今回はATピボットバンパーの作成方法を解説していきます。
対応シャーシについては今回作成するATピボットバンパーのベースとなるフロントATバンパーを取り付けることができるものであればどのシャーシでもOKです。
今回の改造のコンセプトとしては、入手しやすいパーツでシンプルな改造を目指したので初心者の方でも比較的簡単にできる改造となっており完成したATピボットバンパーは以下のような形となります。
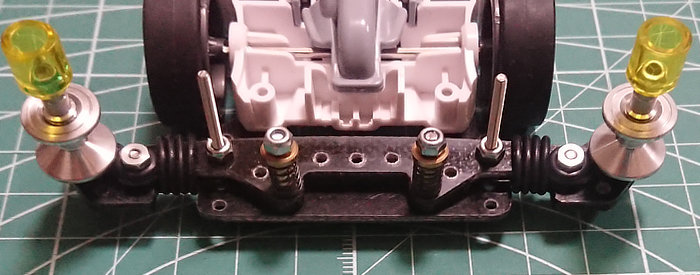
また、ピボットバンパーは構造上 バンパーのビス穴の左右の位置が微妙にずれてローラー幅(最大幅)の調整が面倒くさかったりします。
しかし、本記事で紹介するピボットバンパーは既存のローラー取り付け用のビス穴がそのまま使用できる仕様になっています。
このことから、各ビス穴に適したローラーを取り付けることでローラー幅も規定最大幅(105mm)に簡単に合わせることが可能となっています。
尚、今回紹介するType1とは異なる形状のType2も別記事にて作成方法を紹介しています。
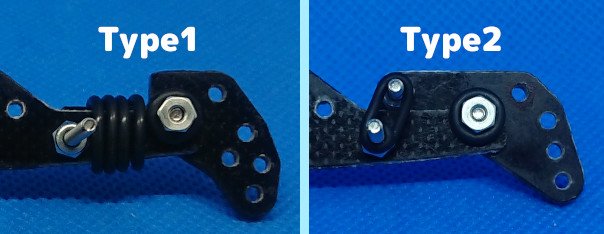
上記2タイプの見た目以外の違いについては以下のType2の記事内で詳しく解説しているので、そちらの記事も読んだ上で気に入った方を作成して頂ければと思います。
必要パーツ・工具
ここでは今回のATピボットバンパー作成に必要なパーツ・工具を紹介していきます。
今回紹介するピボットバンパーは当サイトの別記事で紹介しているフロントATバンパーをベースとしているため、それを作成するためのパーツを用意していることを前提として それ以外に別途必要となるパーツ・工具を紹介していきます。
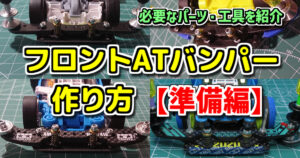
ARシャーシ FRPリヤワイドステー
今回のATピボットバンパーのピボット部(バンパーのローラーを取り付ける部分)となるパーツです。
今回は引っ掛かり防止用としてもう1枚使用するので、合計で2枚必要となります。
(引っ掛かり防止を別の方法でする場合は1枚で構いません)
より安く仕上げたいのであればFRPリヤワイドステーも価格が少し安いARシャーシ FRPフロントワイドステーでも代用可能です。
ただFRPリヤワイドステーは綺麗に加工すれば余ったパーツをお辞儀防止ステーやリヤアンカーのパーツとしても使い道があるので、それらも作る予定でしたら結果的にFRPリヤワイドステーの方がお得になります。
他に代用できるパーツとしてHGカーボンリヤワイドステーでも可能で FRPに比べて価格は高いものの、こちらも綺麗加工すれば余ったパーツを別の用途で使用できバンパーとしての強度も更にアップします。
ただ、FRPパーツでもピボットバンパーに関しては壊れやすさはほぼ変わらないのでお好みで構いません。
尚、本記事では最初に紹介したARシャーシ FRPリヤワイドステーを使用した方法でATピボットバンパーを作成していきます。
スーパーXシャーシ FRPマルチ強化プレート
こちらは元となるフロントATバンパーでも使用しているパーツではあるんですが、ATピボットバンパーではこのパーツが2つ必要となることと少し加工方法が異なるため紹介しました。
予算的に余裕があれば1枚をスーパーXシャーシ カーボンマルチ強化プレートを使うのもありです。
(もう1枚はそれほど強度を必要としないため、カーボンタイプは1枚あれば十分です)
尚、本記事では2枚ともFRPタイプを使用するパターンで解説していきます。
17・19mmローラー用ゴムリング
ピボットバンパーの可動部分で使用するパーツとなります。
自分がしたいピボットバンパーの硬さにより必要個数は変わってきますが基本的には左右2個づつの計4個か多くても計6個あれば十分かと思うので1パッケージ購入しておけば問題ありません。
3mm Oリング
ピボットバンパーの旋回軸となるビスを適度な圧力で固定するためのもので今回は2個使用します。
ハトメ(はとめ)
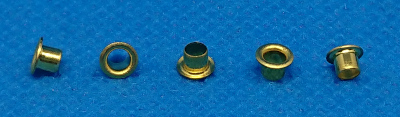
ピボットバンパーの旋回軸となるビス穴の摩耗を抑えるために2個使用します。
基本的にマシンキット(1台につき5個)に含まれているのでわざわざ購入する必要はなくマシンキットの余りのもので構いません。
ただし、ARシャーシ・MAシャーシ・FM-Aシャーシ・VZシャーシにはハトメが付属されておらず、これらのシャーシしか所持していないという方は、上記以外のシャーシを購入する もしくはタミヤから発売されている「AOパーツ ミニ四駆 はとめ」をご購入ください。
2.5mmドリル刃
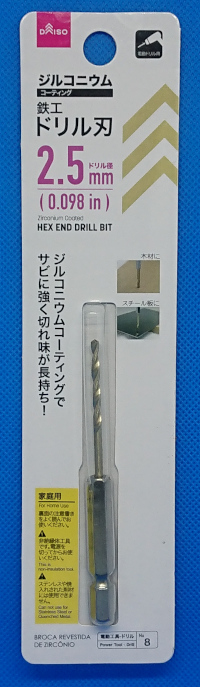
マルチプレートにハトメを取り付けるための穴拡張に使用します。
上記の商品画像は100円ショップで販売しているものとなりますが、これでなくてもタミヤ ベーシックドリル刃セットにも2.5mmドリル刃は付属しています。
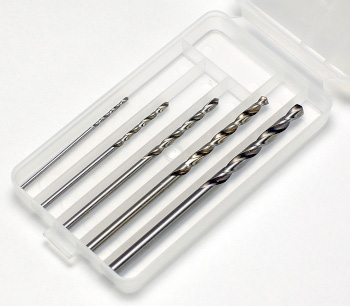
タミヤ ベーシックドリル刃セットには2.5mmドリル刃以外に「1.0mm、1.5mm、2.0mm、3.0mm」のドリル刃が付属しており、それなりに使用頻度が高いサイズのものが多いので 手持ちのドリル刃の種類が少ない方はこちらを購入するのもありかと思います。
※タミヤ ベーシックドリル刃セットを使用する場合はドライバーのビットを差し込み箇所が「ドリルチャック式」である必要があるので、お手持ちドリルが対応しているかどうかのご確認をお忘れなく。
4.0mmドリル刃
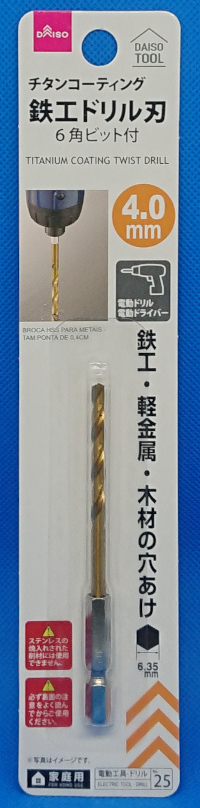
ピボット部分のストッパーの形状加工のために使用します。
このサイズのドリル刃があるのがベストですが、これがなくてもリューターでも加工はできるので無理に揃える必要はありません。
