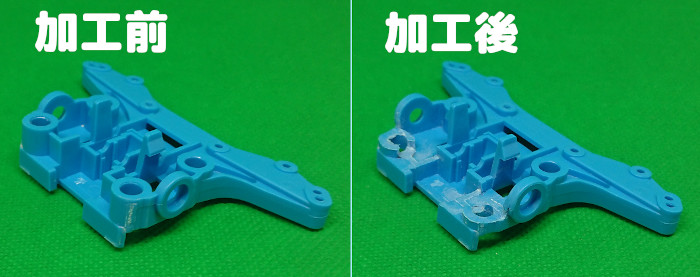
ここの加工については3段階に分けて解説していきますが、加工に慣れている方は以下のフェーズ1・2・3を見ずに上の画像を参考にして加工してしまっても問題ありません。
フェーズ1
まずはフレキ可動域を調整できるようにするため、ギヤボックスの高さに合わせて以下の画像の黒い箇所をカットしてきます。
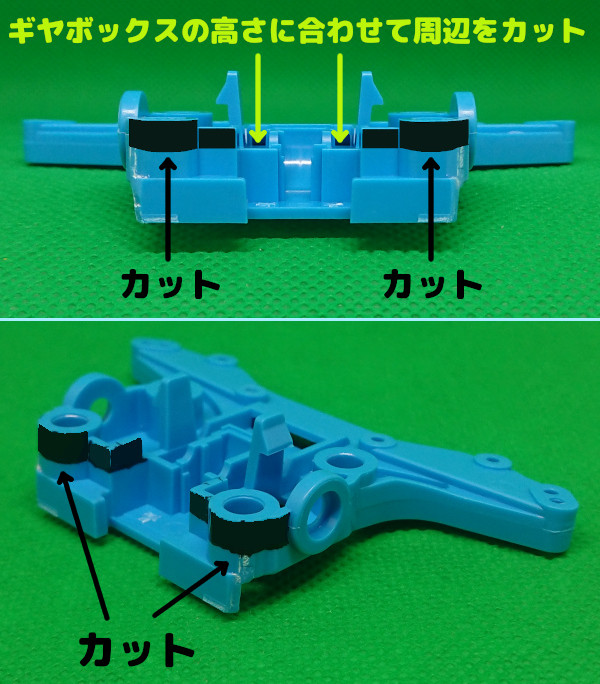
カット作業はギヤボックスの位置を随時確認しながらでも構いませんが、油性ペンかマルチテープで以下の画像のようにカットする目安を付けておくと作業がやり易くなります。
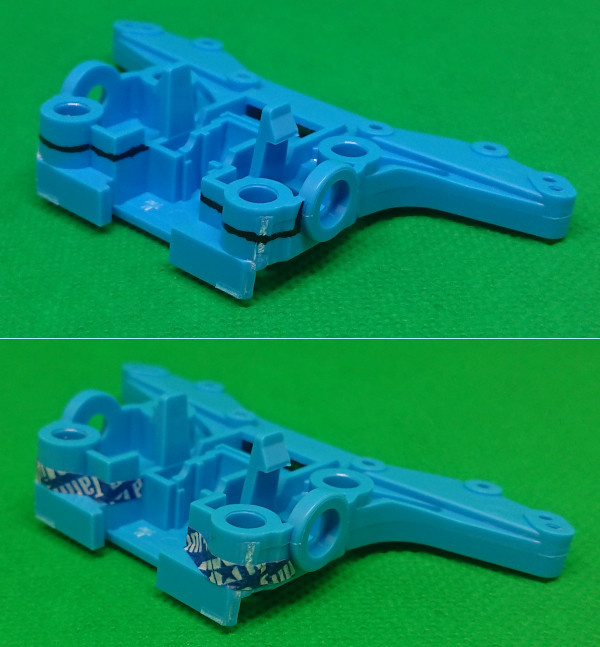
尚、私の場合は油性ペンで境界線を引いた後にカットする箇所に斜線を引いてカットする目印を付けました。
(この辺は各自 間違えずカットできる 自分の分かりやすい目安を付けていきましょう)
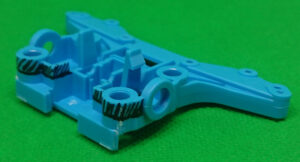
目印を付けたらニッパーでひたすら切り落としていきます。
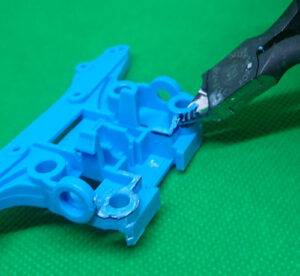
クラフトのこの扱いになれている方であれば、以下の画像のように 最初はまずフロントユニットの真横からカットする境界線めがけてのこ刃を入れます。
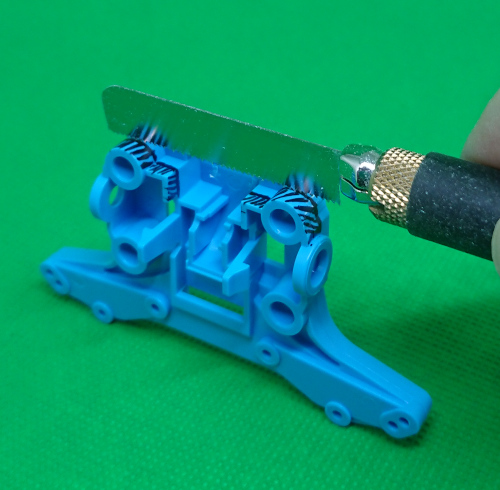
ある程度削れたら今度は縦からのこ刃を入れ、削り取れなかった箇所はニッパーで切り落とす やりの方が早いかもしれません。
最終的に以下の画像の形まで削ってフェーズ1は完了です。
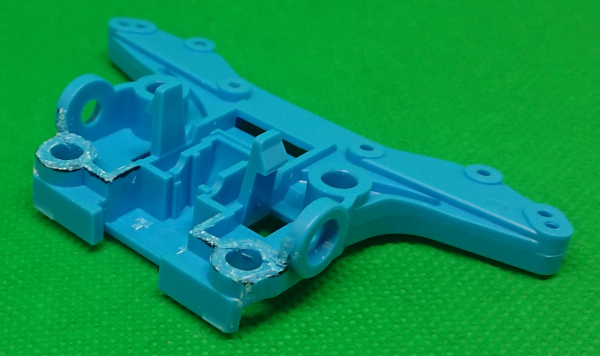
上の画像だと切り口が粗くなっていますが、後ほど綺麗に整えていくので まずはざっくり削った形で問題ありません。
上記加工作業は可動域を調整するために実施しますが、カットした部分の高さで可動域の範囲が決まるわけではないので、誤ってギヤボックスよりも低い位置まで削ってしまっても問題ありません。
むしろ少しだけギヤボックスよりも低めに削っておいた方が後々楽になります。
尚、今回の加工では樽バネは使用しませんが、樽バネを使用するケースでは上記のカットする位置の高さで可動域を調整することになるので、その場合はギヤボックスの高さに合わせて加工していきましょう。
上記作業をする際にシャフトホールをカットしてしまうと、シャフト・タイヤ周りの耐久性が落ち駆動に影響してしまうことがあるので、シャフトホイールの周りはしっかりと残すようにしましょう。
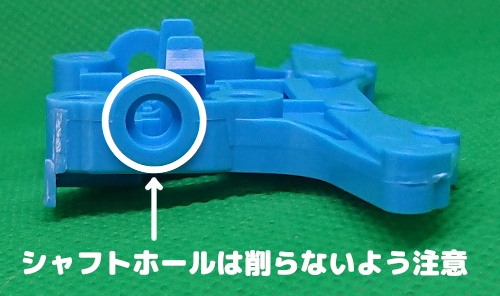
特にのこ刃を使用する際は刃を入れすぎてシャフトホールまで削ってしまった… ということにならないよう注意しましょう。
ただし、シャフトホールが多少削れる分には問題ないので、少しぐらい削れてしまっても気にせず作業を続けていきましょう。
フェーズ2
フェーズ1のカットが完了したら、次にフレキ可動域を調整するためのパーツとなるスペーサー・スプリングを置くためのスペースを作るため 以下の黒い箇所をカットしていきます。
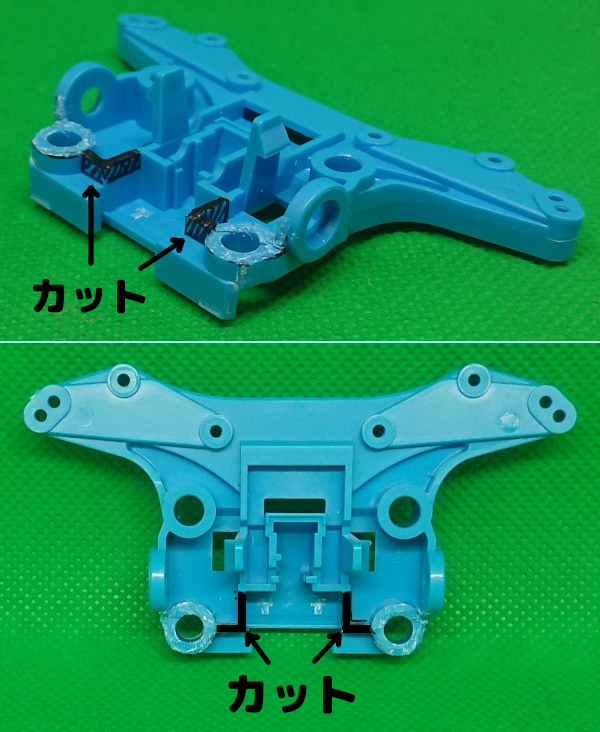
加工作業については先程と同様にニッパーで簡単にカットすることが可能です。
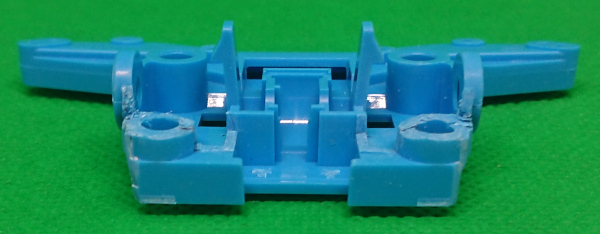
ここから更にスペーサー・スプリングを置くスペースを拡張するため、以下のセンターシャーシ接続穴の一部をカットします。
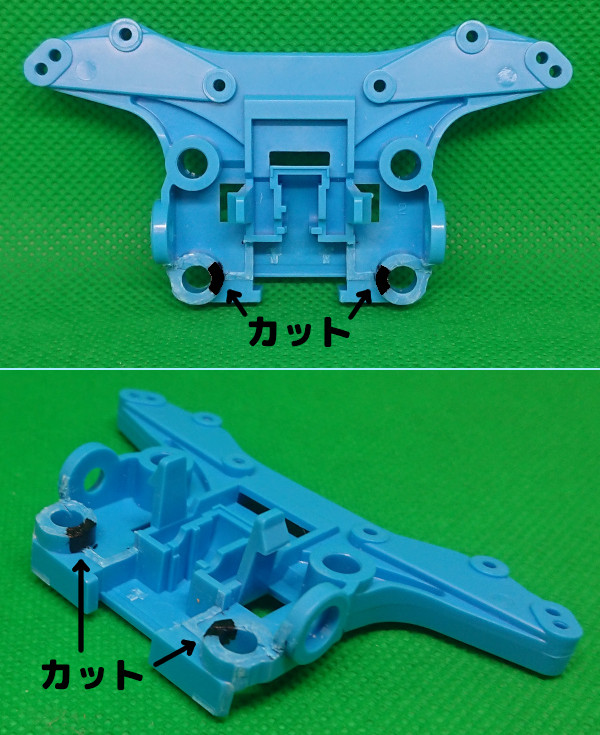
ここもニッパーを使ってカットしていきます。
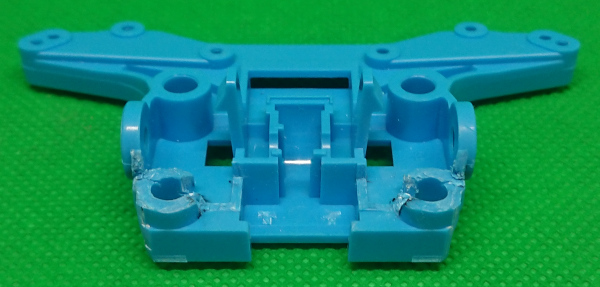
この箇所のカットは具体的な目安はないので大体で構いませんが、カットする位置が分かりづらいという方は「スペーサーの設置」の所を見てからカット位置を決めてください。
上記の加工では穴の一部をカットしましたが、穴の側面を棒ヤスリで地道に削り 以下の画像のように穴の一部をごっそり削り取らなくてもスペーサー・スプリングを置くスペースを確保することができます。
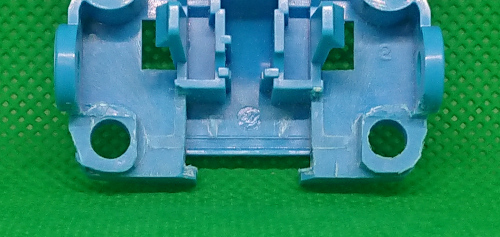
それと、穴全体を残しておくとフレキ可動の精度が良くなると思われがちですが、今回カットする穴の位置なら精度には影響しません。
むしろ、穴の一部をごっそりカットした方がスプリングを置きやすくなるのでどちらかと言えば穴の一部を切り落とす方法を推奨します。
結論として、お好きな方 もしくはやり易い方でOKです。
フェーズ3
フェーズ2までの加工が完了したら、スペーサーを置きやすくするために紙ヤスリ・棒ヤスリを使ってフェーズ2でカットした箇所をなるべく平らな状態にしていきます。
ここの加工は地味に手間がかかりますが、100均でも買える小さめの棒ヤスリがあると比較的楽になります。
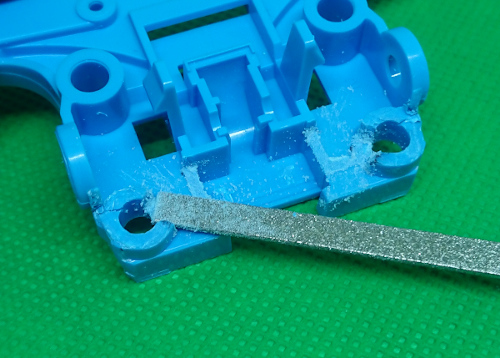
ついでにセンターシャーシ接続穴も棒ヤスリで高さを調整しながら綺麗に整えていきます。
下の画像ではツボサンの棒ヤスリで二穴同時に削っていますが、下の画像のように同時に穴を削る際は くれぐれもヤスリの側面でシャフトホールを削ってしまわないよう注意しましょう。
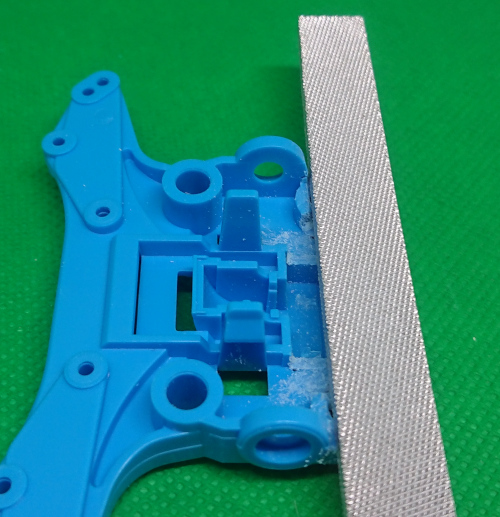
※シャフトホールが多少削れるぐらいなら問題ありません。
ちなみに、上の削り方だと円の一部が削れないので、削れなかった箇所はニッパーで切り落とします。
また、比較的幅が狭い棒ヤスリであれば1穴ずつになりますが一度に穴全体を均等に削ることもできます。
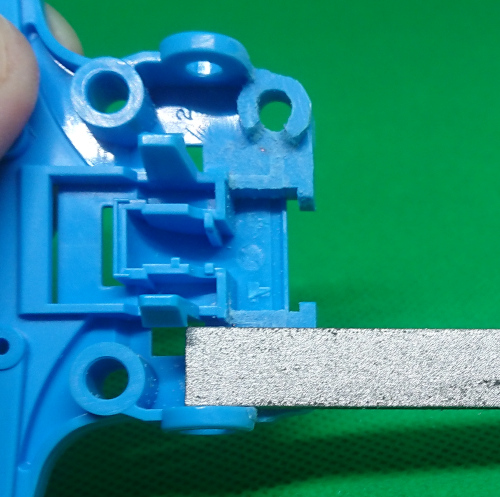
上の棒ヤスリは100円ショップで購入することができます。
スペーサー設置箇所を平らにして、センターシャーシ接続穴の高さの調整が終わったら「ギヤボックス周辺の加工」は完了となります。