尚、そこそこ規模が大きい100円ショップであれば4.0mmドリル刃を購入することができます。
事前準備
今回のATピボットバンパーの作成にあたり事前にフロントATバンパーのベースとなるリヤブレーキステーの加工 及びシャーシにリヤブレーキステーを取り付けるためのシャーシの加工を済ましておく必要があります。
上記の加工についてはフロントATバンパー作成方法 解説の記事内の「シャーシの加工」「リヤブレーキステーの加工」項目の中で解説しているので、まだこれらの加工が完了していない方は上記のリンクを参照しシャーシとリヤブレーキステーの加工をお願いします。
尚、今回使用するリヤブレーキステー(以下 ブレーキステー)にはスラスト抜け対策用に穴を拡張し、スラスト角度をつけるためにスラスト角調整用チップをあらかじめ取り付けた状態としています。
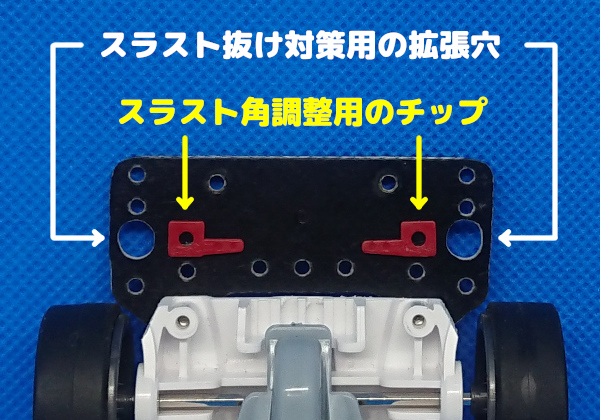
また、上の状態からピボットバンパー用に更に加工をすることもあるので、本記事内の「シャーシへの取り付け」の内容を確認してからリヤブレーキステーの加工をしても構いません。
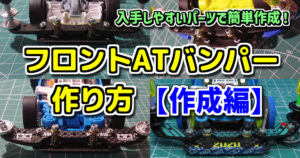
マルチ強化プレートの加工
ここではATピボットバンパーの基幹部分となるスーパーXシャーシ FRPマルチ強化プレート(以下 マルチプレート)の加工方法を解説していきます。
ATピボットバンパーではこのパーツが2枚必要となり、本記事ではFRPマルチ強化プレートを2枚使用していきます。
1枚目(上段パーツ)の加工
1枚目はピボットバンパーの旋回を担う役割で、マルチプレートの上段パーツとなります。
※上段パーツはプレート強度があるに越したことがないので用意できるのであればカーボンマルチ強化プレートが推奨です。
今後の加工工程の中でマルチプレートの表面・裏面という表現を一部使用することがあり表面・裏面の表現をより分かりやすくするためにはまずは表面の時のマルチプレートの向きを紹介していきます。
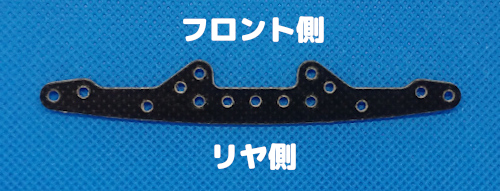
2箇所の出っ張りがある箇所の方がフロント側・反対側がリヤ側となり、この向きを踏まえて以後解説を進めて行きます。
ビス穴の拡張・ハトメの取り付け
ピボットバンパーはピボット部の旋回によりフェンス接触時の衝撃をいなすわけですが、旋回するための旋回軸には負担がかかり摩耗が激しい箇所であるので、摩耗を極力減らすためにハトメを取り付けていきます。
今回は必要最低限のハトメの取り付け方法の紹介となり、作業時のコツや注意点などの詳細方法については別記事[ハトメ 固定方法・圧入方法]にて解説しているので、時間があれば以下の作業前に一読して頂ければと思います。
まず、ハトメを取り付けるためにピボット旋回軸となる以下の既存のビス穴を2.5mmドリル刃で拡張していきます。
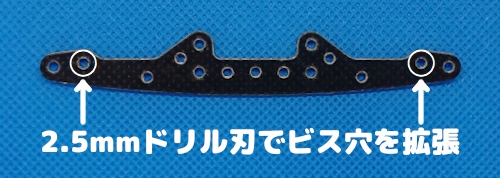
※一度だけの貫通だとハトメがうまく通せないこともあるので、ドリル刃で拡張後にハトメが取り付けれない場合は何度かドリル刃を通して穴を更に拡張させましょう。
穴の拡張が完了したら、ハトメの広い方をマルチプレートの表面にセットします。
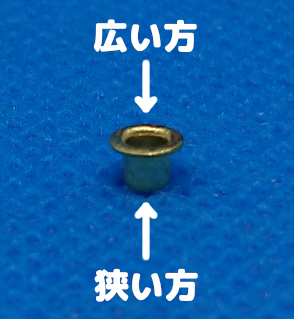
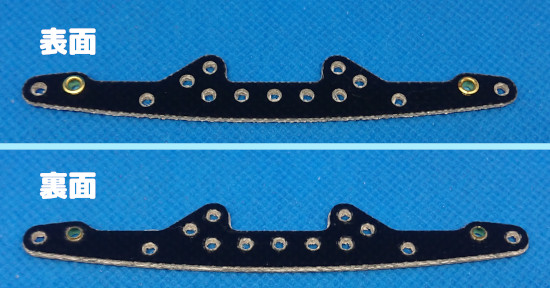
次に皿ビスの頭をハトメの狭い方に向けて取り付け、皿ビス頭の反対側からナットを取り付け プラスドライバーとボックスドライバーで締め付けていきます。

ハトメの狭い部分が潰れてハトメが固定されたら、一旦皿ビスとナットを取り外します。
※この段階ではハトメが抜け落ちない状態であればOKで、若干ハトメが上下にブレても問題ありません。
最後にトラスビスの頭をハトメの潰した方(狭い方)に向けて取り付け、トラスビス頭の反対側からナットを取り付け プラスドライバーとボックスドライバーで締め付けていきます。
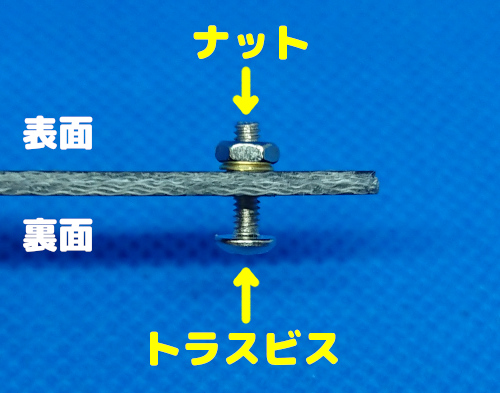
これでハトメがマルチプレートにしっかりと馴染みハトメの取り付けが完了となります。
ちなみにハトメを上記の向きにした理由については、ハトメの裏面の出っ張りを極力無くしたく ハトメの狭い方が出っ張りが小さいためです。
可能であればハトメの出っ張りが完全にない状態が望ましく、ハトメの出っ張りを無くす方法については別記事[ハトメ 固定方法・圧入方法]内の「ハトメの取り付け方法【応用編】」にて詳細方法を記載しているのでよろしければこちらもご参照ください。
尚、ハトメの表裏を間違えて取り付けてしまっていても、この段階であればマルチプレートをひっくり返せばハトメの表裏も変えられるので、左右のハトメの向きが一緒であれば表裏気にせずに取り付けて構いません。
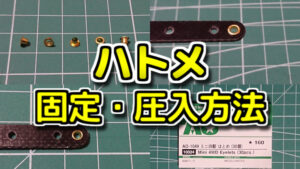
冒頭でも言いましたがハトメはビス穴の摩耗を極力減らすためのものであって、ハトメを付けないからといってピボットバンパーの可動精度自体には影響がないので、ここでのビス穴の拡張及びハトメの取り付けは必須ではありません。
仮にここで加工しなくてもピボットバンパーが完成後でも穴の拡張及びハトメの取り付けは可能で、 しばらくハトメなしでピボットバンパーを使用し旋回軸のビス穴が摩耗してからでもハトメの取り付けは間に合うので、「極力作業工程を短くしたい」「ハトメが手元にない」という方は後回しにしても構いません。
不要箇所のカット
ここではピボット部との干渉箇所をカットしてきます。
厳密に言うとマルチプレート自体はピボット部とは干渉しませんが、ローラーを取り付けた場合にローラー・ローラーのビスと干渉することがあるので基本的にはカットが必要となります。
(11mmローラー使用時はマルチプレートの加工は不要です)
カットする箇所は以下となり、リューターのダイヤモンドカッターで切断していきます。
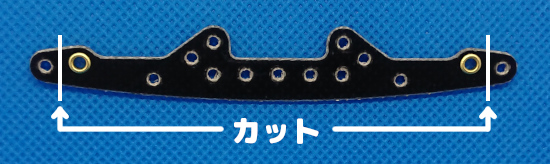
カットについては旋回軸であるハトメを取り付けた部分をしっかりと残しておけばOKで、旋回軸の穴周辺の強度を失わないよう注意しましょう。
カット時の注意点としてハトメを取り付けた旋回軸の穴周辺の強度を失わないようにしましょう。
カットについては直接不要部分をカットしてもいいのですが、端の部分はカット後にフロントATバンパー・ATスライドダンパーで使用できるスラスト抜け対策用パーツにもなるので、必要な方は[フロントATバンパー 作り方]記事内の「カーボンマルチ強化プレートの加工」を参考に、端の穴拡張やヤスリがけを先に実施してからカットを行いましょう。
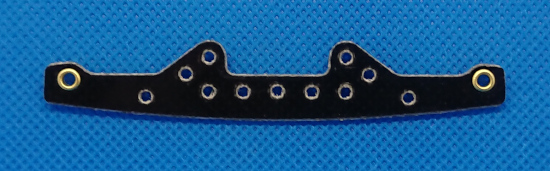
※今回は加工ではマルチプレートのATバンパー支柱部分の厚さが3mmとなりスプリングの圧力も強くなることから、カットした端材でのスラスト抜け対策は実施しません。
2枚目(下段パーツ)の加工
2枚目はプレート部分の下段にあたるパーツで、ピボット部がブレーキステーと干渉することを防ぐための役割となります。
基本的にマルチプレート2枚目はピボットバンパー全体の高さを調整するためのパーツであることから、プレート強度は特別必要としないので 使用するパーツはFRPマルチプレートで問題ありません。
不要箇所のカット
ここではピボット部及びストッパーとの干渉箇所をカットしてきます。
2枚目のどの箇所が干渉するかについては加工済みのピボットバンパーを交えて解説していきます。
まず以下の画像はピボットバンパーの裏面となります。
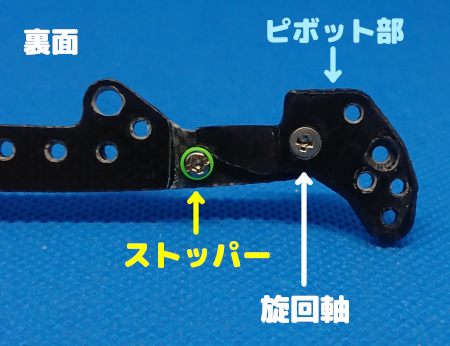
この旋回軸のビスを軸としてピボット部が以下のように可動します。
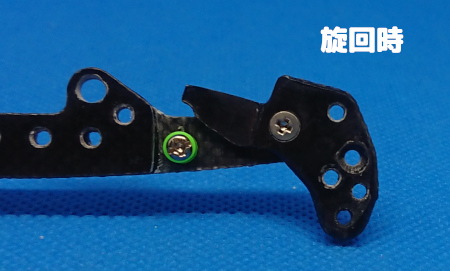
ピボット部の動きを制御するストッパーは1枚目のマルチプレートに設置します。
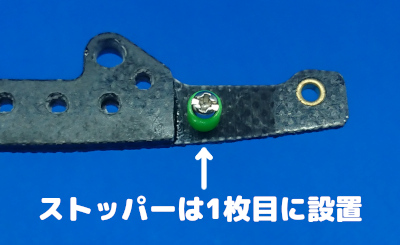
そして、2枚目のマルチプレートがストッパーと同じ高さに位置するため、2枚目は1枚目に取り付けるストッパーとの干渉を避ける必要があります。
このことから1枚目のストッパー部分に該当するビス穴よりも内側を残す形でカットをおこないます。
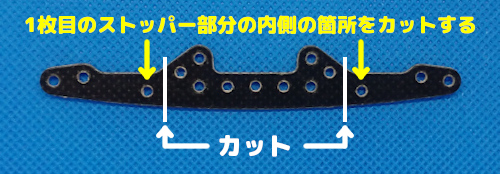
カットはリューターのダイヤモンドカッターを使用し、目視でざっくりとカットしてしまっても構いませんが、左右均等にカットしておきたいという場合は以下の方法でカットしていきます。
まず、マルチプレートの出っ張っている部分の内側のラインに合わせて10mm幅のマルチテープを垂直に貼っていきます。
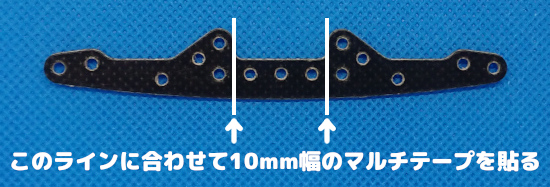
マルチテープを貼ったら、マルチテープ外側をリューターのダイヤモンドカッターでカットします。
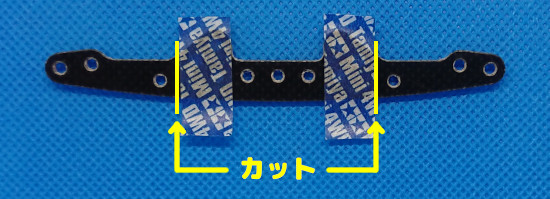
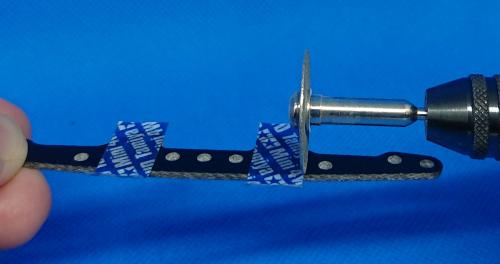
こうすることで左右のカットが限りなく均等になります。
カットしたら1枚目にストッパー(スペーサー)を装着した状態でプレートを重ね、2枚目がストッパーに干渉していないかを確認します。
問題なければ、ダイヤモンドカッターの側面などで切り口を整えてマルチプレート2枚目の加工は完了です。
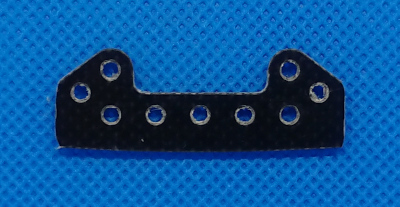
マルチプレート最終加工
1枚目(上段)・2枚目(下段)のマルチプレートの加工が完了したら2枚をまとめて加工していきます。
穴の拡張
まず2枚のマルチプレートを接着剤で接着する前にビス・ナットでマルチプレートを結合した状態で以下のビス穴を3.1mmドリル刃で拡張していきます。
(3.1mm刃がない場合は3.0mm刃でも構いません)
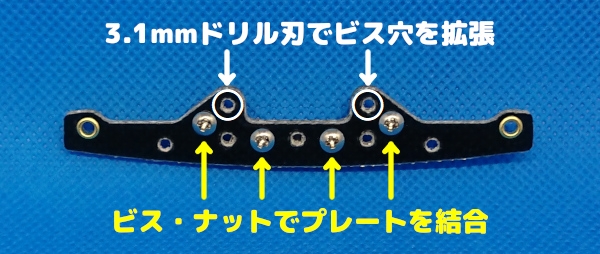
何故、接着する前にドリル刃をあてる必要があるかについては、ドリル刃をあてた際のプレートにかかる負荷が非常に強く、仮に2枚接着した状態で2枚まとめてドリル刃で穴を拡張させようとするとプレート同士の接着が剥がれることがあります。
そうした理由から、まずはビス・ナットで固定した状態でドリル刃を垂直にあてビス穴を拡張していきます。
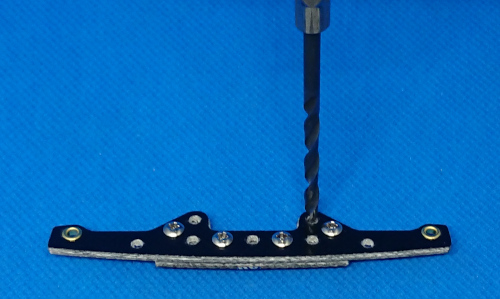
※2枚まとめてドリル刃をあてる場合、電動ドリルの力が弱いと穴拡張に非常に時間がかかることもあるので、穴があけにくいようであれば2枚を分離して1枚ずつの加工でも構いません。
垂直に穴を拡張した後はATバンパーの可動を想定してマルチプレートを傾けた状態でドリル刃をあて 更に穴を拡張していくわけですが、実際にどのくらい削るべきかは全パーツを組み立ててからでないと分からない部分もあるので まずは軽く斜めに削り本格的に削るのは後回しにしても構いません。
ただし、このあとマルチプレート2枚を接着して各パーツを組み立て際に「もう少しマルチプレートの可動域を広げたい」という場合にはドリル刃を使わないようにしてください。
ドリル刃を使っていけない理由は先程話した通りで、もしマルチプレート接着後に可動域を広げたいということであればドリル刃の代わりにリューターか棒ヤスリを使用してください。
リューター・棒ヤスリであれば接着したプレートが剥がれることもありませんので接着後でも安心して穴の拡張ができます。
穴を拡張する工具がドリル刃しかなく接着後に削る必要がある場合は、再度ビス・ナットで固定することで接着剤が剥がれることを回避できます。