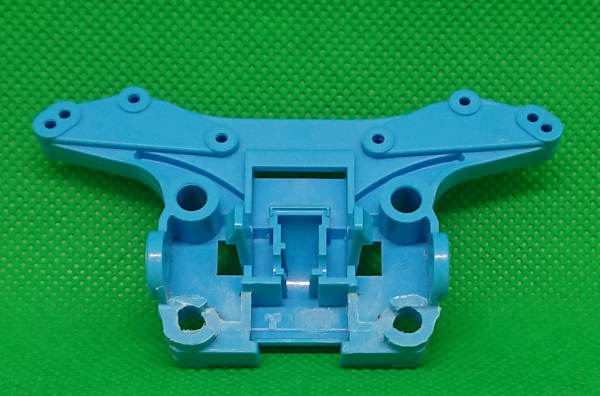
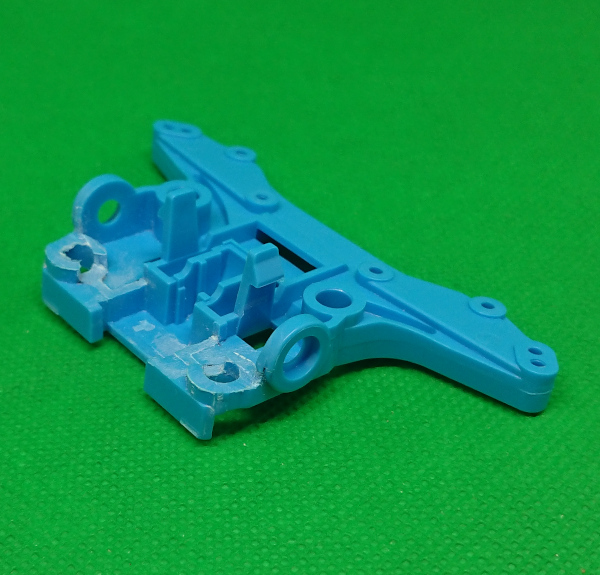
センターシャーシ接続穴の高さは、この後設置するスペーサーの高さよりも低くする必要があります。
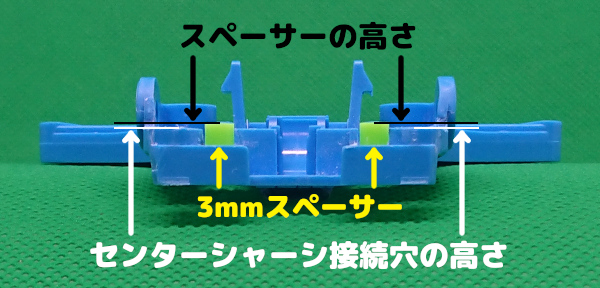
今回は高さ3mmのスペーサーを使用するパターンで解説を進めていきますが、センターシャーシ接続穴の加工が終わったら一度3mmスペーサーを仮置きし 3mmスペーサーの方が高い位置になっていることを確認します。
もし、センターシャーシ接続穴の方が高い場合はヤスリ・ニッパー等でセンターシャーシ接続穴を削って低くしていきます。
尚、この高さ調整はMSフレキの可動範囲をどのくらいの幅にしたいかによって、適切なスペーサーの高さも変わります。
そして、スペーサーの高さによってセンターシャーシ接続穴の適切な高さも変わってくるので、必ずしも上の加工度合いが正解というわけではありません。
※3mmスペーサー以外を使用した例は「スペーサーによる可動域の調整」をご参照ください。
センターシャーシ接続穴の拡張
センターシャーシの接続穴の高さ調整が完了したら、穴周りの仕上げとしてフレキ可動をスムーズにするためにセンターシャーシ接続穴を拡張していきます。
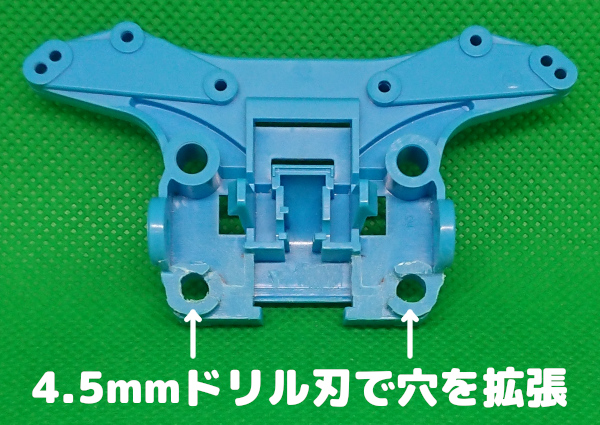
穴の拡張は4.5mmドリル刃を使って貫通させます。
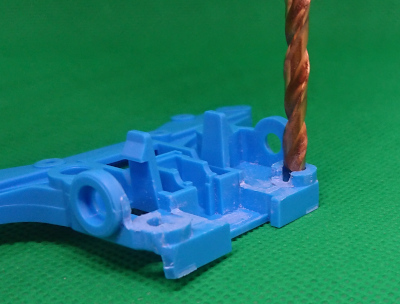
ここはフレキ可動をスムーズにすることも当然なんですが、そのままの穴の状態だとフロントユニットを奥まで押し込むことができずフレキ可動すらしないので この作業は必須となります。
センターシャーシ穴は拡張しすぎてしまうと、ガタつきの原因にもなってしまうのでドリル刃を1回通して拡張完了で構いません。
ただし、ドリル刃を1回通しただけでは可動がスムーズにいかないことがあり、その場合はセンターシャーシ側の加工で補っていく必要があります。
可動がスムーズにいかない原因や具体的な加工方法については別記事[MSフレキの加工精度を上げる方法]の「シャーシ間接続穴周り」にて解説しているので、そちらをご参照ください。
※この箇所の加工はMSフレキ作成において 非常に重要な部分でもあるので慎重におこなってください。
ツメ周りの加工
ここでは可動をスムーズにするために以下の加工を行います。
先程ツメを切断した箇所にバリ(不要な出っ張り)があるので、このバリごとニッパーで斜めにカットします。
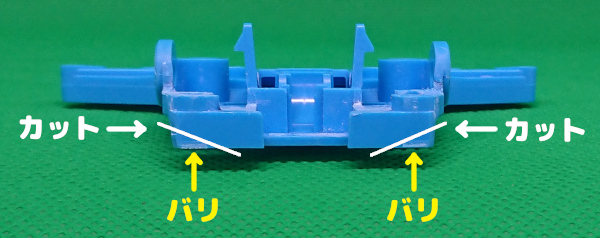
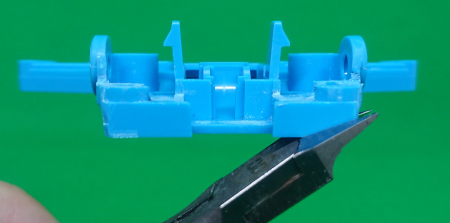
ここのカット具合でフレキ可動の精度に影響するということはないので、目視でざっくりカットして構いません。
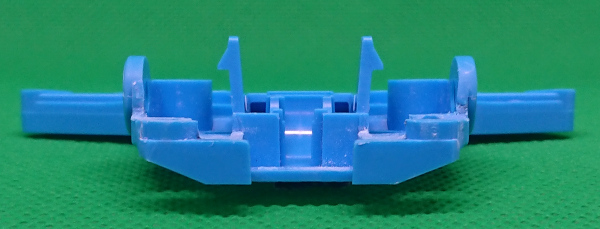
この部分をカットする目的としてはセンターシャーシの接触箇所の面積を若干ではありますが減らすことで摩擦が減りフレキ可動がスムーズになりやすくなります。
ただ、正直なところカットしてもしなくてもほぼ変わらないので、斜めカットの状態が好きではない方はこの作業は飛ばして次の作業に行っても構いません。
※カットしなかった場合は次の加工作業でバリを取っていきます。
バリのカットが完了したら、バリがあった面を板ヤスリか棒ヤスリで削っていきます。
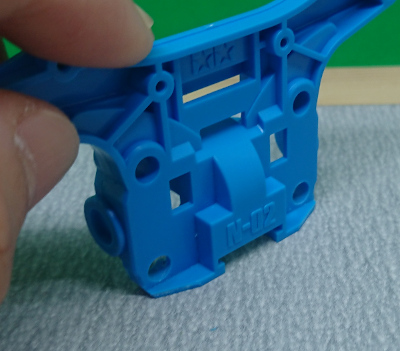
この作業をおこなうことでセンターシャーシとの摩擦箇所を減らし、フレキ可動をスムーズにすることができます。
また、センターシャーシと接触する箇所のため なるべく面をツルツルの状態にしておきたいので、最初は粗目のヤスリで削って問題ありませんが、最後の仕上げは番手#1000以上のヤスリを使うことを推奨します。
削りすぎるとガタが出る。
この箇所を削らないとスムーズに可動しませんが、削り過ぎるとフロントユニットがガタついてしまうので、ここは慎重に削っていきます。
削る目安としてはセンターシャーシ接続穴の側面の横幅が2mm~3mmぐらい削れるぐらいまでがおすすめです。
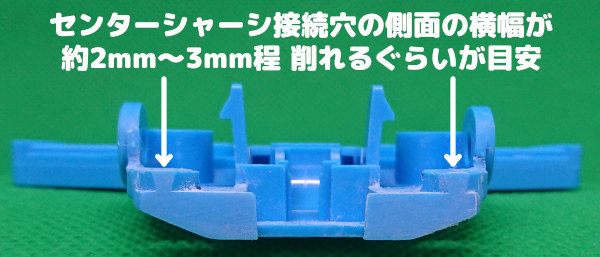
ただし、パーツにより個体差もあるので必ずしも上画像の削れ具合がベストということではありませんのでご注意ください。
どのくらい削ってよいか分からない場合は、一旦は軽めに削り 後ほどセンターシャーシと組み合わせて可動テストをした際にスムーズでなければ再度削るで構いません。
ギヤケース外側の接触部分の加工
ここではセンターシャーシのギヤケース外側と接触する以下の画像の白線部分を加工していきます。
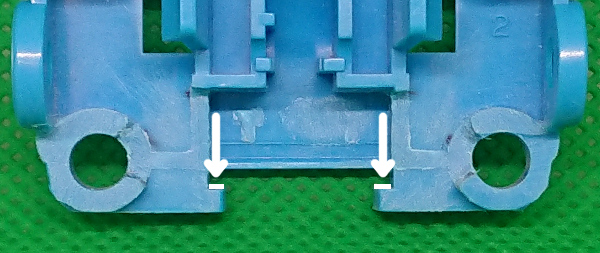
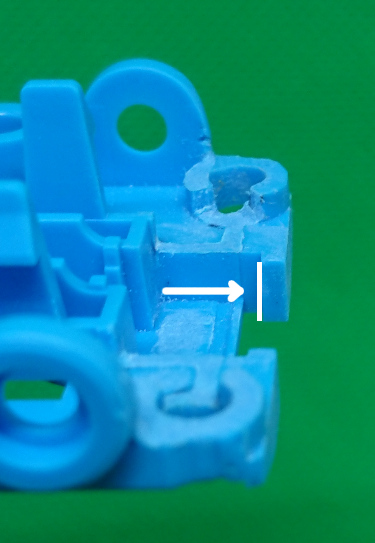
ここ加工はフレキ可動をスムーズにするためと可動域調整をできるようにするための複数の要素があり、加工しすぎてしまうとシャーシのガタつきにも影響してしまうので慎重に作業をおこないましょう。
※この箇所の加工が必要な具体的な理由については「ギヤケース外側での可動域調整」で解説しています。
この箇所の加工手順は2フェーズに分けて解説していきます。
フェーズ1
このフェーズ1の加工は必須ではなく、可動域を広くする必要がなければ不要です。
今回は3mmスペーサーを設置した場合の可動域を考慮したパターンとして以下の箇所をカットしていきます。
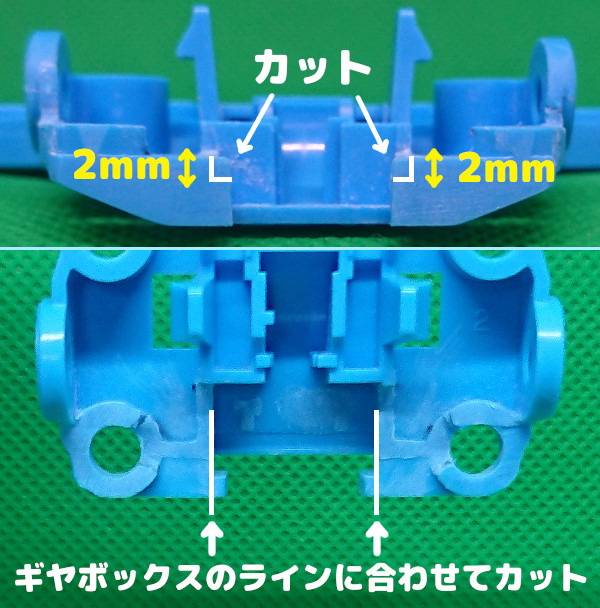
まずは上から2mm程の高さまでのところにニッパーで縦に切り込みを入れ、次は横からニッパーを入れて四角形の形に切断します。
上記以外の加工パターンについては「ギヤケース外側での可動域調整」をご参照ください。
フェーズ2
フェーズ2では下画像の白線の箇所を棒ヤスリで削っていきます。
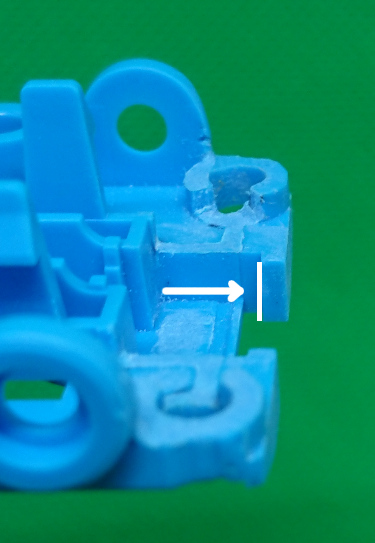
隙間が狭い箇所のため使用する棒ヤスリが厚めのものだと関係ない箇所まで削ってしまうので、薄めの棒ヤスリを使用することをおすすめします。
薄めの棒ヤスリを持ってない人は100円ショップで買える小さい棒ヤスリを使用すると作業がやり易くなるのでおすすめです。
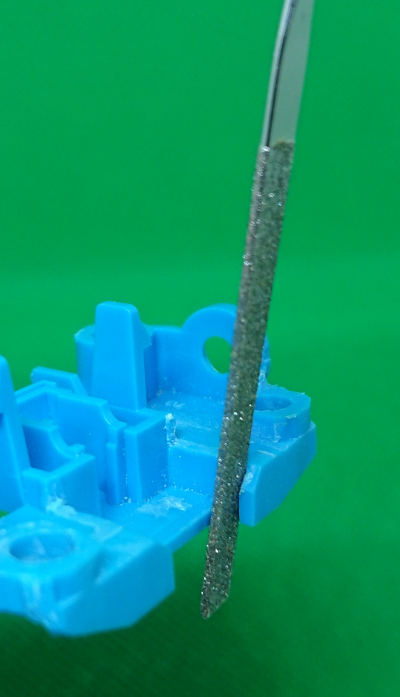
この箇所の削り方については色々なパターンがあり、個人的には下の部分は幅を広めにして上にいくにつれて徐々に狭くして斜めに削るパターンがおすすめです。
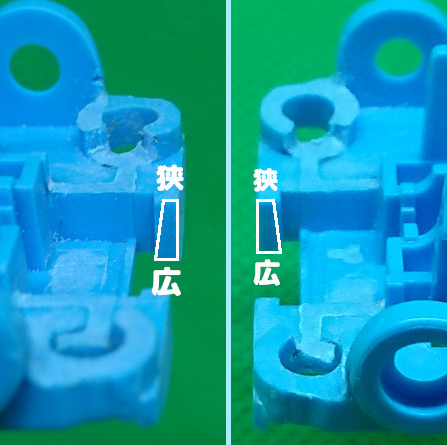
私自身が削った後の状態は以下となりますが、この形がベストというわけではないので1例として参考にしてください。
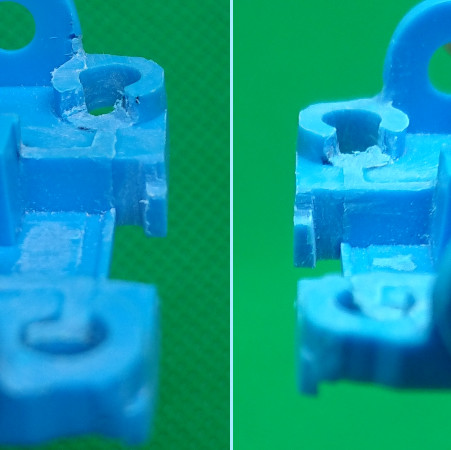
またこの箇所は自分が可動させたい範囲によっても加工具合が変わってきます。
可動域を狭くしたい場合は軽く削るぐらいで構いませんが、可動域を広くしたい場合はそれなりに削らないといけませんので一概にこれぐらい削った方がいいという指標がありません…
とにかく「少し削って可動確認、また少し削って可動確認」という具合に できるだけで削る量を最小限に抑えるようにしましょう。
尚、センターシャーシ側を加工することにより この箇所の加工を最小限にすることも可能です。
センターシャーシ側の加工方法については別記事[MSフレキの加工精度を上げる方法]の「ギヤケース外側」で解説しているので、そちらを見てからこの箇所をどのくらい加工するか決めても良いです。
下部は極力削らない。
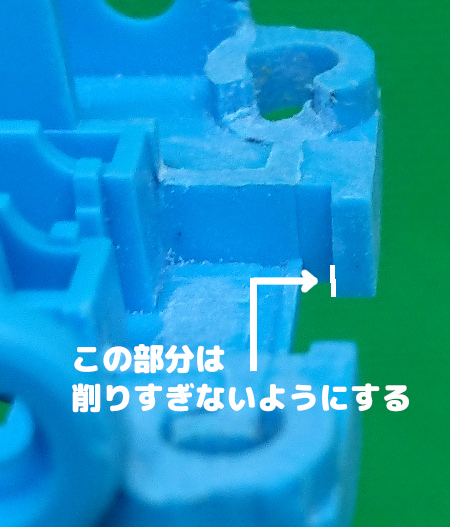
上の画像で記した白線の箇所(地面側の箇所)を削りすぎてしまうとシャーシがガタつきやすくなるので要注意です。
とは言え、下部を削らないことには可動がスムーズにならないので、最低限削る必要があり今回の改造で最も調整が難しい箇所でもあります。
極力ガタつかないシャーシにするためにも、手間ではありますが 少し削っては加工済みのセンターシャーシと組み合わせて 可動の確認を繰り返し 地道に削っていきましょう。
また棒ヤスリで削る場合、厚さがある棒ヤスリだと関係ない箇所を削ってしまう可能性があるので、適切な厚さの棒ヤスリがない場合は紙ヤスリで地道に削ることをおすすめします。
Tモールド箇所の加工
ここの加工作業についてはフレキの可動域によっては不要になるので、組み立てて可動確認をしてからの実施でも構いません。
Tモールドについてはフレキ可動時にセンターシャーシ側のギヤと干渉するため冒頭の作業で切り落としましたが、フレキ可動域を広くした場合はTモールドをカットした状態でもギヤが干渉してしまいます。
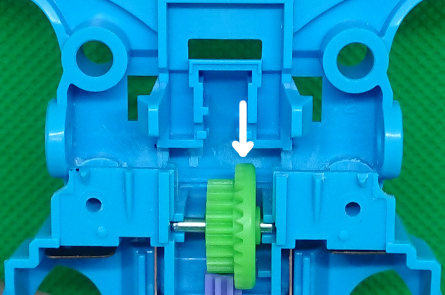
そこでセンターシャーシ側のギヤとの干渉をなくすためにTモールドがあった箇所をごっそりカットしていきます。
加工する箇所の目安としてフロントユニット裏面文字の「N-」の部分を削り落とせばOKです。
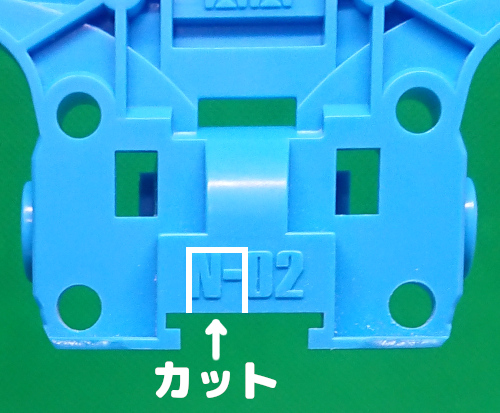
加工方法は以下の画像のような感じでニッパーで切り取れるところまで削って、あとは棒ヤスリで微調整すればそれなりに早く加工可能です。
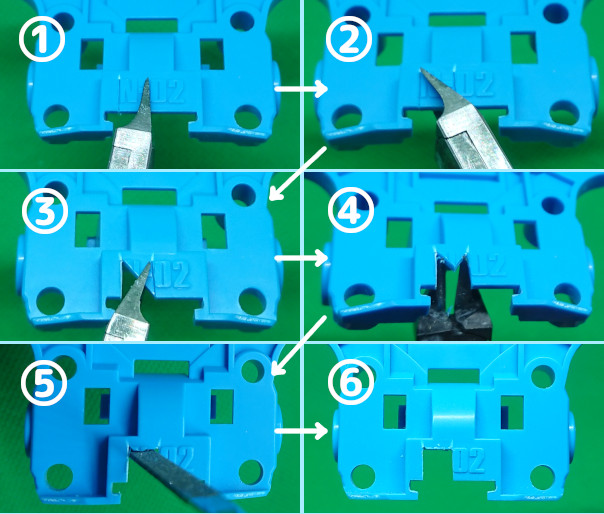
ただ、このままの状態だとギヤが剝き出しの状態になり、ミニ四駆公認規則である「シャーシからグリスが飛散してコースを汚す恐れのある改造は認められない」に抵触してしまいます。
そこでミニ四駆公認規則の条件を満たすために、クリヤーボディーの端材を使ってTモールドの箇所を覆っていきます。
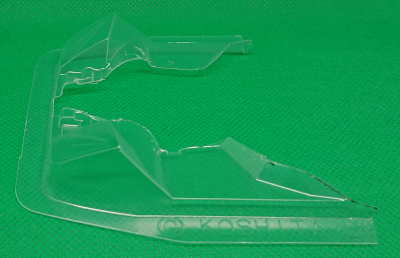
クリヤーボディーは平らな部分の僅かな面積で構わないので適切なサイズに切り取り、接着剤でクリヤーボディーの端材を固定してTモールドの隙間を埋めて完了です。
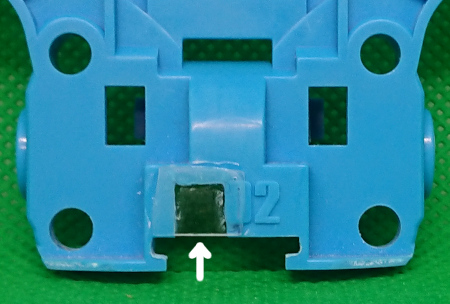
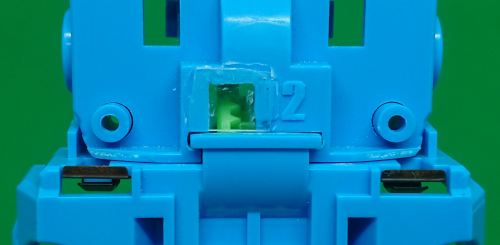
Tモールドの隙間を埋めるパーツはクリヤーボディの端材でなく、マルチテープでも構いません。
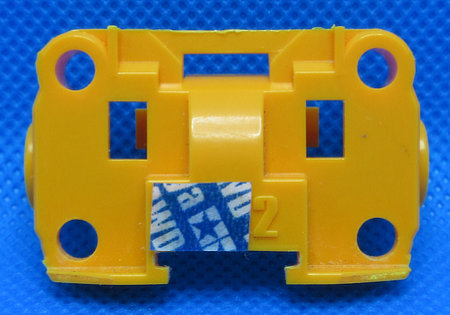
マルチテープでもギヤからグリスが飛散することを防げますし、何よりも作業が圧倒的に楽になります。
『クリヤーボディ自体 所持していない』『クリヤーボディのカット・貼り付けが面倒』という方は、まずはマルチテープを使ってみてはいかがでしょうか。
スペーサーの設置
ここではフレキ可動域を調整することとスプリングを固定させるために、フロントユニットにスペーサーを取り付け固定させます。
今回使用するスペーサーは3mmスペーサーとなりますが、スペーサーでフレキ可動域を調整しないのであれば1.5mmスペーサーを使用する、もしくはスペーサーなしでスプリングを直接フロントユニットに接着剤で固定するでも構いません。
※スペーサーを使わずにフレキ可動域を調整する場合は「可動域の調整方法」をご参照ください。
そして、スペーサーはフロントユニットの以下の場所に設置していきます。
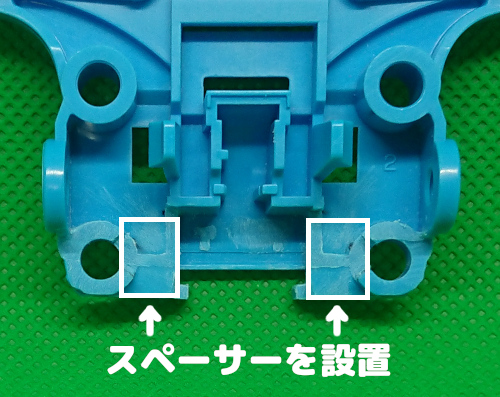
スペーサーの設置する場所は「具体的にここ」という指定はないので お好きな場所で構いません。
ただし、スペーサーにスプリングを取り付けた状態で以下の画像の黄色・黒ラインを超えてしまうとスプリングが正常に動作しなくなるので、スプリングがライン内に収まる位置でスペーサーを設置します。

スペーサーだけだとどの辺に置けば枠内に収まるかがわからないこともあるので、一旦スプリングを仮置きして設置位置を確認しておきましょう。
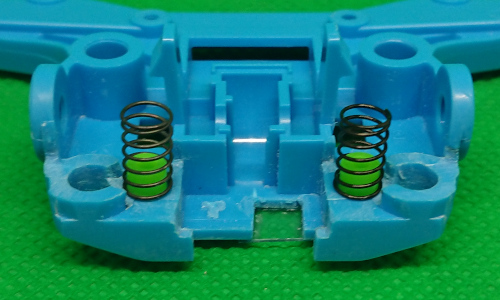
また、スペーサーをしっかりと接着させるためにも事前にブラシがけか水洗いをして削りカスを取り除いておきます。
位置が決まったら接着剤でスペーサーを固定してフロントユニットの加工は完了となります。