※マルチプレートを傾けて削る理由・削り方・使用する工具については別記事[フロントATバンパー 作り方]内の「可動の確認」にて詳細を解説しているのでそちらをご参照ください。
ビス穴拡張後、マルチプレート固定したビス・ナットを取り外す前に2枚目のプレートの表・裏が分かるよう必ず何か目印を付けておいてください。
もし、目印を付けずにプレート表・裏を逆に接着してしまうと、1枚目・2枚目の斜めに拡張した部分がズレてしまい拡張した穴が不揃いになってしまうので、マルチテープを貼るなどして自分のやり易い方法で目印を付けておきましょう。
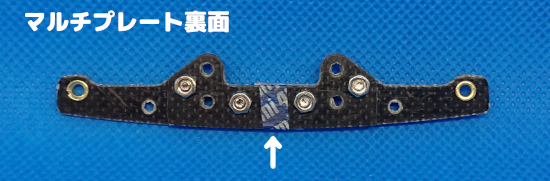
尚、1枚目に関してはハトメの形状で表・裏を判別できるので特に目印を付ける必要はありません。
プレートの結合
穴の拡張が完了したら、ビス・ナットを取り外して2枚のマルチプレートを接着剤で固定していきます。
接着の際、双方のプレートの表・裏の向きには十分注意してください。

プレートを接着剤で固定するコツ・手順については別記事の「ステー・プレート(バンパー)の補強方法」にて詳しく解説しているのでそちらをご参照頂きたいのですが、一つだけ接着時のポイントを伝えると「1枚目のヤスリがけする箇所は中央部分のみ」でOKとなります。
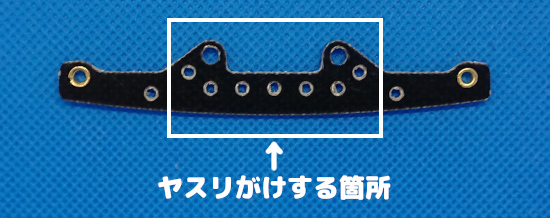
ただ上記の中央部分だけを均等に削る方が意外と面倒くさかったりもしますので、中央部分をピンポイントで削るのが難しいということであれば全体をヤスリがけしても構いません。
2枚のマルチプレートを接着が完了したら、マルチプレートの加工は完了となります。
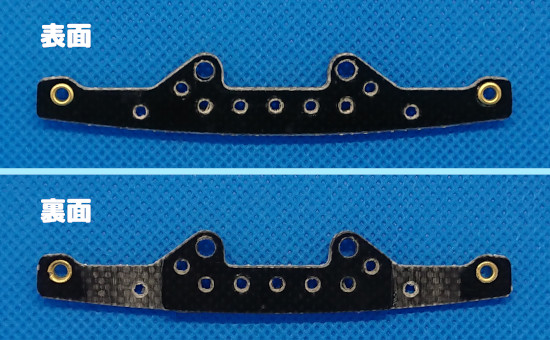
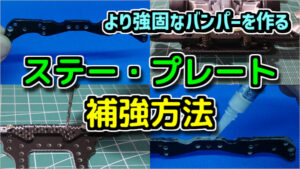
FRPリヤワイドステーの加工
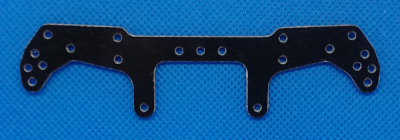
ここではFRPリヤワイドステー(以下 リヤステー)を加工してピボット部(ローラーを取り付けるためのピボットバンパー先端部分)を作成する方法を解説していきます。
尚、リヤステーの加工手順については私が紹介する順番通りでなくても構いませんので、一旦全工程を見てからご自分のやり易い順序で加工して頂ければと思います。
穴の拡張
まずはピボット部の可動範囲を制御するためのストッパーとピボット部がフィットするように、以下の既存ビス穴を4.0mmドリル刃で拡張していきます。
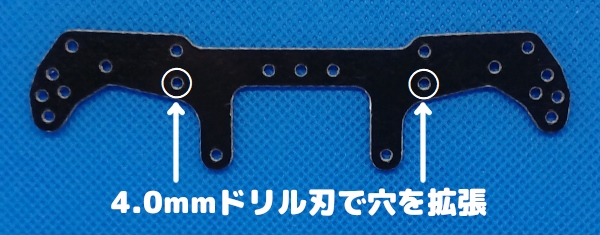
そして4.0mmドリル刃で拡張した箇所がピボット部 旋回時のストッパー部分となり、これ以降 4.0mmに拡張した箇所をストッパー穴という名称で解説を進めていきます。
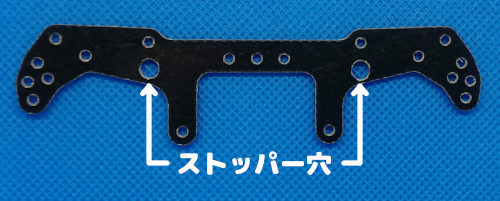
不要部分のカット
ストッパー穴ができたら、次に不要部分をカットし ピボット部の形を整えていきます。
カット手順については以下の3フェーズに分けて紹介していきますが、必ずしも以下の手順がベストということではないので、一旦全工程を見てからご自分がやりやすい順序で加工してもらって構いません。
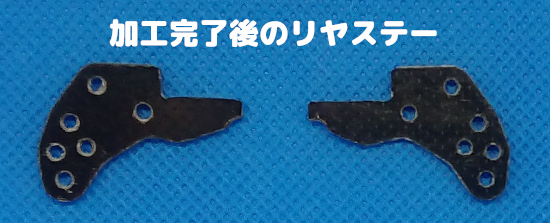
加工に慣れている方は上の加工完了後の画像の形になるよう一気に加工しても構いません。
フェーズ1
フェーズ1では以下のラインをカットしてリヤステーの両サイドを切り落としていきます。
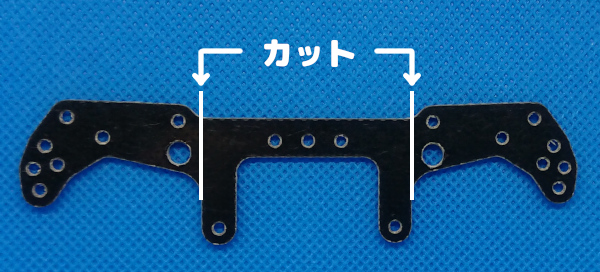
両サイドのカットにはリューターのダイヤモンドカッターを使用します。
※ダイヤモンドカッターがなければクラフトのこでカットしても構いません。
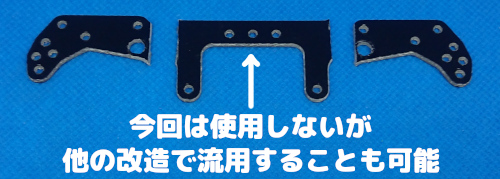
このような形でカットしておけば、残った端材をお辞儀防止ステーやリヤアンカーのパーツとしても使うことも可能です。
フェーズ2
フェーズ2ではストッパー穴の周りをカットしていきます。
ストッパー穴は以下の黄色いラインの箇所さえ残しておけばピボット旋回時のストッパーとして機能するので、この箇所を残した形で他の不要な箇所をカットします。
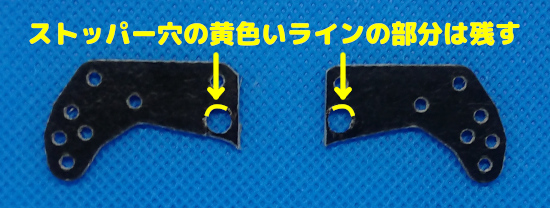
簡単なカット方法として、以下の白ラインをダイヤモンドカッターで一気にカットすると、ストッパー穴の大事な箇所を残しつつ不要な箇所をカットすることができます。
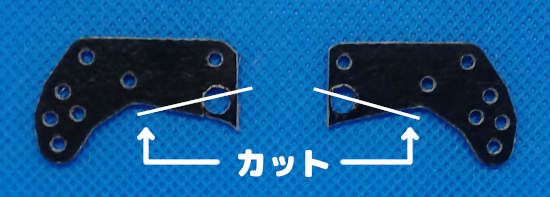
どの角度でカットして良いのか分からなければ、これ以降いつでも削る事は可能なので、一旦はある程度ストッパー穴の周辺を残しておいても構いません。
また、以下の画像がカットした後のものとなり 左側のリヤステーはストッパー穴の原型がほぼ分からない状態となっていますが、この状態でも しっかりとピボットの動きを制御してくれます。
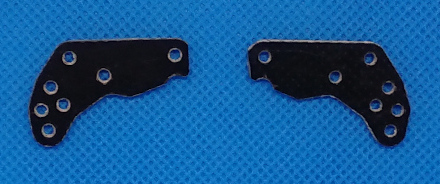
カットした両サイドのステーは最終的に左右対称の形になるので フェーズ2とフェーズ3の作業は2枚のステーをビス・ナットで結合した状態で実施しても構いません。
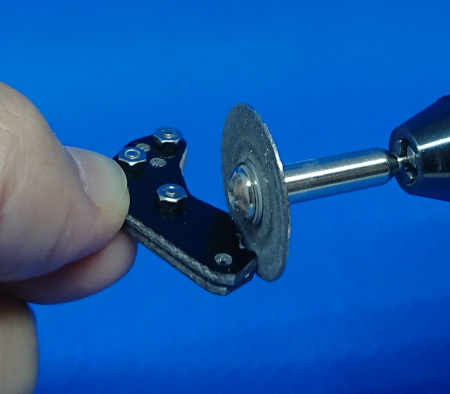
フェーズ3
フェーズ2完了の段階でピボット部として機能するわけですが、このままの形状だとピボット部が旋回した時にブレーキステーと干渉し 旋回がスムーズにいかないことがあります。
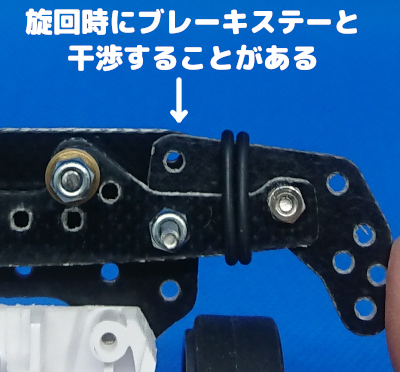
厳密に言うと、ゼロスラスト(スラスト角0℃)の状態であれば干渉することがないのでフェーズ3の加工をする必要はありませんが、スラスト角を付けるケースの方が多くなるのでフェース3の加工はほぼ必須になるのかと。
より旋回をスムーズにさせるための加工は、旋回時に干渉する以下の箇所をカットしていきます。
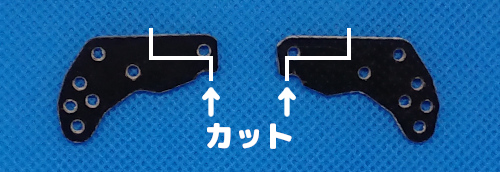
カットにはリューターのダイヤモンドカッターを使用していくわけですが、上の画像の表記だと具体的にどのラインでカットして良いのか分かりづらいです。
そこでカットするラインを より明確にする方法を紹介します。
まず、シャフトの軸受けで使用する外径6mmのプラベアリングを2個用意します。
(マシンキットに付属しているものでOKです)
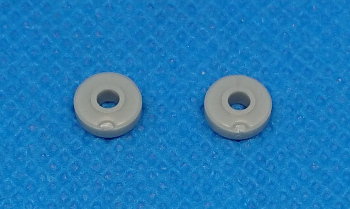
このプラベアリングをビス・ナットを使って旋回軸のビス穴に固定します。
※ハトメを装着できるプラ部品を使用する場合は穴の直径が大きく位置がブレやすいのでハトメを装着した状態でビス穴に固定していきます。
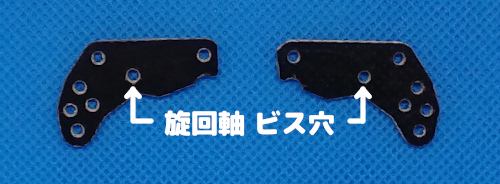
あとは以下の画像のように既存ビス穴とプラベアリングを指標にして以下の白いライン部分をカットしていきます。
(黄色のラインはあくまで指標であってカットするラインではないのでご注意ください)
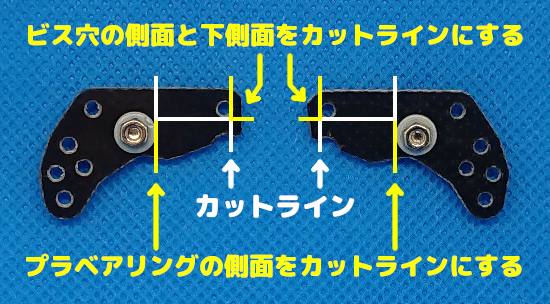
より慎重にカットするのであれば、以下の画像ようにカットラインをはっきりとさせるためにマスキングテープを貼ることをおすすめします。
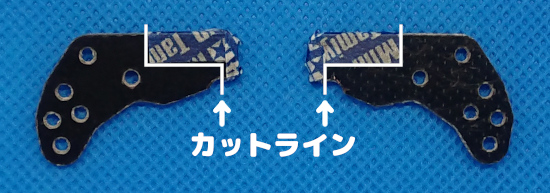
カットし終わったら棒ヤスリなどでカット面を整えてピボット部の完成となります。
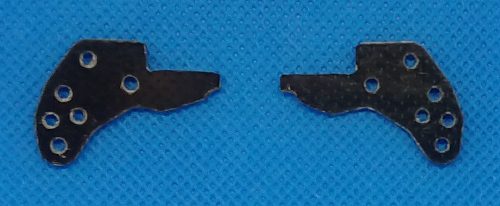
フェーズ3の加工方法については下準備に少々手間がかかる工程となりますが、ここまで厳密に加工する必要はなく ある程度ざっくりカットしても可動に影響が出るということではありませんで、印を付けたりするのが面倒くさい方は上の完成画像に近い形にカットすればOKです。
皿ビス加工
リヤステーの最後の加工として、ピボット部の裏面の旋回軸となる以下のビス穴に皿ビス穴加工用ビットを使用して皿ビス加工をしていきます。
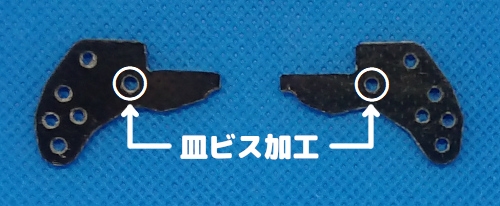
皿ビス加工はリヤステー加工の最初の段階で実施しても構わないわけですが、最後に紹介したのには理由があって 今回 皿ビス加工するのは先程加工してきた上の画像のリヤステーではなく、新たに用意するもう1枚のステー(FRPリヤワイドステー)におこなうからです。
この新たに用意するステーは引っ掛かり防止用となり引っ掛かり防止ステーとして使用するもので、このステーが下側(地面側)になることから 引っ掛かり防止ステーとして使用するもう1枚のステーに皿ビス加工が必要となります。
尚、引っ掛かり防止ステーを必要としない場合はすでに加工済みのリヤステーに皿ビス加工をしていきます。
本記事では具体的な引っ掛かり防止ステーの各ビスに対応した加工方法は省略しますが、今回のピボット部に適した形の引っ掛かり防止ステーの形の作り方は少しコツがあるので、ここだけは解説しておきます。
※これ以降、すでに加工済みのリヤステーを「1枚目」という名称とします。
引っ掛かり防止ステーの作成手順は、まず旋回軸のビス穴を皿ビス加工し、皿ビス加工した部分を残した形で不要箇所をカットしていきます。
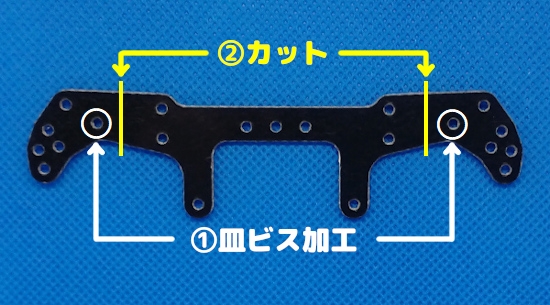
※カットする際は皿ビス加工した箇所の強度が落ちない程度の位置で切断すればOKです。
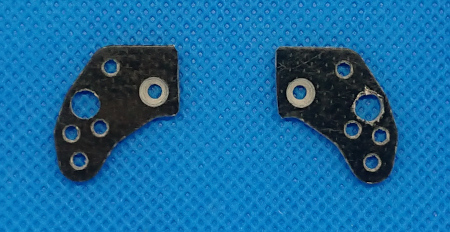
※今回は13mmローラーをキャップスクリューを使って取り付けることを想定しているので、事前に13mmローラー用のビス穴を拡張しています。
また、上記の引っ掛かり防止ステーは皿ビス加工穴付近は結構残した形になっていますが、後のゴムリングを装着させることを考慮すると、もう少し皿ビス加工穴に近い所まで削っておいた方が良かったりもします。
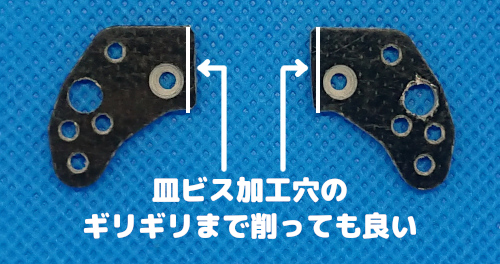
何故、更に削っておいた方が良いのかについては後に実施する「シャーシへの取り付け」にて解説しています。
※ビス穴の拡張方法・拡張に使用する工具等については以下の記事にて詳細を解説しているので、そちらをご参照ください。
引っ掛かり防止ステーの皿ビス加工・カット・ビス用の穴拡張が完了したら、1枚目と接着剤で固定していきます。
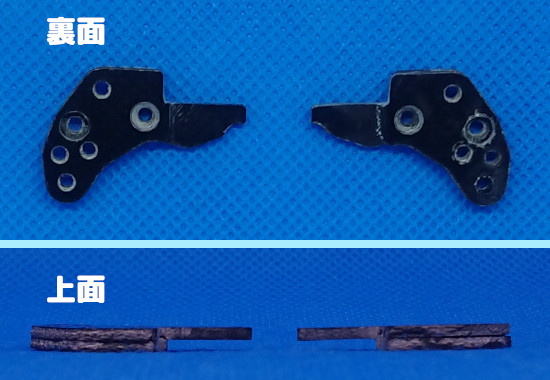
上の画像は接着後に少し加工を加えた状態となっていますが、引っ掛かり防止ステーの上部が1枚目からはみ出すことがあるので、そうした場合はリューターやヤスリを使って1枚目の形に合うように引っ掛かり防止ステー側を削っていきます。
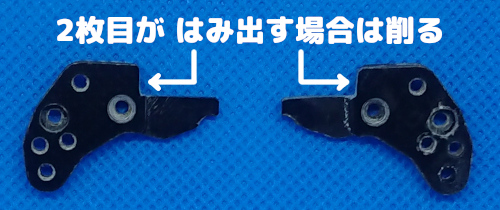
※逆に1枚目の方がはみ出しているという場合はそのまま手を加える必要はありません。
あとは引っ掛かり防止用の最終加工を施しピボット部の作成が完了となります。
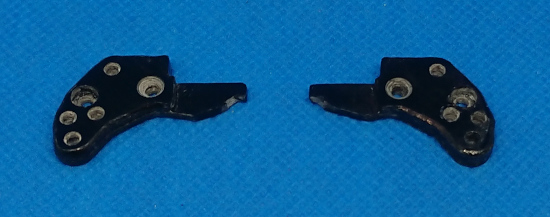
組み立て
ここではATピボットバンパーの組み立て方を解説していきます。
ピボットバンパーの組み立て
ここでは今回加工してきたマルチプレートとピボット部(リヤステー)を結合しピボットバンパーを組み立てる手順を解説していきます。
まずマルチプレートのストッパー部分となるビス穴に以下の配置でスペーサー・皿ビス・ロックナットを取り付けていきます。