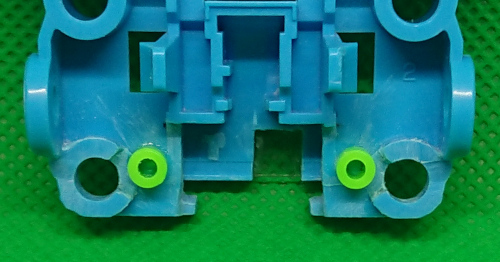
この後 可動確認にてスムーズに可動しなかった場合にフロントユニットを再度加工する必要がでてきます。
スペーサーを接着剤で固定していると再度加工する際に加工箇所によってはスペーサーが少し邪魔になったりします。
そのため、ここでは一旦スペーサーを両面テープ等で仮止めして、可動に問題ないのを確認してからスペーサーを固定しても構いません。
スペーサーの強固な固定
ここでは上記のスペーサーの設置の項目で取り付けたスペーサーをより強固に固定する方法を解説していきます。
ただし、ここの加工作業は必須ではなく 必要と感じた時に実施すればよいので初めてMSフレキを作成する場合は、ここは飛ばして次の可動確認に進んでもらって構いません。
すでにスペーサーを固定しているにも関わらず何故スペーサーの強固な固定が必要なのかといいますと、接着剤の固定だと何かしら強い衝撃を受けた際にスペーサーがフロントユニットから剝がれてしまうことがあります。
準備編でも紹介した以下の接着剤であればかなり強力に固定してくれるので そう簡単に接着は取れませんが、完全に固定できるわけではありません。
仮に走行中にスペーサーが外れてもシャーシ内部にあることとスプリングも付いているので 走行中にマシンからこぼれ落ちてることはありません。
ただ、そのままにしておくとスプリングが正しい位置に固定されないので、再度スペーサーを接着剤で固定する必要があります。
スペーサーが外れる度に接着剤で固定しても問題ないと思う方であればこのままでOKですが、外れる度に接着剤を使用するのが面倒くさいという方は、ビスとナットを使った以下のスペーサー固定の加工をすることをおすすめします。
スペーサーをより強固に固定する方法は以下となります。
まずはフロントユニットにスペーサーが接着剤で固定されている状態で、スペーサーをガイドとしてスペーサーの穴に2mmドリルをあてフロントユニットにビス穴をあけます。
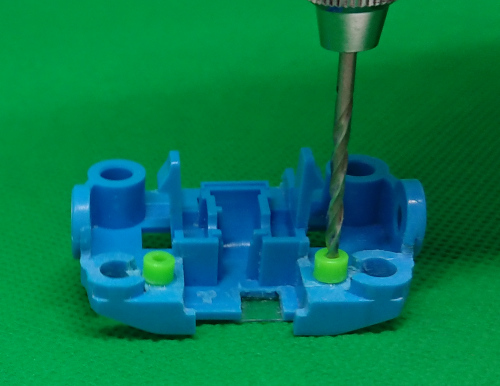
ビス穴をあける作業の際に接着剤で固定したスペーサーが取れてしまうと思いますが、取れてしまって問題ありません。
ただ、ビス穴が開く前にスペーサーが取れてしまうと穴の位置がズレる可能性もあるので、スペーサーの固定している位置に正確に穴あけをするのであれば電動ドリルよりもピンデバイスを使って慎重に作業した方が無難でもあります。
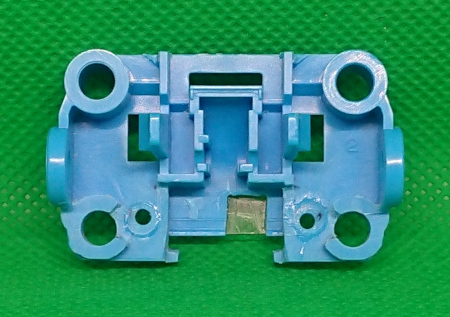
上の画像はビス穴をあけたあとの状態となりますが、ビス穴をあける際はナットを取り付けるスペースを確保することを意識してください。
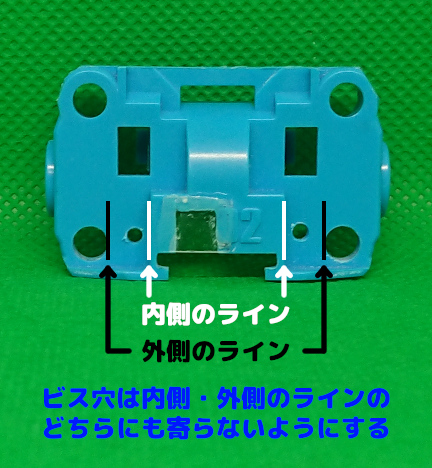
上画像の内側と外側のラインのどちらかに寄り過ぎてしまうとナットの取り付けが難しくなるので注意してください。
もし、接着剤で固定したスペーサーの穴の位置がどちらかに干渉しているのであればスペーサーを外して、スペーサーをガイドとして使わず フロントユニットの裏面から穴あけをしても構いません。
穴あけが完了したら、スペーサーに皿ビスを取り付けるために皿ビス加工をしていきますが、このスペーサーへの皿ビス加工が地味に面倒くさいのです。
そこで、以下の皿ビス加工作業が手間と思う方は、以下の画像のようにスペーサーの高さを変えてワッシャーを使うことで皿ビス加工をせずに皿ビス加工したスペーサーと同じ高さにする方法がおすすめです。
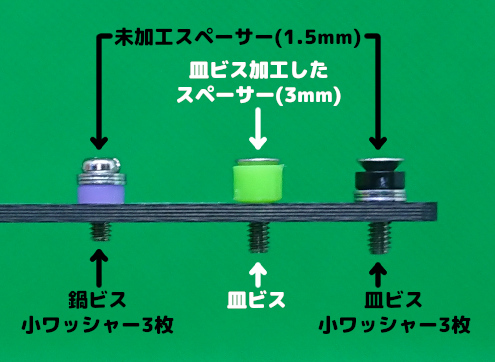
皿ビス加工したものよりも若干重量は増えてしまいますが、上記のようにワッシャーの枚数・種類を変えることで高さの微調整も可能になります。
スペーサーの皿ビス加工方法
ここではスペーサーに皿ビス加工する方法を解説していきます。
フロントユニットに設置するスペーサーはMSフレキの可動域を調整するためのもので、このスペーサーに皿ビスを取り付けた際に極力スペーサーの高さを変えないためにもスペーサーに皿ビス加工をしていきます。
尚、プラスペーサーをランナーからまだ切り離していない状態であれば、そのままスペーサーに皿ビス加工用ビットをあてるだけで簡単に皿ビス加工できます。
このため、以下の方法はランナーからプラスペーサーを切り離した時のみ実践してください。
皿ビス加工はリューターの皿ビス加工用ビットを使用しプラスペーサーを削っていくわけですが、プラスペーサーを床・作業シートなどに直接置いての作業は止めてください。
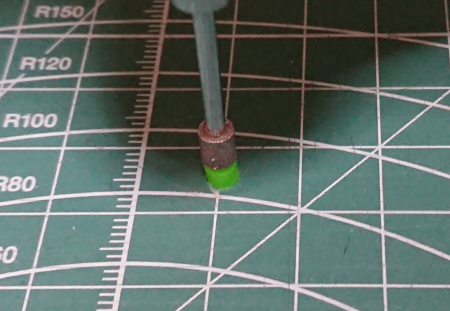
上の画像はカッティングマットの上に直でプラスペーサーを置いていますが、この状態でリューターをあてるとプラスペーサーが回転していまい、プラスペーサーが溶けて下画像のようにカッティングマットも削れてしまいます。
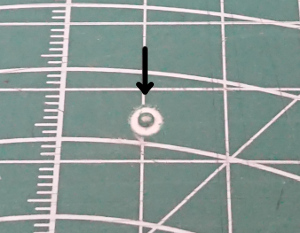
こうなってしまわないためにも、以下の方法を推奨します。
まずは、適当なステー・プレートとビスとアルミスペーサーを用意して以下の画像のように組んでいきます。
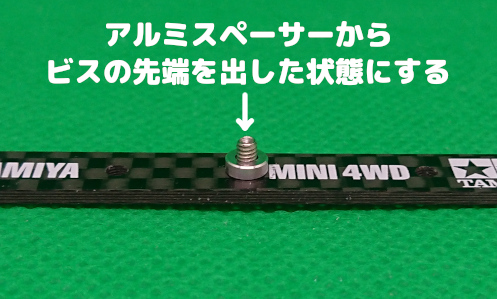
ビスは鍋ビス・トラスビスどちらでも構いません。
ビスの先端がスペーサーから少しはみ出るぐらいになるよう、ビスとスペーサーの長さで調整します。
※上の画像ではカーボンプレートとトラスビス(5mm)とアルミスペーサー(1.5mm)を使用しています。
続いて、アルミスペーサーの上に皿ビス加工をしたいプラスペーサーを置きます。
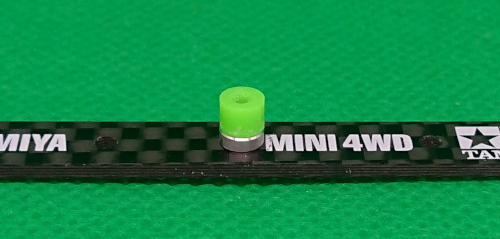
この状態で上からリューターをあてますが、上の画像を見て分かるようにプラスペーサーは完全に固定されている状態ではないので、リューターをあてるとプラスペーサーも一緒に回転してしまいます。
上からリューターを強く押しあてればプラスペーサーの回転は抑えられますが、そうなると肝心のプラスペーサーの皿ビス加工がスムーズにいかなくなります。