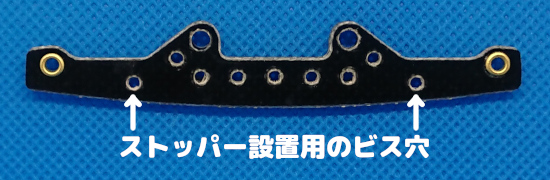
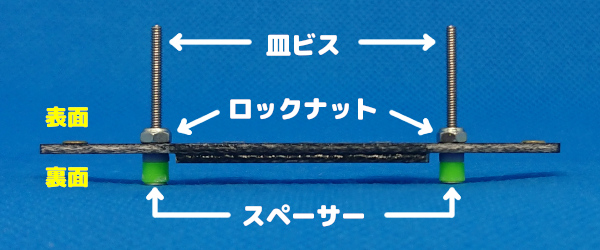
スペーサーはピボット旋回時のストッパーとなり、基本的には1.5mmのもので十分ですが、今回はスラスト抜け対策の役割も担うため1.5mm+3mmの構成となっています。
ビスについてはフロント提灯を取り付けることを想定し25mmの皿ビスを使用していますが、フロント提灯を取り付けないのであれば短いビスでOKで、ビスの種類も皿ビスである必要はなく鍋ビスでも構いません
ただし鍋ビスを使用する場合はブレーキステー側の穴を拡張していないと鍋ビスの頭の部分がブレーキステーに干渉し、バンパーの高さが変わってしまうのでご注意ください。
(逆に、この特性を生かしてスラスト角を付けることも可能です)
上記のプラスペーサーは皿ビスを取り付けるために皿ビス加工を施しており、プラスペーサーの皿ビス加工の方法については別記事[MSフレキ 作り方]内の「スペーサーの皿ビス加工方法」にて詳しく解説しているので そちらをご参照ください。
次に17・19mmローラー用ゴムリング(以下 ゴムリング)を2重にして以下のように取り付けていきます。
(今回はゴムリングを2個使用していますが、使用する数はお好みで構いません)
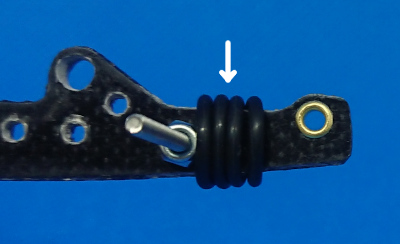
次にピボット部をゴムリングに取り付けていきます。
ピボット部の先端部分をゴムリングの間に通すようにしてマルチプレートに仮固定していきます。
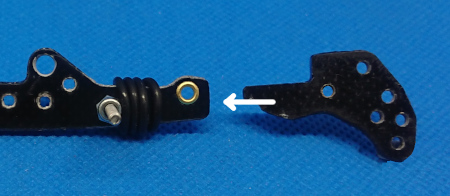
配置はマルチプレートが上でピボット部が下となります。
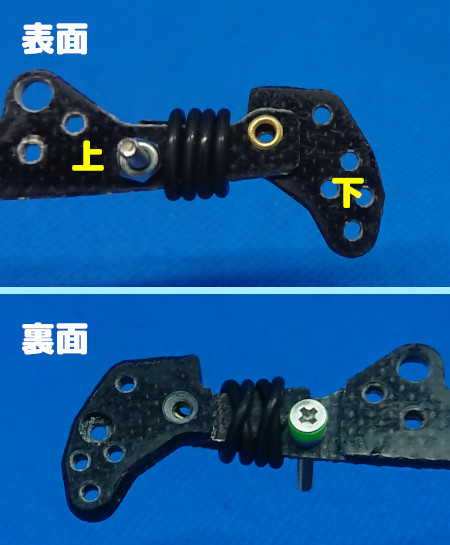
次にマルチプレートとピボット部の旋回軸となるビス穴に、ピボット部の裏側から皿ビスを通していきます。
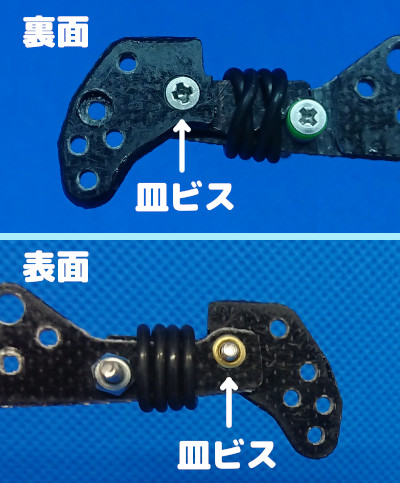
※ここでは8mmの皿ビスを使用しています。
皿ビスを通したら以下の配置で3mmOリングとロックナットを設置します。
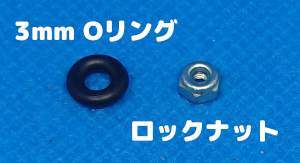
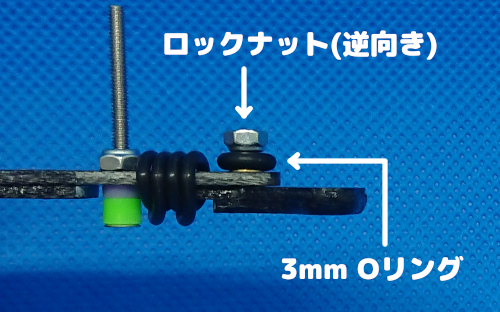
ここでのロックナットは3mmOリングの形状にフィットしやすくするために逆向きで取り付けていきます。
ちなみに3mmOリングを使用した理由については、ロックナットの間に3mmOリングを挟むことでマルチプレートとピボット部を適度な圧力で固定できるようになるからで、ピボット部がしっかりと固定されつつもスムーズな旋回が可能となります。
あとはボックスドライバーとプラスドライバーで適度な硬さになるようロックナットを締めていきます。
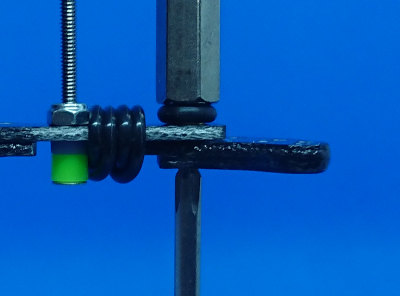
ピボット部がガタつかず且つスムーズに旋回する状態になればOKです。
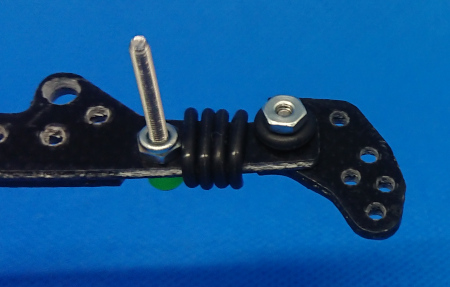
反対側も同じ手順でピボット部を取り付け、両サイドにピボット部を取り付けてピボットバンパーの完成となります。
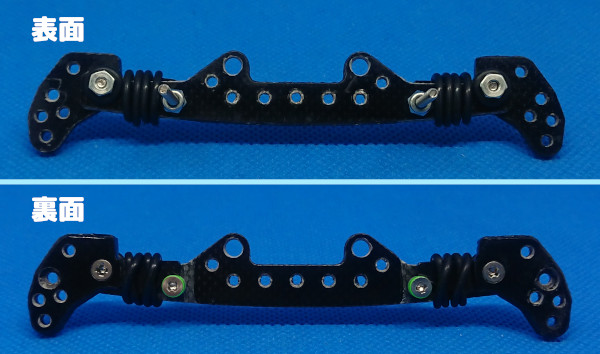
シャーシへの取り付け
ピボットバンパーが完成したら、シャーシ(ブレーキステー)に取り付けていきます。
シャーシへの取り付けに使用するパーツ・取り付け手順についてはフロントATバンパーと同じ方法となり、ここでの取り付け作業については 別記事[フロントATバンパー作り方 解説]記事内の「組み立て」の項目にて詳しく解説していているので そちらをご参照ください。
そして、ピボットパンパ―をシャーシに取り付けた状態が以下となります。
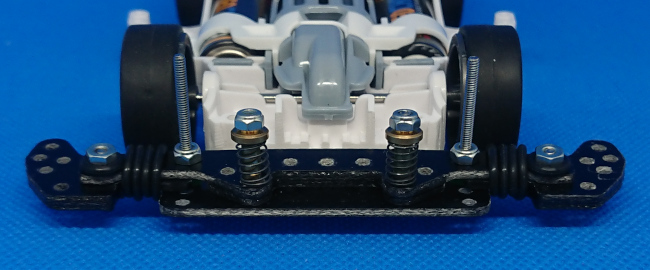
ゴムリングの位置に注意!
ピボットバンパーをシャーシに取り付けた際にゴムリングが内側に寄りすぎてしまうと ブレーキステーの上にゴムリングが載っかり、以下の画像ように何もしていない状態でもバンパーが斜めになってしまうことがあります。
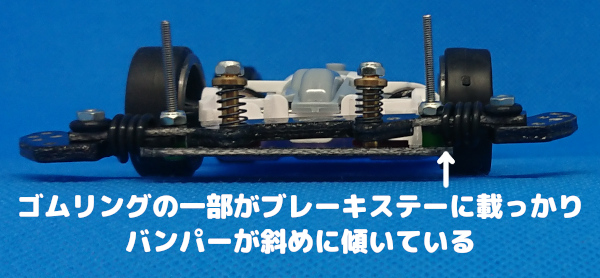
上の状態にならないようゴムリングはできるだけ外側に寄せるようにしてください。
ただ、ゴムリングの設置スペース自体が狭いこともあり、走行中にゴムリングが僅かにずれて何かの拍子にブレーキステーの上に載ってしまうということもあるかもしれませんので、そういった場合はブレーキステーの外側を削ることで対処できます。

この辺は使用するゴムリングの数や元々のブレーキステーの加工具合によっても変わってくるので、実際に組み立ててから加工が必要かどうかを判断して頂ければと思います。
そして、もう一つの対応策として、ピボットバンパーのピボット部を加工することでもゴムリングのスペースを僅かではありますが広げることが可能です。
これはピボット部に引っ掛かり防止ステーとなる2枚目のステーを取り付けている場合のみの方法となりますが、以下の画像の矢印で印した箇所を残しすぎるとゴムリングの設置スペースが狭くなることがあります。
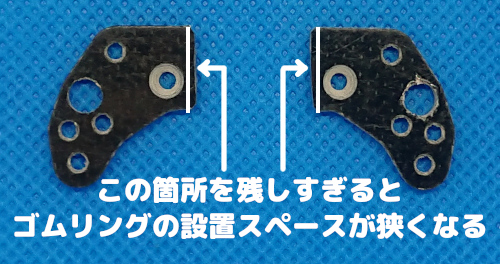
このことから皿ビス加工穴のギリギリまで削れば僅かではありますがゴムリング設置スペースを増やすことができ、すでに引っ掛かり防止ステーである2枚目を1枚目のリヤステーと接着済みでも棒ヤスリを使えば2枚目だけを削ることができるので、上記の引っ掛かり防止ステーを使用している方は試して頂ければと思います。
ローラーの取り付け
今回加工したピボット部は9mm・11mm・13mm・17mm・19mm ローラー用のビス穴があり いずれか お好みのサイズのローラーを取り付けることが可能ですが、13mm以上のローラーを取り付ける場合はローラーの位置(高さ)に注意する必要があります。
以下の画像は13mmローラー(2段アルミローラー)を取り付けた状態となりますが、ローラーがOリングに干渉して回らなくなっています。
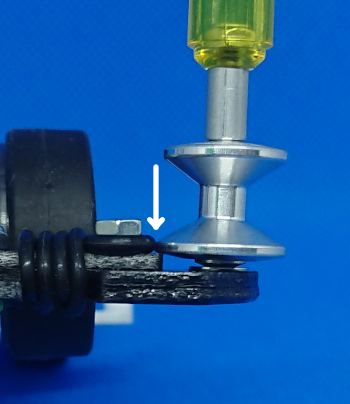
このOリングとの干渉を回避するための方法は2通りあり、1つ目の方法はローラー自体の高さを上げることです。
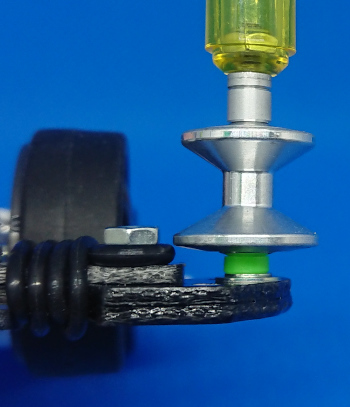
上の画像はピボット部とローラーの間に小ワッシャー1枚・大ワッシャー1枚・1.5mmスペーサーを挟みローラーの高さを上げてOリングとの干渉をぎりぎり回避しています。
(ローラーの適切な高さは同じローラー径でもローラーの形状によって異なるのでご注意ください)
ただし、13mmローラーはOリングさえ回避すれば問題ありませんが、17mm・19mmローラーに関してはロックナットにも干渉してしまうのでロックナットも回避する必要があり、上の画像のローラー位置よりも更に高い位置に配置する必要があります。
このことからローラー径が大きくなるほどローラーの高さを上げざる得ないという欠点があるので、大径ローラーを使用する際はローラーの位置には十分気をつけてください。
そして、干渉を回避するための2つ目の方法はピボット部の下側にローラーを配置することです。
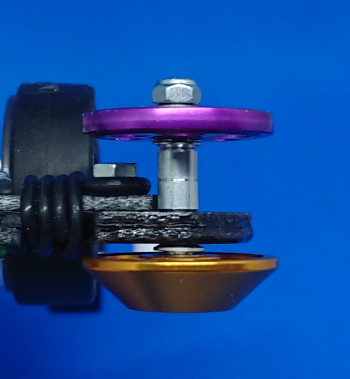
ピボット部の下側であればゴムリング・ロックナットとの接触を気にする必要はないのでローラー径が大きかろうが問題ありません。
そして、ピボット部の上側に上段ローラーを追加する場合はゴムリング・ロックナットを回避させる必要はありますが、よほど下段のローラーと寄せようとしない限りは取り付けられるので上段ローラーも実用的な高さで取り付けることができるのかと。
ただし、19mmローラーの場合はピボット可動部分でもあるゴムリングが外側に寄っているとローラの高さによってはぎりぎりローラーと干渉してしまうので注意してください。
また、ピボット部の下側にローラーを設置する場合は地上高の問題や引っ掛かり防止の問題なども出てくるので、ピボット部の下側にローラーを設置する場合はブレーキステーの高さ自体を上げたりするなどして対処するようにしてください。
ローラーを適切な位置に取り付け終えたら、ATピボットバンパーの完成となります。
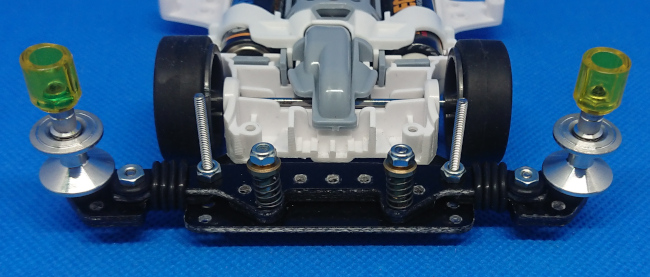
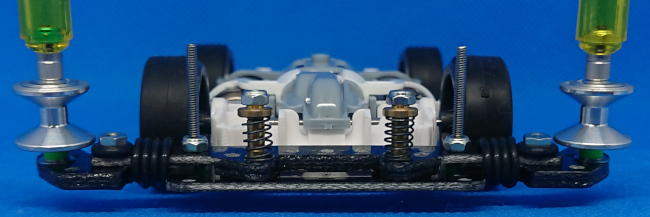
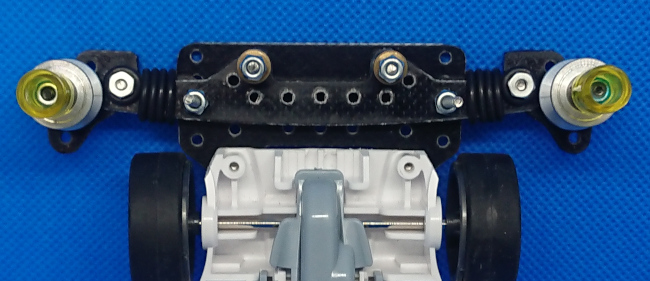
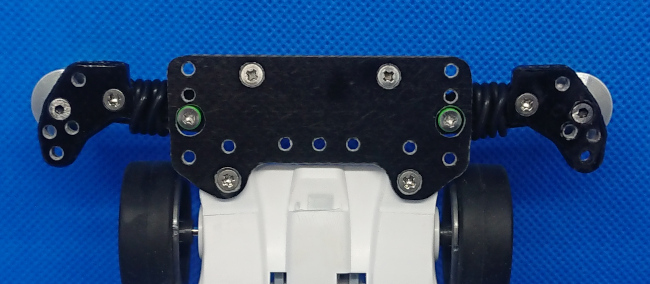
可動確認・最終調整
ATピボットバンパーが完成したら最後に可動に問題がないかを確認し、問題があれば該当部分を改善していきます。
可動の確認
まずはATピボットバンパーとして以下の3つの項目に問題がないかを確認していきます。
硬さの確認
ピボットバンパーとしてフェンスに接触した際にピボットバンパーが適切な硬さか正しく可動してくれるか、ピボット可動時にスラスト抜け等の不具合がないかを確認していきます。
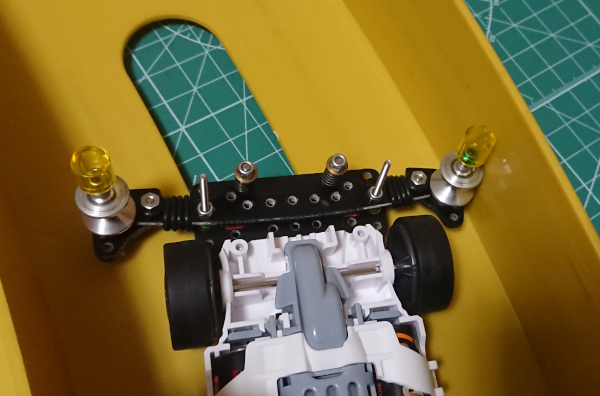
ピボットバンパーの硬さについてはゴムリングの数量で変わるので柔らかくしたい場合は数を減らし、硬くしたい場合は数を増やします。
ただし、片側に17・19mmローラー用ゴムリング(以下 17・19mmゴムリング)を3つ付けると以下の画像のように結構ゴムリングが窮屈な状態になり、ブレーキステーに干渉し ピボットバンパーがブレーキステーに乗り上げてしまうことがあります。

どうしても片側に17・19mmゴムリングを3個付けたい場合はブレーキステー側を削れば干渉することも避けれます。
それと、ピボットの硬さを微調整したいという場合は13-12mmローラー用ゴムリング(以下 13-12mmゴムリング)がおすすめです。
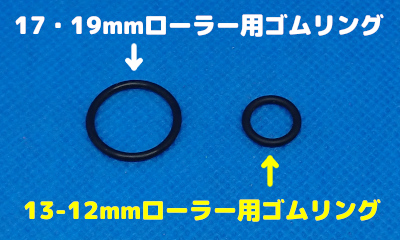
13-12mmゴムリングを使用する場合は2重にせずにそのまま取り付けていくわけですが、13-12mmゴムリングだけだとぶかぶかになってしまい ゴムリングの意味を成しません…
13-12mmゴムリングを使う場合は、17・19mmゴムリングを取り付けた上で17・19mmゴムリングの2重にした箇所に重ねるように取り付けてください。
そうすることで適度な硬さを出すことができるようになります。
いなし機能の確認
また、フェンスに乗り上げた際のいなし機能もしっかりと機能するかを確認していきます。
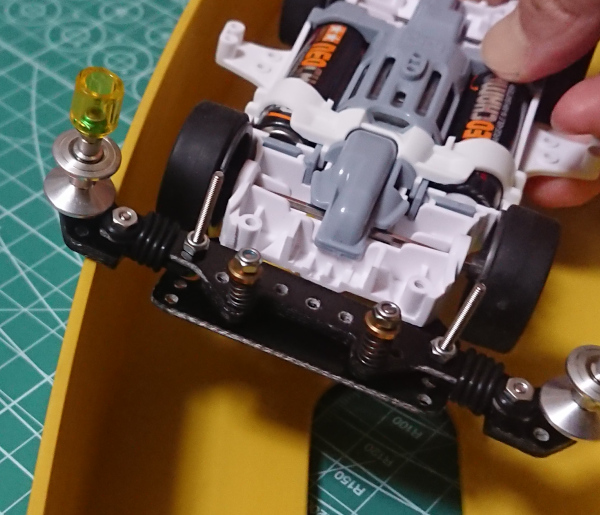
いなし機能の調整方法についてはATスライドダンパーのベースとしているフロントATバンパーに依存してくるので、別記事[フロントATバンパー作成方法]をご参照ください。
(ATバンパー支柱穴の拡張にドリル刃を使用する場合はビス・ナットで2枚のマルチプレートを固定することをお忘れなく)
マシン最大幅の確認
可動とは直接関係ないのですがこちらも大事な要素でマシン最大幅が規定サイズ内(105mm以下)に収まっているかどうか確認します。
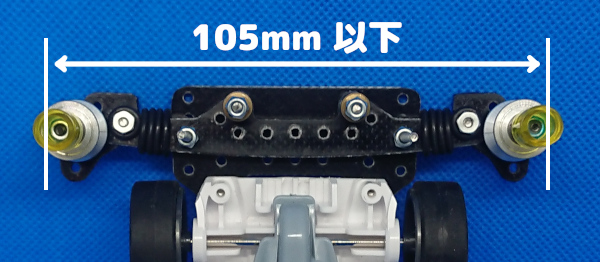
今回作成したATピボットバンパーのバンパー幅は規定通りのサイズとなり、各ローラーを適切なローラー穴に設置すれば規定通りの最大幅になるようになっています。
しかし、正常時の状態でピボット部が僅かに旋回していたり戻り過ぎたりしていると最大幅が微妙に変わり規定サイズを越えてしまうことがあります。
この最大幅が変わる場合の改善策については次の項目で解説していきます。