そこでプラスペーサーの回転を抑えるために、ペンチでプラスペーサーをガッチリおさえて固定します。
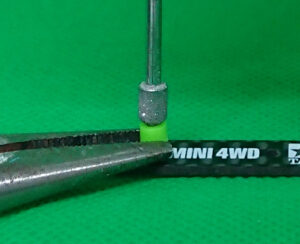
こうすることでプラスペーサーの回転を抑え且つスムーズに皿ビス加工ができるようになります。
尚、上の画像は加工作業を見やすくするよう撮影用の背景用紙の上で作業していますが、土台となる部分も多少削れたりすることもあるので 土台は多少削れても問題がないものを用意しましょう。
身近にあるものでしたら、使わなくなった布類や雑誌などがいいかもしれません。
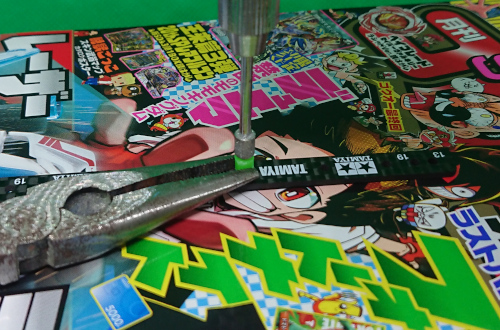
皿ビス加工が終わったら皿ビス(8mm)・ナットで固定して完了です。
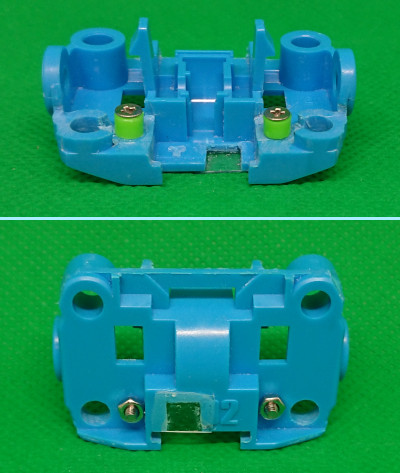
尚、ナットは使用せずにビスごと接着剤で固定することでもスペーサーを強固に固定することができます。
その場合はビスの再利用はできなくなりますが ナット分の重量が無い分 軽くできますし ビスを適切な長さにカットすればより軽くできます。
ビス穴の位置が内側・外側に寄り過ぎてナットが付けられない場合は開き直ってビスごと接着剤で固定するのもありかと思います。
可動確認
フロントユニットの加工が完了したらセンターシャーシと組み合わせて可動がスムーズに行くか確認していきます。
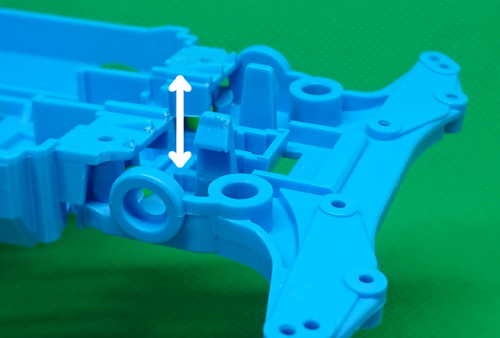
フロントユニットを上下に移動させ、引っ掛かりがなくスムーズに移動できることを確認します。
また、削りカスが原因で可動がスムーズにいかないこともあるので、事前にブラシがけか水洗いで削りカスを取り除いておきます。
もしスムーズにいかないようであれば別記事[MSフレキの加工精度を上げる方法]の「可動をスムーズにする方法」を参考にして、可動がスムーズになるように加工していきましょう。
尚、ここでの可動確認はシャフト・ギヤなどのパーツは取り付けず、フロントユニットとセンターシャーシのみの構成で問題ありません。
ただ、実際にギヤなどのパーツを取り付けるとスムーズさが落ちてしまうので、この段階では可動がスムーズに行くというよりもスカスカに動くぐらいがいいかもしれません。
ただし、スカスカにしすぎた結果 シャーシがガタついてしまったということにも成りかねません。
どのくらいが適切なスムーズさ なのか判別できなければ追加の加工は一旦中断し、最後の仮組みの可動確認の時に追加の加工をするか否かを判断しても構いません。
リヤユニット(T-01)の加工
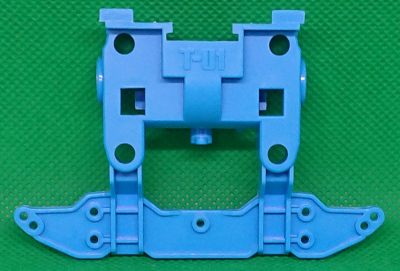
リヤユニット(T-01と文字が入ったパーツ)の加工についてはフロントユニットと同じ加工手順となりますので、加工方法詳細はフロントユニットの加工をご参照ください。
ただし、一部フロントユニットの加工と異なる点があるので、そこだけピックアップして解説します。
まずは加工前と加工後の画像を載せておきます。
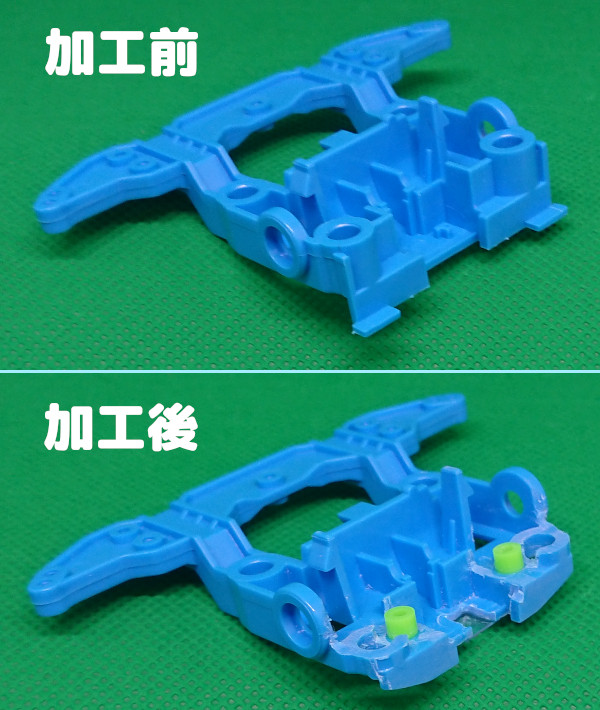
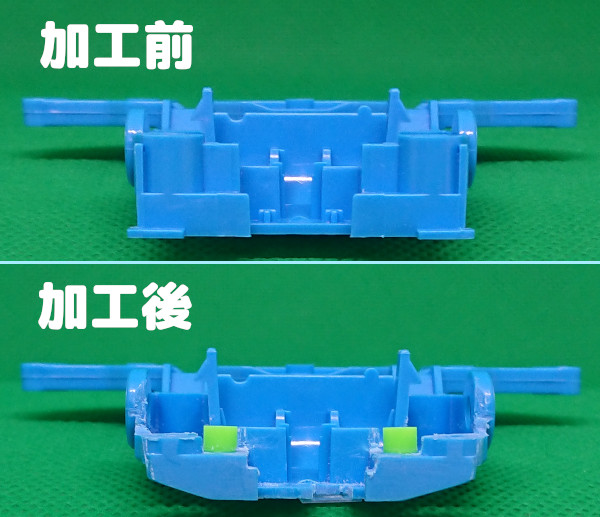
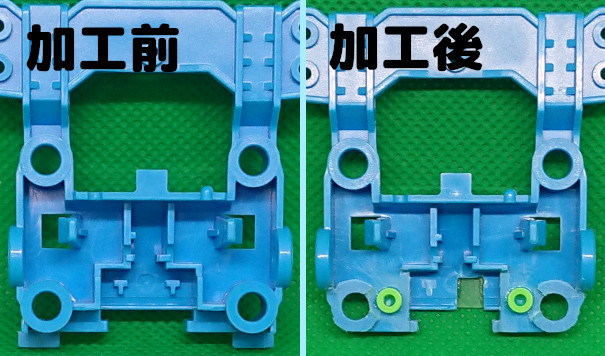
フロントユニット加工と異なる点 -その1-
リヤユニットの加工はフロントユニットの加工に比べて多少加工が甘くてもスムーズに可動させることが可能で、フロントユニットよりも加工難易度が低くなります。
スムーズに行きやすい理由としては、リヤユニット自体の作りもそうなんですが、センターシャーシのリヤ側は支柱の直径が僅かにフロント側よりも細かったりとフロント側とリヤ側で若干作りが異なっています。
試しにフロントユニットをセンターシャーシのフロント側とリヤ側の両方に取り付け 可動のスムーズさを比較するとリヤ側の方がスムーズに行くはずです。
このことからリヤユニットの加工はフロントユニットよりもやや控えめに加工して構いません。
フロントユニットと同じ感覚で加工してしまうとガタついてしまうこともあるので、リヤユニットは慎重に加工することを推奨します。
フロントユニット加工と異なる点 -その2-
フロントユニット加工ともう一つの異なる点としてTモールド箇所の加工目安です。
加工方法自体はフロントユニットのTモールド箇所の加工と同じになるのですが、カットの目安としていた文字が異なってくるので、リヤユニット側の目安となる箇所を以下の画像に記載します。
リヤユニットのTモールド箇所の加工は「01」の部分をカットする形で「0」の所は少し残しても構いません。
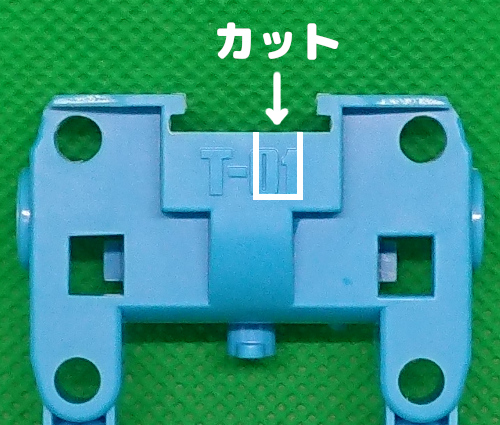
カット方法はフロントユニットのTモールド箇所の加工を参考にして頂き、カットしたらこちらもクリヤーボディの端材を貼り付けていきます。
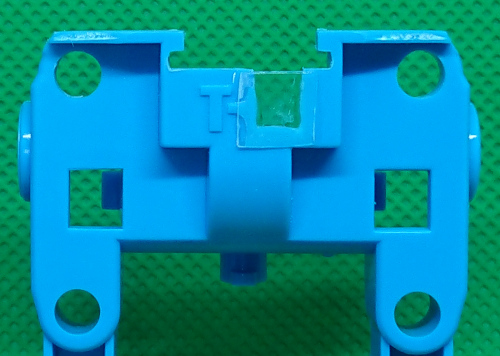
こちらもフロントユニットと同様にクリヤーボディの端材ではなくマルチテープでも構いません。
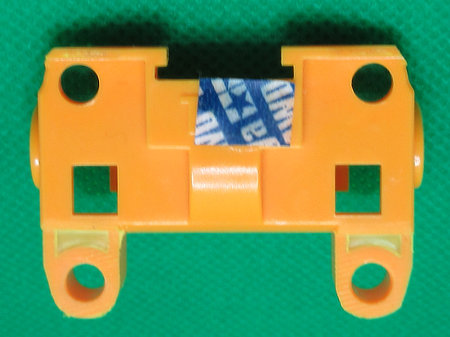
可動域の調整方法
ここで解説する内容はMSフレキを作成する上で必須事項ではなく MSフレキ作成の豆知識的な内容でもあるので、すぐにフレキ作成の続きをしたいという方は「組み立て」に進んでください。
今回解説しているMSフレキ作成方法では3mmスペーサーを使って可動域(可動範囲)を調整していますが、マシンのタイヤ径やコース状況によりMSフレキの適切な可動域(可動範囲)も変わってきます。
そこでスペーサーを使っての可動域を変える方法や、それ以外の箇所で可動域を調整する方法を解説していきます。
スペーサーによる可動域の調整
スペーサーで可動域を調整する場合は、スペーサーの幅が長いほど可動域が狭くなり、幅が短いほど可動域が広くなります。
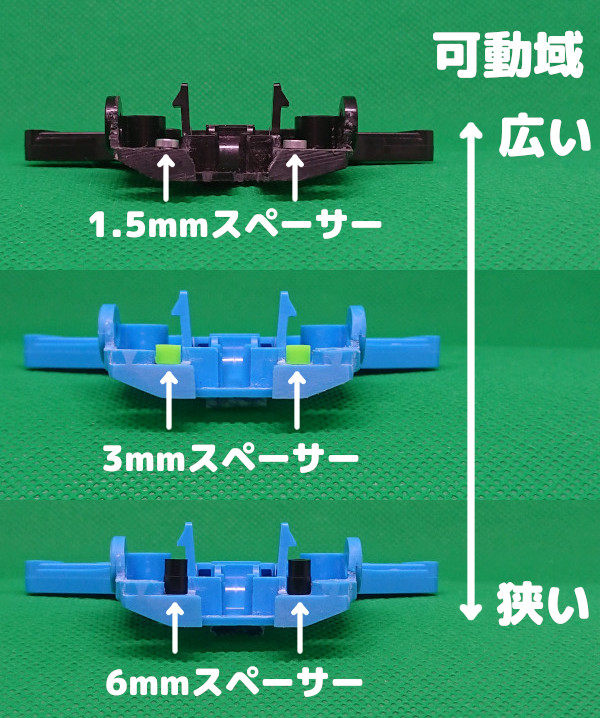
ただし、スペーサーを変えただけでは可動域の調整が完全にできるわけではなく、センターシャーシ接続穴の高さをスペーサーよりも低くする必要があります。