問題点と改善策
ここでは今回のATピボットバンパーにて起こりうる問題点と その問題点を解決するための対応策を解説してきます。
まず起こりうるであろう問題点が以下となります。
次からは上記の各問題点の具体的な内容及び その問題点を改善するための対応策を説明していきます。
マシン最大幅が規定サイズを越えている
先程の可動の確認の項目でも触れた内容となりますが、デフォルトの状態でピボット部が旋回していたり・戻り過ぎているとマシン最大幅の規定サイズの105mmを越えてしまう場合があります。
最大幅が広くなる原因になるのがピボット部のストッパー接触箇所の加工具合です。
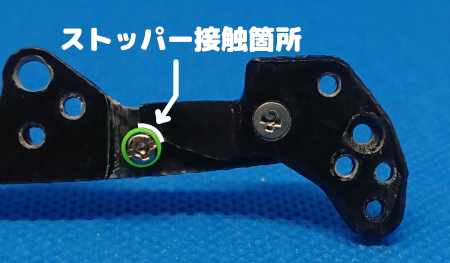
まずはピボット部のストッパー接触箇所がストッパーであるスペーサーにしっかりと接触しているかどうかを確認します。
ストッパー接触箇所の一部だけしかスペーサーに接触していないということであれば、ピボット部が戻りきれていない状態(旋回している状態)の可能性が高いので、ピボット部のストッパー接触箇所を削りスペーサーにピッタリとフィットするようにしていきます。
逆にストッパー接触箇所を削りすぎてピボット部が戻りすぎているという場合は、スペーサーにマルチテープなど巻いて僅かにスペーサーの直径を広げる、もしくはピボット部のストッパー接触箇所に接着剤やパテなどをつけて厚みを戻して、ピボット部の戻りすぎを防いでいきます。
ピボット旋回時の動きがぎこちない
この問題点は旋回軸のビスを締めすぎていたり、ピボット部とブレーキステーで無駄に干渉している場合に発生します。
まず旋回軸のビスを緩めてみて旋回がスムーズになるか確認し、スムーズになったようであれば再び旋回軸のビスを締め直してピボット部がガタつかず且つスムーズに旋回する強度で調整していきます。
ビスを緩めも旋回がスムーズにいかない場合はピボット部とブレーキステーの以下の箇所が干渉している可能性があります。
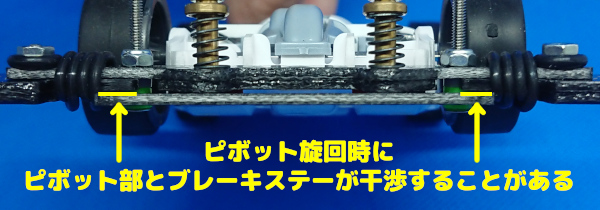
特にスラスト角の傾斜が大きくなるほど干渉度合いが増すわけですが、対処法としては「ピボット部とブレーキステーの干渉箇所にグリスを塗る」か「ピボット部の干渉箇所をヤスリで削る」のいずれかになります。
「グリスを塗る」方法の方がお手軽ではあるんですが ブレーキステーはそれなりに触れる箇所であり 手にグリスが付着すると何かと煩わしくなるので、まず「ヤスリで削る」方法を試して、それでもスムーズにならなければ「グリスを塗る」を実行することを推奨します。
尚、「ピボット部の干渉箇所をヤスリで削る」場合は裏面の以下の箇所をヤスリで削っていきます。
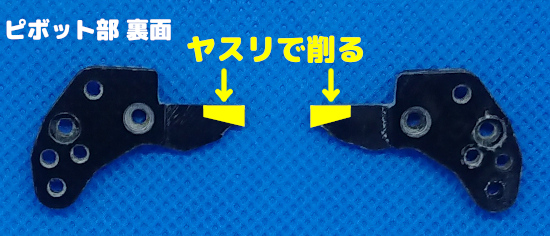
スラスト角に合わせて斜めに削るのがポイントで、より多く削れば干渉箇所を無くすことができますが該当箇所の強度も落ちてしまうのでくれぐれも削りすぎには注意してください。
ピボットが旋回して戻る時の動きがぎこちない
この問題点は旋回軸のビスを締めすぎていたり、ピボット部とストッパーのかみ合わせが悪い場合に発生します。
旋回軸のビスを締めすぎていても旋回はスムーズに行くことがあるんですが戻りが変にゆっくりすぎたり戻りきらないことがあるので、まず旋回軸のビスを緩めてみてスムーズに戻るかどうかを確認し、スムーズに戻るようであれば適度なビスの締め具合に調整し直します。
ビスを緩めても変わらない場合はピボット部とストッパーの噛み合わせが悪い可能性が高く、ピボット部の以下の箇所を残しすぎているとピボット部がストッパーに引っ掛かる事があります。

ピボット部の加工のフェーズ2のところでも説明しましたが、ピボット部のストッパーとの接触箇所は以下の箇所だけ残しておけば しっかりとピボット部を制御できるのでストッパー接触する無駄な部分は極力削っていきましょう。
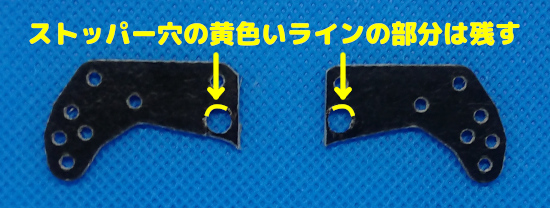
ピボット旋回時にスラストが抜ける
ピボット部の旋回時にはバンパー自体にもかなり負荷がかかっており、スラスト抜け対策をしていないとピボットが可動する前にスラスト抜けを起こし、最悪コースアウトを招くことがあるのでATピボットバンパーにおいてスラスト抜け対策は必須とも言えます。
しっかりとスラスト抜け対策ができているかどうかは、硬い壁にピボットバンパー部分を押し当てピボットバンパーが可動しつつスラスト抜けが起きていないかを確認しましょう。
もしスラスト抜けでお困りの場合は以下の[スラスト抜け対策方法]記事を参考にしていただき、スラスト抜け対策を実施して頂ければと思います。
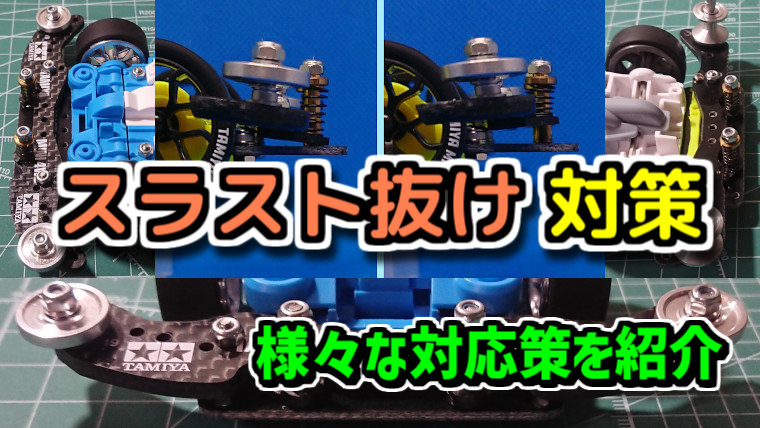
尚、今回のATピボットバンパーの構成では個人的には「つっかえ棒を付ける」がおすすめです。
最後に
今回はATピボットバンパーの作成方法を解説してきたわけですが、本記事の冒頭でも話したように今回のType1とは異なる形状のピボットバンパーであるType2も別途紹介しているので、よろしければそちらもご覧頂ければと思います。
Type1・Type2のどちらが優れているということはなく、マシンの構成や使いたいシーンによっても適するタイプが変わり、Type2の記事の方でType1とType2の違いについて詳しく解説しているので、そちらを見てから ご自分のマシン・走らせるコースによりマッチしたタイプを選んで頂ければと思います。
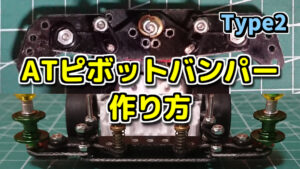
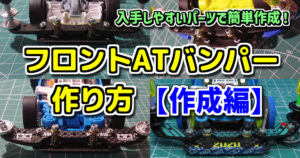
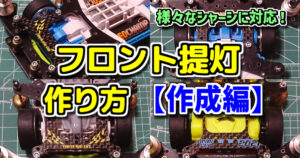
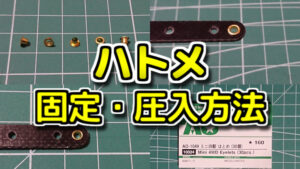
コメント