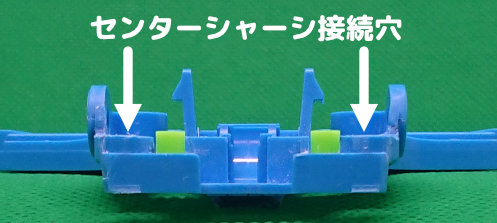
特に1.5mmスペーサーを使う場合はセンターシャーシ接続穴をかなり削る必要があり、センターシャーシ接続穴を削りすぎるとシャーシのガタつきにも影響してきますの 加工には注意が必要となります。
実際のところ、可動域が広すぎるのは実践向けではないと言われており、個人的には3mmスペーサーを使用するがおすすめです。
どの高さのスペーサーを使うかは個々の理想の可動域によって変わってくるので 必ずしも3mmスペーサーを使用する必要はありませんが、短いスペーサーを使用する場合はセンターシャーシ接続穴の削りすぎだけには くれぐれもご注意ください。
また、可動域を微調整したいという場合はスペーサーを削り高さを変えることで対応できます。
スペーサーの高さを微調整加工する際の注意点として、なるべく左右スペーサーの高さが均一になるよう加工します。
同じユニットに設置する左右スペーサーの高さが異なると、同じユニットの左右で可動域に違いが出てフレキ可動の精度が悪くなってしまうことがあります。
参考程度にスペーサーの高さを左右均一にするための加工方法の一例を紹介しておきます。
まず、適当なプレートと適当な長さのビスとナットを用意して、以下のように取り付けます。
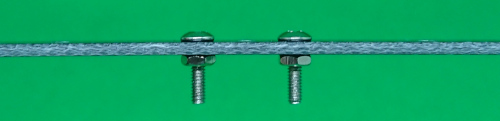
あとは加工したい同じ高さのスペーサーを2個用意して、ビスに取り付け、板ヤスリを使ってプレートを左右に動かしながらスペーサーを削っていきます。
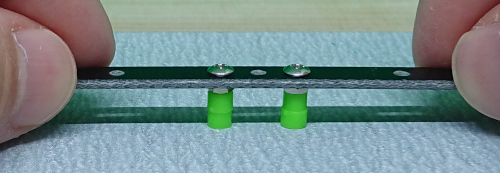
フロント・リヤともに同じ可動域にしたいという場合はビス・ナット・スペーサーを4組用意して一度に4つ削っていきましょう。
またフロントユニット側に少しの加工が必要にはなりますが、スペーサー自体は一切加工せずにビスやワッシャーを使って高さを微調整することも可能で、そのやり方については「スペーサーの強固な固定」の項目で解説しているのでそちらをご参照ください。
ギヤケースでの可動域の調整
可動域を狭くしたい場合は、センターシャーシのギヤケースで可動域を調整する方法がおすすめです。
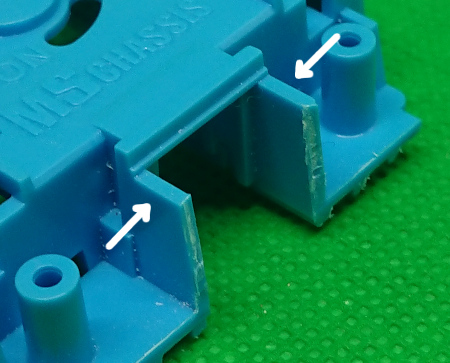
通常であればフレキ可動及び可動域の調整を可能にするためにざっくりカットする箇所ですが、ここを敢えてカットせずに残すことで可動域を調整することができます。
加工方法は至ってシンプルでギヤケースの左右の端を棒ヤスリで削るだけです。
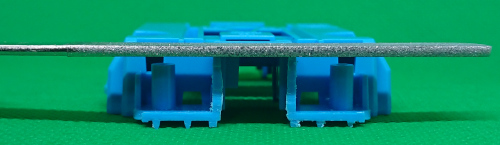
削った分の幅がそのまま可動域になるので、可動させたい幅だけ削ればOKです。
ただ、センターシャーシを見てもらえれば分かりますが、上記の棒ヤスリでギヤケースを左右同時に削れるのは支柱の高さのところまでで、基本的に支柱にヤスリをあてるのはNGなため それ以上削る場合は片方ずつ削っていく必要があります。
片方ずつ削る場合は左右同じ高さにするために微調整していく手間もそうですが、加工する際に支柱が邪魔になり加工難易度が上がるので、可動域を広くしたい場合はこの箇所はざっくりカットしてスペーサーを使う方法が無難ではあります。
このことからギヤケースでの可動域の調整は可動域を狭くしたい時のみに適用した方が良いということなります。
ちなみにギヤケースでの可動域調整方法であればスペーサーは不要?と思うかもしれませんが、スペーサーは可動域を調整する以外にスプリングを固定するための役割もあります。
このため、可動域をギヤケースで調整する場合でも基本的にはスペーサー設置することを推奨します。
(スプリングを直接 接着剤でシャーシに固定するのであればスペーサーは不要です)
ギヤケース外側での可動域調整
以下の画像の矢印で示したセンターシャーシのギヤケース外側の溝の箇所とフロント(リヤ)ユニットの出っ張っている箇所で可動域を調整することが出来ます。
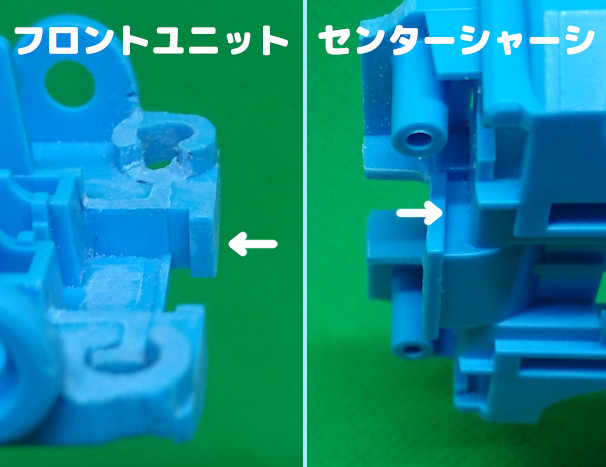
ただ、この箇所の加工については可動域を調整するためというよりは、可動域の制限をなくすためという表現が正しいかもしれません。
というのもこの箇所が未加工のままだと互いのパーツが結合した際にフロント(リヤ)ユニットの出っ張りの箇所がセンターシャーシのギヤケース外側の溝の奥のストッパーに当たって可動域が制限されてしまいます。
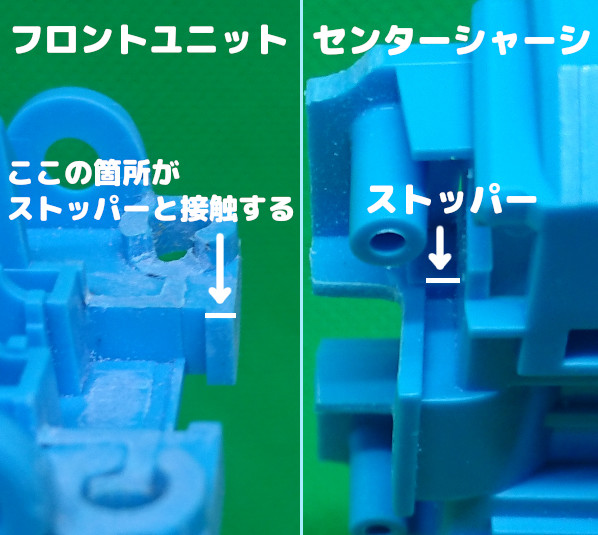
実際に各パーツを加工して可動確認をした時に、フロント(リヤ)ユニット側のギヤボックス周りをカットして、センターシャーシ側のギヤケースもカットしてるのに何故か広く可動しないという現象が起きることがあります。
その原因がこのセンターシャーシのギヤケース外側の溝の奥のストッパーによるものです。
このストッパーで制限された場合の可動域は、スペーサーの高さで可動域を調整した場合で例えると、高さ4mmちょっとのスペーサーを設置した時と同じぐらい可動域となります。
このぐらいの可動域で問題なければ、先に紹介した可動域調整箇所をそれなりに広く可動できるように加工しておけば、ギヤケース外側で箇所で勝手に可動域を調整してくれます。
反対に可動域をもっと広くしたい場合はフロント(リヤ)ユニットを加工する必要があり、その加工方法は以下となります。
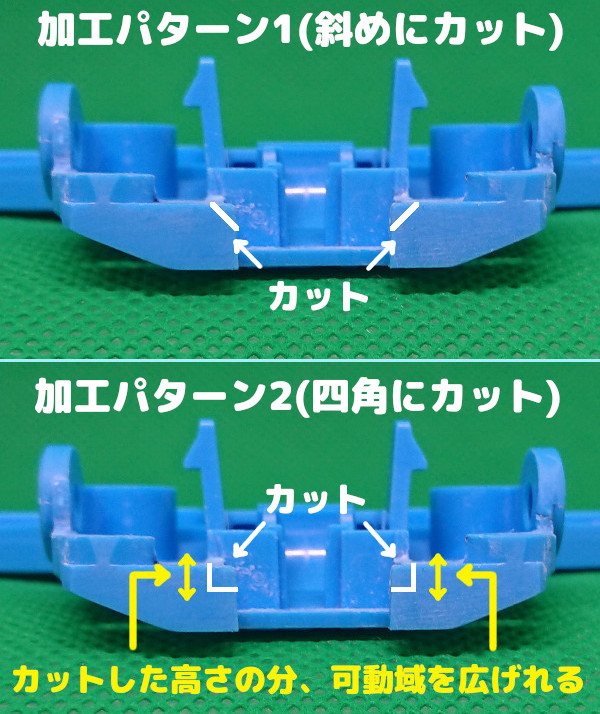
斜めカットで若干可動域が広くなり、四角にカットの場合は縦の高さのカットする幅により可動域を更に広くすることができます。
尚、今回の改造では3mmスペーサーの高さまで可動できるよう、加工パターン2(四角にカット)で約2mm程の高さをカットしています。
組み立て
最後に シャーシの組み立てからMSフレキ完成までを解説していきます。
仮組み・加工・可動確認
ここではギヤ等のパーツがある状態でMSフレキ可動を確認をするために、一旦 各パーツを仮で組み立てていきます。
センターシャーシの組み立て
まずはセンターシャーシにギヤ・モーター・電源スイッチ・ターミナル等の実際に走行させるためのパーツを取り付けていきます。
特にカウンターギヤがあるかないかでMSフレキ可動の感触もだいぶ変わってくるので、各パーツの取り付けが面倒でもカウンターギヤだけは必ず取り付けてください。
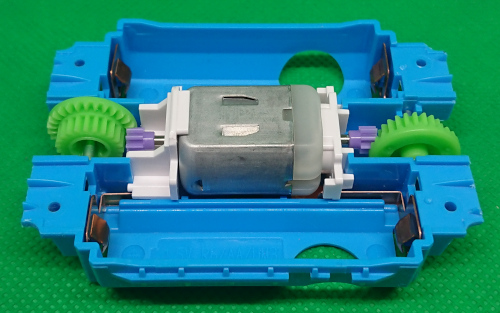
次にギヤカバー・電池を取り付けます。
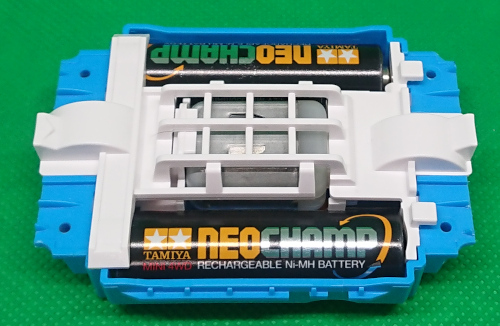
※電池についてはここでは取り付けなくても良いですが、電池の重さがあるかないかでフレキ可動の挙動も変わったりしてくるので、できれば電池も取り付けておくことを推奨します。
電源スイッチの加工
ここで、組み立ての続きをする前に電源スイッチの箇所を加工していきます。

電源スイッチが未加工だとフレキ可動した際に電源スイッチの出っ張り部分が先に地面に触れてしまい、可動域が狭くなってしまうためセンターシャーシの底面と同じ高さになるよう、ニッパーで出っ張り部分をカットしていきます。
くれぐれも電源スイッチをカットすぎて電源が入れられないということにならないよう注意してください。
それと、これは物によって異なる可能性があるので以下の症状に該当する場合のみの加工で構いませんが、電源スイッチのオンオフが結構硬くやりづらいものがあります。
そうした硬い電源スイッチだと出っ張り部分をカットすると尚更オンオフがやりづらくなりますが、オンオフを繰り返しやることで徐々にほぐれてきます。
ただほぐれると言ってもそれなりにオンオフを繰り返す必要があり、そうなる前に自分の爪が割れるなんてことにもなりかねません。
電源スイッチのオンオフが硬いという方は以下の加工を施すと ほぐれてくるので よろしければ試してみてください。
まずスイッチのオンオフが硬くなる原因としては、以下の画像のターミナルと電源スイッチの干渉度合いが強くなっているためです。
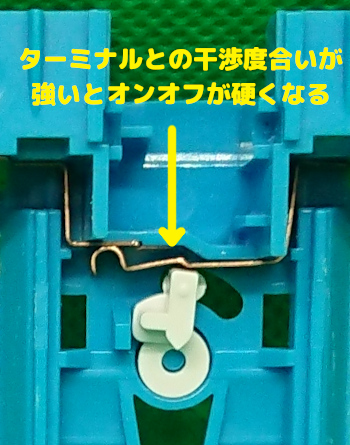
ターミナルとの干渉度合いを減らすことでスイッチがスムーズになるので、以下の画像の箇所を棒ヤスリ等で削っていきます。
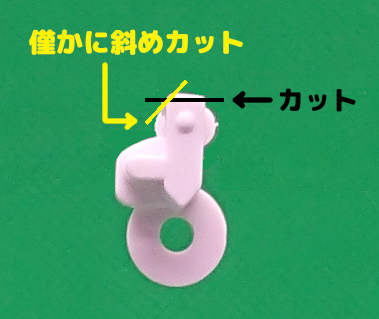
斜めライン(黄色のライン)のカットは極わずかで構いません。この斜めカットをすることでスイッチオンが若干やり易くなります。
また、横ライン(黒のライン)のカットの目安としては、オンオフ時に触れる出っ張り箇所と同じラインになる ほんの少し前ぐらいまで削っていきます。
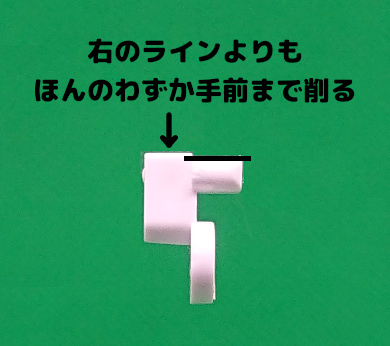
横ラインを削る際はくれぐれも削りすぎには注意してください。
削りすぎると電源オンオフがスムーズになるどころかガバガバになってしまい、走行中に電源オフなんてことにもなりかねません。
少々手間ではありますが、少し削ったらモーター・モーターカバー一式をシャーシにセットしてオンオフ可動が適切な硬さかどうか確認しましょう。
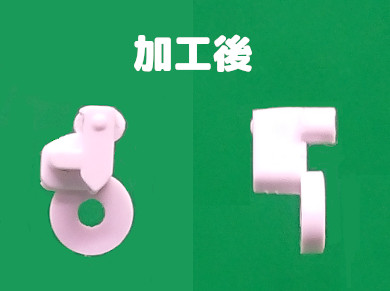
上の加工後の電源スイッチの横ラインはやや削り過ぎてしまった感じもありますが、この状態でも適度な硬さになっているので動作に支障はありませんでした。
軽量センターシャーシは以下の画像のようにスイッチの形状が異なります。
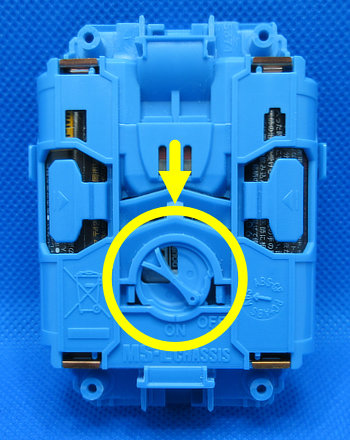
こちらのスイッチもやや出っ張るので削る必要がありますが、このスイッチは削ってもオン・オフのやり易さはさほど変わらず 特別 追加で加工する必要もありません。
通常のマシンキットのスイッチだとオン・オフしづらいということであれば、軽量センターシャーシを使ってみるのもありかと思います。
フロント・リヤユニットの組み立て
続いてはフロントユニット・リヤユニットにギヤ・シャフト・ホイール等の実際に走行させるためのパーツを取り付けていきます。
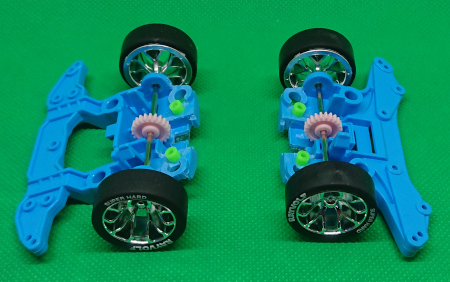
仕上げに加工したユニットカバーを取り付け、スペーサーの箇所にスプリングをセットします。
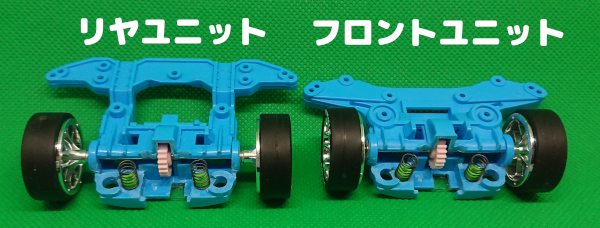
尚、ここで使用するスプリングは以下の4種類から選びます。
基本的にはスプリングセットの黒スプリングが主流ですが、反発が弱いと感じたのであれば同梱している銀スプリングに変えます。
逆に銀スプリングの反発が強いと感じるようでしたらスプリングセット2の金スプリングを使ってみると良いかもしれません。
各パーツの結合
ここまで組み立ててきたセンターシャーシとフロントユニットを結合させていきます。
結合させる際はフロントユニットのシャーシ間接続穴にセンターシャーシの支柱を通します。

リヤユニットも同じようにセンターシャーシと結合させていきます。
MSフレキの可動確認
センターシャーシとフロント・リヤユニットの結合が完了したら、平らな所にマシンを置いてセンターシャーシを上から押してみてスムーズに可動するか確認します。
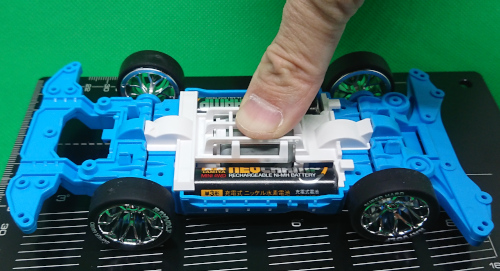
ここで可動がスムーズにいかないようであれば、別記事[MSフレキの加工精度を上げる方法]の「可動をスムーズにする方法」を参考にし、スムーズにいかない原因がどこなのかを調べてみてください。
再度加工が必要であれば一度パーツを分解して該当箇所を加工していきましょう。
MSフレキ可動がスムーズであれば次の工程に進みます。
本組立・最終調整
ここでは最後の組み立てを行い、最終調整をおこなっていきます。
本組み立て
一旦、各パーツを分離して、モーター・ターミナル・電源スイッチのみを取り付けた状態にします。
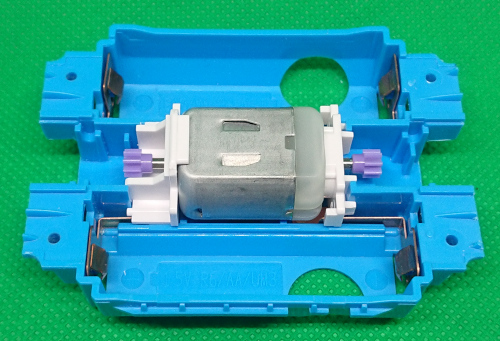
ここでプラベアリング・ビス(15mm)・ナットを用意します。
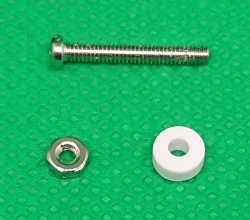
※お辞儀防止ステーを使用する場合はプラベアリングは不要です。
ここで使用するプラベアリングはカウンターギヤ用のものを使用し計4個必要になるんですが、こちらはMSシャーシキット内に2個しかありません。
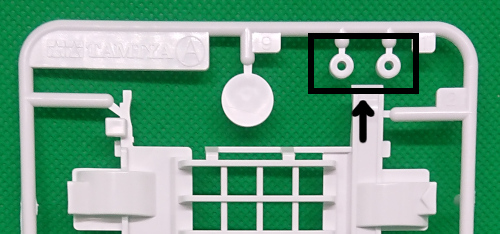
このためMSシャーシのマシンを2キット以上所有している必要があり、所持していない場合はシャフトホールに取り付けるプラベアリングを代用品として使ってください。
ただしシャフトホール用のプラベアリングは直径が大きめで、そのまま取り付けるとフロント・リヤユニットに干渉してしまうので、ヤスリ等で削って直径を小さくします。
ここでは綺麗に円形に削る必要もなく最悪四角形になっても構わないので干渉しない大きさに加工していきます。
それ以外の代用品としてはFRPプレートの余りがあれば、そちらを干渉しないサイズに切り取って使用するのもありです。
上記パーツの用意ができたら再度、フロント・リヤユニットを結合させていきます。
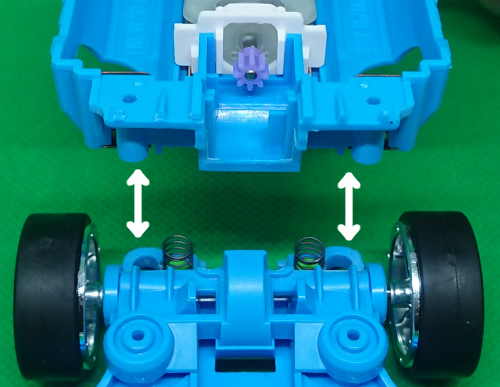
(フロント・リヤユニットはすべてのパーツを取り付けた状態にしておきます)
結合したらシャーシ裏面からプラベアリング・ビスを取り付けます。
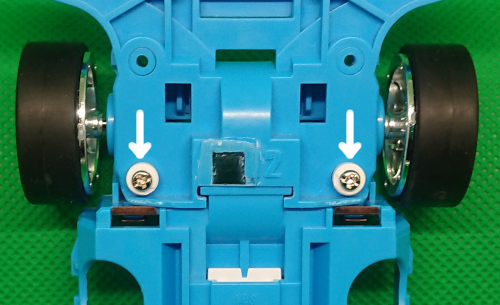
次にシャーシをひっくり返して、表面にナットを取り付けます。
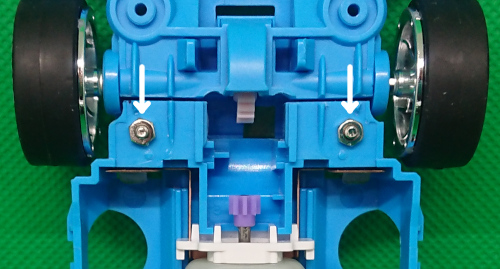
これをフロント・リヤ側の両方でおこない、センターシャーシとフロント・リヤユニットを結合します。
シャーシ間の結合が完了したら、ギヤ・ギヤカバー・電池・バッテリーホルダーを装着して組み立て完了となります。
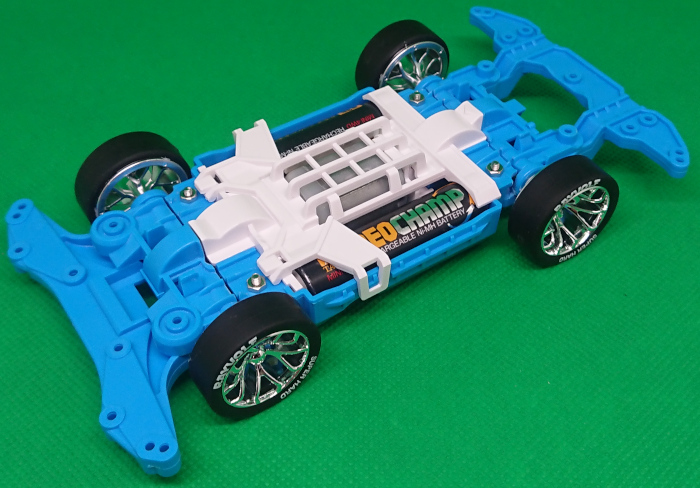
これでMSフレキは完成したわけですが、この後にマシンをメンテナンスする際にバッテリーホルダーが外しづらいという問題が発生します。
この問題については別記事[MSシャーシ ギヤカバーの簡単外し方]の「ギヤカバーの簡単な外し方」の所でバッテリーホルダーの外し方を解説しているので、バッテリーホルダーがうまく外せない方は以下の記事をご参照ください。
また、今の状態だとフロント側のナットを着脱する際に、ギヤカバーのツメにボックスドライバーが干渉してしまうため、事前にギヤカバーを取り外しておく必要があります。
しかし、ギヤカバーのツメをニッパー等でカットして短くすれば、ギヤカバー・バッテリーホルダーを付けたままでフロント側のナットの固定・取り外しができるようになります。
今後のメンテナンスのことを考慮すると この加工も施しておいた方が良いかと思います。
ただし、ツメをカットしすぎるとバッテリーホルダーが固定できなくなるので、くれぐれもツメのカットしすぎには注意しましょう。
ギヤカバーのツメのカット詳細方法は以下の記事で解説しているので、ギヤカバーのツメをカットする際はこちらをご参照ください。
最終確認
シャーシの組み立てが完了したら、センターシャーシを押したり・シャーシを上から落としたりして、フレキ可動に問題ないかを確認します。
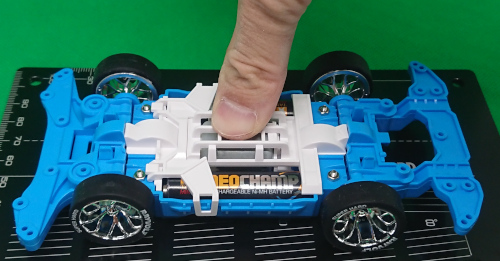
理想的なフレキ動作としては「スッ」と素早く戻るのではなく「すー」とゆっくり戻るのが望ましく、素早く戻ってしまう場合はスライドダンパーグリスを使ってフレキ可動を減衰させます。
グリスを塗る場所は基本的にセンターシャーシとフロント・リヤユニットが接触する箇所であればどこでもいいんですが個人的におすすめなのは以下の箇所です。
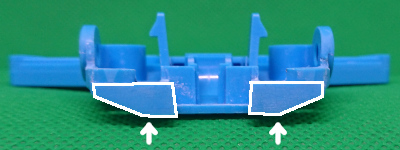
上画像の箇所は比較的にシャーシ間の接触面積も大きいのでグリスを付けた際の効果が出やすく、拭き取りやすい箇所でもあるのでグリスの粘度をいろいろ試しやすく おすすめです。
グリスを付ける以前に、フレキ可動自体がスムーズにいかないということであれば、以下の[MSフレキの加工精度を上げる方法]記事を参考にして よりスムーズな可動になるよう追加で加工をしてみください。
MSフレキ完成
自分の理想のフレキ可動になったらMSフレキの完成です!
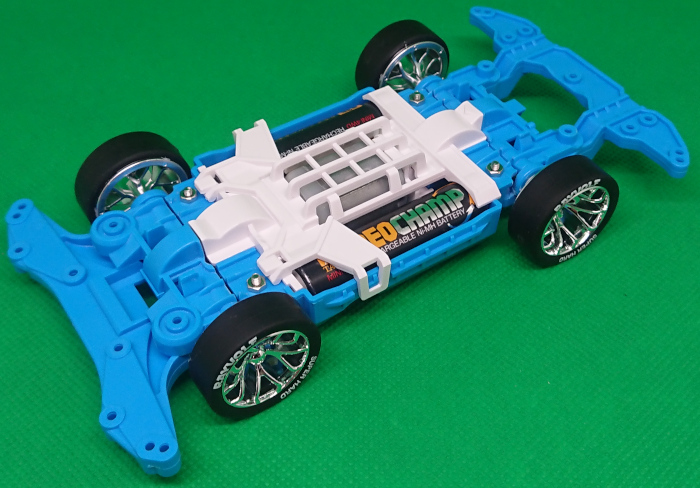
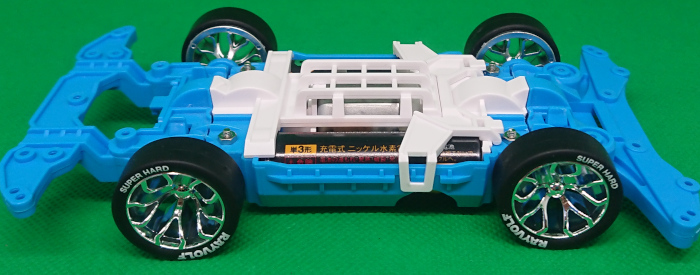
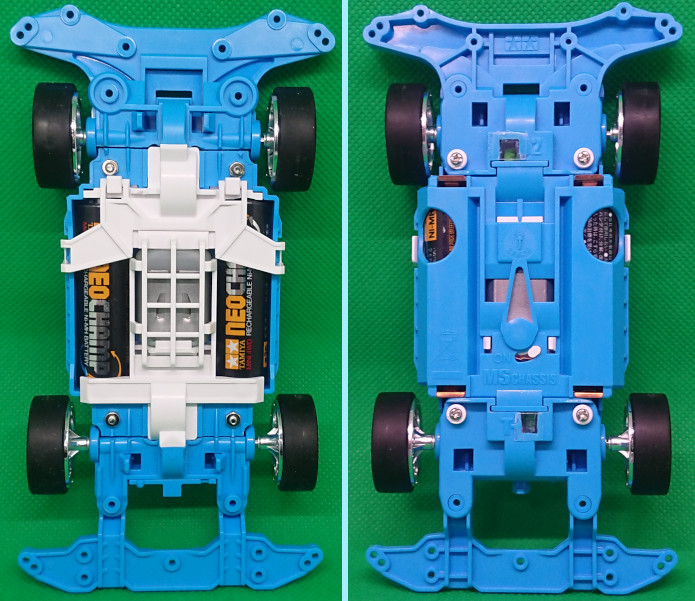
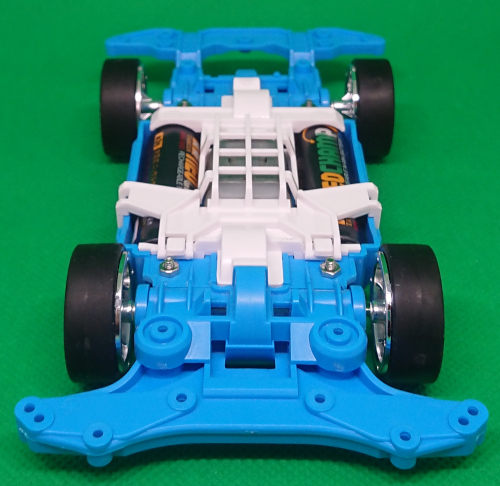
あとはお辞儀防止ステーを付ければ より精度の高いMSフレキになり、フロント・リヤバンパーが不要であれば切断して自分好みの改造をしていきましょう。
※お辞儀防止ステーの作成方法やフロント・リヤバンパーの切断方法については以下の記事で紹介していますので、こちらもよろしければご参照ください。
最後に
MSフレキと言えば初心者から上級者まで実践していて、ミニ四駆をやっている人なら一度はやるであろうと言われる改造です。
今回、自分自身初めてMSフレキを作成するにあたり、書籍・ブログサイト・動画など様々な情報を頼りにしたんですが中々1つの媒体からの情報で作成するのが難しく、調べるだけで かなりの労力を使いました…
そうした自分の経験から、できる限り情報を集約して1つの媒体だけでMSフレキができるような意味も込めて本記事を書きました。
MSフレキの作り方も様々あり、本記事ですべての作り方を紹介できているわけではありませんが、MSフレキ作成を初めてやる方がつまづくであろう点は抑えているので、初めてMSフレキ作成に挑戦する方には非常に有用な内容かと。
またMSフレキを作成していく中で、自分により適した作り方や使用工具・パーツを精査して、自分に適したMSフレキの作り方を見つけてみてはいかがでしょうか。
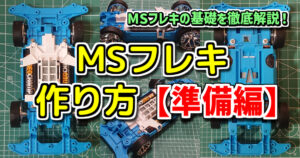
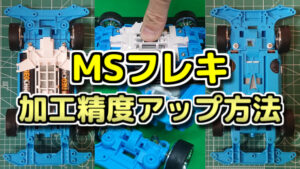
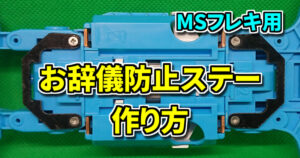
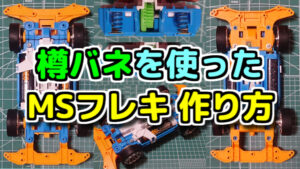
コメント